The Vital Role of Automated Alignment in High-speed Web Guiding Applications
Table of Contents
In high-speed web guiding systems, precise alignment is critical to maintaining the quality and efficiency of the production process. These systems are commonly used in industries such as printing, packaging, and textiles, where large rolls of material (or web) are processed continuously. The demand for higher production speeds, coupled with the need for superior accuracy, has led to significant advancements in automated alignment technologies in web guiding applications.
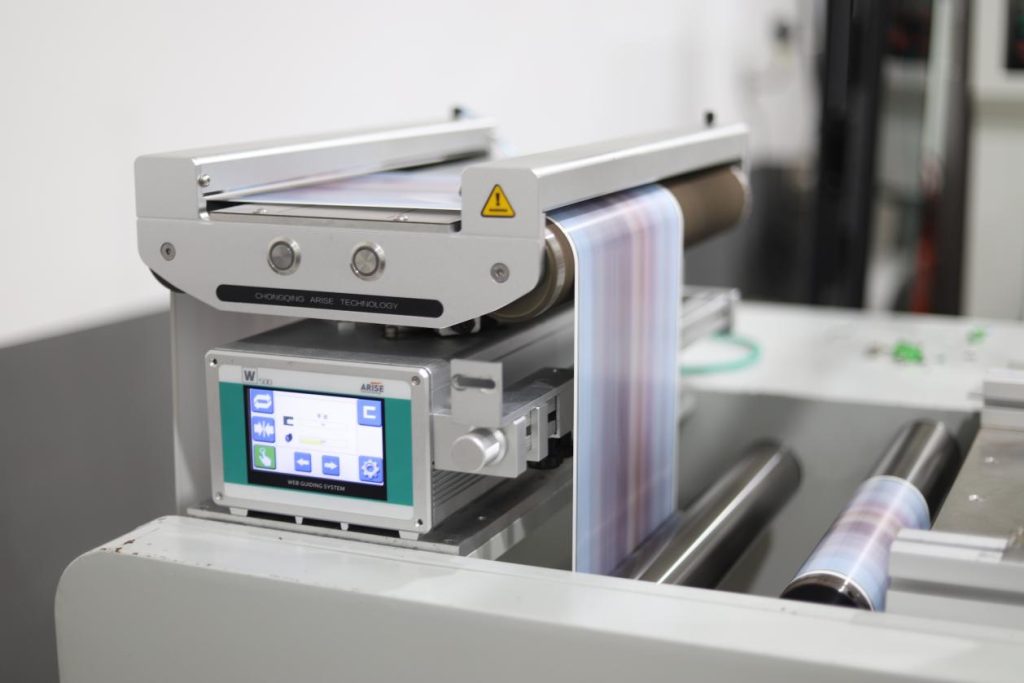
The Importance of Alignment in Web Guiding Systems
In web guiding systems, materials such as paper, plastic, or fabric are processed at high speeds, often over rollers, before undergoing operations such as printing, coating, or slitting. Without accurate alignment, the material can drift off course, resulting in defects, material waste, and equipment downtime. For instance, in a printing application, misalignment can cause ink to be applied unevenly or outside of intended areas, leading to quality issues.
Maintaining precise alignment is particularly challenging in high-speed operations due to factors like tension fluctuations, material variations, and machine vibrations. Automated alignment systems provide real-time correction to keep the web on track, enhancing both production efficiency and product quality.
