Web Inspection Systems for Wide Web vs. Narrow Web Printing
In the competitive printing industry, web inspection systems are essential in ensuring defect-free outputs across various applications. These systems are designed to monitor the quality of continuous printed substrates, identifying defects in real-time to prevent waste, reduce rework, and maintain brand integrity. However, the needs of wide web and narrow web printing environments differ significantly, calling for tailored printing inspection solutions for each.
Table of Contents
Understanding Wide Web and Narrow Web Printing
Wide web printing typically involves substrates wider than 40 inches (1,000 mm), often used in flexible packaging, wallpaper, and large-scale publications. These processes are high-speed and high-volume, focusing on consistency across large surface areas.
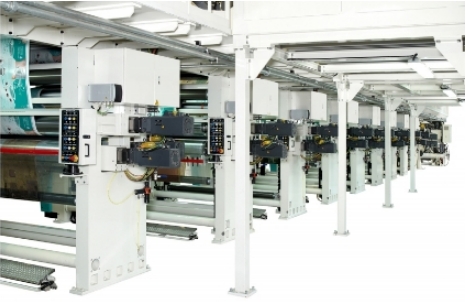
Narrow web printing, by contrast, handles web widths usually under 20 inches (500 mm). It is widely used in the production of labels, tags, and specialty packaging, where shorter runs and rapid design changes are common.
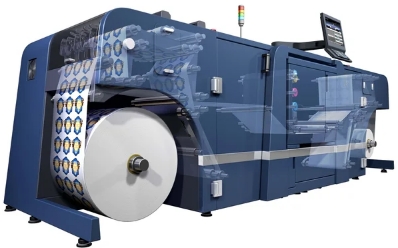
Key Differences in Web Inspection Systems for Wide Web vs. Narrow Web Printing
Understanding the fundamental differences between these two applications is essential for selecting the right printing inspection system that matches operational needs and performance goals.
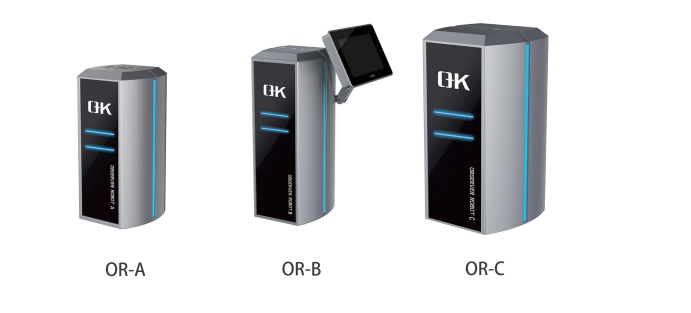
1. Web Width and Area Coverage
One of the most obvious differences lies in the physical width of the printed material. Wide web printing, often used for large-scale applications such as flexible packaging, newspapers, and wallpaper, involves web widths typically greater than 40 inches. This requires inspection systems capable of covering broad surface areas efficiently. To achieve full coverage, multiple cameras and lighting units must be strategically positioned to scan the entire web.
In contrast, narrow web printing, which is commonly used for labels, tags, and small packaging formats, involves substrates less than 20 inches wide. This significantly reduces the area the system needs to monitor. In many cases, a single high-resolution camera with a suitable lighting arrangement is sufficient to inspect the entire web width.
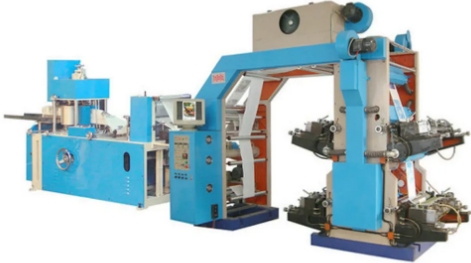
2. Speed and Data Processing Capabilities
Wide web printing lines often operate at high speeds to meet large-volume production demands. Web inspection systems for these setups must therefore be capable of processing massive volumes of image data in real time. The system must analyze data from multiple cameras simultaneously, requiring powerful processing hardware and intelligent software to ensure that no defect is missed, even at high speeds.
Narrow web inspection systems, while still operating at considerable speeds, typically have lower throughput. This allows for simpler, more streamlined data processing. The inspection software in these systems is optimized for detail and accuracy, especially important for identifying fine defects such as barcode errors, misprints, or micro-text faults that can be critical in label printing.
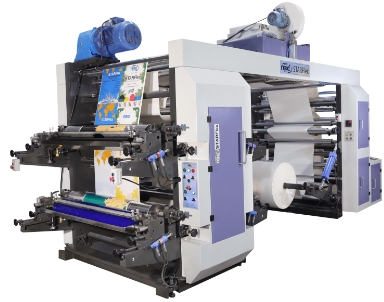
3. Camera Configuration and Resolution
Due to the larger area in wide web applications, inspection systems often incorporate several cameras arranged in a linear or tiled layout. These cameras must be precisely calibrated to ensure seamless stitching of images and consistent defect detection across the web. The resolution of each camera must be high enough to detect minute flaws over a wide field of view.
