The Role of Tension Control in Emerging Industries
In the rapidly evolving manufacturing and industrial processes, tension control systems have become critical for ensuring product quality, operational efficiency and cost optimization. As emerging industries introduce novel materials and production techniques, the demand for advanced tension control solutions has skyrocketed. This article delves into the critical role tension control plays in these industries and explores how innovations are shaping the future of these emerging industries.
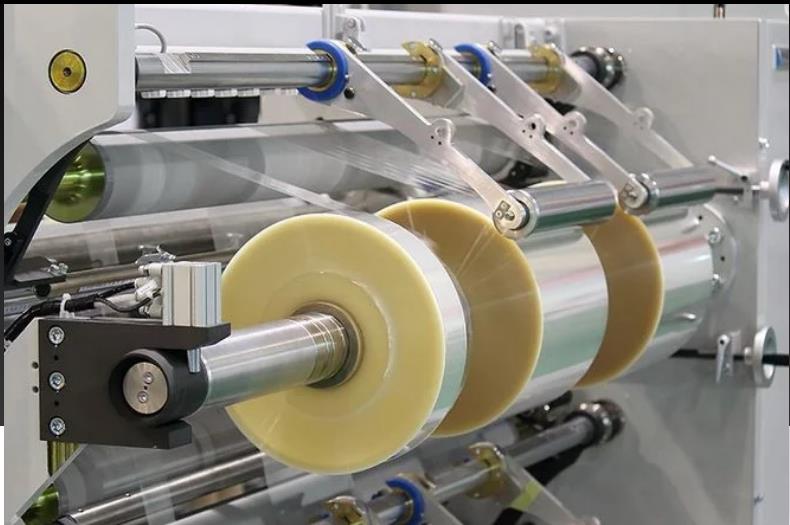
Table of Contents
What is Tension Control
Tension control refers to the process of maintaining a consistent and optimal level of tension in materials as they are processed, transported, or wound. This is particularly important in industries where materials such as films, fibers, wires, or sheets are subjected to stretching, pulling, or rolling. Proper tension control ensures that materials are handled without damage, deformation, or breakage, which is essential for maintaining product quality and minimizing waste.
In traditional manufacturing, tension control has long been a staple in industries like paper production, printing, and metal processing. However, as emerging industries push the boundaries of material science and production techniques, the demands on tension control systems have become more complex and sophisticated.
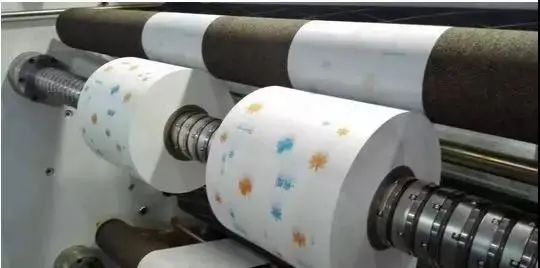
The Applications of Tension Control in Emerging Industries
1. Flexible Electronics
Devices such as foldable smartphones, wearable sensors, and flexible displays rely on ultra-thin, lightweight materials that are highly sensitive to tension variations. During manufacturing processes like deposition, etching, and lamination, even minor inconsistencies in tension can lead to defects such as wrinkles, tears, or misalignment. These defects not only compromise the functionality of the final product but also result in significant material waste. By implementing advanced tension control systems, manufacturers can ensure the precise handling of these materials, enabling the production of reliable and high-performance electronic devices.
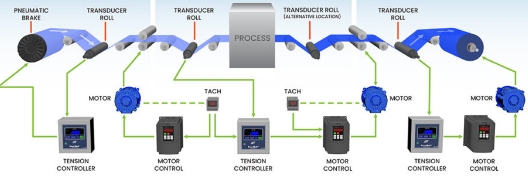
2. Renewable Energy
In the renewable energy sector, tension control is equally indispensable. The manufacturing of solar panels, wind turbine blades, and battery components requires meticulous attention to detail. For instance, in the production of photovoltaic films, maintaining uniform tension is essential to achieve consistent thickness and alignment, which directly impacts the efficiency of the solar cells. Similarly, in the fabrication of wind turbine blades, tension control is used to manage composite materials that must be precisely wound and layered to meet stringent strength and durability requirements. Without effective tension control, the performance and longevity of these renewable energy solutions could be severely compromised.
3. Advanced Textiles and Composites
The development of smart textiles, which integrate conductive fibers and sensors, demands precise handling to maintain both structural integrity and functionality. In the production of carbon fiber composites, even slight deviations in tension can lead to weak spots or defects, undermining the material’s performance in high-stress applications such as aerospace or automotive manufacturing. Tension control systems enable manufacturers to navigate these challenges, ensuring that advanced materials meet the rigorous standards required for cutting-edge applications.
4. Additive Manufacturing (3D Printing)
While 3D printing is often associated with layer-by-layer deposition, processes that involve filament feeding or wire-based printing rely heavily on consistent tension to ensure smooth material flow. This is particularly important in industries like aerospace and healthcare, where precision and reliability are non-negotiable. By integrating advanced tension control mechanisms, manufacturers can achieve higher resolution prints, reduce errors, and unlock new possibilities in additive manufacturing.