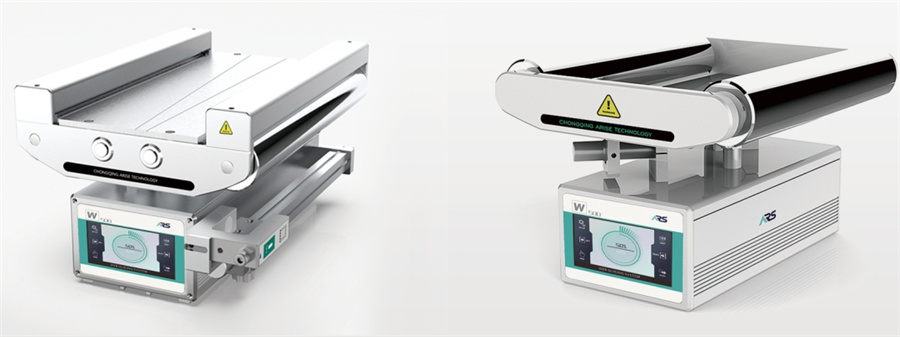
Key Components of Automated Web Guiding Systems
The key components that make up these web guide systems work together to monitor, adjust, and maintain the correct position of the web material.
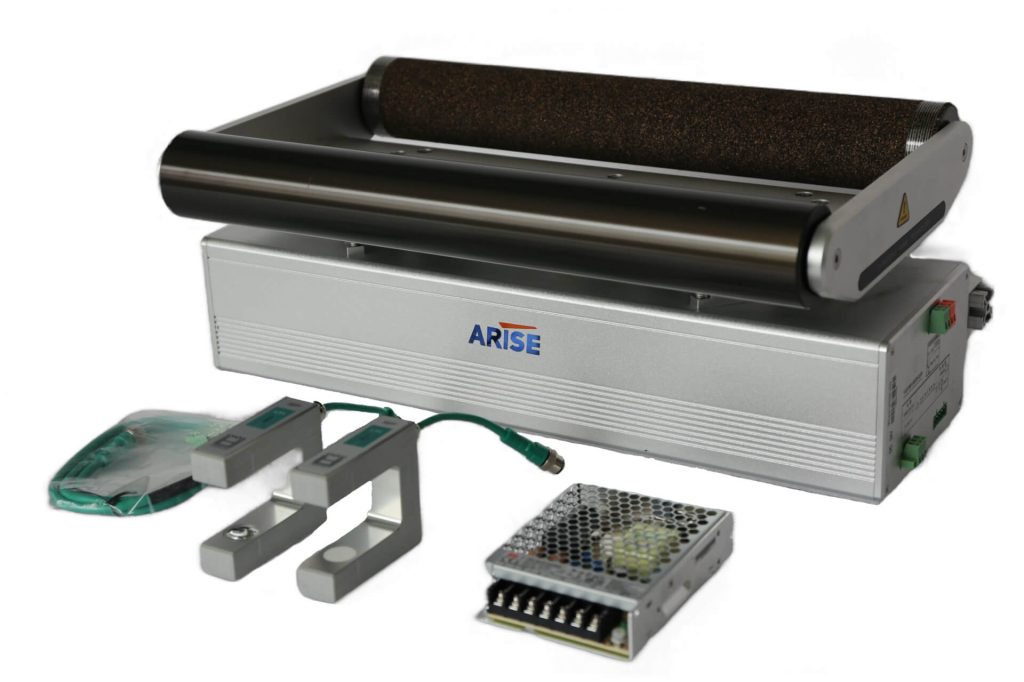
1. Sensors
Web guide sensors are critical to detecting the position of the web material in real time. They continuously monitor the web’s lateral position and provide feedback to the control system. The type of sensor used can vary based on the material and application:
- Optical Sensors: These are used for detecting the edges or contrasts of the material. They are ideal for transparent or thin materials.
- Ultrasonic Sensors: These ultrasonic edge sensors are useful for detecting opaque or reflective materials where optical sensors may not perform well. They emit ultrasonic waves to determine the distance from the web edge.
- Infrared Sensors: These infrared web guide sensors are used in heat-sensitive applications, offering non-contact detection of the web position.
