The Role of Vision Systems in High-speed Printing Inspection
In the high-speed printing industry, maintaining precision and quality is crucial to meet customer expectations and regulatory standards. Vision systems have emerged as a key technology in printing inspection, ensuring real-time inspection, minimizing defects and optimizing production efficiency. These advanced systems use cameras, sensors, and software algorithms to detect printing errors and ensure consistent quality control.
Table of Contents
What are Vision Systems
Vision systems are integrated technologies that combine cameras, sensors, lighting, and software to capture, analyze, and interpret visual data. In the context of printing, these systems are designed to inspect printed materials in real-time, identifying defects, inconsistencies, or errors that may occur during the production process. They are capable of detecting issues such as misprints, color variations, smudges, missing text, and alignment errors, often at speeds that far exceed human capabilities.
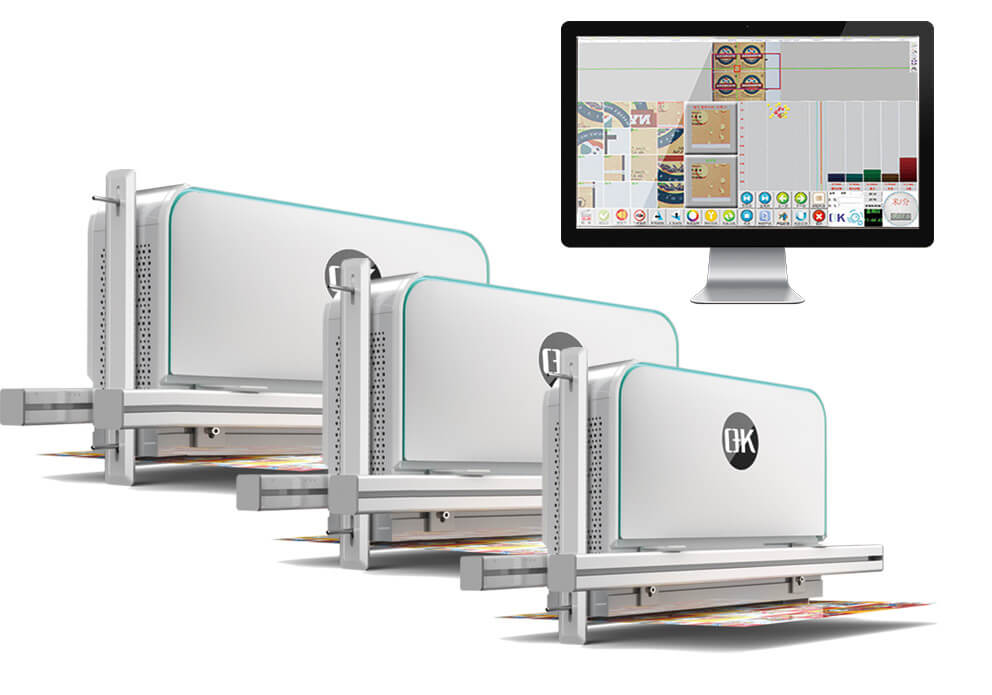
The Need for Vision Systems in High-speed Printing Inspection
As printing technologies have evolved, production speeds have increased dramatically. Modern printing presses can produce thousands of prints per minute, making manual inspection impractical and inefficient. Human inspectors are limited by fatigue, subjectivity, and the inability to keep up with the rapid pace of production. Vision systems, on the other hand, offer a reliable, consistent, and scalable solution for quality control in high-speed printing environments.
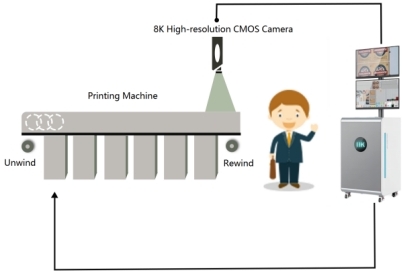
Key Functions of Vision Systems in High-speed Printing Inspection
1. Defect Detection and Classification
One of the primary functions of vision systems is identifying and classifying defects in printed materials. High-resolution cameras capture detailed images of prints, and intelligent image-processing software detects issues such as misalignment, smudging, streaks, and missing elements. By categorizing defects based on severity, the system helps operators determine corrective actions, reducing waste and improving output quality.
