What are 100% Automated Printing Inspection Systems
As the fast-paced development in printing industries and high- quality products demanded, precision, speed, and consistency are key factors for success. With industries relying on high-quality printed materials, the need for flawless prints has become more critical. This is where 100% automated printing inspection systems come into play. These cutting-edge systems have revolutionized the way we approach in printing quality control, ensuring that every printed product meets the highest standards of excellence without the need for manual inspection.
Table of Contents
Understanding the Need for Automation in Printing Inspection Systems
Traditional methods of inspecting printed materials often rely heavily on manual inspection, which can be time-consuming, prone to human error, and limited in its ability to detect subtle defects. With the increasing complexity of print designs and the growing demand for high-volume production, relying on human intervention alone can lead to inconsistencies, defects, and inefficiencies.
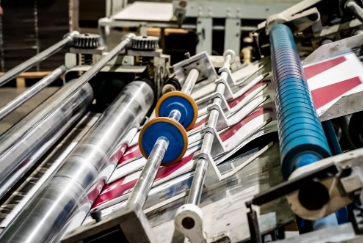
Automation addresses these challenges by introducing printing Inspection systems that can detect even the smallest defects with unmatched speed and accuracy. These innovations are transforming industries such as packaging, commercial printing, textiles, and label printing, where product quality directly impacts brand reputation and customer satisfaction.
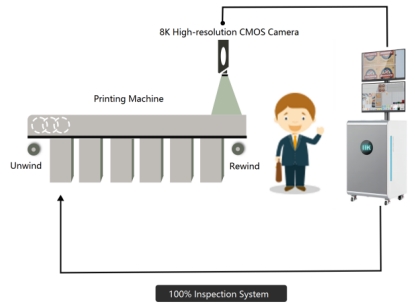
Key Technologies Driving the Advancement of 100% Automated Printing Inspection Systems
1. High-Resolution Optical Imaging
One of the foundational innovations in automated printing inspection is the use of high-resolution optical imaging. These systems employ advanced cameras, including multi-spectral and hyper-spectral cameras, to capture highly detailed images of printed materials. This allows for the detection of even the most subtle defects, such as color variations, misalignments, and defects in the print texture, at a microscopic level. The ability to detect these imperfections in real-time ensures that no defective products make it to the market.
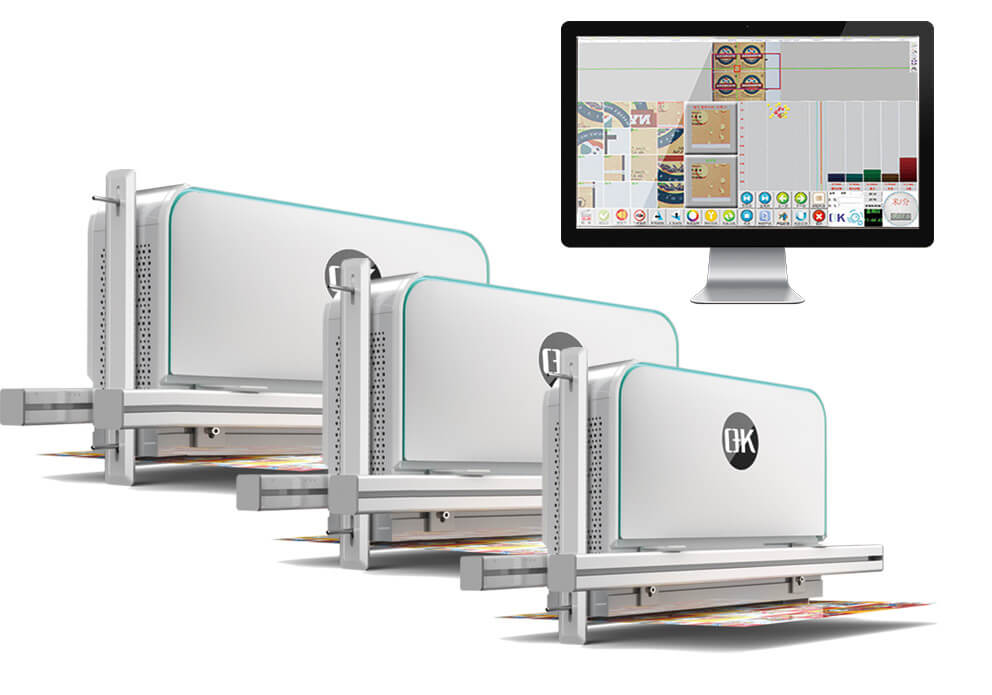
2. Artificial Intelligence (AI) and Machine Learning (ML)
The integration of AI and ML algorithms has significantly enhanced the capabilities of automated inspection systems. These technologies allow the systems to learn from large datasets, improving their ability to detect defects over time. AI can recognize patterns in the print, identify recurring problems, and adapt the inspection criteria based on real-time data. This results in fewer false positives, increased accuracy, and a higher level of adaptability to different printing processes and materials.
