Why Choose Printing Inspection System for Maintaining Color Consistency and Accuracy
Whether you work in commercial printing, packaging, or graphic design, it’s critical that the colors on your printed goods match your expectations. Obtaining this uniformity and accuracy can be difficult due to a variety of factors such as differences in printing equipment, ink formulations, and climatic conditions. The integration of printing inspection system, on the other hand, has revolutionized the process of monitoring and maintaining color quality. This article will look at the important role of printing inspection systems in maintaining color consistency and accuracy in the world of printing.
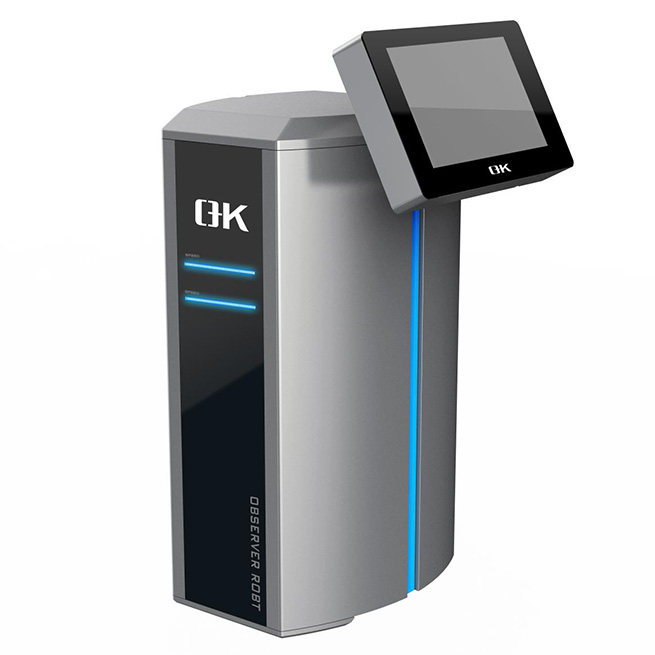
The Importance of Color Consistency and Accuracy
Consistent and accurate color reproduction in printing is crucial for several reasons:
Brand Identity
Color consistency across all brand products, from business cards to banners, is critical for developing a recognizable and unified brand identity. When customers see a specific color associated with a brand, they immediately connect it with the products or services offered.
Client Expectations
Client satisfaction is dependent on meeting or exceeding client expectations for color fidelity. Clients frequently have certain brand guidelines that must be followed, and any variation can result in disappointment.
Quality Assurance
High-quality printed materials require accurate color reproduction. Color variations can make even the most professionally designed artwork appear unprofessional.
Cost Efficiency
Color discrepancies can result in lead to wasted materials, reprints, and additional costs. Color uniformity decreases these costs while increasing profitability.
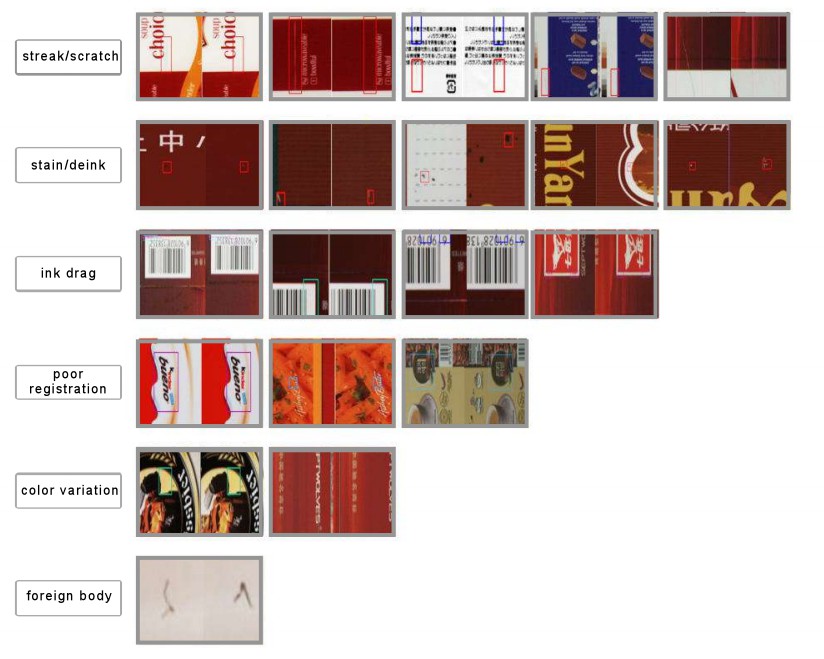
Regulatory Compliance
Adherence to stringent color standards is critical in several industries, such as pharmaceuticals and food packaging, for meeting legal criteria and maintaining product safety.