In narrow web applications, a single or dual-camera setup is typically adequate. Since the web is narrower, the camera can focus more closely on small sections of the material, allowing for higher optical resolution and sharper detection capabilities. The reduced complexity also makes narrow web systems easier to install, maintain, and calibrate.
4. Lighting Systems
Uniform and powerful lighting is critical in wide web printing inspections due to the sheer width and material variety. These systems often use synchronized LED lighting modules to ensure consistent illumination across the web. Achieving even lighting over a wide surface can be challenging, particularly for reflective or textured materials.
Narrow web inspection systems, on the other hand, have more flexibility in lighting design. With a smaller inspection zone, it’s easier to create ideal lighting conditions using compact light sources. This contributes to greater image clarity and better detection accuracy, particularly for subtle print defects.
5. Integration with Production Lines
Wide web inspection systems are usually integrated into comprehensive printing production workflows that include printing presses, slitting machines, and rewinders. These systems often feature centralized defect mapping, reporting tools, and automated feedback to printing controls for real-time adjustments.
Narrow web inspection systems tend to be more modular. They are commonly added as plug-and-play units to existing narrow web presses or digital label printers. Their adaptability makes them suitable for converters handling frequent job changes and variable printing formats.
6. Cost and Scalability
Given their complexity and scale, wide web inspection systems generally require a higher investment. However, their capabilities deliver substantial value in minimizing waste, preventing large-scale defects, and maintaining high production efficiency. These systems are best suited for operations that require continuous output over long runs.
Narrow web inspection systems are more cost-effective and are typically favored by small to medium-sized businesses. They offer excellent return on investment through improved quality control, faster defect detection, and reduced material wastage in short-run production environments.
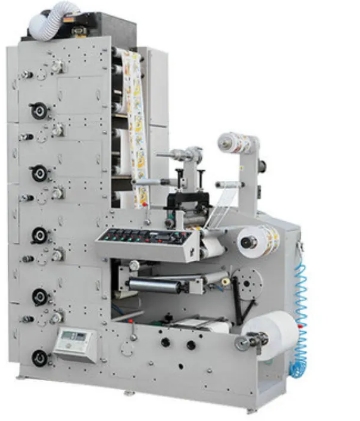
Printing Defects Detected Through Web Inspection Systems: Wide Web vs. Narrow Web Printing
Defect Type | Wide Web Printing | Narrow Web Printing |
Color Variation | Common due to large surface area and ink spread | Detected in fine gradients on small labels or tags |
Registration Misalignment | Large-scale shift across width | Micro-level shift affecting small text or barcodes |
Streaks and Banding | Caused by ink delivery or roller issues | Less common but critical in fine graphics |
Coating Gaps or Overlays | Significant in flexible packaging or wallpaper | Detected in adhesive or varnish layers |
Scratches or Substrate Damage | Visible across wide areas due to material handling | Critical for pharmaceutical or cosmetic labels |
Missing Print Elements | Entire sections may be affected | Barcodes, serial numbers, or fine design details |
Smudging or Ink Splashes | Broad surface ink smears | Localized, small-scale, yet highly visible |
Die-Cut or Finishing Defects | Detected in post-print inspection | Common in label edges or perforations |
Repeating Pattern Defects | Roller or plate-related issues across width | Affect logo consistency on multiple labels |
Barcode and QR Code Errors | Occasionally checked in packaging | Frequently detected and verified in label printing |
Text Clarity Issues | Detected but less critical in large graphics | Extremely critical in small product information text |
Delamination or Curling | Noticed during high-speed rewind | Especially relevant in multilayer narrow substrates |
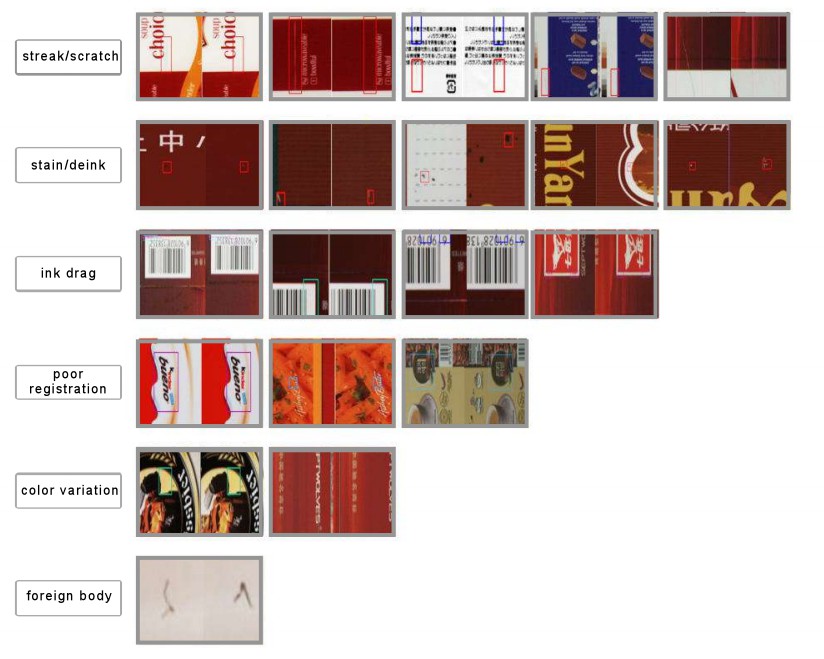
Future Trends in Web Inspection Systems for Wide Web and Narrow Web Printing
As industry demands evolve, so too do the technologies underpinning inspection capabilities. Emerging trends reflect a clear shift toward smarter, faster, and more adaptive web inspection systems. While the goals remain the same, defect detection and process optimization and the future of print inspection system promises a tailored evolution for both wide and narrow web applications.
