What are Wireless Web Guide Systems: 5 Key Points Need to Know
Table of Contents
In industries like printing, packaging, and textiles, maintaining precise alignment of web materials is crucial for quality and efficiency. Traditional web guide systems, while effective, often require extensive wiring and manual calibration, leading to higher installation costs and maintenance challenges. The adoption of wireless web guide systems has transformed these operations, introducing a new level of flexibility and precision.

Understanding the Basics of Wireless Web Guide Systems
A web guide system ensures the lateral alignment of continuous materials, such as paper, film, or fabric, etc, during processing. Wireless web guide systems advance this concept by incorporating wireless communication between sensors, controllers, and actuators, eliminating the need for physical wiring.
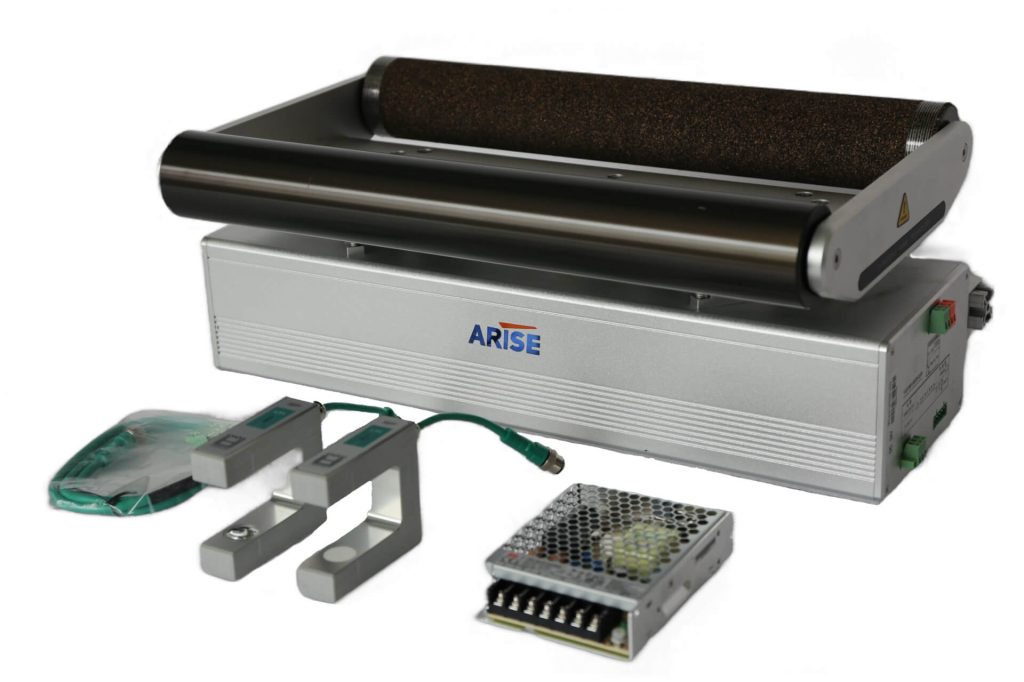
Key Features of Wireless Web Guide Systems
- Wireless Communication: Wireless technology replaces the need for physical connections, enabling seamless data transmission between sensors, controllers, and actuators. This reduces clutter and installation complexity.
- Advanced Sensing Technologies: These systems incorporate cutting-edge web guide sensors like infrared edge sensors, ultrasonic web guide sensors, optical sensors, etc, capable of detecting edges, alignment markers, and deviations with high precision.
- Real-Time Feedback and Control: The systems offer instantaneous feedback on web alignment, allowing for rapid adjustments to maintain accuracy during high-speed operations.
- Remote Monitoring and Accessibility: Operators can manage and monitor system performance through wireless devices such as smartphones, tablets, or centralized control hubs, increasing convenience and operational oversight.
- Compact and Modular Design: Designed for flexibility, these systems integrate easily into various machinery setups and can be scaled or reconfigured with minimal effort.
- Energy Efficiency: Optimized for low power consumption, some wireless systems incorporate energy-harvesting technologies, making them eco-friendly and cost-effective.