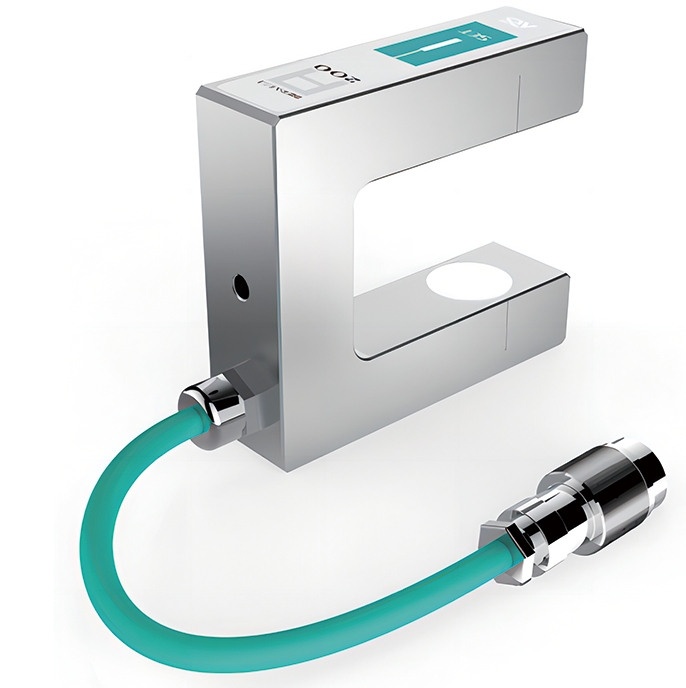
2. Actuators
Web guiding actuators are mechanical devices responsible for physically moving the web or the guiding rollers to correct any misalignment. Upon receiving instructions from the control system, actuators make precise adjustments to the web’s position.
- Servo Motors: Highly accurate motors used to move rollers or other guiding mechanisms with precision.
- Stepper Motors: These motors move incrementally and are often used in positioning tasks where fine control is needed.
- Linear Actuators: These are used to create straight-line movements, adjusting the lateral position of the web as required.
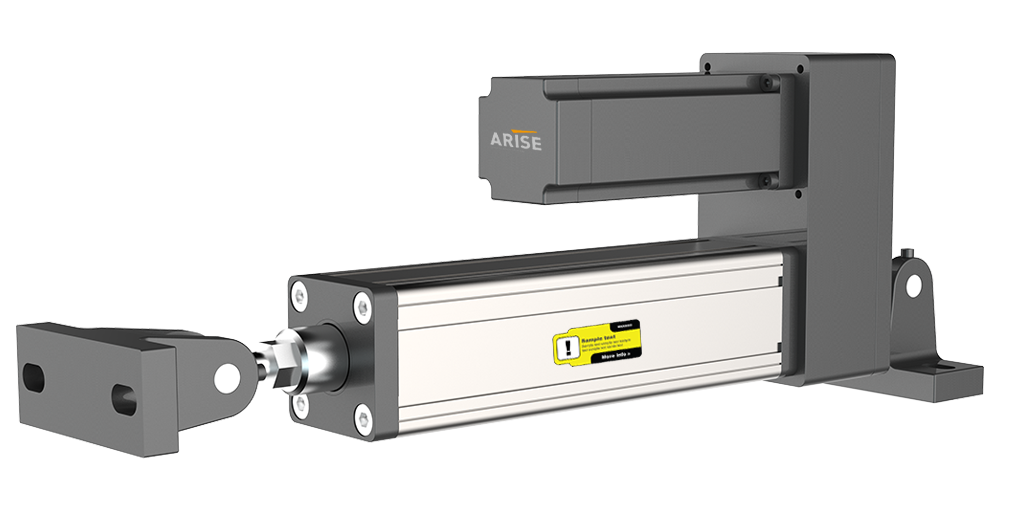
3. Guide Rollers
Web guide rollers are used to steer or guide the web through its path during processing. They work in conjunction with actuators to adjust the direction of the web based on sensor feedback. These rollers must be carefully designed to handle the speed and material type, ensuring minimal wear and optimal performance.
- Pivoting Rollers: Used to pivot the web material laterally to correct its position.
