What are Web Guide Systems for Centering Guiding
In industrial processes where precision is critical, maintaining the proper alignment of materials as they move through machinery is a challenge. A web guide system for centering guiding is designed to address this issue, ensuring that materials stay perfectly aligned, even at high speeds or under varying load conditions. This article explores the importance of centering web guide systems, how they work, their benefits in diverse industries and how to choose the right type.
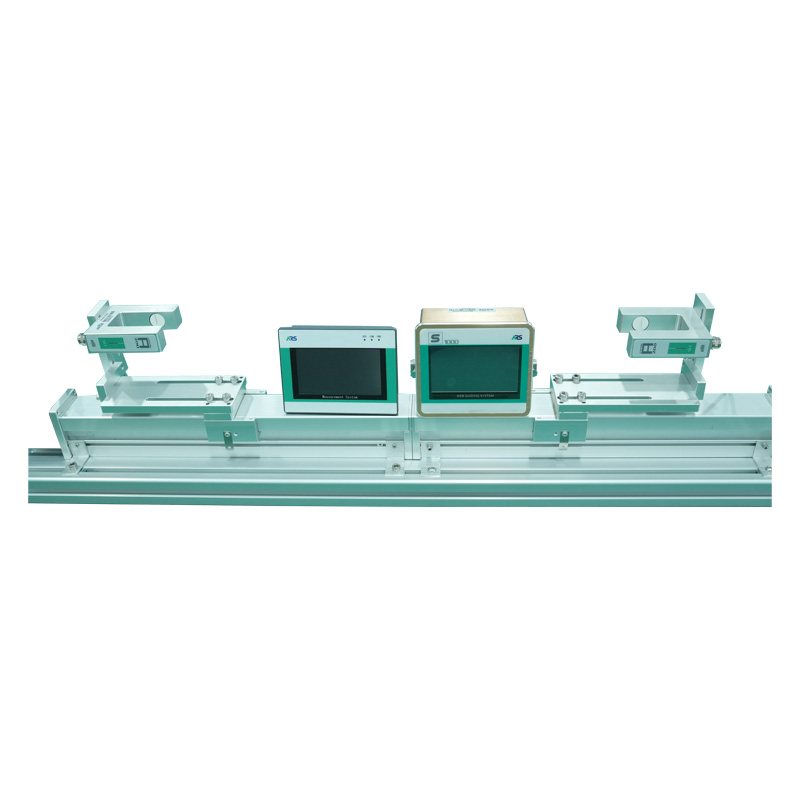
Table of Contents
Understanding a Web Guide System for Centering Guiding
A web guide system is a control mechanism designed to keep moving materials, such as paper, film, textiles, or metal foils, centered on a production line. In centering guiding, the system continuously monitors and adjusts the material’s lateral position to ensure it stays aligned along the center of the production path. This is particularly useful for processes where even slight deviations can lead to defects or inefficiencies.
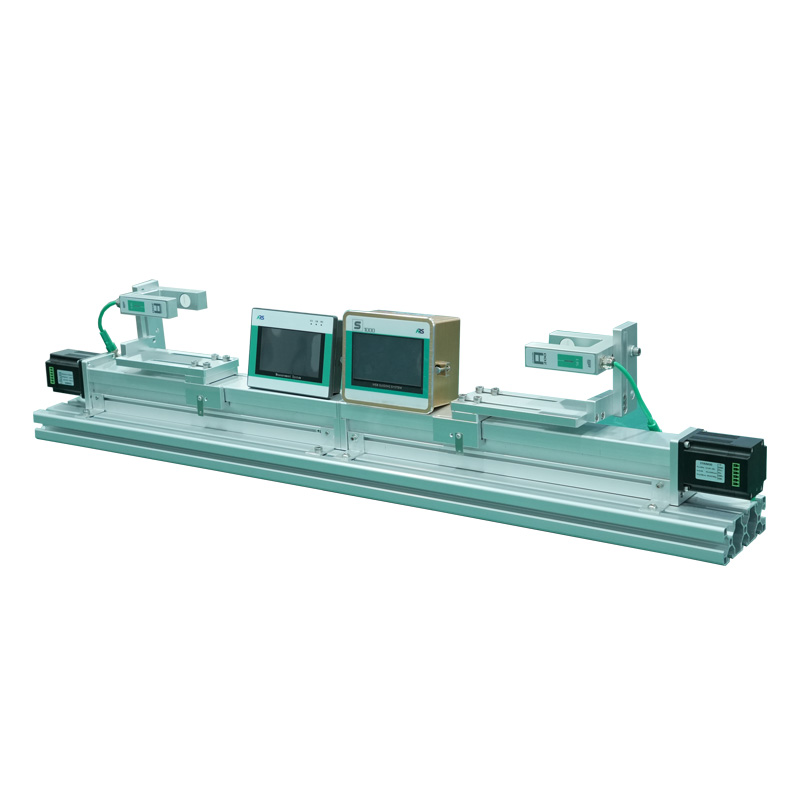
How Does a Web Guide System for Centering Guiding Work
A web guide system for centering guiding operates through a seamless interplay of sensors, controllers, and actuators, designed to ensure continuous alignment of materials during production.
