Why Vision-based 100% Inspection Systems are Widely Used for Quality Assurance
Table of Contents
Traditional inspection methods, which relied on sampling or manual oversight, often left gaps in defect detection and consistency. However, 100% inspection systems powered by advanced vision technologies now allow manufacturers to inspect every item in real-time, reducing defects and increasing production efficiency.
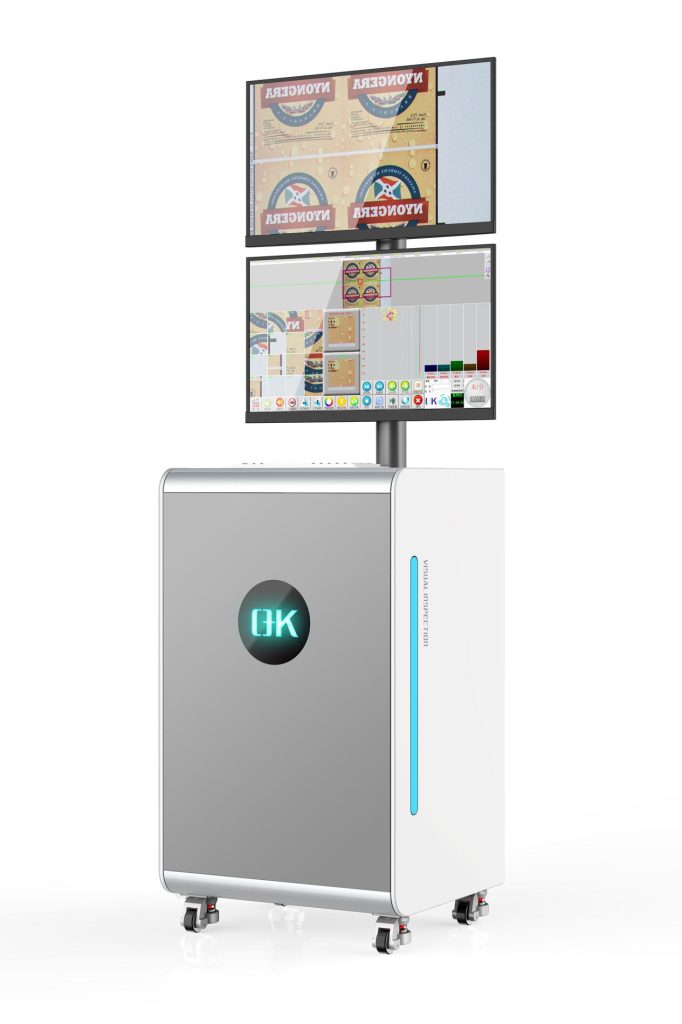
Evolution of Vision-based 100% Inspection Systems
The journey of vision inspection systems began with simple image-capture and analysis technologies. Early systems relied on fixed cameras and basic algorithms, capable of detecting only large, overt defects. With advancements in sensor technology, machine learning, artificial intelligence, etc, today’s vision-based 100% inspection systems are far more accurate, flexible, and capable of detecting even subtle imperfections.
Key Technologies in Vision-based 100% Inspection Systems
The key technologies in vision-based 100% inspection systems are transforming how industries achieve comprehensive and real-time quality assurance.
1. High-Resolution Imaging and 3D Vision
- High-Resolution Cameras: Advanced high-resolution cameras capture intricate details, enabling the detection of micro-defects and small deviations that traditional cameras might miss.
- 3D Vision Technology: Adds depth perception, which is especially useful for complex shapes and surface variations. This enables precise measurement of object dimensions and geometry, essential for industries like electronics and automotive.
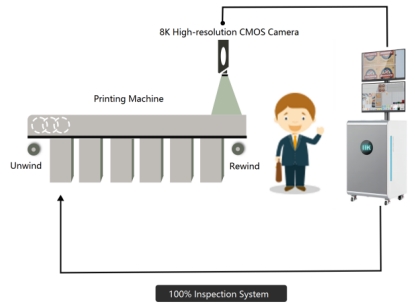
2. Artificial Intelligence (AI) and Machine Learning (ML)
- AI Algorithms: These are trained on large datasets to identify and classify defects accurately. Over time, AI can learn and improve, adapting to recognize new defect types, boosting reliability.
