What are the Latest Innovations in Web Guiding Technology
Table of Contents
Web guiding technology plays a pivotal role in industries such as printing, packaging, textiles, and materials converting, where precision and efficiency are critical. With advancements in automation and digitization, web guiding systems have undergone significant transformations, integrating cutting-edge technologies to meet modern industrial demands. This article focus on the latest innovations driving the evolution of web guiding technology.
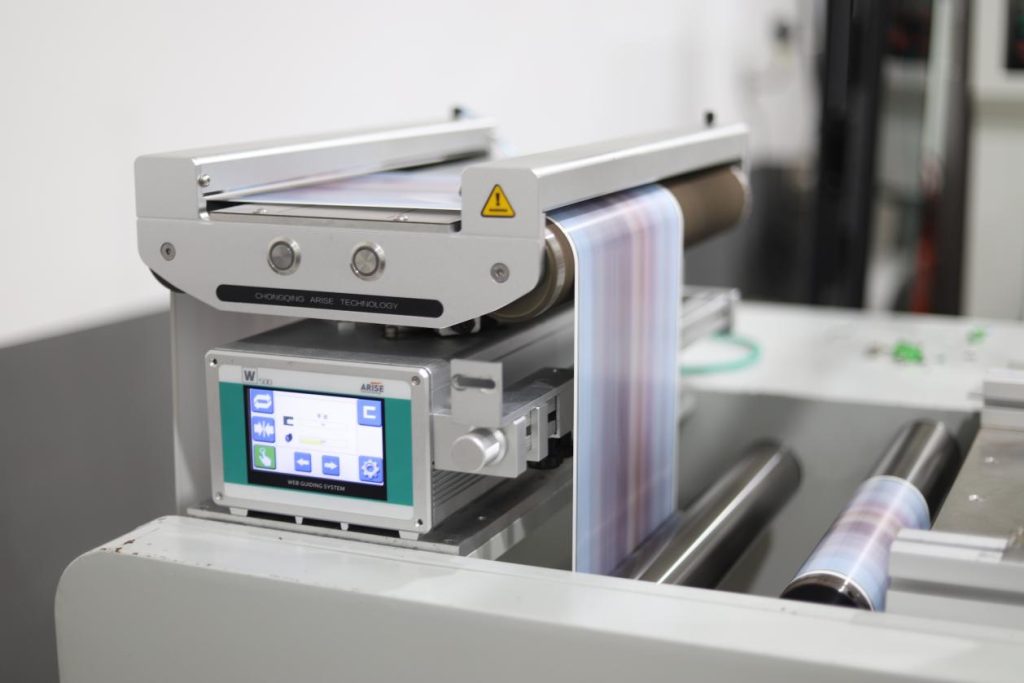
What Is Web Guiding Technology
Web guiding technology refers to systems designed to maintain the correct alignment of a moving web (a continuous flexible material) during manufacturing processes. These web guide systems detect misalignment and correct the web’s position in real time, ensuring it stays within predefined tolerances.