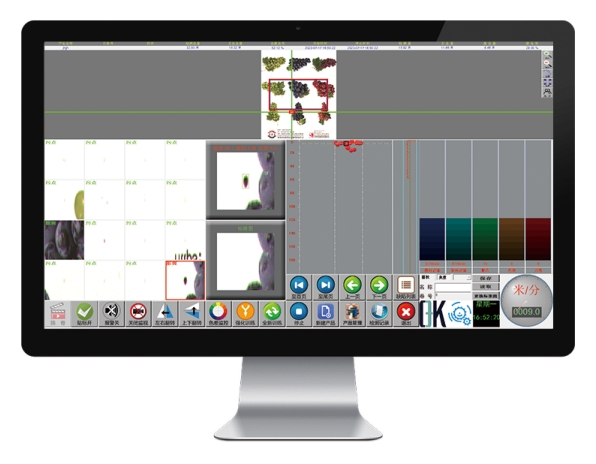
2. Real-time Quality Monitoring
Visual print inspection systems continuously monitor printing processes, ensuring that every print meets predefined quality standards. These systems compare live images of printed materials with reference templates, instantly flagging any inconsistencies. Real-time alerts enable operators to take immediate corrective action, preventing defective prints from progressing further in the production cycle.
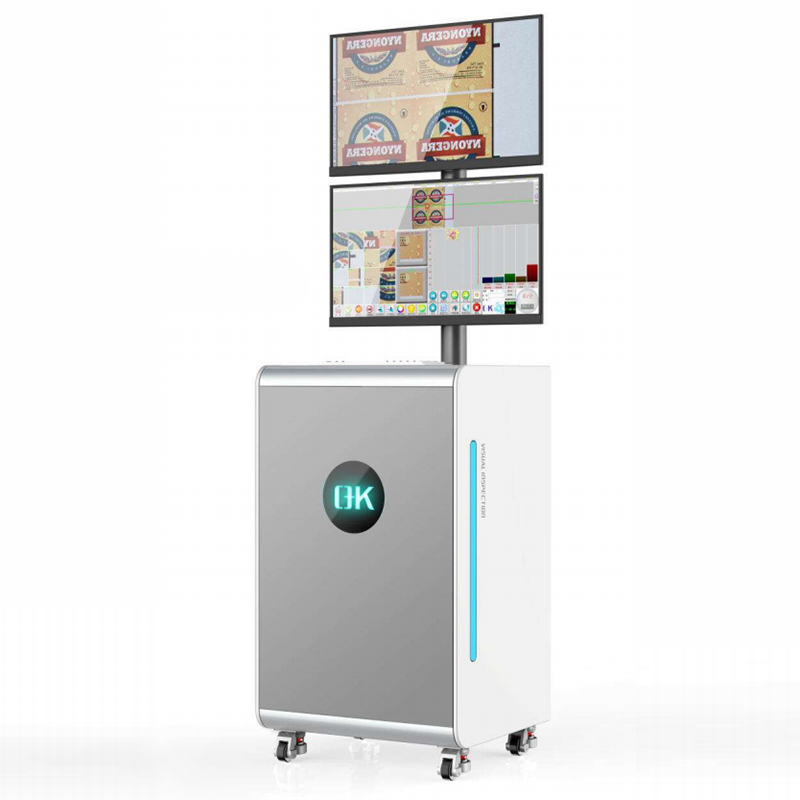
3. Registration and Alignment Verification
In high-speed printing, precise alignment of colors and design elements is crucial for producing sharp, high-quality images. Vision systems measure and adjust registration in real time, ensuring that all printed elements are correctly positioned. This prevents issues such as color misregistration and image distortion, which can impact the final product’s appearance and readability.
4. Barcode and Label Verification
In packaging and labeling applications, accurate barcode printing is essential for inventory management, tracking, and regulatory compliance. Vision systems inspect barcodes, QR codes, and serial numbers for clarity, correctness, and proper placement. Any unreadable or incorrectly printed codes are flagged to ensure they meet industry standards and can be scanned without errors.