- Machine Learning Models: These models continuously refine themselves, enhancing detection rates and reducing false positives. ML is also applied in predictive quality management, allowing for proactive adjustments to production processes.
3. Edge Computing for Real-Time Processing
- Local Data Processing: Instead of sending data to a centralized server, edge computing allows inspection data to be processed locally. This minimizes latency, enabling vision inspection systems immediate defect detection even on high-speed production lines.
- Enhanced Efficiency: By processing data close to the source, edge computing reduces network dependency and enhances overall system reliability, crucial for time-sensitive manufacturing environments.
4. Multispectral and Hyperspectral Imaging
- Beyond Visible Spectrum: These imaging techniques extend inspection beyond visible light, capturing data across various wavelengths (e.g., UV or infrared). This makes it possible to detect internal defects, contaminants, or subtle material inconsistencies that might be invisible to standard vision systems.
- Precision in Material Analysis: Especially valuable in food, pharmaceuticals, and textile industries, hyperspectral imaging can differentiate materials based on chemical composition and physical characteristics, ensuring high-quality outputs.
5. Advanced Lighting Systems
- Adaptive Lighting: Modern systems use adjustable lighting to control intensity, direction, and angle, ensuring optimal conditions for capturing images. This flexibility minimizes shadows and highlights specific product features, enhancing defect visibility.
- Structured Lighting: Using structured patterns projected onto objects, this method enhances 3D image capture, improving the inspection of surface textures, contours, and depth.
6. Robotic Integration for Dynamic Inspection
- Robotic Vision Systems: Robotic arms equipped with cameras can adjust angles, lighting, and focus in real time, offering flexibility to inspect complex and large products.
- Automated Adaptation: Robots can dynamically adapt inspection strategies, such as adjusting camera angles based on product orientation or moving the inspection point to accommodate specific inspection criteria.
7. Deep Learning for Defect Classification
- Deep Neural Networks: These advanced models are capable of understanding complex image patterns and can differentiate between types of defects with remarkable accuracy.
- Automated Defect Categorization: Deep learning enables the system to classify defects (e.g., cracks, color mismatches, misalignments) and sort products accordingly, making it easier to analyze production quality trends.
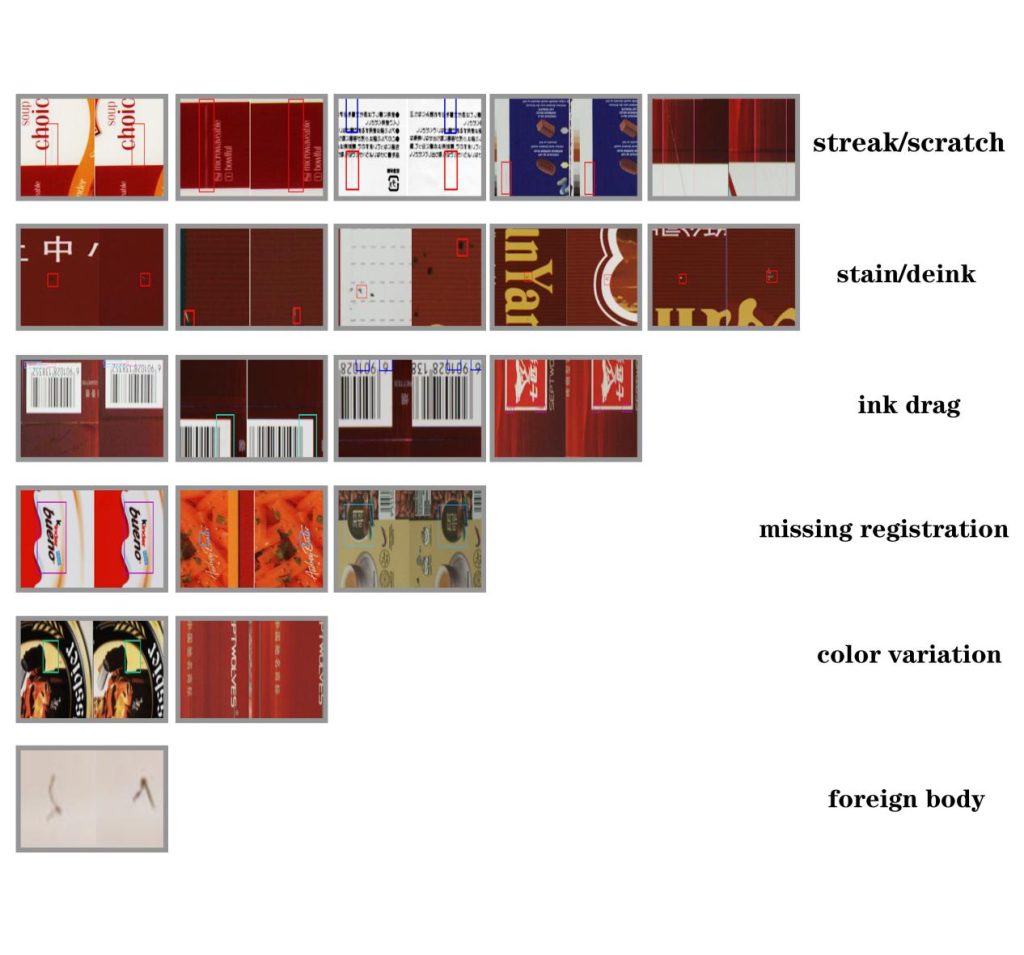
Applications Across Industries of Vision-based 100% Inspection Systems
