Web Guiding System Effectively Used For Edge Position Control
web guiding system can ensure continuous, precise edge position control of various coil materials in various manufacturing processes, ensuring that the material does not deviate from the correct position and minimizing waste and downtime,
What Causes Acceleration Offsets In The Process Of The Edge Position Control
One of the most troublesome edge position deviations is known as the acceleration or ramp offset. When the machine speed is increased or decreased, the web moves sideways. The rate of movement is usually greatest at the top and bottom of the speed difference rather than on the speed ramp itself. Unfortunately, the term “acceleration offset” misrepresents the true nature of the edge movement. Indeed, the web has no idea how fast it is moving.
As a result, every roller or element that touches the web also steers it. The path of the web, on the other hand, will remain constant if the roller is stationary and the state of traction is constant. That is not to say it is straightforward. The web will obviously snake through the machine in accordance with web handling laws. What we mean is that the path will, for the most part, remain consistent.
However, if the web switches from full to partial tracking, the web’s path will shift slightly in response. This shift in traction will be subtle and difficult to detect using traditional observations and measurements. Nonetheless, it will move the web in response.
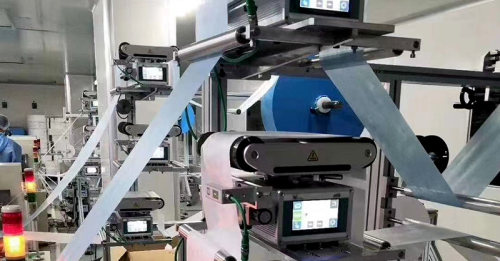
Why Choose Web Guiding System For Edge Position Control
The automatic web guiding system is made up of components such as a correction control board, a correction controller, controller, an actuator, and so on. The photoelectric switch tests the edge or line part to pick up the deviation data signal and wirelessly transmit the data to the photoelectric control board for logical operation, as well as send the manipulation data signal to the mechanical electric actuator. The electric actuator, also known as an electric driver, is responsible for adjusting the deviation of the coil material during operation to ensure uniform linear motion. It provides edge alignment to avoid deviation of the waterproof coiled material during the entire production and processing process, as well as ensuring accurate and stable performance of the waterproof coiled material during the entire production process with the neatly divided rewinding machine.
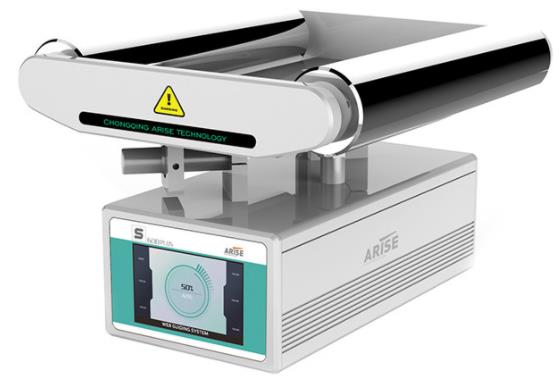
How Does The Web Guiding System Work
A sensor, an actuator, and a controller comprise a web guiding system. Any detector that can reliably detect the edges of a web can be used as the sensor. Pneumatic (nonporous webs), photoelectric (opaque webs), and paddies are the most common (thick webs). Through the edge sensor, the web must be flat (no curl) and stable (no flutter). The sensor is frequently placed near a roller for this and other reasons. The web could be guided to the front edge, back edge, or center if two sensors are used.
The sensor’s output is routed to a controller, which sends a movement command to the actuator. If the controller’s gain is too low, the guide’s response will be sluggish and slow to correct. If the controller’s gain is too high, the guide will be hot but overshoot, and may even be unstable. For smaller assemblies, the actuator may be a stepper motor and ballscrew, while for larger assemblies, it may be a hydraulic cylinder. For responsive operation, the actuator and framework must be stiff.