- Steering Rollers: These rollers dynamically change the web’s direction, providing a more flexible solution for correcting alignment.
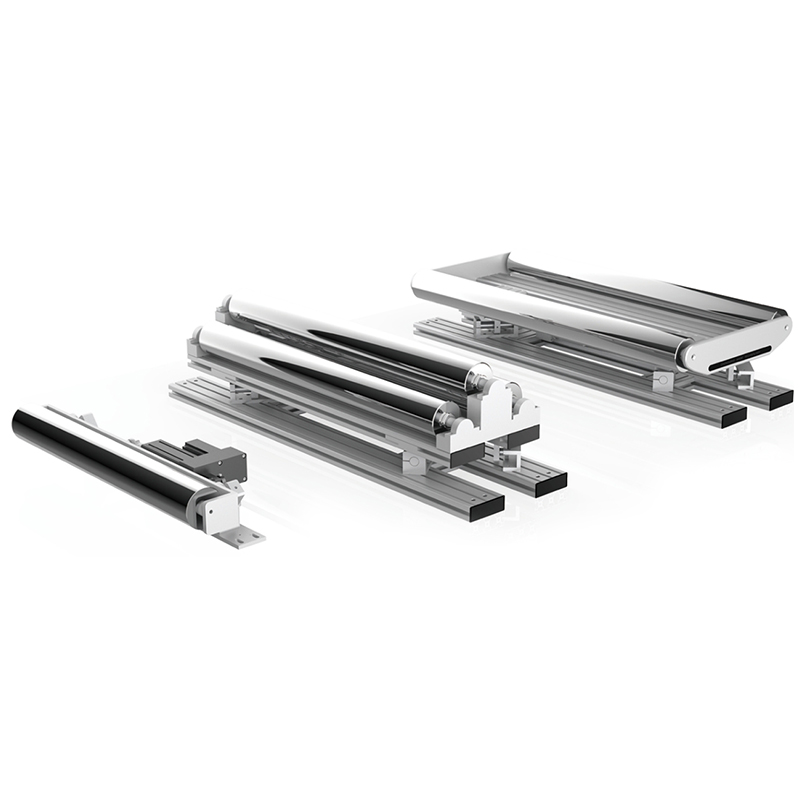
4. Control System
The control system is the “brain” of the automated web guiding setup. It processes the data from the sensors and sends commands to the actuators to adjust the web’s position. The control system can range from simple programmable logic controllers (PLCs) to more advanced systems using AI algorithms and machine learning.
- PID Controllers: These web guide controllers are commonly used for maintaining continuous control of the web by adjusting the actuators based on proportional, integral, and derivative functions.
- Smart Controllers: Modern controllers incorporate adaptive algorithms that learn from past operations, adjusting the system’s response to improve performance over time.
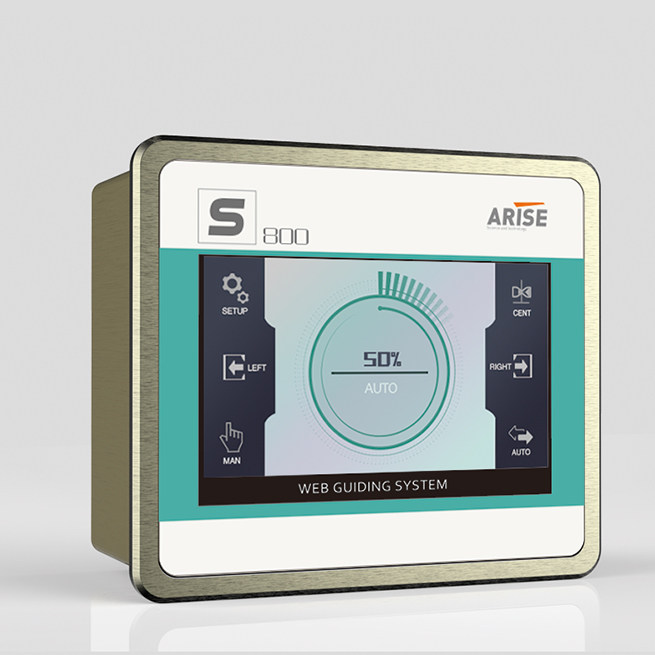
5. Feedback Loop
In a fully automated system, feedback loops play a crucial role in ensuring real-time corrections. The sensors detect any deviation from the setpoint, and this information is sent back to the control system. Based on this feedback, the control system makes precise adjustments through the actuators to correct the web position.