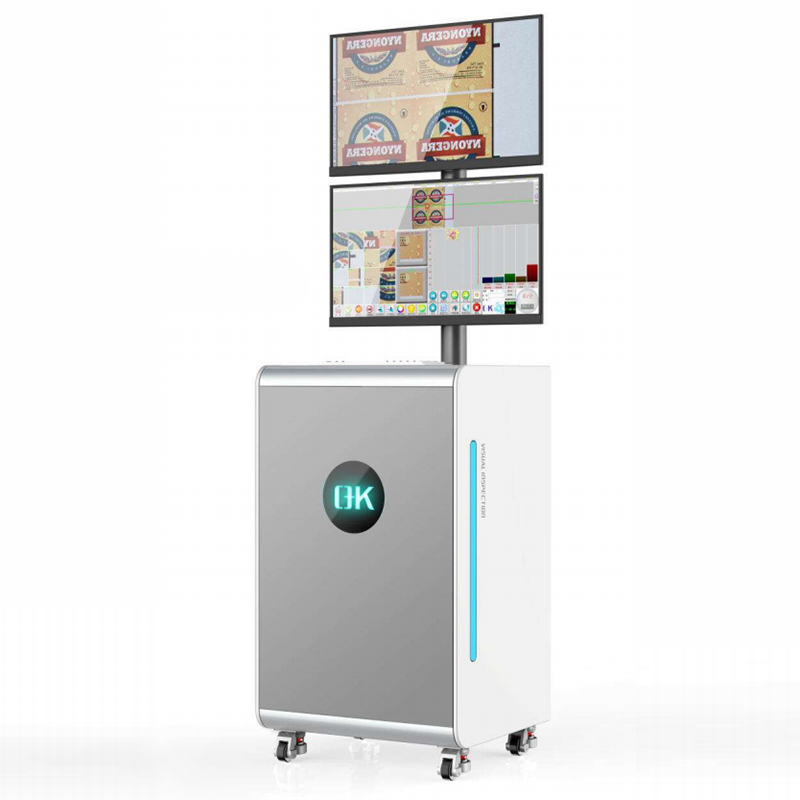
Key Challenges in Achieving Color Consistency and Accuracy
Device Variability
Colors may be interpreted and reproduced differently by different printing devices, such as printers and monitors.
Ink and Paper Variability
In the printing industry, variations in ink formulations, paper or substrate characteristics, and ink drying rates can affect how colors appear on printed materials. Different combinations of inks and substrates can lead to color shifts.
Environmental Factors
Environmental factors, such as temperature, humidity, and air quality, can influence the appearance of colors. For example, high humidity may cause ink to spread differently on paper, affecting the final color output.
Workflow Complexity
Complex production workflows often involve multiple software applications, devices, and production stages. These workflows can introduce inconsistencies in color output, making it challenging to maintain accuracy.
Material Aging
Due to exposure to light, air, or other environmental variables, materials such as fabrics, paints, and printed materials can age and change color over time. Color shifts and inconsistencies can result from aging.
Color Matching Across Media
t can be difficult to provide consistent color fidelity across multiple media, such as print, digital displays, and physical objects. Each media has its own color space and set of constraints.
Production Speed
Due to the rapid production cycle, color constancy can be challenging to maintain in high-speed manufacturing processes. Color accuracy necessitates quick modifications.
Cost Constraints
Achieving high levels of color consistency and accuracy often requires the use of advanced equipment and materials. Meeting these requirements can be costly, and budget constraints may limit the ability to invest in top-tier solutions.
The Role of Printing Inspection Systems in Maintaining Color Consistency and Accuracy
Printing inspection systems are sophisticated solutions that meet the aforementioned difficulties and play a critical role in ensuring color consistency and accuracy.
Color Measurement and Verification
Colors are measured and verified using advanced color measurement technologies such as spectrophotometers and colorimeters. They compare the actual colors to the intended values and look for differences.
Ink Density Control
Ink density is monitored and controlled by printing inspection devices, ensuring that the correct amount of ink is applied. Color differences caused by over-inking or under-inking are reduced.