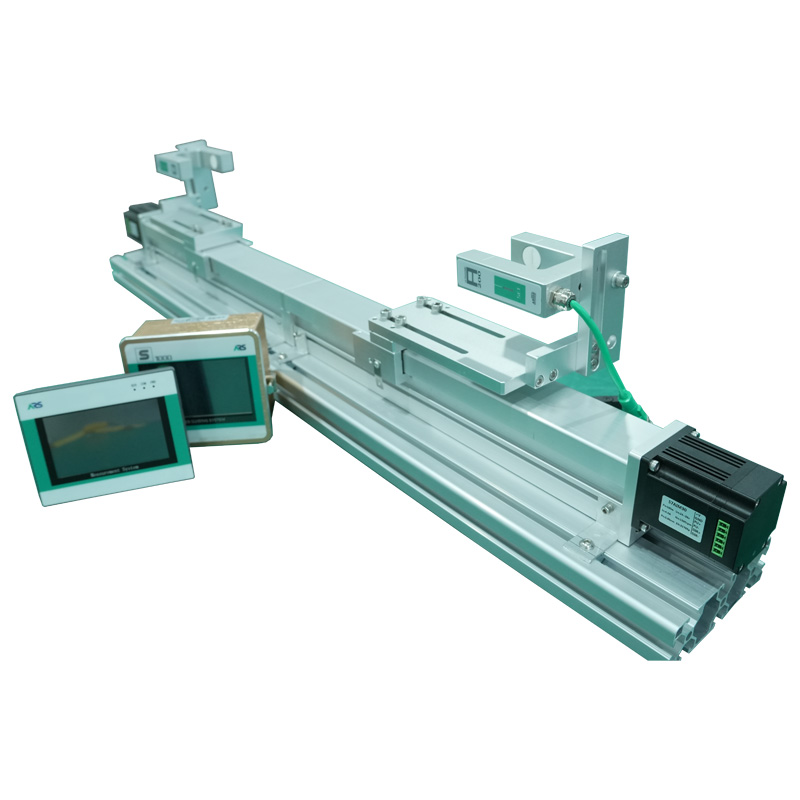
Sensors
The process begins with web guide sensors that monitor the material’s position. These sensors, which may use technologies like ultrasonic, infrared, or optical detection, precisely identify the edges or center of the moving web. They provide real-time data to the system about any deviations from the required alignment.
Guiding Controllers
This data is sent to the controllers, which acts as the decision-making unit of the system. The web guide controllers process the information received from the sensors and determines if the material is misaligned. If a deviation is detected, the controller calculates the necessary corrective action to bring the material back to its proper position.