Vision-based 100% inspection systems have proven invaluable across a wide array of industries, offering detailed quality assurance that helps ensure safety, consistency, and compliance.
1. Automotive Industry
- Component Inspection: Vision 100% inspection systems systems inspect critical components like engines, transmission parts, and brake systems, identifying microscopic defects that could impact vehicle safety or longevity.
- Surface Quality Control: Detecting surface scratches, dents, and imperfections on painted or coated automotive parts to maintain high aesthetic and quality standards.
- Weld Quality Verification: Systems check the quality of welds on assemblies, ensuring structural integrity and alignment, which are essential for safety in vehicles.
2. Electronics and Semiconductor Manufacturing
- PCB Inspection: Vision systems detect defects in printed circuit boards (PCBs), such as missing components, solder defects, and misalignments, ensuring proper functionality.
- Micro-Crack Detection: Advanced imaging identifies micro-cracks and flaws in semiconductor wafers and chips, preventing device failures in the field.
- Connector and Solder Joint Inspection: These systems ensure proper placement and connection of components, essential for reliability in electronic devices.
3. Food and Beverage Industry
- Foreign Contaminant Detection: Multispectral imaging detects contaminants like metal, glass, or plastic particles in food products, safeguarding consumer health.
- Packaging and Label Verification: Vision web inspection systems verify that labels are correctly applied, legible, and include necessary information, ensuring compliance with regulations.
- Product Consistency: Ensuring product consistency by checking size, shape, and color to meet quality standards, especially for baked goods, snacks, and beverages.
4. Pharmaceutical Industry
- Tablet and Capsule Inspection: Vision 100% inspection systems systems detect defects in shape, size, and surface quality of tablets and capsules, ensuring each product meets quality standards.
- Packaging Integrity: Ensures blister packs, vials, and bottles are sealed properly, preventing contamination and ensuring product efficacy.
- Label Accuracy and Traceability: Verifying that drug information, barcodes, and batch numbers on labels are accurate for traceability and regulatory compliance.
5. Textile and Apparel Industry
- Fabric Quality Control: Vision-based systems identify defects in fabric such as tears, color inconsistencies, and weave errors, maintaining quality in clothing and upholstery production.
- Pattern Alignment: Ensures patterns on fabrics are correctly aligned and consistent, especially for high-value garments and designer textiles.
