What are Effective Tension Control Solutions for Small-scale Production
Table of Contents
In small-scale production environments, tension control plays a vital role in ensuring product quality, minimizing waste, and optimizing operational efficiency. Unlike large-scale production lines, small-scale setups often face unique challenges such as limited space, budget constraints, and the need for greater flexibility to handle diverse materials. This article explores the key tension control solutions tailored to small-scale production.
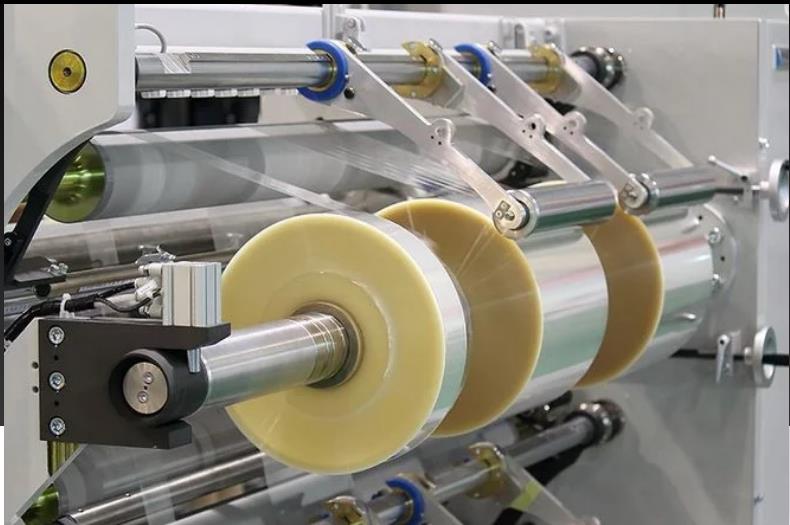
Importance of Tension Control in Small-scale Production
Tension control refers to maintaining consistent force on materials as they move through various stages of a production process. It is essential for industries such as printing, packaging, textiles, and electronics manufacturing, where uneven tension can lead to defects like wrinkles, stretching, or misalignment.
Key Aspect | Why It Matters | Examples |
Consistency in Product Quality | Prevents defects like wrinkles, stretch marks, or tearing; ensures proper alignment. | Adhesive tape production requires even adhesive application to avoid bubbles or gaps. |
Minimizing Material Waste | Reduces over-tensioning and under-tensioning, lowering waste costs. | Wire manufacturing avoids rejection caused by misaligned or coiled wires. |
Optimizing Operational Efficiency | Ensures smooth machine operations, preventing jams and downtime. | Label application machines achieve consistent positioning, avoiding misfeeds. |
Extending Equipment Lifespan | Reduces stress on rollers, belts, and motors, minimizing wear and tear. | Proper tension extends weaving loom lifespans in textile workshops. |
Supporting Scalability | Facilitates process replication without compromising quality as production scales. | A boutique paper mill scales operations while maintaining product quality. |
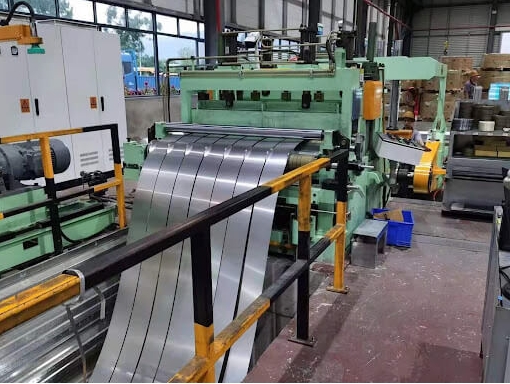
Key Challenges Faced in Tension Control for Small-scale Production
- Limited Space Availability: Small-scale production facilities typically operate in compact environments, leaving minimal room for tension control equipment. This constraint requires solutions that are not only space-efficient but also capable of integrating seamlessly into existing systems.
- Diverse Material Requirements: Small-scale operations often handle a wide variety of materials, such as thin films, textiles, papers, and foils. Each material has unique tension control needs, such as varying elasticity, thickness, and resistance to stress, making it challenging to maintain consistent control across different production runs.
- Budgetary Constraints: With smaller budgets compared to large-scale manufacturers, small-scale producers often struggle to invest in advanced tension control systems. This financial limitation necessitates finding cost-effective solutions that deliver reliable performance without requiring significant capital investment.
- Manual or Semi-Automated Processes: Many small-scale setups rely on manual or semi-automated production lines, increasing the likelihood of human error in maintaining consistent tension. Operators may struggle to make precise adjustments, leading to variations that affect product quality.
- Sensitivity to Material Defects: Small-scale production is often geared toward niche markets or high-value products, where even minor defects caused by improper tension can lead to significant losses. Ensuring the consistent handling of delicate or sensitive materials is a critical challenge.
- Inconsistent Production Speeds: Production speeds in small-scale setups may vary depending on manual intervention or batch-specific requirements. This variability can disrupt tension control, leading to over-tensioning or slack in the material.