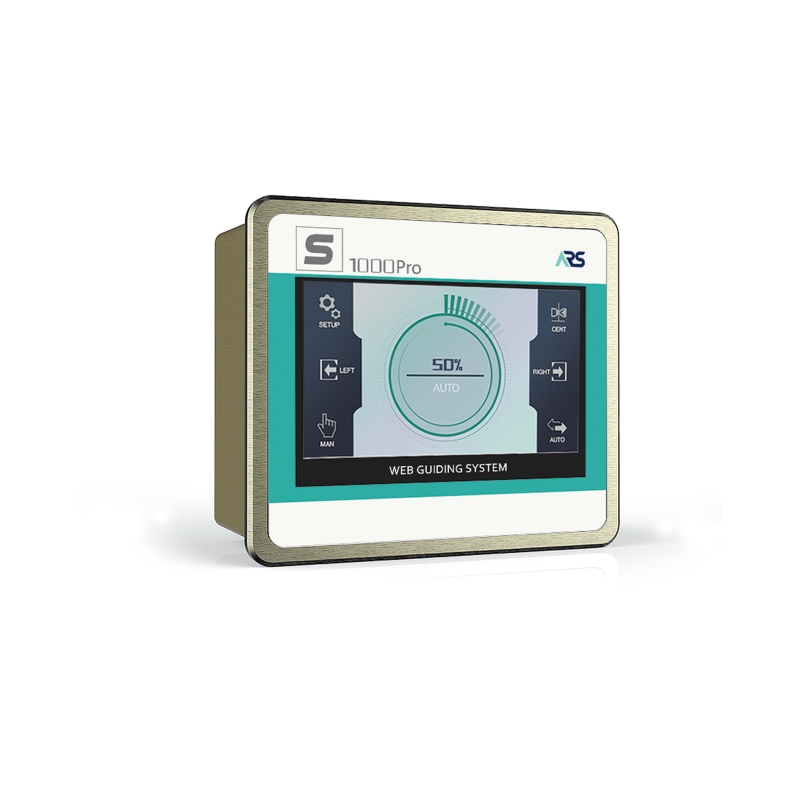
Actuators
Once the corrective action is determined, the controller sends signals to the web guiding actuators, which are the mechanical components responsible for making adjustments. The actuators move the web guide rollers or steering frames, gently shifting the material back to its correct path. This adjustment happens dynamically and continuously, ensuring that the material remains centered even during high-speed operations or when handling materials with variable properties.
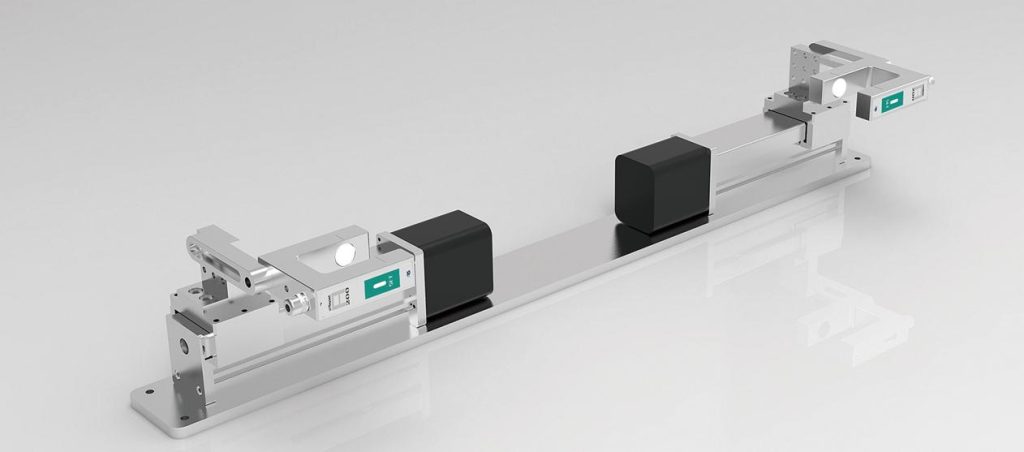
Through this continuous feedback loop, the centering web guide systems ensure that materials remain precisely aligned throughout the production line, eliminating the risk of defects and reducing material waste.
Key Applications of Centering Web Guiding Systems
- Printing and Packaging
In the printing and packaging industries, centering web guiding systems play a vital role in ensuring accuracy during high-speed operations. They help maintain precise alignment of materials like paper, plastic films, and laminates to prevent misregistration of designs, uneven printing, and improper folding. This is especially crucial for multi-color printing processes, where even slight deviations can ruin an entire batch.
