Why Choose Automatic Web Guiding Calibration for Multi-layered Materials
Table of Contents
Multi-layered materials, in particular, pose significant challenges to web guiding systems due to their complex structure and varying thickness. Automatic web guiding calibration offers a precise solution, ensuring that these materials move in a controlled manner during processing. This article explores the significance of automatic web guiding calibration for multi-layered materials, how it works, its benefits and best Practices for Implementing it.
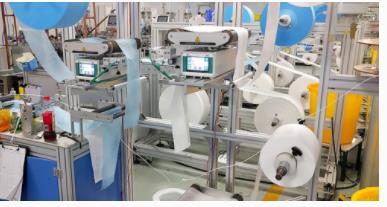
The Significance of Automatic Web Guiding Calibration for Multi-layered Materials
Challenges in Handling Multi-Layered Materials
Multi-layered materials, often composed of films, foils, or composite fabrics, present unique challenges in web guiding. These include:
- Layer Slippage: The individual layers in a multi-layered material can slip against each other during movement, which can cause the layers to misalign.
- Thickness Variations: Different layers may have different thicknesses, leading to inconsistent tension and misalignment if not properly calibrated.
- Material Stretching: Some multi-layered materials, particularly films, can stretch under tension, requiring dynamic adjustments during processing.
- Increased Sensitivity: The added layers increase the overall material sensitivity, making it more difficult to control the movement accurately without calibration.
Without automatic calibration, these challenges can lead to inefficiencies, poor-quality products, and downtime during production.
What is Web Guiding Calibration
Web guiding calibration refers to the process of adjusting and fine-tuning the alignment of a web (a continuous strip of material) as it moves through processing equipment such as rollers, printers, and laminators. The primary goal of web guiding is to ensure that the material remains aligned and free from tension inconsistencies that could lead to defects, jams, or product quality issues.
In the case of multi-layered materials, each layer may have different properties, such as varying thickness, stretchability, or weight. This makes it essential to calibrate the web guide system automatically for optimal alignment, taking into account the material’s characteristics to prevent misalignment and ensure smooth processing.
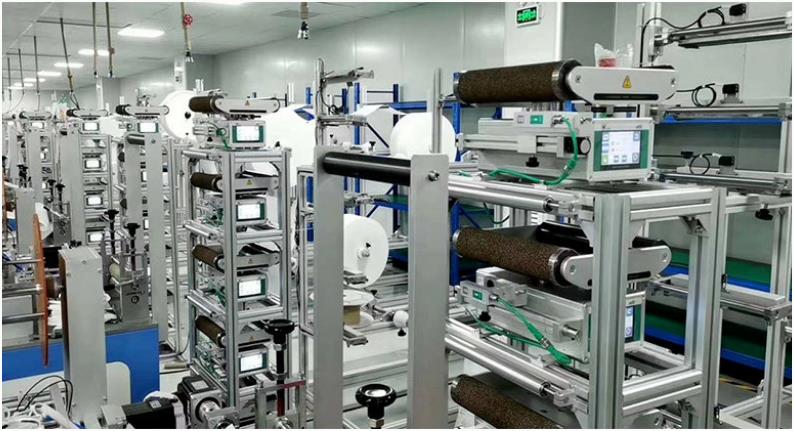
How Does Automatic Web Guiding Calibration Work
Automatic web guiding calibration is a sophisticated process used to maintain proper alignment of materials (or webs) as they move through industrial machinery.
1. Sensors and Detection Systems
The process begins with the deployment of various sensors that monitor the position, speed, and tension of the web as it moves through the system. These sensors detect any deviations from the desired position or alignment.
- Edge Sensors: These edge web guide sensors track the position of the material’s edge, ensuring it stays within the defined boundary of the machinery.
- Laser Sensors: Used for detecting the exact location of the web’s centerline, laser sensors provide high precision and are capable of detecting very small misalignments.