- Open-loop Systems: Perform corrections without feedback, based purely on pre-set conditions.
- Closed-loop Systems: Provide continuous feedback to ensure that the web stays aligned under varying operating conditions, making them more accurate.
6. Edge Detection and Web Tracking
Edge detection mechanisms are part of the sensor array, helping to identify the edge or center of the web material. Some systems may also include web tracking cameras, which provide visual feedback of the web alignment and can detect more subtle deviations in position.
- Edge Detectors: These components specifically detect the position of the web’s edge and are crucial for lateral adjustments.
- Centerline Sensors: Used in applications where the center of the web must be maintained.
7. Web Tension Control System
While not strictly part of alignment, tension control systems work closely with the web guiding system to maintain proper tension throughout the process. Uneven tension can lead to misalignment and material defects.
- Load Cells: Measure the tension in the web material and provide feedback to adjust the system accordingly.
- Dancer Rollers: Provide mechanical tension adjustments by compensating for speed changes in the system.
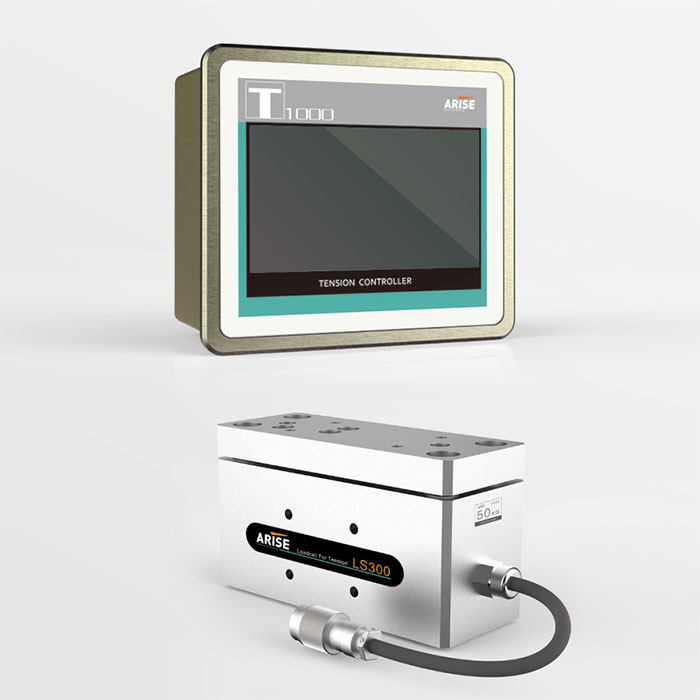
8. User Interface and Monitoring Systems
Advanced web guiding systems often come with an integrated user interface (UI) that allows operators to monitor system performance and make adjustments. This interface displays real-time data from the sensors and control system, providing insights into the web’s alignment.
- Touchscreen Panels: Enable real-time monitoring and manual adjustments of system parameters.
- Data Analytics Tools: Some systems provide analytics that help operators optimize the process by analyzing past performance and alignment deviations.
Advancements in Automated Alignment Technologies Applied in High-Speed Web Guiding
Over the years, significant advancements in automated alignment technologies for web guiding control systems have helped address the growing demands for speed, accuracy, and flexibility.
1. Machine Learning and AI-Driven Alignment Systems
The integration of artificial intelligence (AI) and machine learning (ML) algorithms in automated alignment systems has revolutionized web guiding technology. These intelligent systems analyze vast amounts of historical and real-time data to make more accurate decisions and predictive adjustments.