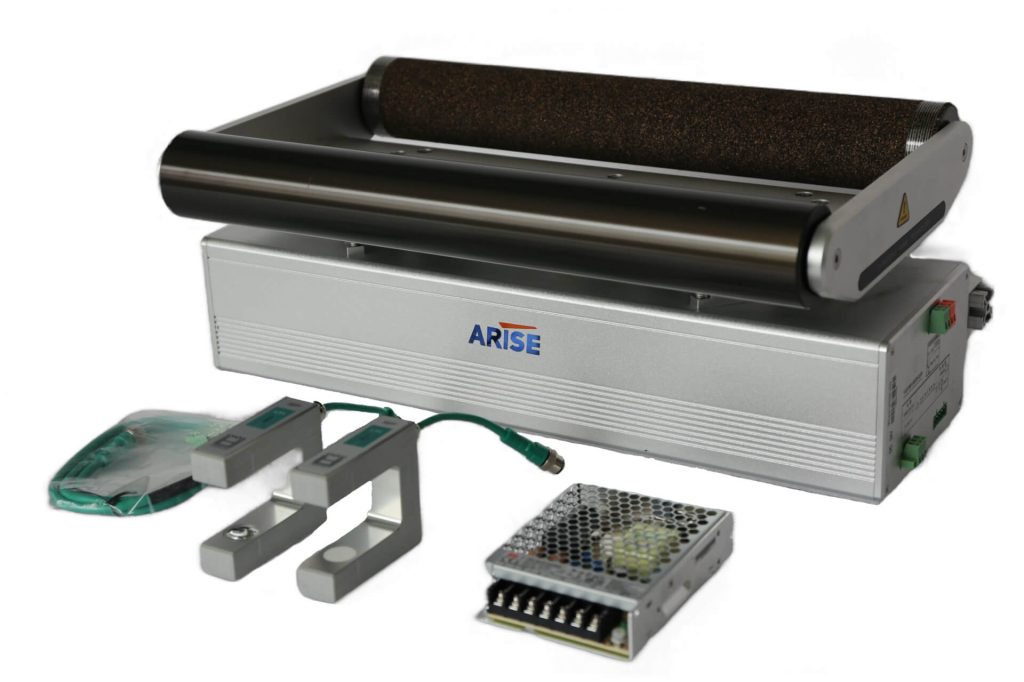
Key Components of Web Guiding Systems
Sensors
Web guide sensors are critical in detecting the web’s position. Different types of sensors are used depending on the material properties:
- Ultrasonic sensors: Ideal for opaque or transparent materials.
- Infrared sensors: Suitable for reflective or heat-sensitive webs.
- Laser sensors: Offer high precision for fine alignment.
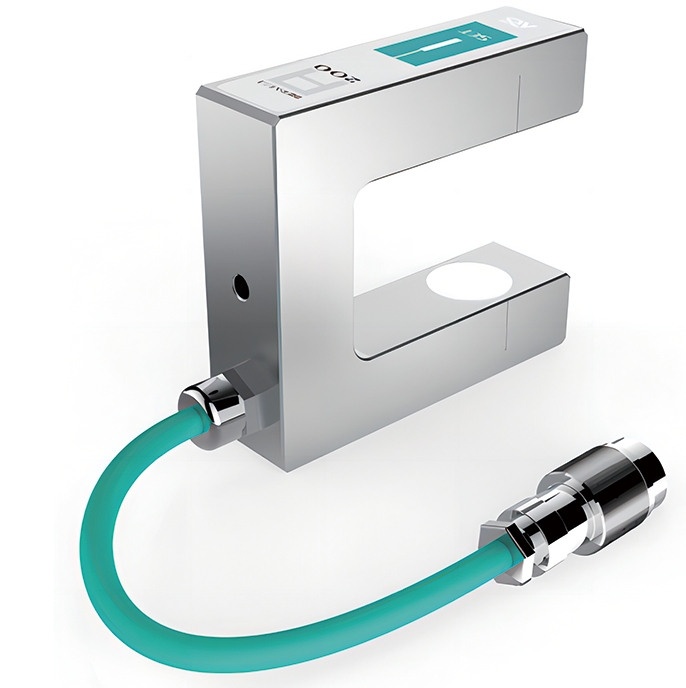
Controllers
The web guiding controller acts as the system’s brain, processing input from sensors and sending commands to actuators to adjust the web’s position. Advanced controllers may include programmable logic for complex alignment tasks.