5. Predictive Maintenance and Process Optimization
Advanced web inspection vision systems go beyond defect detection by analyzing production data to identify recurring issues. By recognizing patterns in print defects, these systems provide insights into potential machine malfunctions, ink distribution problems, or environmental factors affecting quality. Predictive maintenance features help reduce unexpected downtime, optimize ink usage, and improve overall production efficiency.
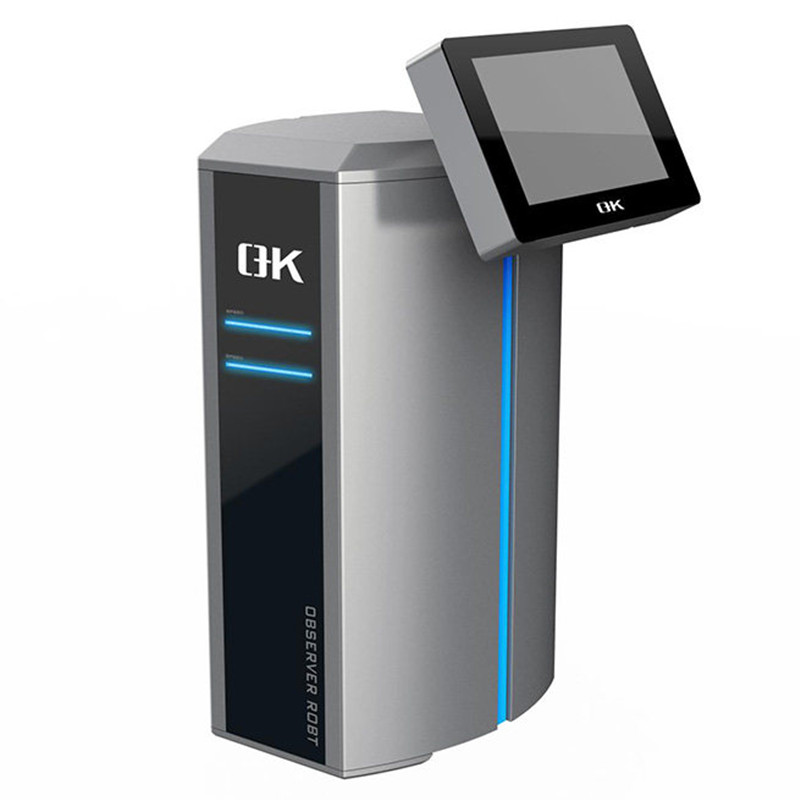
6. Cloud-Based Monitoring and Remote Diagnostics
Modern vision systems are increasingly integrated with cloud-based platforms, allowing operators to monitor quality control remotely. Real-time inspection data can be accessed from any location, enabling centralized decision-making and rapid responses to quality issues. This enhances traceability, improves operational efficiency, and supports data-driven process improvements.
Applications of Vision Systems in Different Printing Inspection Sectors
This chart highlights how vision systems enhance quality control, improve efficiency, and ensure compliance across various printing sectors.
Printing Sector | Application of Vision Systems | Key Benefits |
Packaging Printing | Inspecting barcodes, labels, and logos for accuracy | Ensures compliance, reduces misprints, prevents recalls |
Commercial Printing | Detecting color inconsistencies, smudging, and registration errors | Maintains print quality, enhances brand reputation |
Security Printing | Verifying banknotes, passports, and certificates for authenticity | Prevents counterfeiting, ensures document integrity |
Label Printing | Ensuring proper alignment and readability of product labels | Avoids labeling errors, ensures regulatory compliance |
Newspaper & Magazine | Checking print clarity, text alignment, and image sharpness | Improves readability, enhances production efficiency |
Flexible Packaging | Detecting defects in plastic films and laminated materials | Reduces material waste, ensures consistent packaging design |
Pharmaceutical Printing | Validating dosage instructions, expiry dates, and batch numbers | Meets strict regulatory standards, prevents mislabeling |
Textile Printing | Identifying misprints, pattern distortions, and color mismatches | Ensures fabric quality, maintains design consistency |
3D Printing Inspection | Monitoring layer accuracy and surface texture in additive printing | Ensures precision, reduces defects in manufacturing |
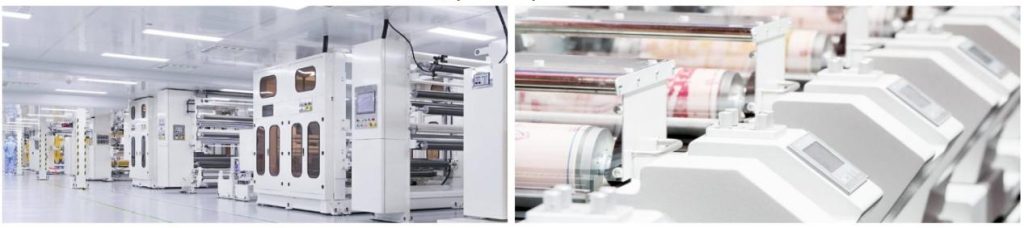
Challenges and Future Solutions of Vision Systems in Printing Inspection
1. High-Speed Performance
Challenge:
Vision systems may struggle to maintain accuracy and performance at extremely high production speeds, which are common in modern printing operations. At high speeds, it becomes difficult for the system to capture clear images, leading to missed defects and decreased inspection accuracy.
