The Vital Role of Regular Maintenance and Calibration in Web Guiding Systems
Precision and accuracy are extremely important in industrial manufacturing. This is especially true in operations that include continuous webs of materials such as paper, film, or foil, where even tiny variations can result in costly faults and production delays. To ensure seamless operations and high-quality outputs, regular maintenance and calibration of web guiding systems are indispensable. In this article, we explore the significance of maintenance and calibration practices in maximizing the efficiency and reliability of web guiding systems.
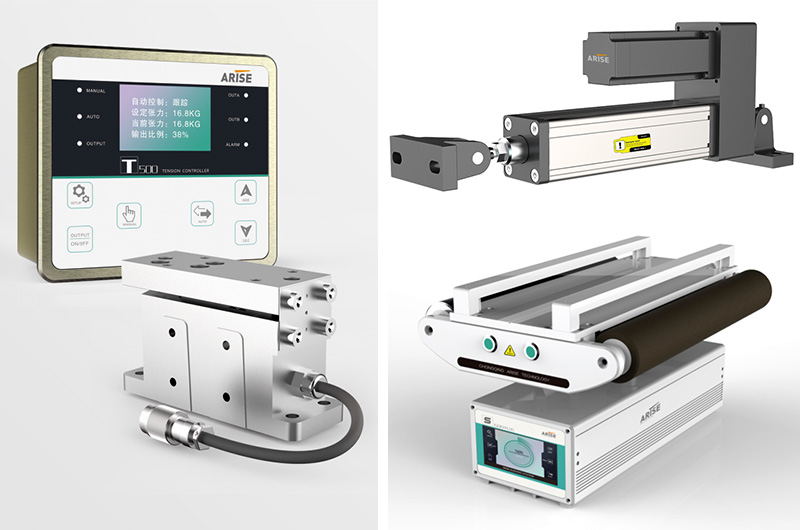
The Importance of Web Guiding Systems
Importance | Description |
Precision and Accuracy | Web guiding systems ensure precise alignment and tension control of continuous webs, preventing defects and maintaining product quality. |
Minimize Waste | By minimizing misalignments and tension variations, web guiding systems reduce material waste and optimize production efficiency. |
Enhance Productivity | Improved alignment and tension control lead to smoother production processes, reducing downtime and increasing throughput. |
Quality Assurance | Web guiding systems contribute to consistent product quality by preventing defects and deviations in the web material. |
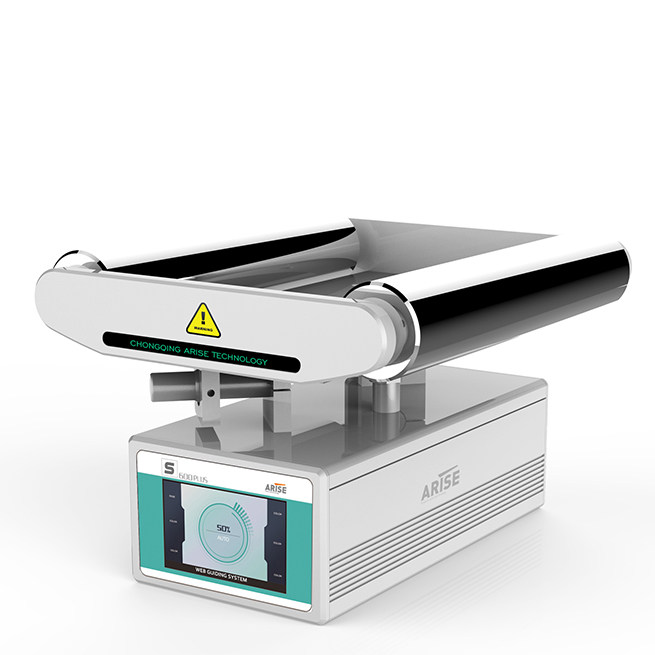
Regular Maintenance Practices in Web Guiding Systems
Regular maintenance is key to ensuring the continued functionality and reliability of web guiding systems.