- Vision Systems: Cameras or imaging systems can capture real-time visuals of the web, which are analyzed for any wrinkles, misalignments, or defects in the material.
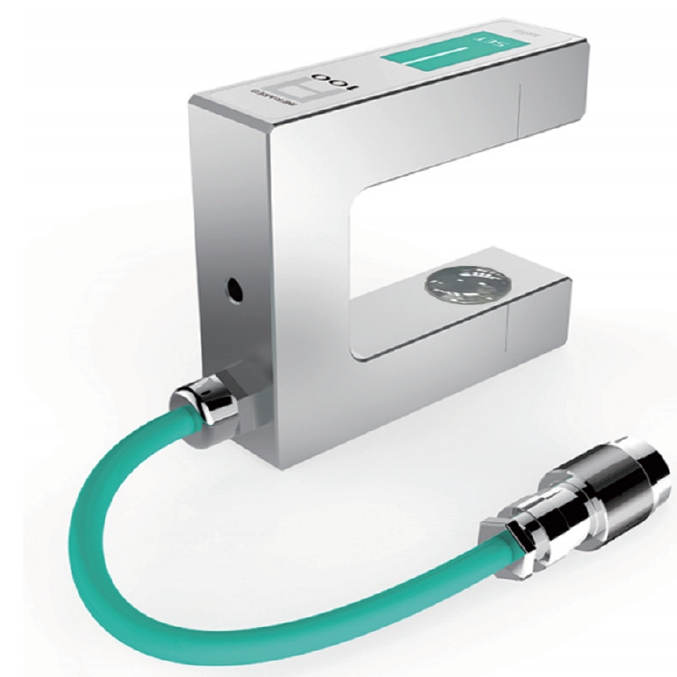
2. Real-Time Alignment Adjustments
Once the sensors detect any misalignment or deviation, the system makes real-time adjustments to correct the position of the web. This process happens continuously during the production cycle, ensuring that the material stays aligned.
- Actuators: These are mechanical components that adjust the position of rollers or guides in response to the sensor data. The web guide actuators can shift the web horizontally or adjust tension to bring the material back into alignment.
- Motorized Rollers: The rollers can be adjusted in response to feedback from the sensors, ensuring the web remains at the correct angle, preventing drifting or skewing.
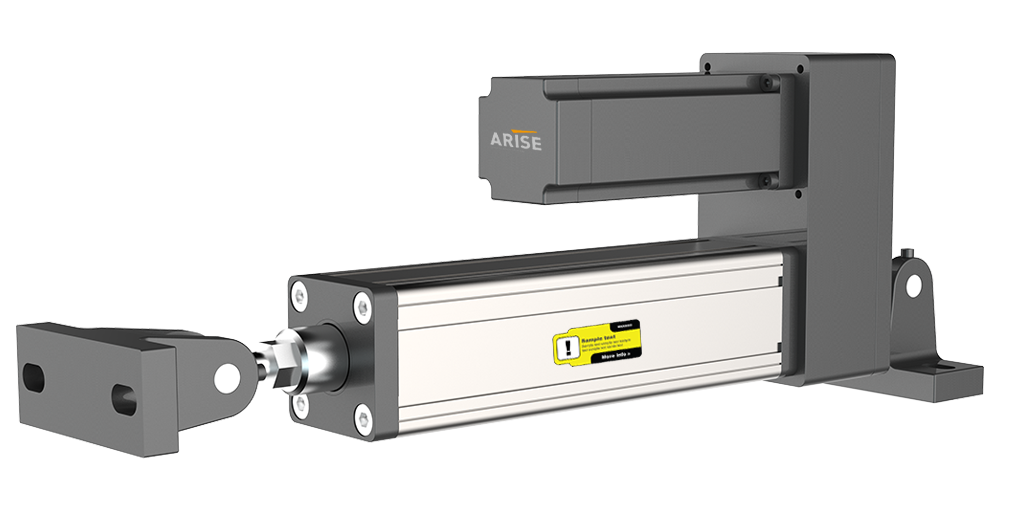
3. Layer-Specific Calibration (for Multi-Layered Materials)
When working with multi-layered materials, it is essential to ensure that each layer moves correctly without slipping or misaligning. Automatic web guiding systems incorporate algorithms that can handle the complexity of multi-layered materials:
- Independent Layer Control: Each layer of the material is adjusted independently based on its specific properties (e.g., thickness, elasticity). This prevents one layer from moving out of sync with another.