- Adaptive Learning: Machine learning algorithms can adapt to different materials and operating conditions, optimizing the alignment process without manual intervention. Over time, the system “learns” from past errors and continuously improves.
- Predictive Maintenance: AI-driven systems can predict alignment issues before they occur by analyzing trends and anomalies in sensor data. This leads to proactive maintenance, minimizing downtime and avoiding costly repairs.
- Real-Time Decision-Making: AI allows systems to make smarter, faster decisions in real-time, even at high speeds, ensuring that web alignment remains precise despite varying conditions such as tension changes or material variations.
2. High-Resolution and Multi-Spectrum Sensors
Improvements in sensor technology have greatly enhanced the precision and reliability of web guiding systems. Modern sensors are capable of detecting minute deviations in web alignment, even in challenging environments where traditional sensors might struggle.
- High-Resolution Edge Detection: Optical and ultrasonic sensors with higher resolution can detect even the slightest edge deviations, allowing for finer adjustments in real-time. This is crucial for applications that require tight tolerances.
- Multi-Spectrum Sensors: Advanced sensors that operate across different spectrums, such as infrared or ultraviolet, can be used for materials that are transparent, reflective, or heat-sensitive. This enables better performance across a wider range of materials and operating conditions.
- Non-Contact Measurement: Non-contact sensors, such as laser and infrared systems, provide accurate web tracking without physically interacting with the material, reducing wear and tear on the sensors and improving overall system longevity.
3. Multi-Axis Alignment Control
Traditional web guiding systems focused primarily on lateral (side-to-side) alignment. However, modern advancements have introduced multi-axis control, which allows for more comprehensive management of the web’s position across several dimensions.
- Lateral, Longitudinal, and Angular Alignment: Multi-axis control systems can adjust the web not only laterally but also along its length (longitudinal) and rotation (angular). This is particularly beneficial for complex processes where precise alignment in multiple directions is critical.
- 3D Web Alignment: For applications involving multi-layer or multi-material webs, 3D alignment technologies ensure that each layer is perfectly aligned with others, reducing the risk of defects such as wrinkles, folds, or misalignment in final products.
4. Real-Time Data Analytics and IoT Integration
The introduction of Internet of Things (IoT) technology has enabled automated web guiding systems to become more connected and intelligent. By leveraging real-time data analytics, manufacturers can gain deeper insights into the performance of their processes and make data-driven decisions.
- Cloud Connectivity: Web guiding systems can now be connected to the cloud, allowing for remote monitoring and control. This means that operators can track performance, analyze data, and make adjustments from any location, improving flexibility and reducing downtime.
- Data-Driven Optimization: Real-time analytics provide valuable data on web alignment, speed, tension, and other parameters, helping operators identify bottlenecks and inefficiencies in the system. This allows for continuous optimization of production processes.
- Predictive Analytics: By continuously collecting and analyzing data, IoT-enabled systems can predict alignment errors before they occur, enabling manufacturers to take preventive actions that avoid costly issues down the line.
5. Advanced Control Algorithms and Feedback Systems
Control systems have evolved significantly, with advanced algorithms playing a critical role in improving the precision and responsiveness of automated alignment in high-speed web guiding applications.
- PID Controllers with Enhanced Response: Proportional-Integral-Derivative (PID) controllers have become more sophisticated, offering faster response times and more precise control. These controllers can make micro-adjustments to maintain optimal web alignment under changing operating conditions.
- Fuzzy Logic and Adaptive Control: Fuzzy logic controllers can manage systems with uncertain or imprecise inputs by simulating human reasoning. This allows for more adaptive and flexible alignment in environments where conventional control systems would struggle.
- Closed-Loop Feedback Systems: Closed-loop systems with continuous feedback ensure that web alignment is constantly monitored and corrected. They adjust automatically in response to real-time changes, ensuring high accuracy at high speeds.
