Three Commonly Seen Faults Of Tension Control System
There are many factors that affect the tension control system, which in turn can lead to related failures. According to the structure and working principle of the tension control system, analyzing and finding out the causes, and solving the problems with correct methods to ensure stable operation of the tension control system. This article introduces three commonly seen faults and their solutions.
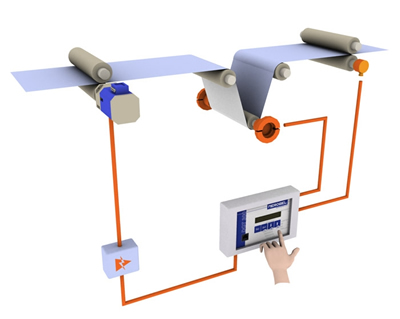
1. Inaccurate Overprinting Of Tension Control System
Fault phenomenon
During the normal operation of the printing equipment, the swing roller swings irregularly and the swing amplitude is large, resulting in inaccurate overprinting.
Solutions
The structure of the tension control system is relatively complex, so there are many reasons for this failure, mainly in the following aspects.
(1) The pneumatic control circuit components of the swing roller cylinder are prone to damage, resulting in piston leakage and unstable loading pressure of the swing roller cylinder. In this regard, it may be considered to replace damaged pneumatic circuit components, and it is necessary to replace the swing roller cylinder if necessary.
(2) The high-precision potentiometer operates for a long time within a certain range, and once the resistance value in that range changes, it is easy to cause the feedback signal of the high-precision potentiometer to be unstable. At this point, the high-precision potentiometer should be replaced in a timely manner.
(3) The gap at the connection between the potentiometer gear and the rotary shaft gear is too large. When the tension changes, the position of the swing roller will change. However, due to the existence of the gap, it is easy to cause the swing roller to continuously swing back and forth, thereby affecting the printing accuracy. For this, the clearance should be adjusted according to standards.
2. Unstable Tension Of Tension Control System
Fault phenomenon
During the winding process, when the winding diameter is large, the winding tension display value often decreases as the winding diameter increases. At this time, the output current of the driver will continue to increase. When the output current exceeds the rated current of the motor, it will cause the driver overcurrent protection and send a fault alarm.
Solutions
First, check the load of the driver and the motor speed encoder, both of which are normal. After calibrating the winding web tension controller, it was found that one of the tension sensors had malfunctioned, resulting in the detected winding tension signal value being half of the actual winding tension value. As the winding diameter increases, in order to achieve the predetermined winding tension, the web tension controller will continuously increase the output until 100%. At this time, the actual winding tension has far exceeded the predetermined winding tension, and the reel material is very tight. The load also increases, resulting in drive overcurrent protection. After replacing the tension sensor and recalibrating, the system returns to normal. It should be noted that when calibrating the winding tension controller, the weight used should be as close to the full tension value as possible to improve the tension control accuracy.
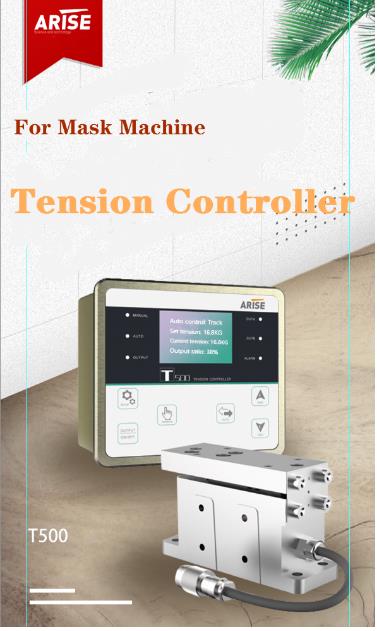
3. Excessive Winding Starting Tension Of Tension Control System
Fault phenomenon
When the winding tension control system starts, it exceeds the full tension value of the winding tension controller, and the equipment needs to run for about 2 minutes to achieve constant tension operation. This not only wastes a large amount of raw materials, reducing the yield but also easily causes zero displacements of the tension sensor, leading to deviation in the tension control value.
Solutions
First, adjust the input signal of the driver, the gain, bias, and PID values of the tension feedback signal, but the fault still exists. Check whether the tension reset signal and tension sensor signal are normal. When detecting the take-up tension controller, it was found that its internal stall storage reset point was damaged, while the external reset signal of the take-up tension controller was normal. In fact, the take-up tension controller not only did not reset but also stored the take-up tension value of the previous roll, resulting in a large take-up starting tension problem. After repairing the internal stall storage reset point of the winding tension controller and replacing damaged parts, the winding starting tension will return to normal.