- Stitch Quality and Measurement: Checks the quality of stitching on apparel, looking for loose threads or missed stitches, and measures dimensions to meet size specifications.
6. Packaging and Printing Industry
- Label and Barcode Verification: Inspects labels and barcodes for accuracy, readability, and proper placement, ensuring traceability and compliance.
- Print Quality Inspection: Vision printing inspection systems detect defects like smudges, misalignments, and color deviations, maintaining brand quality and compliance.
- Seal and Closure Integrity: Ensures the quality of seals and closures on packages, critical for preserving product freshness, safety, and appearance.
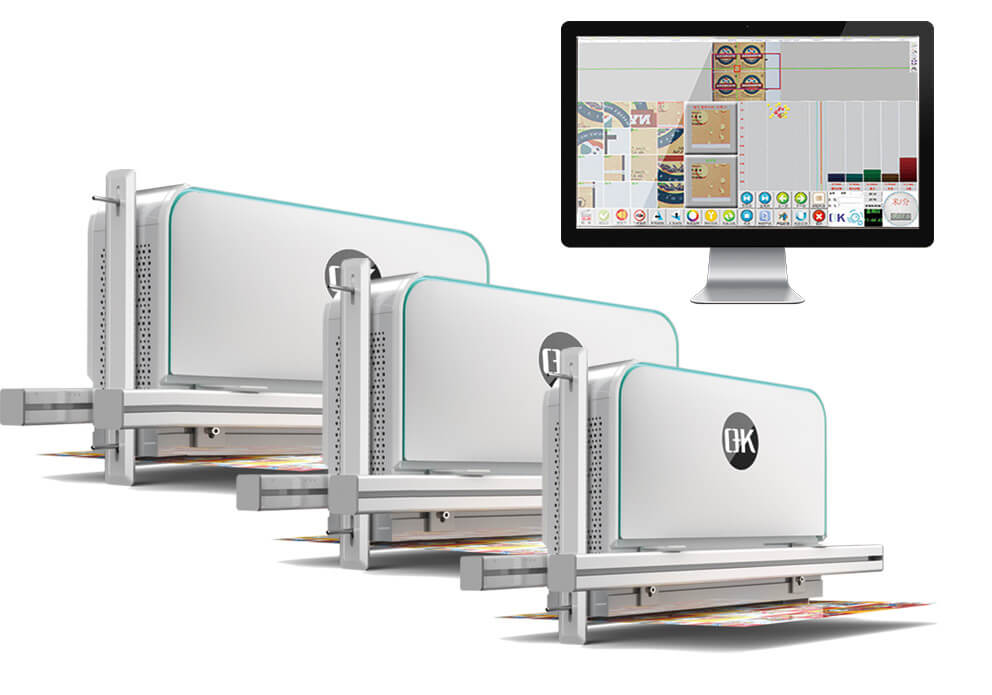
7. Metal and Steel Industry
- Surface Defect Detection: Web video inspection systems identify surface defects on metals, such as cracks, corrosion, and scratches, ensuring the integrity of metal parts and structures.
- Dimensional Accuracy: For components like sheets, rods, and pipes, vision 100% inspection systems verify dimensional accuracy to meet specifications.
- Weld Inspection: Inspects welds on metal assemblies, ensuring weld quality and structural integrity in industries such as construction, automotive, and aerospace.
8. Plastic and Rubber Manufacturing
- Defect Detection in Molded Parts: Vision-based 100% inspection systems identify flaws in injection-molded plastic and rubber parts, such as surface defects, warping, and incomplete mold filling.
- Color and Consistency Check: Ensures that products meet specific color and finish requirements, essential for industries like automotive and consumer goods.
- Size and Shape Verification: Measures the dimensions of plastic and rubber components to confirm they match design specifications.