3. Inline Inspection with Real-Time Corrections
In modern printing production lines, speed is essential. Inline inspection systems are designed to operate in tandem with the printing process, offering continuous monitoring without interrupting the production flow. These systems can detect defects as they occur and provide real-time feedback to operators, allowing for immediate adjustments. For instance, if a misalignment or color issue is detected, the system can automatically adjust the printing parameters, ensuring consistent quality without production delays.
4. Color and Registration Control
One of the most critical aspects of print quality is maintaining color accuracy and registration. Automated inspection systems use color sensors and registration detectors to monitor these variables in real time. By comparing the printed output with predefined color standards and alignment references, the system can ensure that color fidelity is maintained across the entire print run. This innovation is particularly beneficial in industries like packaging and labels, where color consistency is essential for brand recognition and consumer trust.
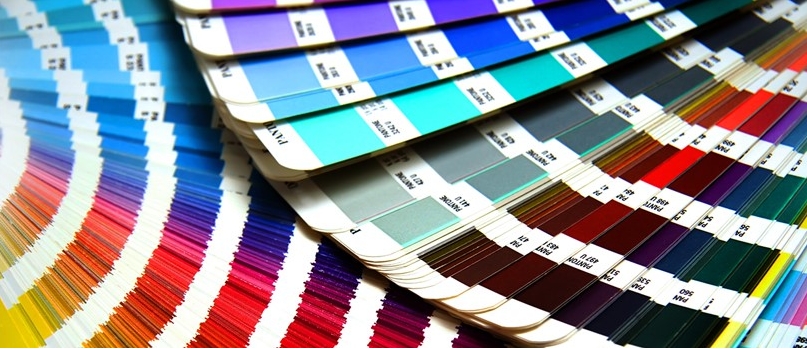
5. Smart Analytics and Reporting
Advanced analytics have become an integral part of automated printing inspection systems. These systems collect vast amounts of data during each print job, and the information is analyzed to provide insights into print quality trends, defect rates, and production efficiency. Manufacturers can access detailed reports that identify the root causes of recurring defects and suggest improvements to the production process. This data-driven approach helps companies optimize their workflows, reduce waste, and improve overall product quality.
6. Multi-Print Technology Integration
With the rise of multicolor printing and multimedia applications, automated inspection systems have evolved to handle complex print jobs that involve different materials, ink types, and printing techniques. By incorporating multi-print technology, these systems are capable of inspecting a variety of print types—ranging from digital, flexographic, and offset to screen printing—ensuring comprehensive quality control across different processes. This flexibility allows companies to use a single inspection system for various printing methods, simplifying operations and reducing the need for specialized equipment.
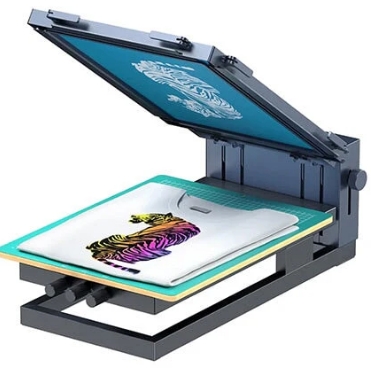
7. UV and Infrared Inspection
For specialized applications, such as security printing, packaging, and labeling, some automated inspection systems are equipped with UV (ultraviolet) and infrared sensors. These sensors can detect inks or coatings that are invisible to the naked eye but are critical for ensuring security features (e.g., anti-counterfeit markings) or print durability. The integration of UV and infrared technology allows for non-visible defect detection, ensuring that even hidden issues, like improper curing or coating anomalies, are caught early in the process.
8. Cloud-Based Connectivity and Remote Monitoring
With the advent of cloud-based platforms, modern inspection systems allow for remote monitoring and data sharing across different production facilities. Cloud integration provides manufacturers with the ability to monitor print quality in real time from any location, facilitating quicker decision-making and better collaboration between teams. Additionally, cloud-based analytics enable businesses to track long-term trends in print quality, empowering them to optimize maintenance schedules, reduce downtime, and improve operational efficiency.
9. Enhanced User Interfaces and Customization
Modern automated inspection systems come with intuitive user interfaces (UIs) that make the inspection process easier to control and customize. Operators can adjust the system’s settings according to specific print requirements and material types. These interfaces also offer visual defect tracking, where operators can visually review flagged defects and make manual adjustments if necessary. This user-friendly approach enhances the efficiency of quality control while reducing the complexity associated with operating high-tech inspection systems.