- Compensation for Slippage: Sensors detect layer slippage and adjust the tension and position of each layer, preventing uneven movement and ensuring precise alignment.
4. Automatic Feedback Loop
The automatic calibration process operates through a closed-loop feedback system. This means that after each adjustment is made, the system continuously checks for misalignment and corrects it again if necessary. This dynamic process ensures that the material remains aligned throughout the entire production run.
- Constant Monitoring: The system works 24/7, constantly monitoring the web’s alignment and making adjustments as needed. This reduces the need for manual intervention.
- Real-Time Adjustments: Even if there are unexpected variations in material properties, the system can make instantaneous adjustments without halting production.
5. Integration with Other Systems
Automatic web guiding calibration does not operate in isolation. It often works in conjunction with other automation systems to ensure optimal material handling:
- Tension Control Systems: These systems ensure the material is under the correct tension, which is crucial for preventing wrinkling, stretching, or tearing. The web guiding system ensures that the tension is evenly distributed across the entire web.
- Speed Monitoring: The speed at which the web moves can affect its alignment. The web guiding system adjusts to changes in speed to maintain constant alignment.
- Edge Tracking: Some systems incorporate edge tracking features to precisely track the material’s edges to prevent it from drifting from side to side.
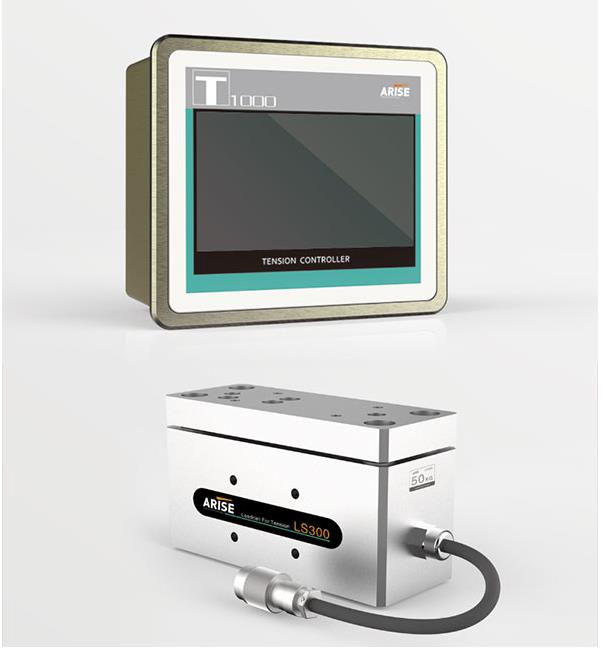
6. Calibration Algorithms
The software behind the automatic calibration system uses complex algorithms to process the sensor data and make necessary adjustments. These algorithms are specifically designed to handle different material types, including multi-layered and stretchable materials.
- Real-Time Data Processing: The algorithms process real-time data from sensors and make split-second decisions on adjustments.
- Pattern Recognition: Advanced algorithms can recognize patterns of misalignment or tension shifts and predict the necessary adjustments before a significant problem occurs.
- Adaptive Control: As different materials are introduced into the system, the calibration system can adapt, learning from past adjustments to improve future performance.