- Textile Manufacturing
Textile production often involves delicate fabrics or wide materials that must be accurately guided through processes such as weaving, dyeing, and finishing. Centering web guide systems ensure that the material is perfectly aligned, minimizing tension fluctuations and preventing wrinkles, creases, or uneven dye application.
- Film and Plastic Production
Thin films and plastic sheets are prone to tearing and misalignment during extrusion and lamination processes. Web guide systems for centering guiding ensure precise positioning of these materials, avoiding defects such as overlapping or edge irregularities, which can compromise the quality of the final product.
- Metal Foil Processing
In metal foil production, used for applications such as packaging, electronics, or automotive components, centering web guiding systems are critical. They ensure the proper alignment of the foil during cutting, slitting, and coating processes, preventing edge defects and achieving consistent product quality.
- Paper and Board Manufacturing
During the production of paper and board, web guiding systems are used to ensure that materials stay aligned throughout various processes like calendaring, coating, and slitting. This prevents unnecessary trimming, reduces waste, and enhances the uniformity of the final product.
- Labeling and Converting
Labeling machines and converting lines rely heavily on precise alignment to ensure accurate cutting, laminating, and adhesive application. Centering web guide systems enable the seamless handling of materials, preventing off-center labels or uneven adhesive distribution.
- Tire and Rubber Manufacturing
In the production of tires and other rubber components, maintaining the correct alignment of materials like rubber sheets and textile cords is essential. Centering web guiding systems prevent overlap and misalignment, ensuring a uniform product and reducing waste.
- Flexible Electronics
Emerging industries, such as flexible electronics, require extreme precision in guiding thin and fragile materials like conductive films. Web guiding systems ensure alignment during the deposition, lamination, and patterning processes, contributing to the functionality and reliability of electronic components.
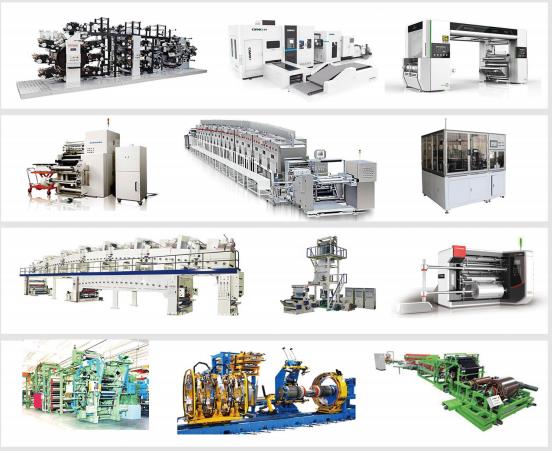
Innovations in Centering Web Guide Systems
Centering web guide systems have evolved significantly with the advent of advanced technologies. These innovations are transforming traditional guiding mechanisms into highly intelligent and efficient systems, meeting the growing demands of precision, speed, and sustainability across various industries.
1. Sensor Advancements
One of the most notable innovations in centering web guide systems is the development of advanced sensors. Modern systems now utilize high-resolution ultrasonic sensors or infrared and optical sensors capable of detecting even the slightest deviations in material position. Some systems incorporate AI-enhanced sensors that can adapt to complex material properties, such as varying transparency, thickness, or reflectivity, ensuring consistent performance even under challenging conditions.