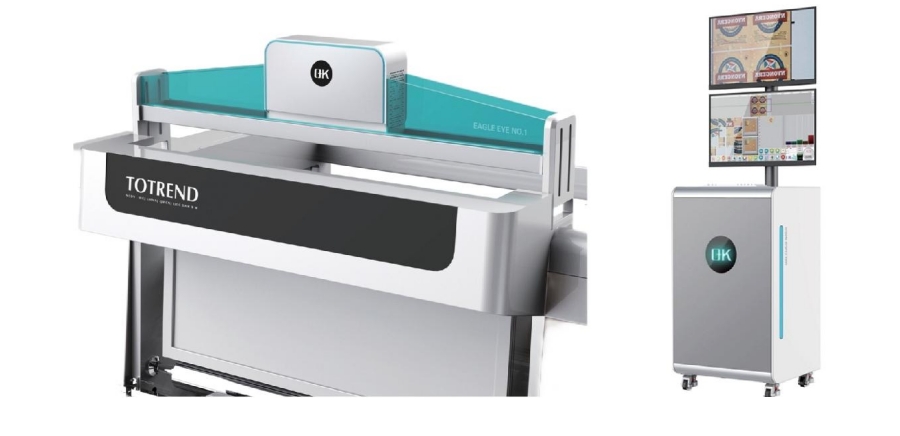
Benefits of 100% Automated Printing Inspection Systems
- Increased Speed and Efficiency: Automated print inspection systems operate at a much faster pace than human inspectors, enabling continuous inspection during high-speed production runs. This results in increased throughput and a reduction in production delays due to inspection bottlenecks.
- Enhanced Accuracy and Consistency: Automated systems are capable of detecting defects with incredible accuracy, ensuring that no flaws are overlooked. This consistency leads to improved product quality and reduces the likelihood of defective items reaching the customer.
- Cost Savings: By reducing the need for manual inspection and eliminating human error, automated systems lower operational costs. They also minimize material waste and rework by identifying defects early in the production process, which helps keep production lines running smoothly.
- Real-Time Quality Control: With the ability to provide real-time feedback and corrections, printing inspection systems empower operators to address issues immediately, ensuring that high-quality standards are maintained throughout the entire production run.
- Scalability: Automated inspection systems for print quality are highly scalable, making them suitable for both small-scale operations and large-scale printing businesses. These systems can be easily integrated into existing production lines, offering flexibility for various production environments.
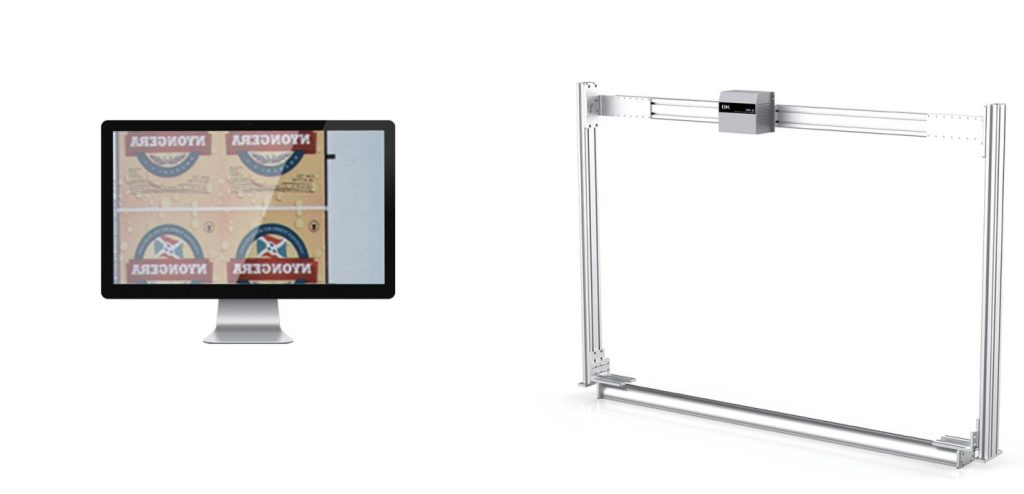
Applications of 100% Automated Printing Inspection Systems
This chart presents a detailed overview of the applications of 100% automated printing inspection systems, focus on how these systems ensure high-quality standards across various industries.