7. Continuous Calibration for Complex Materials
For materials that are sensitive or have complex properties (such as multi-layered films or textiles), continuous calibration ensures the web remains aligned throughout the entire production process. This is especially important when materials have inconsistent elasticity, varying thickness, or surface properties that can influence alignment.

Benefits of Automatic Web Guiding Calibration for Multi-Layered Materials
- Improved Product Quality: By ensuring that multi-layered materials remain perfectly aligned, web guiding calibration prevents defects like wrinkles, overlaps, and misprints, resulting in higher-quality finished products.
- Enhanced Efficiency: Automatic calibration reduces the need for manual adjustments, saving time and reducing the likelihood of errors. This leads to higher throughput and a more streamlined production process.
- Reduced Material Waste: With better alignment and fewer production errors, the amount of material wasted due to misalignment or defects is minimized.
- Cost-Effective: By eliminating the need for manual calibration and reducing downtime, the overall costs of production are lowered. Additionally, consistent alignment reduces wear and tear on machinery, leading to less frequent maintenance.
- Faster Setup Times: Automatic web guiding calibration allows for quicker transitions between different materials or product lines. Operators no longer need to spend time manually adjusting settings, enabling faster setup times.
- Adaptability to Complex Materials: Multi-layered materials with varying properties (such as thickness, stretch, and weight) can be accurately processed without requiring special handling. The automatic web guide system equipment adapts to these materials’ unique characteristics.
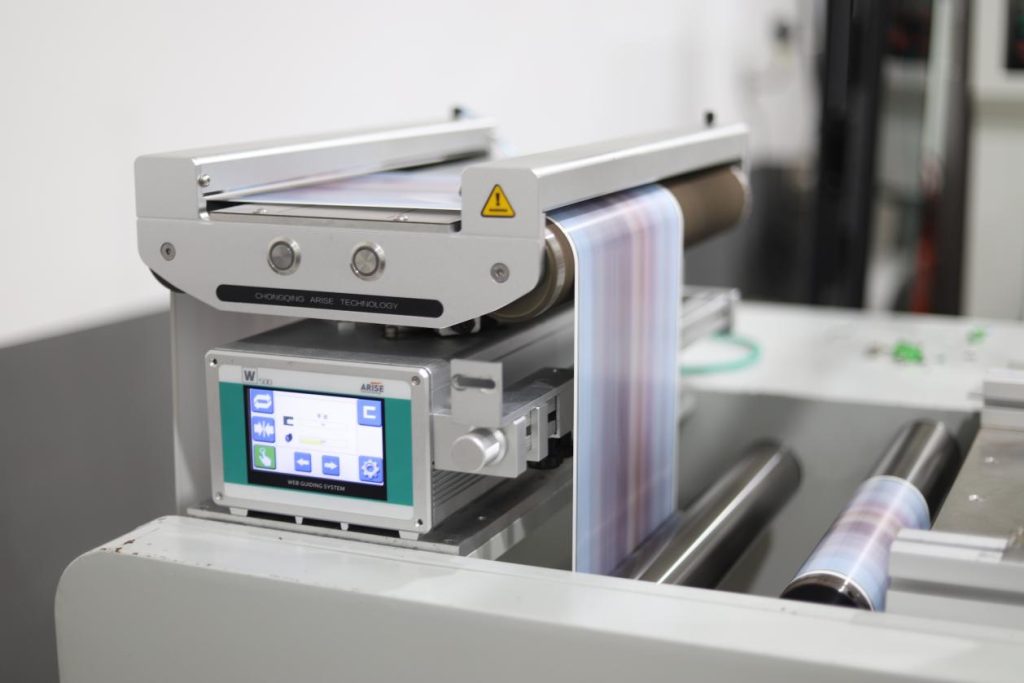
Best Practices for Implementing Automatic Web Guiding Calibration for Multi-Layered Materials
This chart outlines best practices for implementing automatic web guiding calibration specifically tailored for multi-layered materials, ensuring efficiency, accuracy, and consistency in material handling.