6. High-speed Actuation Systems
As production speeds increase, the need for faster and more responsive actuation systems has grown. Recent advancements in servo motors and linear actuators provide rapid, precise movements that help maintain web alignment even at very high speeds.
- High-Speed Servo Motors: Modern servo motors are capable of making ultra-fast adjustments, ensuring that web position corrections can keep up with the speed of production without causing material distortions or defects.
- Smart Actuators: These actuators are equipped with sensors and control capabilities that allow them to adjust in real-time, providing more accurate and dynamic corrections based on the web’s changing position.
7. Touchless and Autonomous Guiding Systems
Recent innovations have focused on contactless guiding technologies, which use advanced sensors and actuators to control web alignment without physically touching the material. These systems are particularly useful for delicate or highly sensitive materials that may be damaged by traditional guiding mechanisms.
- Laser-Guided Systems: Laser-based systems detect the web’s position and provide alignment feedback without physical contact. This ensures minimal material wear and tear and is ideal for high-speed, delicate operations.
- Autonomous Adjustment Systems: These systems can operate independently, without human intervention, adjusting themselves based on sensor data to maintain optimal alignment. Autonomous systems reduce the need for operator input and ensure consistent performance over long periods.
8. Sustainability-driven Developments
Sustainability has become an essential focus in modern manufacturing, and advancements in web guiding technologies are no exception. New systems are designed to minimize energy consumption, material waste, and environmental impact.
- Energy-Efficient Components: New actuators and motors are being developed with energy efficiency in mind, reducing power consumption without compromising performance. This results in lower operational costs and a reduced carbon footprint.
- Waste Reduction Technologies: Improved precision and real-time alignment corrections minimize material waste, which is especially important in industries such as packaging and printing where resources like paper and plastic are extensively used.
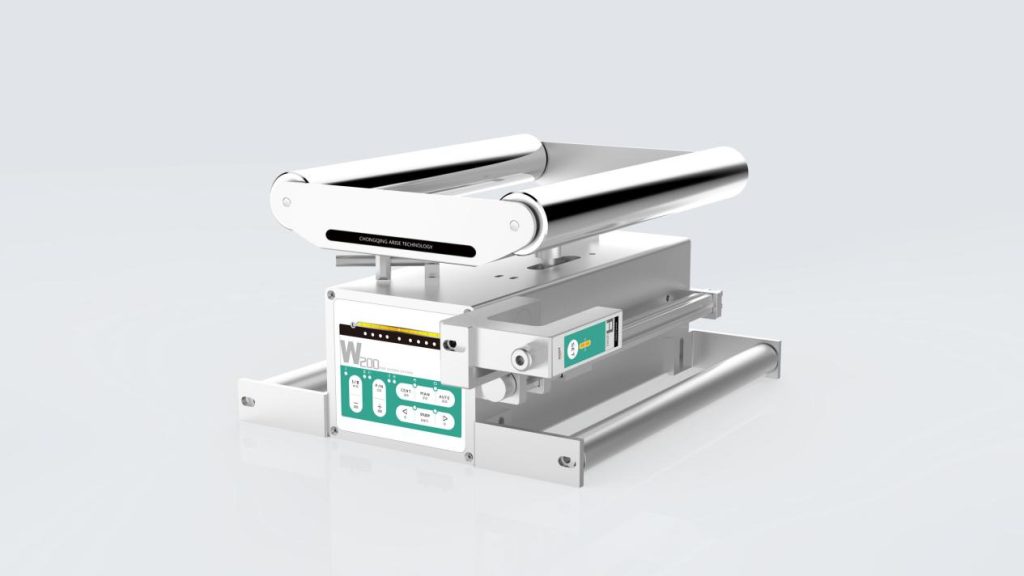
Challenges in Implementing Automated Alignment in High-speed Web Guiding Applications
This chart provides a clear overview of the challenges and how they impact web guiding applications, along with potential solutions to mitigate them.