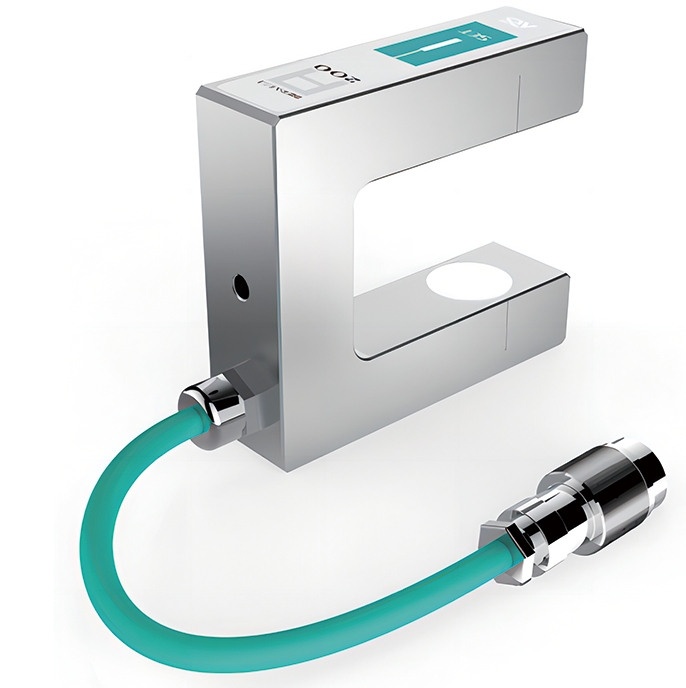
2. Integration with Industry 4.0
The integration of web guide systems into Industry 4.0 frameworks has opened new possibilities for connectivity and automation. Through IoT-enabled devices, these systems now allow for real-time monitoring, data analysis, and remote control. Operators can access performance metrics and make adjustments from centralized platforms, significantly enhancing operational efficiency and reducing downtime.
3. AI and Machine Learning
Artificial intelligence and machine learning are reshaping the functionality of centering web guide systems. AI algorithms analyze patterns and anticipate potential alignment issues, enabling predictive adjustments before deviations occur. This proactive approach minimizes defects and improves overall process reliability, particularly in high-speed applications.
4. Energy-Efficient Actuators
The development of energy-efficient actuators is another milestone in web guide systems. Modern actuators require less power while delivering faster and more precise corrections. This innovation reduces energy consumption, aligning with sustainability goals and lowering operating costs.
5. Enhanced User Interfaces
Contemporary web guide systems come with improved user interfaces that simplify operation and maintenance. Touchscreen panels with intuitive controls, detailed diagnostics, and step-by-step troubleshooting guides empower operators to manage the systems effectively, reducing the need for specialized training.
6. Multi-Material Handling
As industries demand greater versatility, innovations in centering web guide systems now enable seamless handling of multiple material types. From thin films to rigid sheets, the latest systems can automatically adjust to accommodate different material properties, eliminating the need for manual recalibration.
7. Smart Calibration
Smart calibration features are another innovation, allowing the system to self-adjust during start-up or when material properties change. This reduces setup times and ensures optimal performance from the outset, enhancing production line efficiency.
8. Predictive Maintenance
Advanced web guiding systems are equipped with predictive maintenance capabilities. By analyzing operational data, the system can identify wear and tear in components like actuators and sensors, notifying operators of required maintenance before a failure occurs. This minimizes unplanned downtime and extends the system’s lifespan.
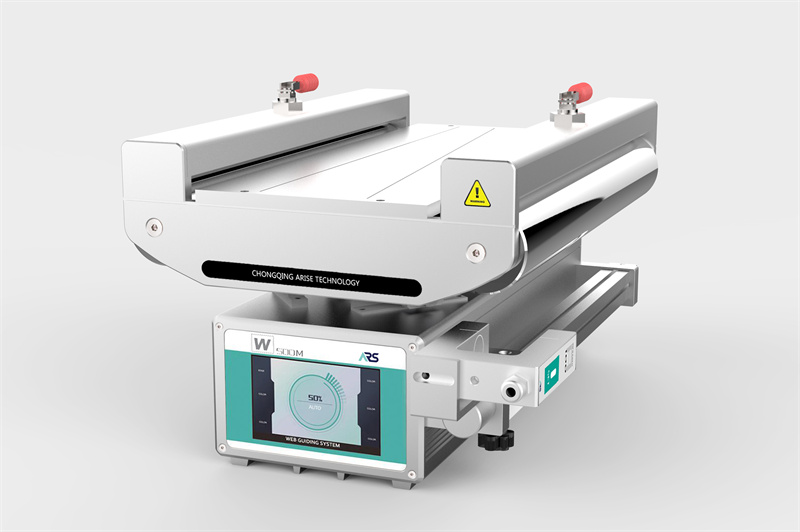
Key Factors to Consider for Choosing the Right Centering Web Guide System
This chart summarizes critical factors, allowing you to select a centering web guide system that aligns with your production needs while ensuring efficiency and cost-effectiveness.