1. Cleaning and Inspection
Regular cleaning and inspection are essential maintenance procedures for web guiding systems. Remove debris, dust, and residue from guiding rollers, sensors, and other components to keep them running smoothly. Visually evaluate for signs of wear, damage, or misalignment, and rectify any concerns as soon as possible to avoid future damage or performance loss.
2. Lubrication
Proper lubrication of moving parts is critical for decreasing friction, minimizing wear, and assuring smooth functioning of web guiding systems. Follow the manufacturer’s recommendations for lubrication type and frequency, and apply lubricant to bearings, rollers, and other components as needed. Regular lubrication extends component life and ensures maximum system operation.
3. Tension Adjustment
Maintaining proper web tension is essential for avoiding wrinkles, creases, and breaks throughout manufacture. Regularly check and change tension settings to ensure consistent tension levels across the web. Monitor tension variations throughout the manufacturing process and make adjustments as needed to reflect changes in material qualities or processing conditions.
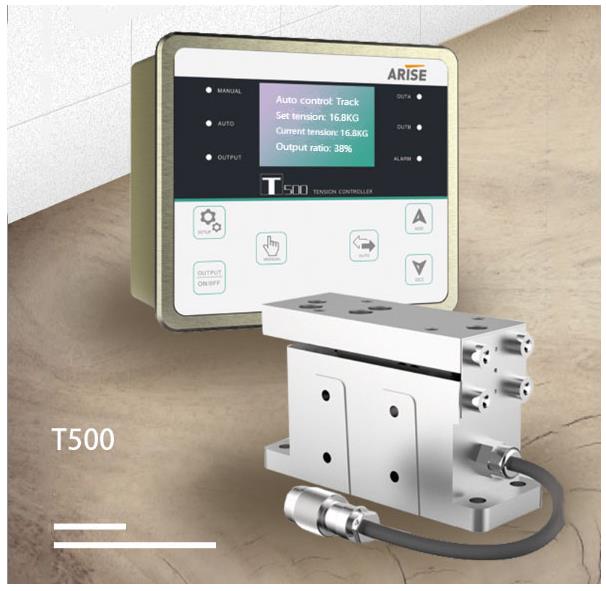
4. Alignment Verification
Regularly verify the alignment of the guiding rollers and sensors to ensure they are properly positioned relative to the web route. Use alignment tools and measurement techniques to ensure alignment accuracy and make necessary modifications. Proper alignment guarantees exact web guidance, reduces edge deviations, and maintains product quality.
5. Software Updates
Stay updated with the latest software releases provided by the manufacturer for web guiding systems. Software updates may include bug fixes, performance enhancements, and new features that improve system functionality and reliability. Install updates promptly to benefit from the latest improvements and ensure compatibility with other equipment and processes.
The Benefits of Regular Maintenance in Web Guiding Systems
Benefits | Description |
Improved Performance | Regular maintenance minimizes downtime and ensures consistent performance, leading to increased productivity and higher-quality outputs. |
Extended Lifespan | Proper maintenance reduces wear and tear on components, prolonging the lifespan of the web guiding system and reducing the likelihood of unexpected failures. |
Cost Savings | By preventing issues before they escalate, maintenance helps avoid costly repairs, material waste, and production delays. |
Enhanced Safety | Well-maintained web guiding systems operate safely, reducing the risk of accidents or injuries associated with equipment malfunction. |
Calibration Practices in Web Guidig Systems
In addition to regular maintenance, periodic calibration is essential to maintain accuracy and precision in web guiding systems. Calibration involves adjusting system parameters to ensure alignment, tension control, and sensor accuracy meet specified requirements.
1. Sensor Alignment
Accurate sensor alignment is critical for reliable detection of web position and deviations. Begin by verifying that web guide sensors are positioned perpendicular to the web path and aligned with the desired tracking position. Use alignment tools or reference markers to adjust sensor positions as needed, ensuring precise detection along the entire web width.