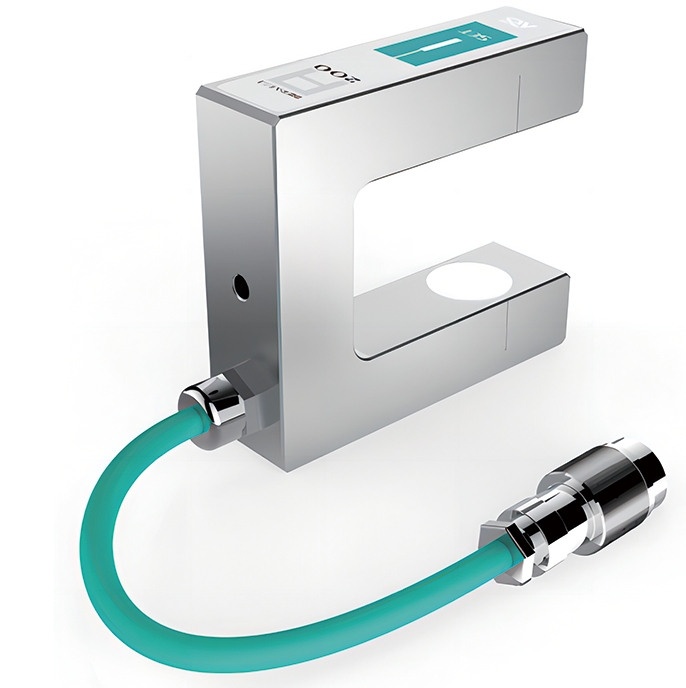
Key Benefits of Wireless Web Guide Systems
- Reduced Installation Costs: By eliminating the need for extensive wiring, wireless systems significantly lower installation costs. The simplified setup also reduces the time required to deploy the system.
- Enhanced Flexibility: Wireless technology allows for easy reconfiguration of system components. This adaptability makes these systems ideal for industries that frequently change production layouts or processes.
- Improved Precision: Equipped with advanced web guide sensors and real-time data transmission, wireless web guiding systems offer superior alignment accuracy, ensuring high-quality output in critical applications.
- Lower Maintenance Requirements: The absence of physical connections reduces wear and tear, minimizing the need for maintenance. Additionally, wireless systems are less prone to damage caused by environmental factors like vibration or humidity.
- Increased Reliability: With fewer physical components like wires, the risk of disconnections or damage is reduced, ensuring more reliable performance in demanding industrial settings.
- Compatibility with IoT and Industry 4.0: Many wireless web guiding systems are IoT-enabled, allowing for integration into smart manufacturing environments and providing actionable data analytics for continuous improvement.
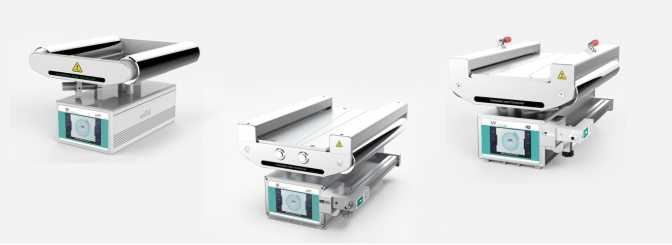
Applications of Wireless Web Guide Systems
Wireless web guide systems have versatile applications across industries, offering precision, efficiency, and cost savings in various material handling and processing tasks.
- Printing Industry: Wireless web guide systems ensure precise alignment of paper or substrates during high-speed printing processes. This improves print quality, minimizes material wastage, and reduces downtime caused by misalignment.
- Packaging Industry: In packaging lines, these web guiding control systems maintain the accurate positioning of films, foils, and other materials. They help achieve consistent sealing, proper folding, and aesthetically pleasing packaging results.
- Textile Industry: Wireless web guide systems are used to align fabrics during weaving, dyeing, and finishing processes. They ensure uniform fabric quality and reduce defects, even during high-speed operations.
- Converting Processes: In slitting, laminating, and coating applications, web guide systems maintain material alignment, ensuring precise cuts, seamless laminations, and consistent coatings.
- Paper and Pulp Industry: During paper manufacturing and finishing stages, these systems help in managing web alignment, resulting in better product uniformity and operational efficiency.