1. Artificial Intelligence and Machine Learning Integration
One of the most significant advancements across both printing formats is the adoption of artificial intelligence (AI) and machine learning. Future web inspection systems will move beyond static rule-based defect detection to more adaptive, self-learning algorithms. These systems will be able to distinguish between acceptable variations and true defects, reducing false positives and improving detection reliability over time.
For wide web printing, AI will prove essential in handling the large volume of image data collected from multiple camera arrays, optimizing real-time analytics and defect categorization. In narrow web applications, AI will enhance the precision required for detailed inspections of barcodes, microtext, and security features.
2. Cloud-Connected and Industry 4.0 Integration
Another forward-looking trend is the deep integration of web inspection systems into cloud platforms and smart factory environments. In wide web applications, cloud connectivity enables centralized quality monitoring across multiple production lines, offering plant-wide or even enterprise-wide analytics and predictive maintenance.
For narrow web printers, especially smaller operations or label converters, cloud platforms will make advanced inspection accessible at a lower cost, with remote monitoring, instant updates, and simplified maintenance.
3. Higher Resolution Imaging and Enhanced Optics
Resolution demands are increasing across the board. Advanced 100% printing inspection systems will offer ultra-high-resolution cameras coupled with advanced optics and multispectral imaging to detect defects invisible under traditional lighting. In wide web printing, this helps uncover issues like faint banding or color drift across broad areas. In narrow web, the increased resolution supports verification of extremely fine print details, such as security patterns or serial codes.
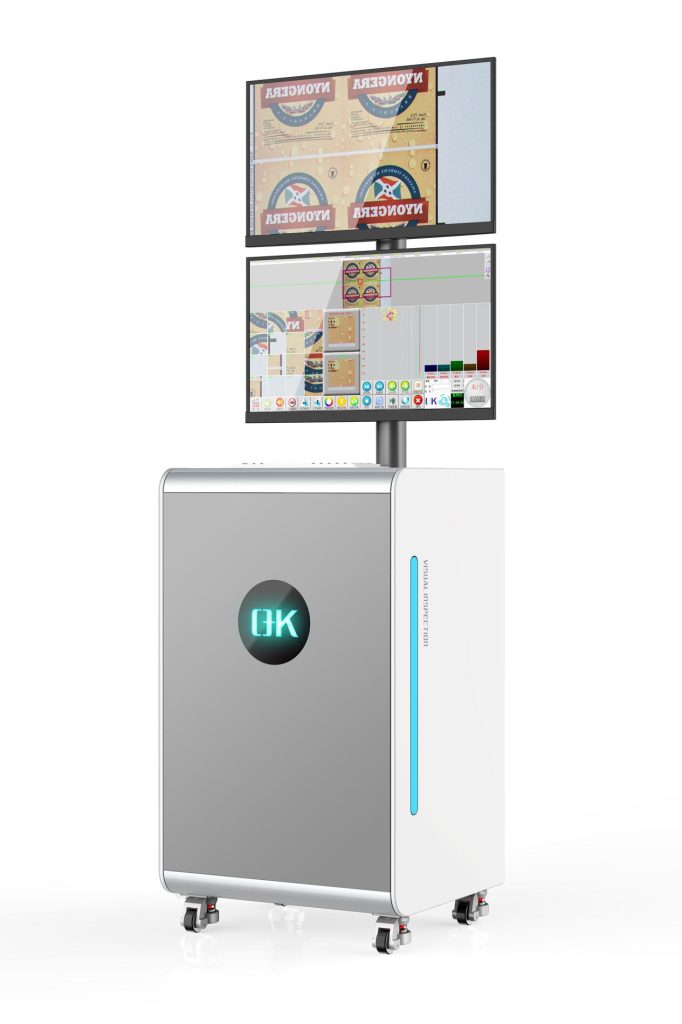
4. Real-Time Feedback and Autonomous Correction
Web inspection systems are moving toward greater autonomy. In wide web printing, real-time feedback loops will be able to communicate directly with press control systems, allowing automatic adjustments to ink flow, tension, or register alignment based on detected anomalies. For narrow web systems, real-time corrections may include adjusting cutting or slitting parameters to maintain label precision.