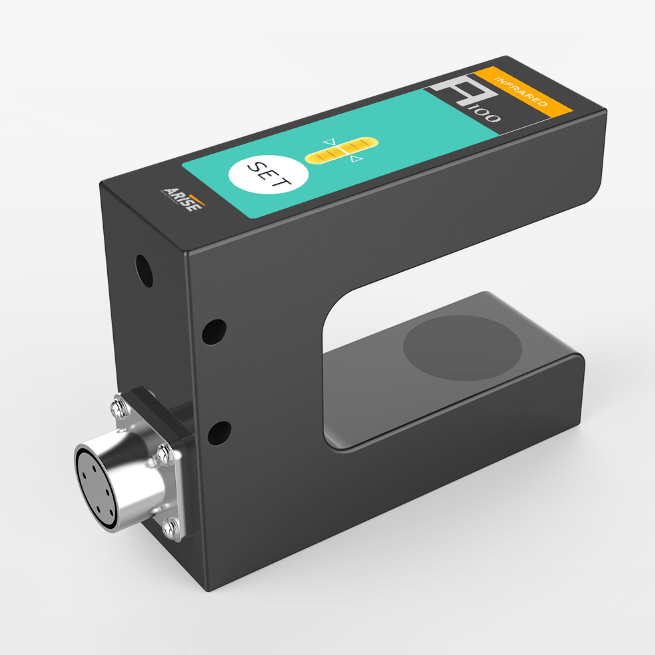
2. Tension Calibration
Proper tension calibration ensures that web tension remains consistent throughout the production process, reducing faults and material waste. Start by monitoring tension levels at several locations along the web path with tension sensors or load cells. Adjust tension control systems, such as dancer rollers or pneumatic brakes, to meet production requirements and material properties.
3. Position Control Adjustment
Calibrating position control settings is critical for maintaining correct web alignment and minimizing edge deviations. Use calibration software or control panels to fine-tune position control settings, such as gain, offset, and response time. Conduct test runs to verify the effectiveness of adjustments and make further refinements as needed to achieve optimal alignment accuracy.
4. Sensor Sensitivity Optimization
Optimizing sensor sensitivity ensures reliable detection of web deviations, even at low contrast or speed variations. Adjust sensor sensitivity settings based on the material characteristics, web speed, and environmental conditions. Conduct sensitivity tests using simulated deviations or test patterns to validate sensor performance and fine-tune sensitivity levels for optimal detection.
5. Verification and Validation
After making calibration adjustments, it is essential to verify and validate system performance to ensure accuracy and reliability. Conduct test runs using representative production materials and operating conditions to evaluate the effectiveness of calibration adjustments. Compare actual performance against specified tolerances and adjust settings as needed to meet performance requirements.
6. Documentation and Record-Keeping
Maintain thorough records of calibration activities, including calibration dates, adjustment details, test results, and any deviations from requirements. Keep calibration records organized and easily available for future reference, audits, or regulatory compliance. Documenting calibration activities improves traceability and responsibility, which aids in troubleshooting and continuous improvement efforts for web guide system.
The Benefits of Calibration in Web Guiding Systems
Benefits | Description |
Improved Alignment | Calibration ensures precise alignment of web guiding systems, minimizing edge deviations and maintaining product quality. |
Consistent Tension Control | Proper calibration results in consistent web tension across the production process, reducing material waste and defects. |
Reliable Deviation Detection | Optimized sensor sensitivity through calibration ensures reliable detection of web deviations, minimizing errors and production disruptions. |
Enhanced Productivity | Calibration leads to smoother production processes, reducing downtime and increasing throughput, resulting in enhanced productivity. |
Conclusion
Regular maintenance and calibration are critical practices for guaranteeing the optimal performance and reliability of web guiding systems. Manufacturers can reduce downtime, eliminatimg defects, and increase production efficiency by following proactive maintenance schedules, conducting thorough inspections, and calibrating system parameters as needed.