Future Solution:
The integration of AI-powered algorithms will enhance real-time processing capabilities. These algorithms will be able to make instant decisions on whether the print meets quality standards, reducing the time needed for defect detection. Additionally, future systems will incorporate faster, higher-resolution cameras and advanced image processing hardware to ensure that inspections are accurate, even at very high speeds.
2. Complex Defect Detection
Challenge:
Identifying subtle or complex defects, such as slight misregistrations, color inconsistencies, or minor ink smudges, can be difficult for vision systems. These defects are often intermittent or small in size, making them challenging to detect reliably.
Future Solution:
The use of machine learning (ML) will enable vision systems to learn from historical data and improve defect detection over time. ML models can be trained to recognize more nuanced and complex defects by learning patterns from past printing runs. Additionally, multi-spectral and multi-angle imaging will allow the 100% printing inspection systems to detect imperfections that are not visible under traditional lighting conditions, improving the detection of hard-to-find defects.
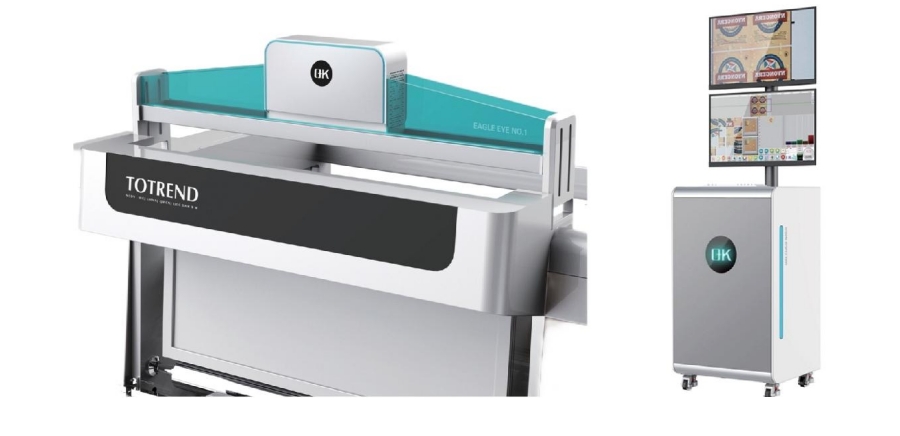
3. Cost and Implementation
Challenge:
The high upfront cost of vision systems, including cameras, sensors, lighting, and software, can be a barrier for small and medium-sized printing businesses. Additionally, the complexity of integrating these systems into legacy machinery often requires significant time and investment.
Future Solution:
Advancements in modular and scalable vision systems will make these systems more affordable and adaptable to various production environments. The increasing availability of cloud-based solutions will reduce hardware costs by enabling data processing and storage in the cloud, thus lowering the need for expensive on-premises infrastructure. Moreover, improved plug-and-play systems will streamline integration, allowing easy adaptation to existing machinery without the need for extensive modifications.
4. Lighting and Environmental Conditions
Challenge:
Lighting variations, dust, temperature fluctuations, and other environmental factors can significantly impact the accuracy of vision systems. Suboptimal lighting or environmental conditions can obscure defects, reducing the reliability of the inspection process.