- Lack of Advanced Monitoring Systems: Small-scale operations may lack the advanced sensors and feedback mechanisms often found in larger setups. Without real-time monitoring, it becomes difficult to detect and correct tension fluctuations, leading to potential material wastage or defects.
- High Downtime for Adjustments: Adjusting tension manually or reconfiguring systems for different materials often results in significant downtime. This can impact overall productivity, especially in small-scale setups where maximizing operational time is critical.
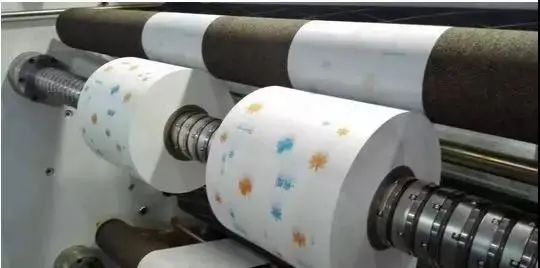
Effective Solutions to Address the Challenges in Tension Control for Small-scale Production
1. Manual Tension Control Systems
- Description: Operators manually adjust tension settings to maintain material consistency.
- Best for: Low-speed production lines with straightforward material handling requirements.
- Advantages: Affordable and simple to operate.
2. Dancer Roll Systems
- Description: A roller mechanism compensates for tension variations by absorbing material slack or stretch.
- Best for: Lightweight materials such as paper, textiles, and films.
- Advantages: Compact, reliable, and versatile for various applications.
3. Magnetic Particle Brakes and Clutches
- Description: Use adjustable magnetic powder brakes to control tension precisely during unwinding or rewinding processes.
- Best for: Processes requiring consistent tension, like packaging or printing.
- Advantages: Compact design, precise tension control, and durability.
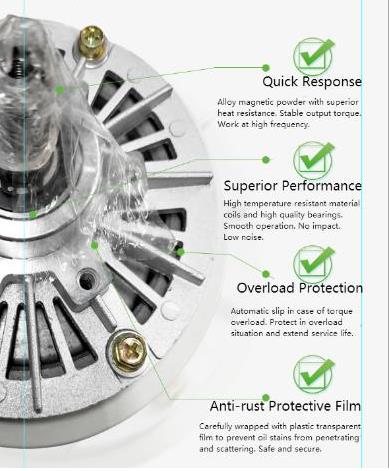
4. Load Cell-Based Systems
- Description: Real-time tension sensors measure and adjust tension to maintain desired levels.
- Best for: High-precision applications involving delicate materials like foils or thin films.
- Advantages: High accuracy and real-time adjustments for superior control.
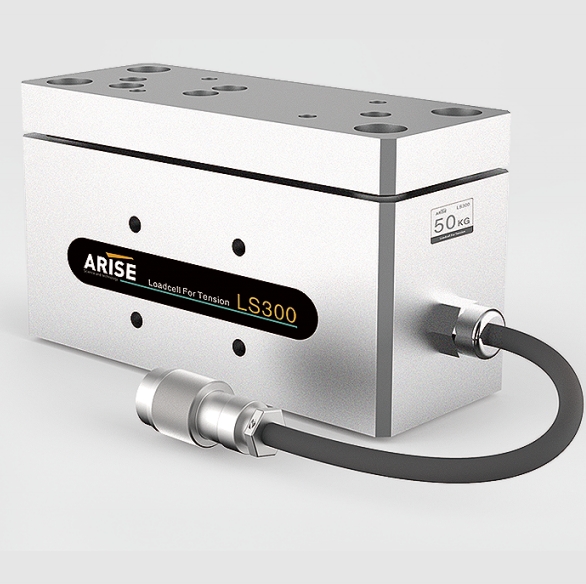
5. Closed-Loop Feedback Systems
- Description: Advanced tension control systems use feedback loops with sensors and actuators to ensure continuous tension regulation.
- Best for: Operations requiring minimal manual intervention and high-quality output.
- Advantages: Fully automated, reduces errors, and supports consistent production.
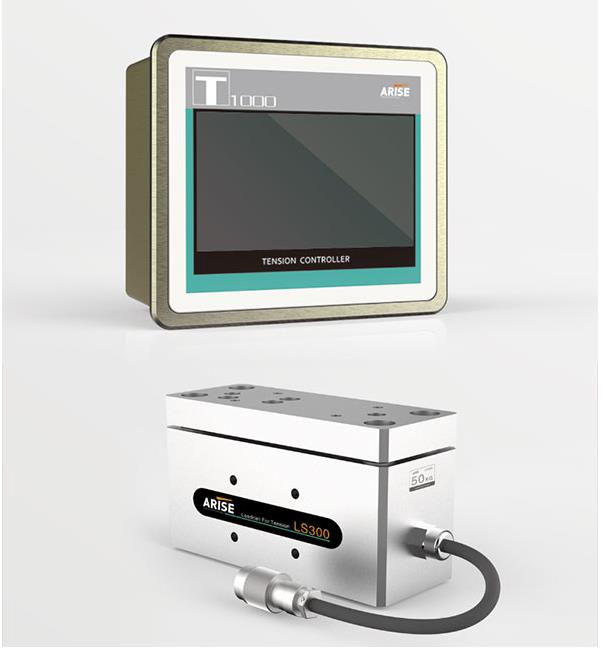
6. Web Guiding Systems
- Description: These web guide systems align and control the tension of web materials, reducing misalignment and defects.
