Why Use a Closed-loop Tension Control System for Precise Tension Management
Table of Contents
In industrial processes where tension control is critical, such as in textile manufacturing, paper production, and metal processing, maintaining precise tension control is essential for product quality and operational efficiency. A closed-loop tension control system has emerged as a sophisticated solution to address these needs. Unlike open-loop systems, closed-loop tension control offers dynamic, real-time adjustments, ensuring accuracy and reliability.
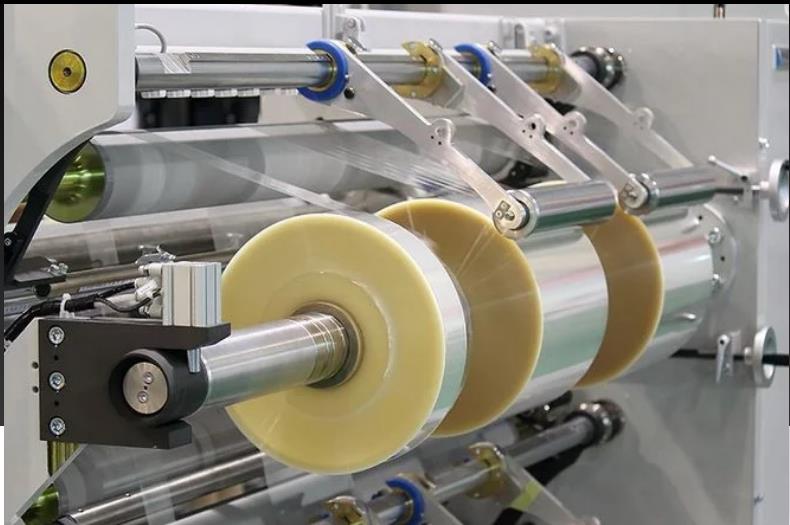
Key Components of a Closed-Loop Tension Control System
The key components of a closed-loop tension control system are designed to work together to maintain precise tension in materials during processes such as winding, unwinding, or web handling.
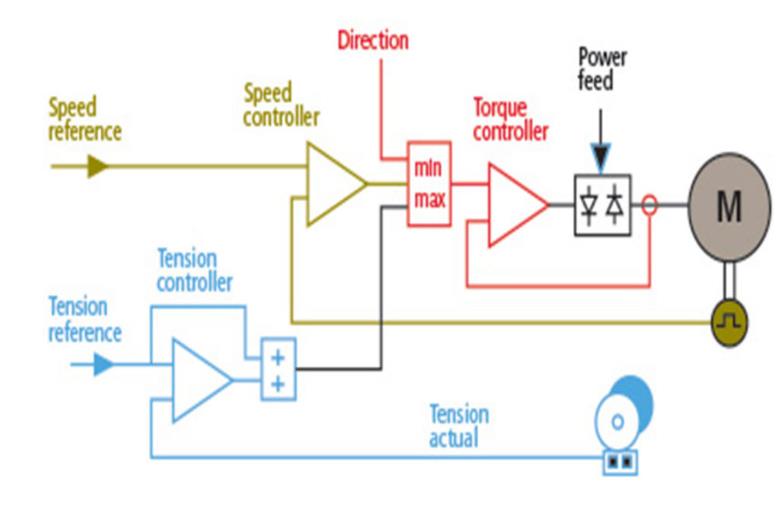
1. Tension Sensors (Load Cells)
These tension sensors are responsible for measuring the actual tension in the material. They convert mechanical tension into electrical signals that can be processed by the controller. Common types include load cells, dancers, and strain gauges.