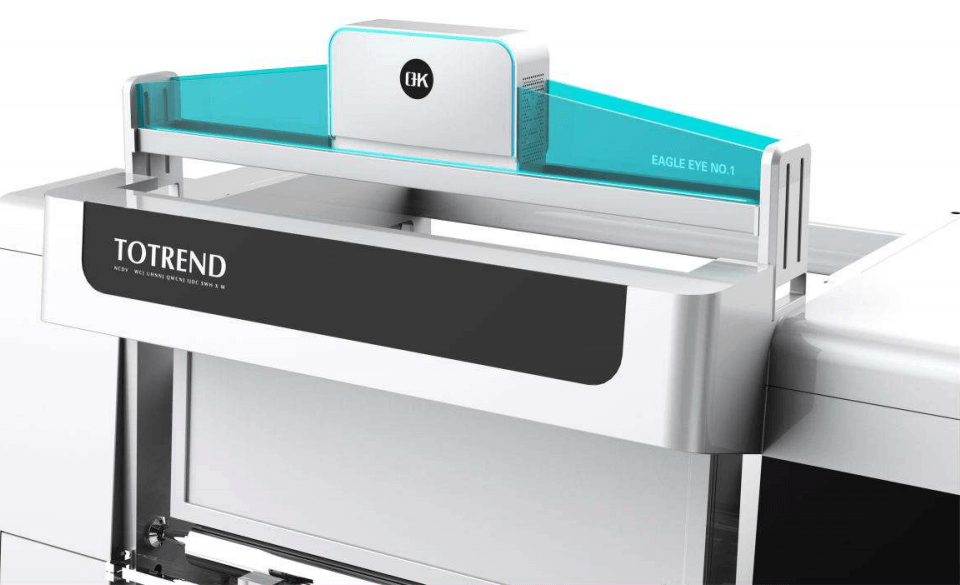
Inline Monitoring
Many systems are integrated directly into the printing process, enabling real-time feedback and modifications to preserve color consistency during production.
Quality Control
The algorithms adopted by printing inspection system can detect additional quality flaws, such as streaks, misrepresentation, and missing text or images, in addition to color.
Compliance with Industry Standards
Some systems are designed to comply with industry-specific standards and regulations, such as ISO standards for color accuracy in printing.
Data and Reporting
Printing inspection systems provide data and reporting tools for analyzing and documenting color consistency over time. This allows for process improvement and facilitates ongoing quality control.
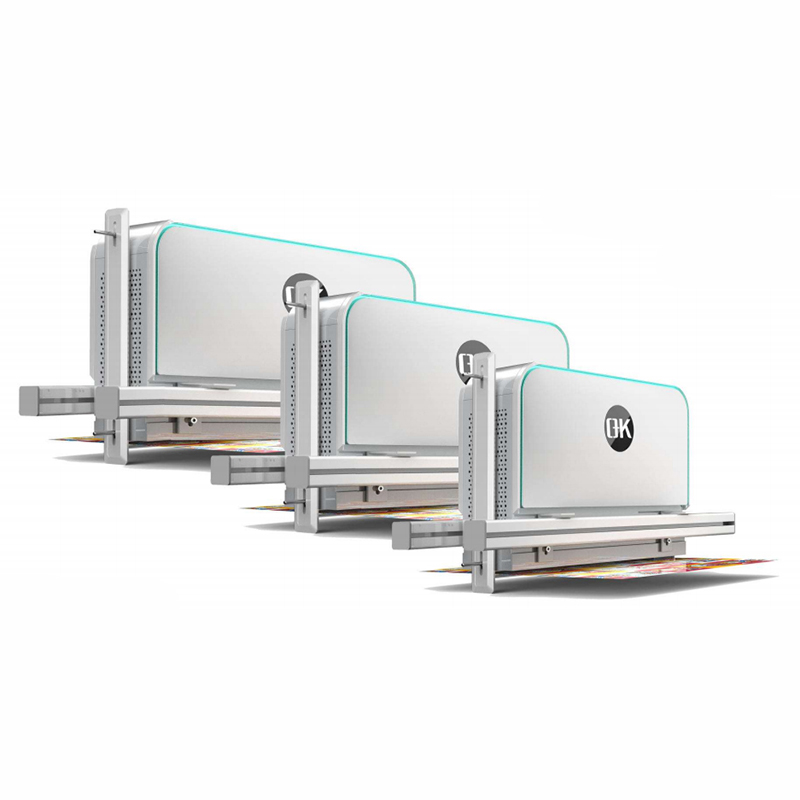
Conclusion
The integration of printing inspection systems has substantially enhanced the printing industry’s capacity to maintain color constancy and precision. These systems provide a variety of tools and features to solve the issues presented by device variability, ink and substrate variances, environmental influences, and complex workflows. Businesses may guarantee that their printed products satisfy the expectations of their clients and conform to industry standards by implementing color measurement and verification, ink density management, and inline monitoring. Finally, these solutions contribute to improved brand identity, regulatory compliance, waste reduction, and overall printing quality. Printing inspection systems have become vital tools for individuals and organizations aiming to offer high-quality printed documents in a world where color constancy is critical.