- Best for: Industries like printing, packaging, and textiles.
- Advantages: Compact designs tailored for small-scale setups, ensuring high-quality results.
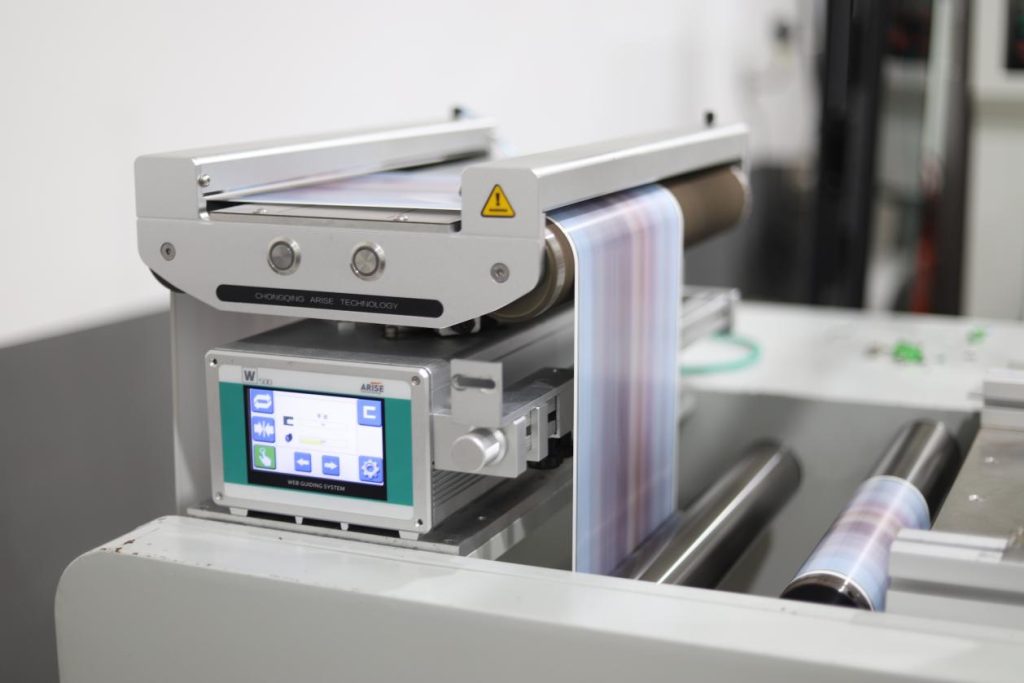
Factors to Consider When Choosing a Right Tension Control System
This chart serves as a quick reference for selecting the right tension control system tailored to specific production needs.
Factor | Description | Importance |
Material Properties | Characteristics like thickness, elasticity, and sensitivity of the material being processed. | Ensures system compatibility and quality handling. |
Production Speed | Speed of operation affects the type of system (manual vs. automated). | Prevents tension inconsistencies at varying speeds. |
System Scalability | Ability to adapt to increased production volumes or changing material types. | Future-proofs the investment. |
Space Constraints | Size and compactness of the system relative to the available workspace. | Fits into small-scale production setups effectively. |
Cost Efficiency | Balance between initial investment and long-term operational costs. | Ensures affordability without compromising quality. |
Ease of Integration | Compatibility with existing machinery and production workflows. | Reduces installation time and complexity. |
Automation Level | Degree of automation required, based on manual or automated operations. | Matches the desired level of precision and labor input. |
Real-Time Monitoring | Availability of sensors or feedback mechanisms for real-time tension adjustments. | Maintains consistent tension for high-quality output. |
Material Versatility | Ability to handle tension control in a wide range of materials without frequent reconfigurations. | Reduces downtime and increases flexibility. |
Maintenance Requirements | Ease of maintenance and durability of the tension control system. | Minimizes downtime and long-term costs. |
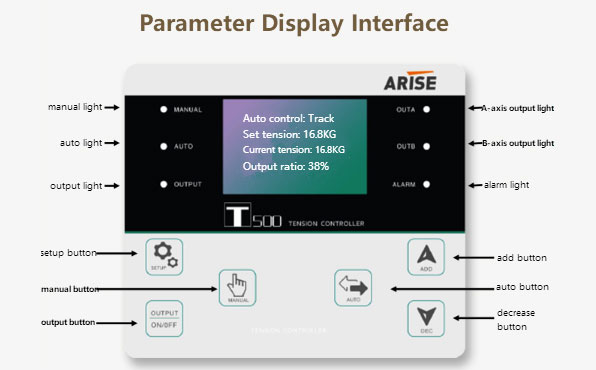
Conclusion
Through understanding the unique requirements of small-scale setups and investing in tailored tension control solutions, businesses can achieve significant gains in performance and competitiveness. Whether through manual devices, dancer rolls, or advanced closed-loop tension control systems, selecting the right technology ensures a smooth production process and superior results.