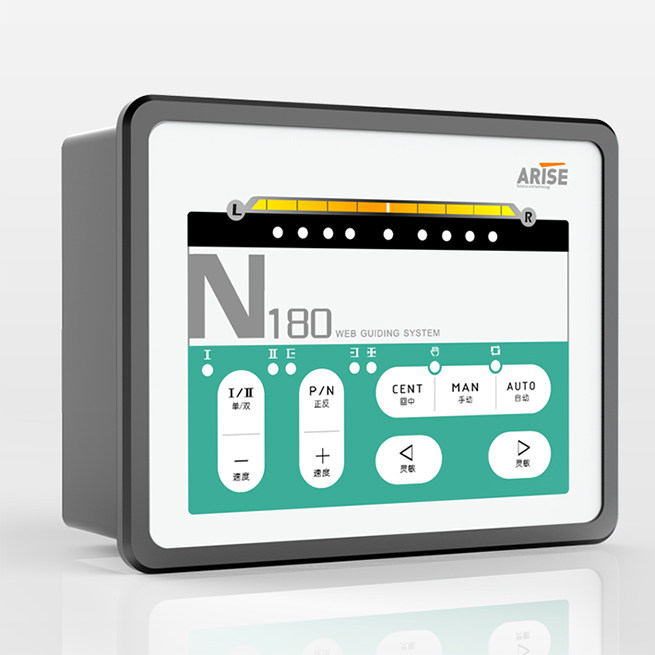
Actuators
Web guide actuators execute the corrective actions, physically moving the web or guiding rollers to the desired position. Servo and piezoelectric actuators are commonly used for their precision and responsiveness.
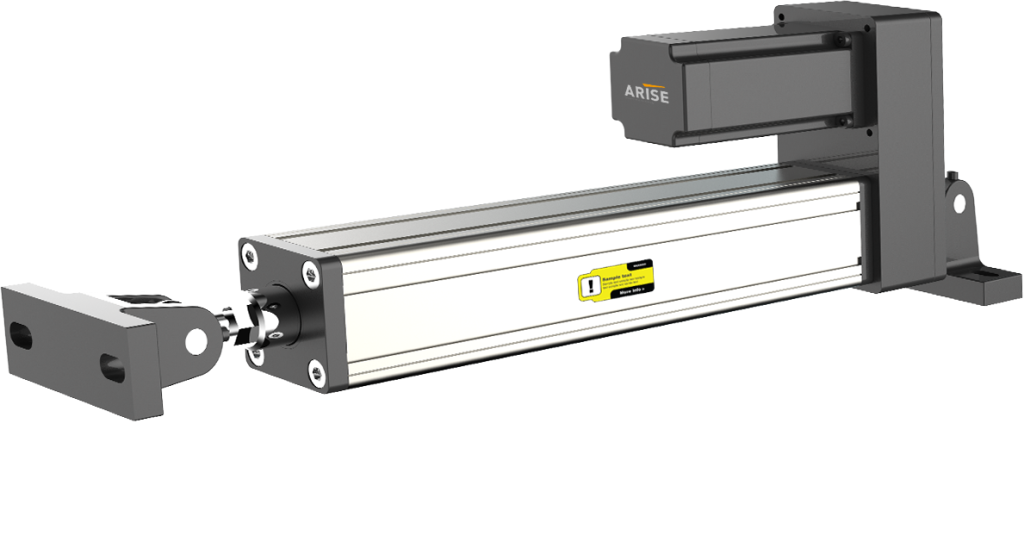
Guiding Mechanisms
These include steering rollers, pivot frames, and other mechanical elements that physically guide the web. The choice of mechanism depends on the web material, speed, and process requirements.

Key Functions
This chart highlights the primary functions of web guiding technology, showing how each contributes to precise material handling and improved operational outcomes.