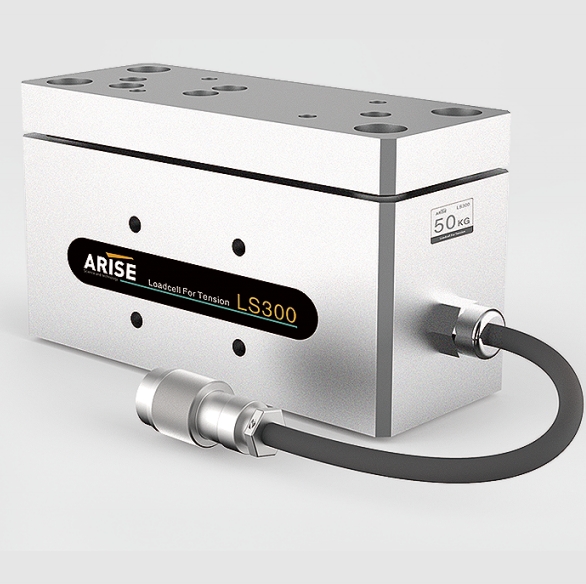
2. Controller
The controller is the brain of the system. It receives the tension data from the sensors and compares it to the desired tension (setpoint). If there’s a deviation, the automatic tension controller sends correction signals to the actuators to adjust the tension. PLCs or specialized tension controllers are typically used.
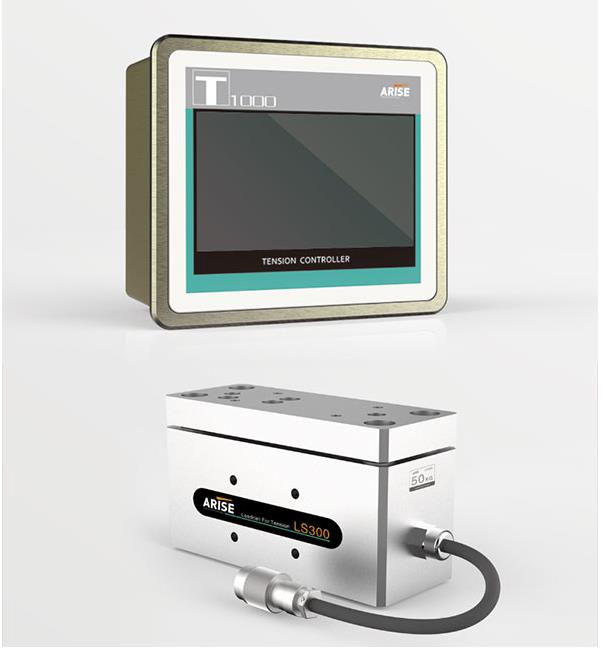
3. Actuators (Brakes, Clutches, Motors)
Actuators are mechanical devices that adjust the tension based on the feedback from the controller. Common actuators include:
- Brakes: Apply resistance to the material to reduce tension.
- Clutches: Engage or disengage to modify the tension.
- Motors: Speed up or slow down to increase or decrease tension.
4. Tension Setpoint Adjustment
This is the mechanism or interface where the operator sets the desired tension level. It can be adjusted manually or through an automated system depending on the application.
5. Feedback Loop
The feedback loop connects the sensors, controller, and actuators in real time. The system continuously measures the actual tension, compares it to the setpoint, and adjusts accordingly. This feedback mechanism ensures that the tension stays within the desired range.
6. Power Supply
The actuators, sensors, and controller need a reliable power source to function effectively. It may vary depending on the system design and industry standards.
7. Web Path Rollers
Rollers guide the material through the system, and some may include tension measurement features like tension-sensing rollers. Their friction and alignment can also affect overall tension.
How a Closed-Loop Tension Control System Works
This flow shows how feedback and real-time adjustments are made to ensure precise tension control in the system.