Factor | Description | Why It Matters |
Material Type | Consider the type of material (paper, film, textile, metal foil, etc.) the system will handle. | Different materials have unique properties like thickness, flexibility, and tension. |
Sensor Technology | Choose between ultrasonic, infrared, or optical sensors based on material transparency and precision needs. | Ensures accurate detection of edges or centerlines for optimal alignment. |
Line Speed | Assess the maximum speed of your production line. | Ensures the system can operate effectively at the required speeds without lag. |
Web Width | Determine the range of web widths the system needs to accommodate. | Supports flexibility for different material sizes in production. |
Tension Control | Evaluate the tension range and stability of the material. | Prevents web sagging or tearing, ensuring smooth operation. |
Operating Environment | Consider environmental factors like temperature, humidity, and dust levels. | Ensures system durability and consistent performance under specific conditions. |
Adjustability | Look for systems with automatic or manual adjustment options. | Allows flexibility for varying production requirements. |
Integration Capability | Ensure compatibility with existing equipment and control systems. | Facilitates seamless integration and reduces downtime. |
Energy Efficiency | Evaluate the system’s power consumption and energy-saving features. | Reduces operational costs and aligns with sustainability goals. |
Maintenance Requirements | Consider ease of maintenance, including component accessibility and diagnostics. | Minimizes downtime and extends the lifespan of the system. |
Cost and ROI | Assess the initial investment, operational costs, and potential return on investment. | Helps balance budget constraints with long-term performance benefits. |
Brand Reputation | Choose a reliable manufacturer with proven expertise in web guide systems. | Ensures quality, reliability, and access to technical support. |
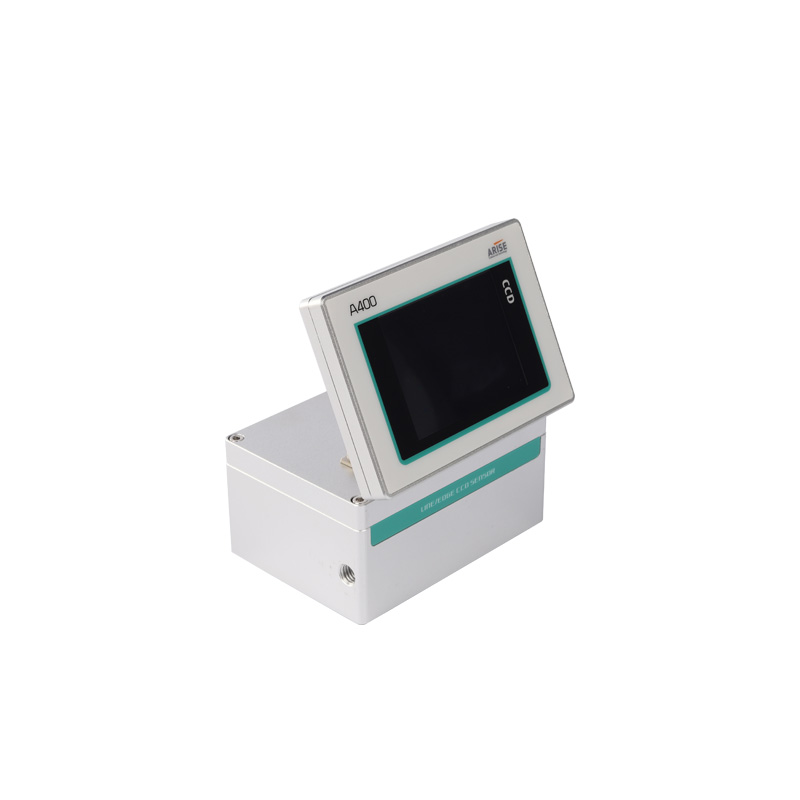
In summary, web guide systems for centering guiding are essential for industries that require precision and consistency in material alignment. Through adopting advanced web guiding technology, manufacturers can improve product quality, reduce waste, and achieve greater operational efficiency.