Why Web Guiding Control System Important For Edge Position Control
The technical operation for the coil materials that must always keep the edge of the coils neat and consistent during the spraying, printing, punching, laminating, slitting, or other coil winding processes is referred to as web guide control. The equipment used in the guiding process is a collection of web guiding control system. A common system consists of a controller, a sensor, a guide mechanism, and a driver.
Why Choose Web Guiding Control System
Webs do not always track down through a machine in the same place. Any offsets in the unwinding roll, for example, will cause the web to start through a machine in a variable CD (cross direction) position on a roll-to-roll operation. Even if a web begins in the position, it may take slightly different paths through the machine depending on a variety of factors.
First, a variably baggy or cambered web will cause the web to track toward the variably tighter side. Second, variations in roller traction or drag can cause web steering. Third, changes in tension will affect how straight the web travels downstream. At zero tension, edge position control is essentially lost. Other edge movement factors include nip roller draw variations, aerodynamics, and so on.
Web guides are used to move the web’s edge or center to a specific CD position. The guide location could be at an unwind to start the web down through a machine in a consistent position, an intermediate location, or the winder to improve roll edge quality. The guide’s accuracy requirements can range from simply keeping the web on the rollers to minimizing trim loss and registering multiple print colors to within a few mils. Guides can be active or passive.
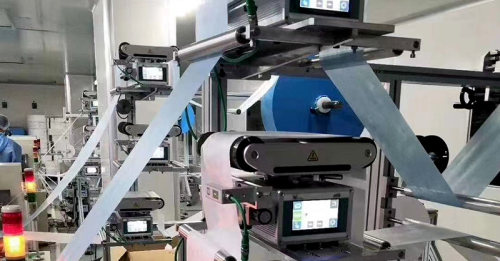
Working Of Web Guiding Control System
The purpose of the web guiding is to direct the sensor to emit infrared or ultrasonic radiation in order to monitor the operation of the coil material and send a signal to the controller. After the controller determines that the web has a positional deviation, the controller controls the drive system to swing to correct the web position using the preset command.
Brushless DC servo motor drive, precision ball screw drive, compact structure, good mechanical rigidity, low inertia, suitable for high-speed and high-precision web guiding are used in the web guide system.
A controller, a sensor, an electric driver, and a correction guide mechanism comprise the system. The sensor detects the coil material’s edge position and reads the deviation between the actual and set positions, converting the deviation into a voltage signal proportional to it. The signal is then sent to the controller. After the signal is amplified and calibrated by the controller, the signal is output to the electric driver, and the electric driver drives the guide mechanism to perform correction actions according to the magnitude of the input signal to guide the coil material to the preset position.
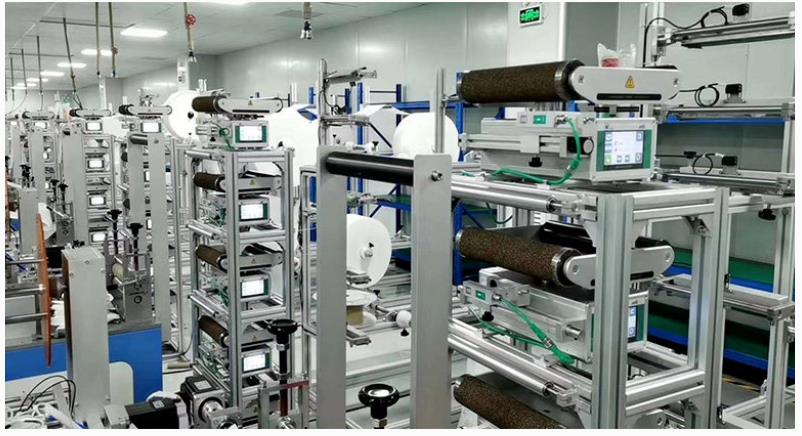
Advanced Web Guiding Control System From Arise
Arise is a leading manufacturer in China, offering advanced web guiding control systems. It is suitable for paper, non-woven fabric, plastic film, self-adhesive label tape, aluminum platinum, hot-rolled strip steel, and other applications. To ensure the neat division of the rewinding machine, the edge or marking line should be tracked and guided by the control border. The photoelectric correction manipulator uses a universal photoelectric controller for edge and line alignment, as well as imported drive machinery and a high-precision controller to control and maintain the edges or lines in a specific direction. The operation of the web guiding machine is simple, with high precision and reliability.