Challenges | Description | Impact | Potential Solutions |
High-Speed Sensitivity | Achieving precise alignment at very high speeds can be difficult, as even minor deviations can lead to significant issues. | Inaccurate alignment, product defects, and material waste. | Use high-resolution sensors and fast-response actuators designed for high-speed applications. |
Material Variability | Web materials can vary in texture, thickness, transparency, and flexibility, making it challenging to implement uniform alignment solutions. | Misalignment, inconsistent product quality, and sensor misreadings. | Incorporate adaptive learning algorithms to adjust for different material properties in real-time. |
Sensor Limitations | Sensors may struggle with certain materials (e.g., transparent or reflective surfaces) or extreme environmental conditions like dust, heat, or moisture. | Poor sensor readings, reduced accuracy, and system malfunctions. | Use multi-spectrum or non-contact sensors (e.g., ultrasonic, infrared) to improve detection capabilities. |
Dynamic Tension Changes | Variations in web tension during the process can cause misalignment, especially at high speeds. | Web distortions, wrinkles, and damage to the material. | Implement advanced tension control systems integrated with the web guiding system. |
Complex Setup and Calibration | Automated systems require precise setup, calibration, and fine-tuning, which can be labor-intensive and prone to errors if not done correctly. | Initial setup delays, increased downtime, and incorrect alignment. | Use automated calibration tools and real-time system diagnostics to simplify and expedite the process. |
Real-Time Data Processing | Processing and acting on sensor data in real time is crucial in high-speed operations but can be challenging with large volumes of data. | Delayed or incorrect adjustments, leading to alignment errors. | Utilize AI-driven systems and high-speed data processors for faster and more accurate decision-making. |
Operator Skill and Training | Operators may need specialized training to manage advanced automated systems, particularly for troubleshooting and system adjustments. | Potential operator errors, downtime, and inefficiencies in handling the system. | Invest in user-friendly interfaces, training programs, and remote system support to aid operators. |
Cost of Implementation | The initial investment for high-speed automated alignment systems, including sensors, controllers, and actuators, can be high. | Increased capital expenditure, slowing adoption for small- to mid-sized businesses. | Analyze cost-benefit ratios and explore scalable systems that allow gradual upgrades over time. |
System Integration with Existing Equipment | Integrating new automated systems into existing production lines can be complex and may require significant modifications. | Downtime during installation, compatibility issues, and increased complexity in the overall system. | Plan for gradual system integration and choose systems compatible with existing setups or easily adaptable. |
Maintenance and Reliability | High-speed systems are prone to wear and tear, requiring regular maintenance to ensure reliability and consistent performance. | Increased maintenance costs, unplanned downtime, and system failure. | Implement predictive maintenance using IoT and AI to detect issues before failures occur. |
Environmental Constraints | High-speed web guiding systems can be sensitive to external factors such as temperature, humidity, and dust, affecting sensor performance and alignment. | Reduced sensor accuracy, alignment drift, and potential equipment damage. | Use robust environmental protection for sensors and actuators, and apply environmental controls as needed. |
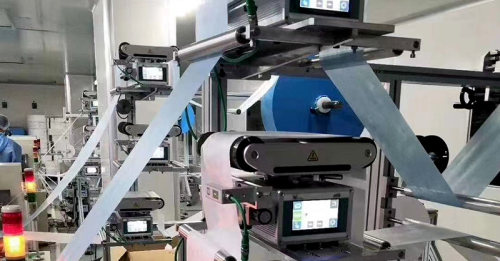
In summary, automated alignment in high-speed web guiding applications is essential for maintaining product quality and optimizing efficiency. The integration of advanced sensors, actuators, and control systems ensures real-time adjustments that keep the web aligned throughout the production process. Through the adoption of machine learning, IoT integration, smart controls, etc, will further enhance the capabilities of automated web guide systems.