Future Solution:
Future vision systems will feature adaptive lighting technologies that automatically adjust to varying environmental conditions. These systems will be equipped with advanced lighting control and multi-source illumination, ensuring consistent and accurate image capture regardless of changes in the environment. Additionally, environmentally robust vision systems designed to withstand factors like dust and temperature extremes will help maintain performance in challenging conditions.
5. Integration with Existing Systems
Challenge:
Integrating vision systems with legacy printing equipment can be a complex and time-consuming process. Older machines may not be compatible with new digital technologies, requiring significant customization and adaptation.
Future Solution:
Future vision systems will be designed for seamless integration with legacy printing equipment through Industry 4.0 standards. These systems will feature open-source software platforms and standardized communication protocols, making it easier to connect vision systems to a wide range of machinery, regardless of age or manufacturer. The rise of IoT (Internet of Things) will also facilitate the integration of vision systems with other smart devices, enabling smooth communication between machines on the production line.
6. Data Overload and Processing Speed
Challenge:
As vision systems generate large volumes of data, processing this information in real time can become a bottleneck, especially as print jobs increase in complexity. Slow data processing can lead to delays in defect detection and corrective action.
Future Solution:
Cloud computing and edge processing will significantly improve data handling. Cloud-based systems will enable faster data processing by offloading intensive computational tasks to remote servers, while edge computing will allow for faster decision-making by processing data closer to the source, reducing latency. The use of data compression algorithms and high-speed processors will also ensure that large volumes of inspection data are processed quickly without compromising accuracy.
7. Training and Skill Requirements
Challenge:
Operating and maintaining advanced vision systems requires specialized knowledge, which can be a challenge for companies without dedicated personnel or resources for training.
Future Solution:
The future of vision systems will involve simplified user interfaces and automated calibration features, making them easier for operators to use with minimal training. Additionally, AI-based diagnostics will help operators identify and address issues without needing deep technical expertise. These innovations will make vision systems more user-friendly and reduce the dependency on highly specialized staff, making it easier for businesses to maintain and operate them.
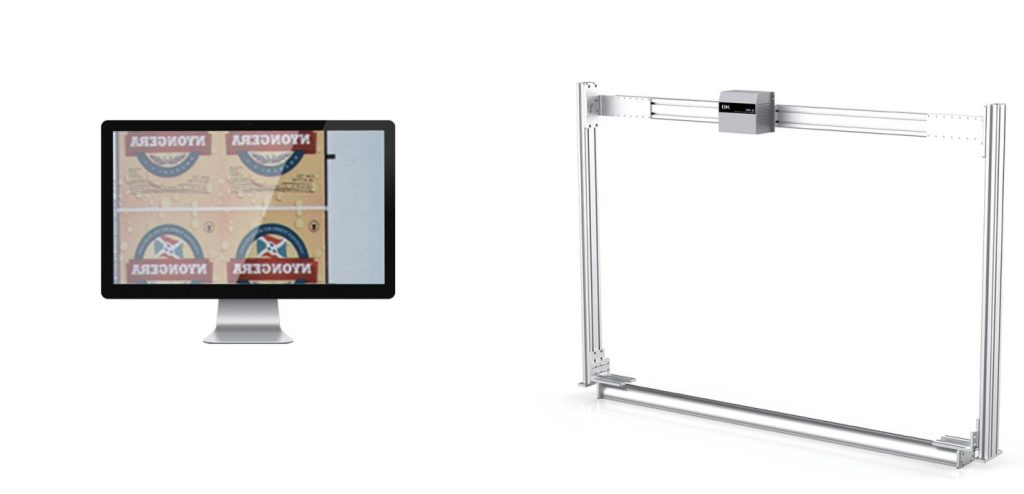
Final Thoughts
Vision systems have become an indispensable tool in high-speed printing inspection by ensuring quality, efficiency, and cost-effectiveness. As technology continues to advance, these systems will become even more intelligent, further revolutionizing the print inspection. Adopting vision-based printing inspection system can achieve higher productivity and maintain competitive in the growing demands of the market with precision and reliability.