Steps | Description |
1. Tension Sensing | Sensors (e.g., load cells, dancer arms) measure the actual tension in the material as it moves through the process. |
2. Feedback to Controller | The sensors send real-time data (tension readings) to the controller. |
3. Comparison to Setpoint | The controller compares the actual tension to the pre-set desired tension (setpoint) and identifies any deviation (error). |
4. Error Correction Signal | If there is an error, the controller generates a correction signal based on the difference between the actual tension and the setpoint. |
5. Actuator Adjustment | The correction signal is sent to actuators (e.g., brakes, clutches, motors), which adjust the tension by either increasing or decreasing force on the material. |
6. Continuous Monitoring | The system continuously monitors the tension, repeating the process to maintain the desired level of tension throughout the operation. |
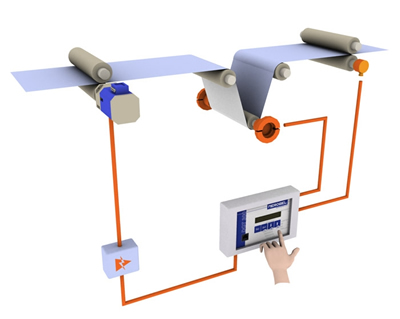
Advantages of a Closed-Loop Tension Control System
- Increased Precision: Closed-loop systems provide high precision in tension control, reducing the risk of defects caused by tension variations. This precision is crucial for industries where product quality is closely tied to tension consistency.
- Improved Efficiency: By maintaining optimal tension, closed-loop systems minimize material waste and downtime. This efficiency translates to cost savings and improved productivity.
- Real-Time Adjustments: The ability to make real-time adjustments allows closed-loop systems to respond quickly to changes in the process or material, ensuring that the tension remains within the desired range.
- Enhanced Process Stability: Closed-loop control contributes to process stability by continuously monitoring and correcting tension variations. This stability reduces the likelihood of process disruptions and enhances overall performance.
- Reduced Operator Intervention: With automated adjustments based on real-time feedback, closed-loop systems reduce the need for manual intervention, allowing operators to focus on other critical tasks.
Applications of a Closed-Loop Tension Control System
- Printing Industry: In printing presses, maintaining consistent tension in paper or other substrates ensures accurate ink registration and print quality. A closed-loop system prevents wrinkles, tears, or misalignment during high-speed printing operations.
- Packaging Industry: Tension control is essential for handling materials such as plastic films, foils, and packaging paper. A closed-loop system helps prevent stretching, tearing, or misfeeding of materials during packaging processes like sealing, labeling, or wrapping.
- Textile Manufacturing: In fabric production, maintaining constant tension prevents stretching or deformation of the textile fibers. Closed-loop systems are used in processes like weaving, knitting, and dyeing to ensure uniformity and reduce material waste.
- Paper and Pulp Industry: Consistent tension is vital during the winding and unwinding of paper rolls, especially in large-scale papermaking operations. A closed-loop system helps in maintaining even tension, preventing breaks, wrinkles, or excessive slack.
- Metals and Foil Processing: In processes like rolling, cutting, or coating of thin metal strips and foils, tension control is crucial. A closed-loop tension system ensures smooth handling without stretching, tearing, or material warping during winding or feeding.
- Plastic Film Extrusion: In plastic film manufacturing, maintaining proper tension ensures uniform thickness and prevents defects like wrinkling or stretching. A closed-loop system maintains the correct tension during extrusion, cooling, and winding stages.
- Converting Industry: In industries that involve converting materials like paper, film, or foil into specific shapes or products (e.g., slitting, laminating), tension control ensures precise cutting and positioning without material distortion.
- Coating and Laminating Processes: Closed-loop tension control systems are used to regulate tension in multilayer materials during coating or laminating processes. This ensures that the layers bond correctly without bubbles, wrinkles, or misalignment.
- Film and Sheet Manufacturing: In the production of polymer films or sheets, a closed-loop system controls the tension to maintain uniformity and avoid defects like sagging, stretching, or breakage during the extrusion and winding process.
- Battery Manufacturing: In processes involving thin electrode films or separators, such as in lithium-ion battery production, tension control is crucial for ensuring the layers are aligned and undamaged during the winding or stacking of battery components.
- Aerospace and Composite Materials: Manufacturing composite materials and advanced materials used in aerospace applications requires precision tension control during processes like prepreg layup and winding, where tension consistency affects material integrity.