Function | Description | Benefits | Common Applications |
Edge Guiding | Aligns the web by detecting and correcting its edge position. | Ensures consistent alignment; suitable for varying material widths. | Printing, packaging, textiles. |
Center Guiding | Aligns the web relative to a centerline or axis for balanced processing. | Maintains symmetry; essential for uniform applications. | Laminating, film and foil converting. |
Line Guiding | Tracks and aligns the web based on printed lines, marks, or patterns. | Provides high accuracy for overprinting and cutting. | Multi-color printing, packaging. |
Tension Control | Maintains consistent web tension during guiding operations. | Prevents web distortion and wrinkling; improves product quality. | Coating, slitting, embossing. |
Tracking Control | Monitors and adjusts the web’s lateral position to prevent misalignment. | Reduces material waste; increases production efficiency. | Flexible packaging, textiles. |
Multi-Mode Guiding | Combines edge, center, and line guiding into a single system for flexibility. | Supports diverse material types and applications. | General converting, high-speed production. |
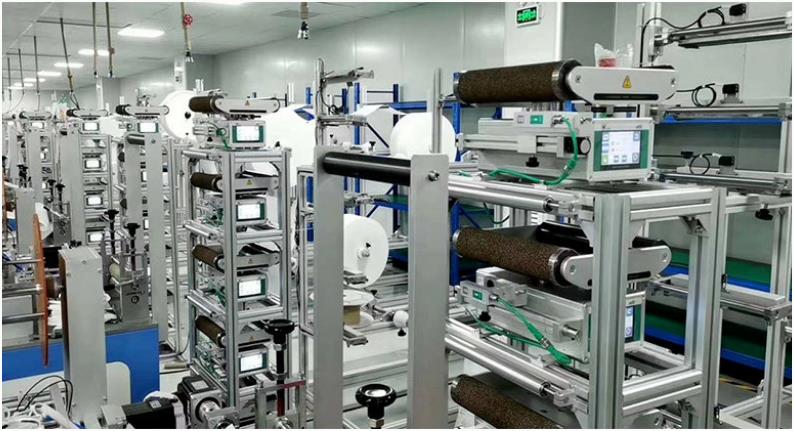
Key Advancement in Web Guiding Technology
1. Advanced Sensor Technology
Advanced web guide systems leverage highly sensitive sensors such as ultrasonic, infrared, and laser sensors. These innovations enable precise detection of web edges, even in challenging conditions like low contrast or transparent materials. Enhanced sensitivity and accuracy ensure consistent alignment, reducing material wastage and improving product quality.
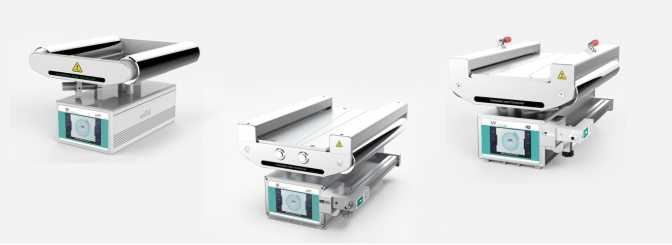
2. Intelligent Control Systems
The integration of artificial intelligence (AI) and machine learning (ML) into web guiding systems has revolutionized their functionality. These systems can now analyze patterns, predict deviations, and automatically adjust alignment parameters. AI-powered web guides are particularly effective in handling complex materials or variable speeds, adapting in real time to maintain optimal performance.
3. Non-Contact Guiding Mechanisms
Non-contact guiding systems, utilizing air jets or magnetic fields, have emerged as a game-changer for delicate or sensitive materials. These systems minimize physical contact, reducing the risk of damage while maintaining precise control over the web’s trajectory.
4. Edge and Center Guiding Systems
Innovations in edge and center guiding systems allow seamless switching between guiding modes based on operational requirements. This flexibility is vital in industries with diverse material types and varying process demands, ensuring uninterrupted operations.
5. IoT and Industry 4.0 Integration
The integration of web guiding systems with the Internet of Things (IoT) and Industry 4.0 ecosystems enables remote monitoring and control. Operators can access real-time data on system performance, receive alerts for anomalies, and implement corrective measures promptly. This connectivity enhances operational transparency and reduces downtime.
6. Energy-Efficient Actuators
The development of energy-efficient actuators, such as piezoelectric or servo-driven systems, has contributed to the sustainability of web guiding technology. These actuators provide precise adjustments with minimal energy consumption, aligning with global efforts to reduce carbon footprints.
7. Modular and Compact Designs
Modern web guiding systems feature modular and compact designs that facilitate easy installation and maintenance. These designs are particularly beneficial for retrofitting existing production lines, allowing manufacturers to upgrade their processes without extensive downtime.