Best Practice | Description |
Conduct Thorough Material Assessment | Analyze the properties of each layer in multi-layered materials (e.g., thickness, elasticity, flexibility) to tailor the calibration approach. |
Use High-Precision Sensors | Implement high-accuracy web guide sensors such as laser or vision-based systems for precise alignment detection across all layers of the material. |
Implement Layer-Specific Control | Set up independent control for each layer to ensure that tension and alignment are maintained separately for multi-layered materials to prevent slipping. |
Optimize Calibration Algorithms | Use adaptive algorithms that adjust for varying material properties, ensuring effective calibration regardless of material inconsistencies. |
Integrate Real-Time Feedback Mechanisms | Establish a real-time feedback loop where sensors continuously monitor material position and adjust guiding parameters to keep alignment within optimal ranges. |
Regular Calibration and Maintenance | Perform regular calibration checks and web guiding system maintenance to ensure ongoing accuracy and prevent misalignment due to equipment wear. |
Monitor Environmental Influences | Account for environmental factors (e.g., temperature, humidity) that could affect material behavior, and adjust calibration accordingly. |
Customize for Production Variability | Tailor calibration settings to handle production variances like speed changes or material defects, ensuring consistent quality across batches. |
Utilize Edge and Center Alignment Tracking | Use both edge tracking and center alignment techniques to ensure complete material alignment, especially for multi-layered materials. |
Test and Validate Regularly | Conduct tests periodically to validate the performance of the automatic web guiding system, ensuring it continues to meet the required accuracy and quality standards. |
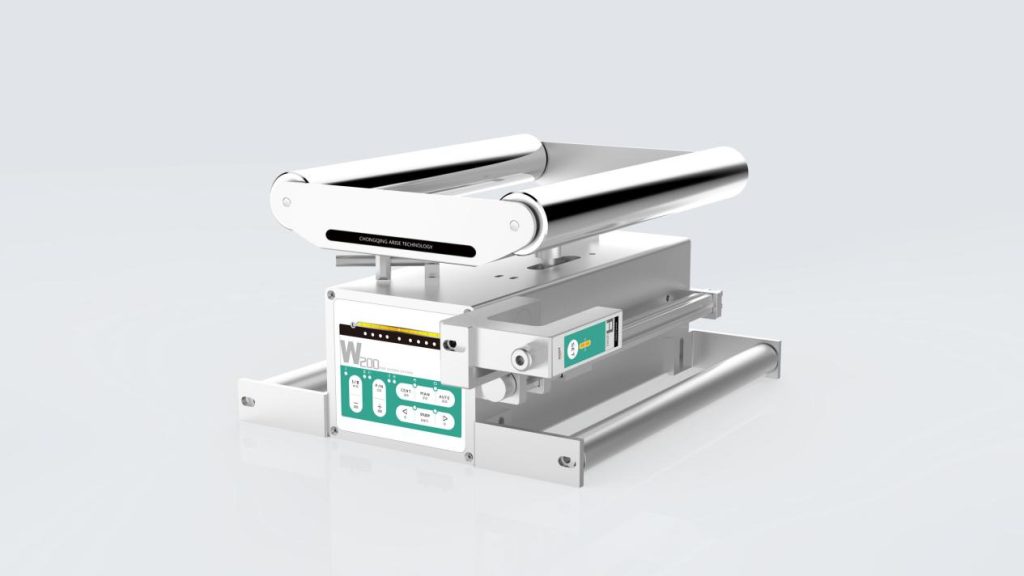
In summary, Automatic web guiding calibration for multi-layered materials is a critical advancement in ensuring the smooth handling and processing of complex materials in industries such as packaging, textiles, and printing. Through incorporating precise sensors, actuators, controllers and adaptive control algorithms, industries can successfully manage the challenges presented by multi-layered materials. Proper implementation and maintenance of web guide systems are essential for optimizing production processes.