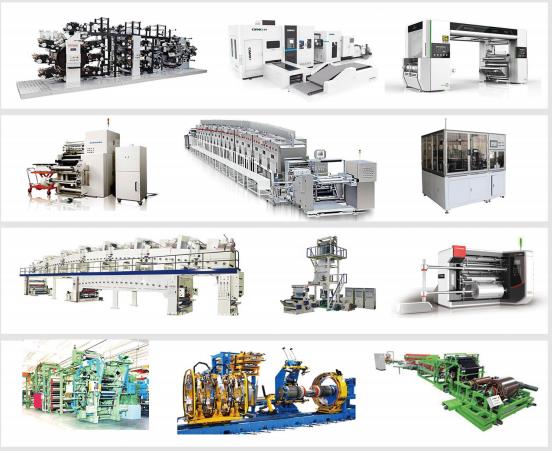
Challenges and Future Directions in Vision-based 100% Inspection Systems
This chart summarizes the primary challenges and future advancements expected in vision-based 100% inspection systems, driving their evolution in quality control across industries.
Aspect | Challenges | Future Directions |
Accuracy & Precision | Difficulty in detecting subtle defects and complex patterns in diverse products | Enhanced AI and ML algorithms for improved defect recognition and pattern analysis |
Speed of Inspection | Balancing high-speed inspections with image processing accuracy on fast-moving production lines | Adoption of edge computing and faster processors for real-time, high-speed data processing |
Lighting & Environmental Sensitivity | Variability in lighting, reflections, and environmental conditions affecting image capture | Development of adaptive lighting and advanced imaging techniques that adjust to different environments |
Complex Defect Identification | Challenges in identifying complex or rare defects, especially in intricate components | Use of deep learning models trained on extensive defect libraries and synthetic defect simulations |
Data Volume & Processing | Large volumes of data strain storage and processing capabilities, especially in continuous operations | Edge and cloud hybrid storage solutions with advanced data compression and real-time analytics |
Integration with Other Systems | Difficulty in integrating inspection data with existing quality control and production management systems | Improved interoperability and standardized protocols for seamless integration with Industry 4.0 systems |
Cost & Maintenance | High initial costs and maintenance expenses, especially for advanced inspection setups | Development of cost-effective 100% inspection system with reduced maintenance requirements |
User Training & Expertise | Requires skilled personnel to operate and interpret inspection results | User-friendly interfaces, augmented reality (AR) support, and automated reporting for ease of use |
Scalability & Adaptability | Limited flexibility to scale for varying product sizes and types | Design of flexible, scalable systems adaptable to different products and production scales |
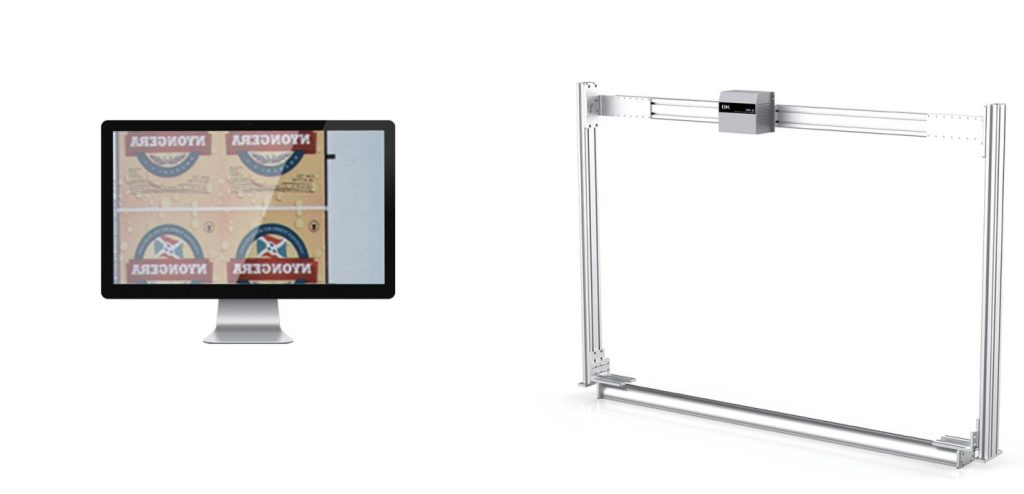
Overall, vision-based 100% inspection systems provide comprehensive and reliable inspection solutions across a range of industries for quality assurance and operational efficiency.