- Flexible Film Manufacturing: Wireless systems guide thin films in extrusion and lamination processes. They prevent wrinkles, folds, or misalignments, ensuring high-quality output.
- Tire Manufacturing: In tire production, web guiding systems maintain precise alignment of rubber layers, improving the quality and reliability of the finished product.
- Metal Processing: These systems guide metal sheets and coils during cutting, coating, and forming operations. They enhance precision, reduce material waste, and ensure better product consistency.
- Electronics Industry: Wireless web guiding systems are used in the alignment of PCBs and flexible circuits during assembly processes. They improve accuracy and yield in electronics manufacturing.
- Food Processing: In food packaging applications, web guide systems help align films, foils, and other materials used for sealing and wrapping. This ensures hygienic and consistent packaging.
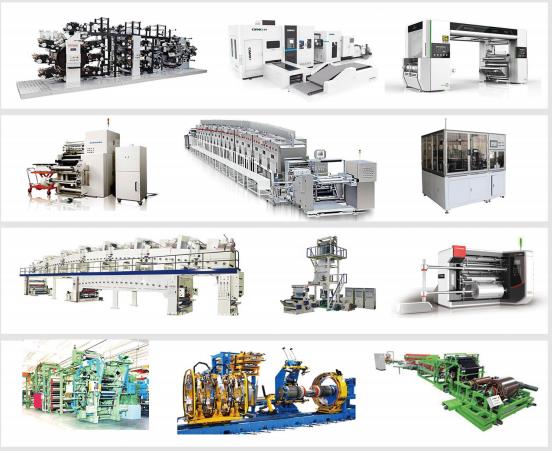
Challenges and Future Solutions in Wireless Web Guide Systems
This chart highlights the key challenges in wireless web guide systems and outlines innovative solutions to address them effectively.
Challenge | Description | Future Solution |
Signal Interference | Wireless communication disrupted by nearby devices or equipment. | Advanced protocols (e.g., 5G, Wi-Fi 6) and frequency-hopping techniques to enhance reliability. |
Battery Dependence | Frequent replacements or recharging disrupts operations. | Energy-harvesting technologies (e.g., vibration or thermoelectric generators) for continuous power. |
Cybersecurity Risks | Vulnerability to hacking or unauthorized access. | Robust encryption, secure authentication, and real-time intrusion detection systems. |
Range and Connectivity Issues | Signal degradation over large distances or complex layouts. | Mesh networking and signal amplifiers to maintain stable communication. |