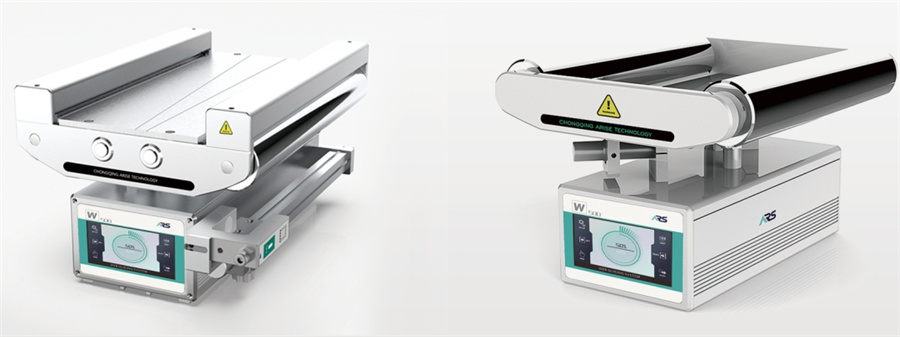
8. Enhanced Durability and Adaptability
Innovations in material science have resulted in web guiding systems that are more robust and adaptable to extreme environmental conditions. For example, systems with corrosion-resistant components are ideal for industries such as paper and pulp, where exposure to moisture is high.
9. Integration with Vision Systems
Combining web guiding technology with advanced vision systems enables real-time inspection and quality control. This integration ensures that material alignment is maintained while simultaneously monitoring for defects, streamlining production processes.
10. Customizable Software Interfaces
User-friendly and customized software interfaces in web guide systems allow operators to set parameters, monitor performance, and troubleshoot issues efficiently. Intuitive interfaces, often featuring touchscreens and multilingual options, simplify system operation and reduce the learning curve for operators. These interfaces enable quick adjustments, troubleshooting, and parameter setting, enhancing usability.
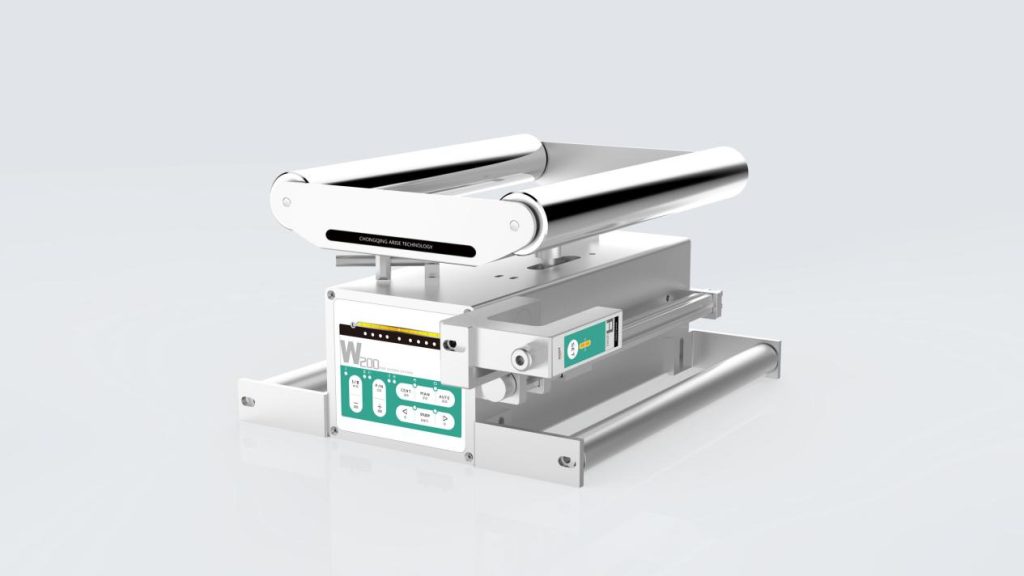
Conclusion
The rapid evolution of web guiding technology reflects the growing need for precision, efficiency, and adaptability in industrial processes. Through incorporating cutting-edge sensors, intelligent control systems, IoT connectivity, energy-efficient designs, etc, modern web guide solutions offer unparalleled performance. These advancements not only enhance production quality but also support sustainable manufacturing practices.