Application | Description | Examples |
Packaging Industry | Ensures the quality of printed packaging materials, detecting defects like misalignments, color variations, and print smudges. | – Inspecting packaging for food and beverages to ensure accurate color, registration, and label integrity. – Detecting defects in printed cardboard and flexible packaging. |
Labeling | Verifies the accuracy of text, images, and barcode alignment on labels, ensuring that they meet regulatory and brand standards. | – Pharmaceutical labels to ensure proper text alignment, expiration dates, and batch numbers. – Beverage labels, confirming text clarity, barcodes, and color accuracy. |
Security Printing | Verifies the authenticity of printed security features such as watermarks, UV inks, holograms, and other covert markers. | – Banknote printing for detecting hidden security features like UV markings or holographic strips. – Inspection of tax stamps and official documents with embedded security features. |
Pharmaceutical Industry | Ensures that printed labels on pharmaceutical products comply with regulatory requirements and maintain readability and accuracy. | – Verifying accuracy of batch numbers, expiration dates, and other critical information on drug packaging. – Ensuring proper alignment and clarity of warning labels on medical devices and medicines. |
Textile and Fabric Printing | Inspects textile prints for color accuracy, pattern alignment, and the detection of defects like smudges or irregular patterns. | – Checking prints on clothing, ensuring accurate color reproduction and pattern alignment. – Inspecting fabric prints for defects, like smears or color mismatches, in textile manufacturing. |
Commercial Print Jobs | Inspects printed materials such as brochures, posters, and catalogs for color consistency, image sharpness, and text alignment. | – Verifying consistency of colors in marketing materials or direct mail pieces. – Ensuring text and graphics are properly aligned and printed clearly in publications. |
Graphic Arts | Ensures high-quality reproduction of graphic designs by verifying color fidelity, registration, and print accuracy. | – Inspecting fine art prints for accurate color matching and image clarity. – Quality check for custom graphic designs or promotional material prints. |
Automotive & Electronics | Verifies the quality and precision of printed labels or markings on automotive parts and electronic components. | – Inspecting serial numbers, safety instructions, and warning labels on car parts. – Verifying component labels on circuit boards or smartphones to ensure they are legible and correctly placed. |
Food and Beverage Industry | Ensures compliance with labeling standards, including nutritional information, barcodes, and branding elements. | – Verifying label integrity and regulatory compliance for food products. – Checking accuracy of ingredient lists, nutritional information, and barcode placements on beverage packaging. |
Direct Mail and Mailing Services | Inspects printed direct mail pieces, catalogs, and promotional materials to ensure proper text placement and image quality. | – Ensuring accurate printing and alignment of addresses, barcodes, and marketing messages on direct mail materials. – Verifying clarity and consistency in promotional materials for bulk mailing. |
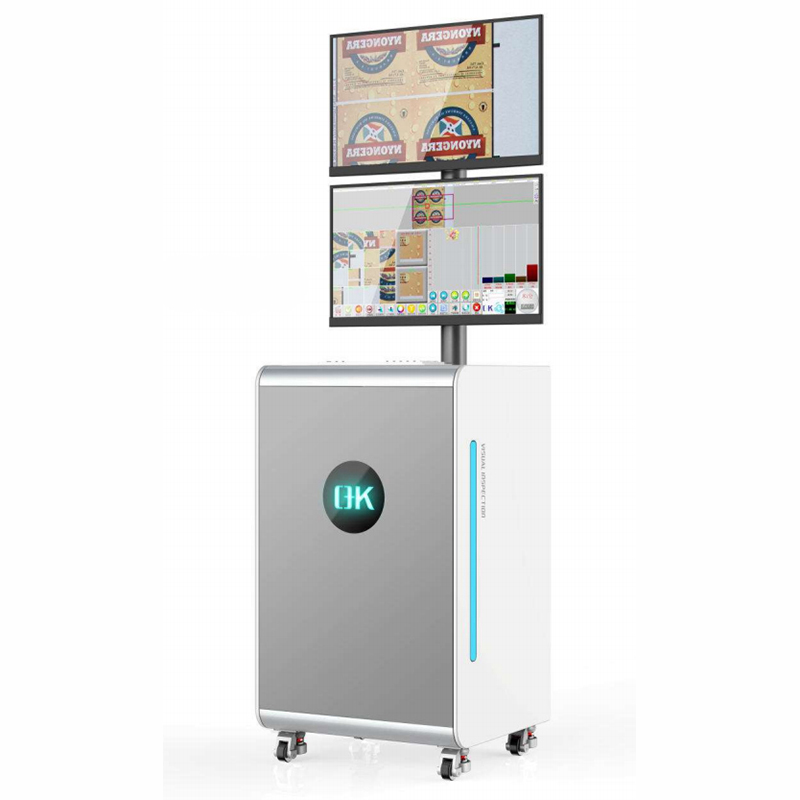
Final Thoughts
100% automated printing inspection systems are transforming the way print quality is maintained in high-volume production environments. With innovations such as high-resolution Imaging, AI-driven defect detection, real-time inline feedback and other multi technologies integration, these systems offer unprecedented accuracy, speed, and scalability.