Environmental Sensitivity | Performance degradation in extreme temperatures, moisture, or dusty conditions. | Ruggedized hardware and corrosion-resistant, heat-tolerant materials for durability. |
Integration with Legacy Systems | Retrofitting into existing setups is complex and costly. | Modular, plug-and-play solutions with standardized protocols for seamless integration. |
High Initial Costs | Prohibitive investment for small and medium enterprises. | Economies of scale and advanced manufacturing techniques to lower costs over time. |
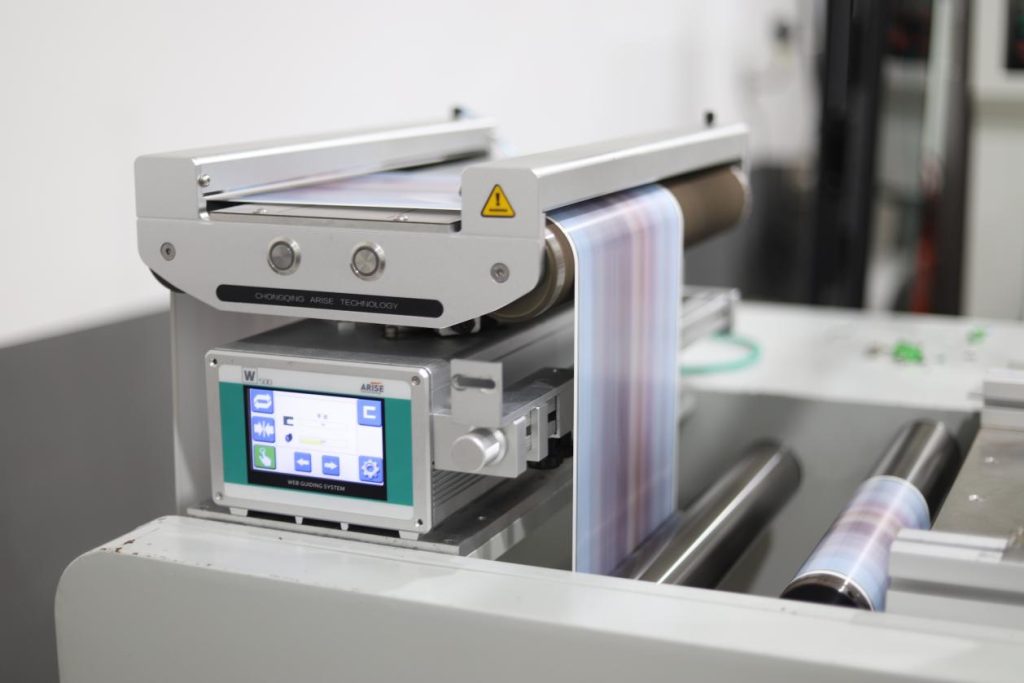
Future Solutions for Long-term Efficiency
- AI-Powered Optimization: AI algorithms can enable predictive maintenance and adaptive control, reducing downtime and enhancing system efficiency.
- IoT Integration: Seamless IoT connectivity will facilitate centralized monitoring and data-driven decision-making, improving productivity across operations.
- Self-Healing Networks: Future systems may incorporate self-healing capabilities to automatically detect and resolve communication disruptions, ensuring uninterrupted operation.
- Smart Sensors: Advanced sensors with built-in processing capabilities can improve alignment accuracy and reduce the load on central web guide controllers.
- Customizable and Scalable Systems: Systems designed for modular scalability will allow users to upgrade or adapt configurations based on changing operational requirements.
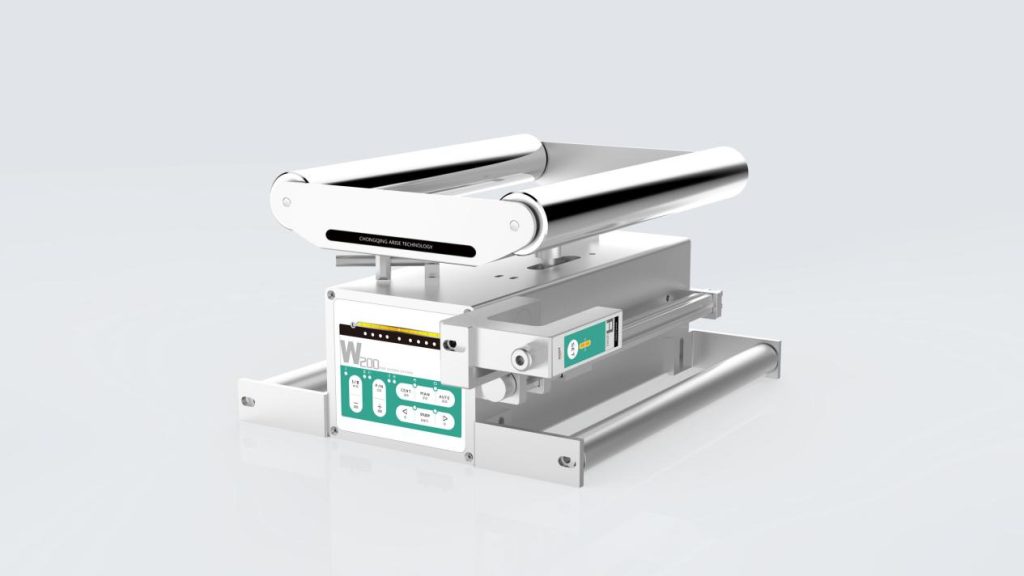
Final Thoughts
Through combining precision, flexibility, and ease of use, wireless web guide systems are reshaping the way industries manage web alignment. As technology continues to advance, these systems will undoubtedly become an indispensable part of modern manufacturing processes.