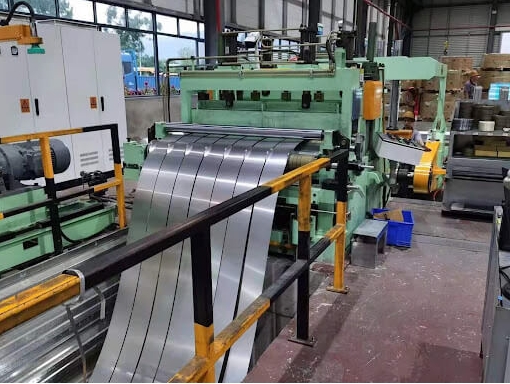
Challenges and Considerations in Optimizing a Closed-Loop Tension Control System
This chart highlights key challenges and practical considerations for optimizing closed-loop tension control systems.
Challenge | Description | Consideration |
1. Accuracy of Tension Measurement | Variations in sensor calibration and mechanical issues may affect tension accuracy. | Use high-quality, calibrated sensors and regularly maintain them. |
2. Material Properties | Different materials have varying elasticity, stiffness, and thickness, impacting tension control. | Tailor system settings to specific material properties; adjust tension limits for sensitive materials. |
3. Speed Variation | Sudden changes in material speed can cause tension fluctuations. | Use responsive controllers that adapt to speed changes in real time. |
4. Dynamic Response and Stability | Delayed response can lead to overshoot, oscillations, or tension instability. | Implement well-tuned PID control for smooth, stable response and fast correction of tension errors. |
5. System Inertia and Friction | Mechanical components have inertia and friction that may delay tension adjustments. | Use low-inertia, low-friction actuators; incorporate predictive control algorithms to compensate for system lag. |
6. Roll Diameter Changes | Changing roll diameters affect tension as winding or unwinding progresses. | Implement automatic compensation for roll diameter variations to maintain consistent tension. |
7. Environmental Conditions | Temperature, humidity, and other environmental factors can impact material behavior and sensor accuracy. | Design the system to account for environmental variations; use sensors that perform well under varying conditions. |
8. System Integration | Integrating the tension control system with existing equipment and controls may be complex. | Ensure compatibility through standardized communication protocols and verify integration with other components. |
9. Maintenance and Calibration | Mechanical wear and sensor drift can degrade system performance over time. | Regularly calibrate sensors and inspect mechanical parts to ensure optimal system performance. |
10. Cost and Complexity | High-precision systems can be expensive and complex to operate and maintain. | Balance cost and complexity against production quality needs; invest in high-precision systems where necessary. |
11. Human-Machine Interface (HMI) | Poor interface design can lead to operator errors and slow response to issues. | Design user-friendly interfaces with clear visualizations and provide operator training for effective use. |
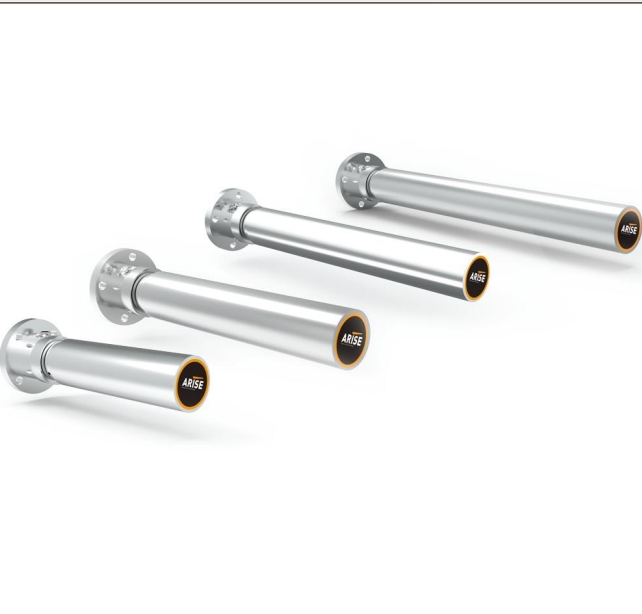
To sum up, through continuously monitoring and adjusting tension in real-time, closed-Loop tension control systems address the challenges associated with maintaining consistent tension and contribute to improved product quality and operational efficiency. As industries continue to demand higher precision and automation, closed-loop tension control will remain a key technology for maintaining optimal tension in manufacturing processes.