This trend enhances quality assurance and reduces dependency on manual interventions, especially in fast-paced or unattended operations.
5. Modular and Scalable Designs
Manufacturers are increasingly focusing on flexibility. Web inspection systems are becoming more modular, allowing printers to scale up inspection capabilities based on project needs. In wide web printing, this means the ability to add more cameras or lighting modules for wider or higher-speed lines. For narrow web printers, modular systems mean adapting easily to changes in job types or substrates, a frequent requirement in label and tag printing.
6. Sustainability and Waste Reduction
As sustainability becomes a global priority, web inspection systems will also play a growing role in waste minimization. Smart defect classification and tracking help identify the root causes of defects, enabling more sustainable practices by reducing material waste, ink usage, and energy consumption. In wide web printing, this is especially valuable given the high volumes and expensive materials involved. In narrow web, it helps smaller printers maintain eco-conscious production at scale.
7. Customization and Application-Specific Solutions
Lastly, there’s a growing trend toward customizing industry-specific web inspection systems. For instance, wide web systems used in flexible packaging may include capabilities tailored to metallized film or translucent substrates, while narrow web systems in the pharmaceutical or beverage sector will increasingly feature compliance-based inspection protocols, such as pharma-grade serialization or food-grade labeling checks.
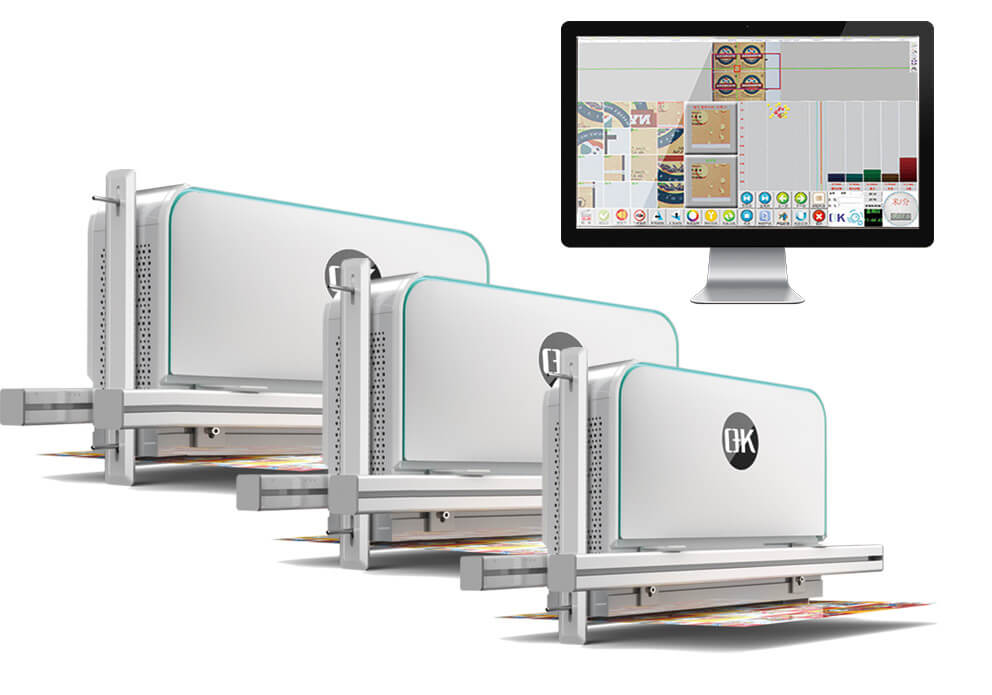
Final Words
Web inspection systems are vital for maintaining high print quality and operational efficiency. While both wide and narrow web printing benefit from these technologies, the design and implementation of the printing inspection systems must align with the specific demands of the web width, printing speed and product type. Choosing the right web inspection system ensures optimal performance, minimal waste, and enhanced customer satisfaction.