5. Electric Vehicles (EVs) and Battery Manufacturing
The manufacturing of EV batteries, for example, involves coating thin metal foils with active materials to create electrodes. Maintaining precise tension during this process is essential to ensure uniform coating thickness and prevent defects that could compromise battery performance and safety. As the demand for EVs continues to grow, the role of tension control in enabling efficient and reliable battery production will only become more pronounced.
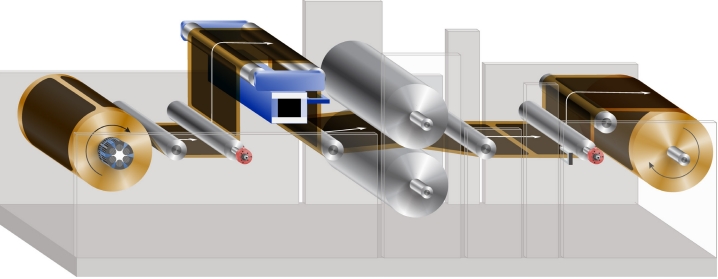
Challenges in Tension Control for Emerging Industries
Challenge | Description | Impact |
Material Diversity | Emerging industries use advanced materials like ultra-thin films, composites, and biopolymers. | Requires customized solutions due to varying mechanical properties, increasing system complexity. |
High-Speed Production | Modern processes demand faster production rates. | Higher speeds can lead to tension fluctuations, impacting precision and product quality. |
Digital Integration | Need to integrate tension systems with IoT, AI, and smart factory technologies. | Incompatibility can limit automation, reducing operational efficiency and innovation potential. |
Environmental Sensitivity | Many advanced materials are affected by changes in temperature, humidity, and other conditions. | Dynamic environmental factors can compromise tension stability, leading to defects or material loss. |
Cost and Scalability | Implementing advanced tension control systems can be expensive. | May deter adoption in smaller operations or industries with tight budgets, limiting growth. |
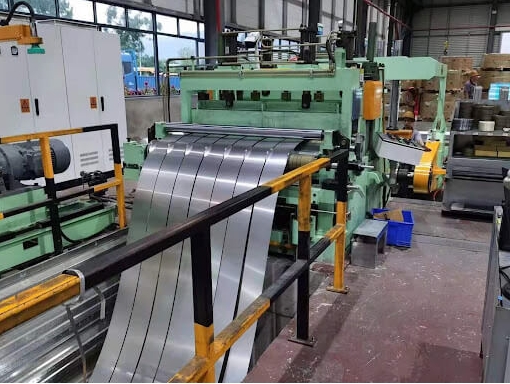
Innovative Tension Control Technology to Address the Challenges in Emerging Industries
1. Real-Time Monitoring and Feedback
These systems integrate advanced tension sensors that constantly measure tension in materials during production. The data collected is processed in real-time, enabling immediate adjustments to maintain consistent tension. This approach minimizes defects caused by fluctuations and ensures optimal performance even in high-speed production lines.
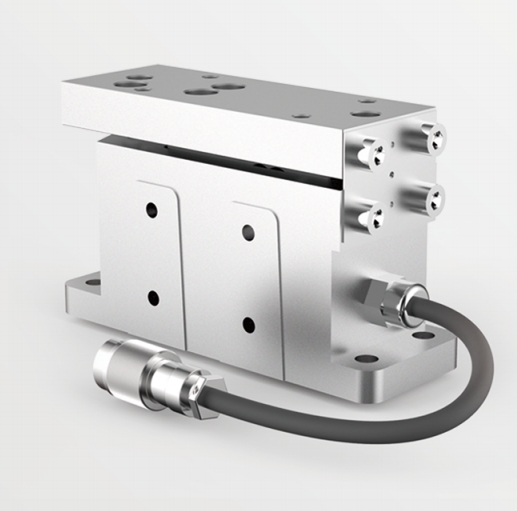
2. Artificial intelligence (AI)
AI-powered systems analyze patterns in tension variations and predict potential issues before they arise. By implementing predictive analytics, manufacturers can proactively adjust settings, reducing downtime and preventing costly material waste. These intelligent systems adapt to the properties of diverse materials, making them particularly effective in industries working with advanced composites, flexible substrates, or biopolymers.
3. Modular Design
Modular tension control systems are designed to accommodate a wide range of materials and production processes. Manufacturers can easily reconfigure or upgrade the system to meet the specific demands of their industry, eliminating the need for extensive overhauls. This flexibility makes modular designs especially appealing in rapidly evolving sectors like flexible electronics and renewable energy.
4. Energy-efficient Drives
Another significant development is the integration of energy-efficient drives in tension control technology. These drives not only regulate tension with precision but also incorporate regenerative braking mechanisms to reduce energy consumption. This innovation aligns with the sustainability goals of many emerging industries, ensuring that production processes are both efficient and environmentally responsible.
5. Digitalization
Digitalization has further enhanced tension control by connecting systems to smart factory networks. By integrating with IoT platforms, tension control systems can share data across the production line, providing a holistic view of operations. This interconnected approach improves coordination and allows for more precise adjustments, particularly when dealing with sensitive materials or intricate processes like embedding sensors into smart textiles.
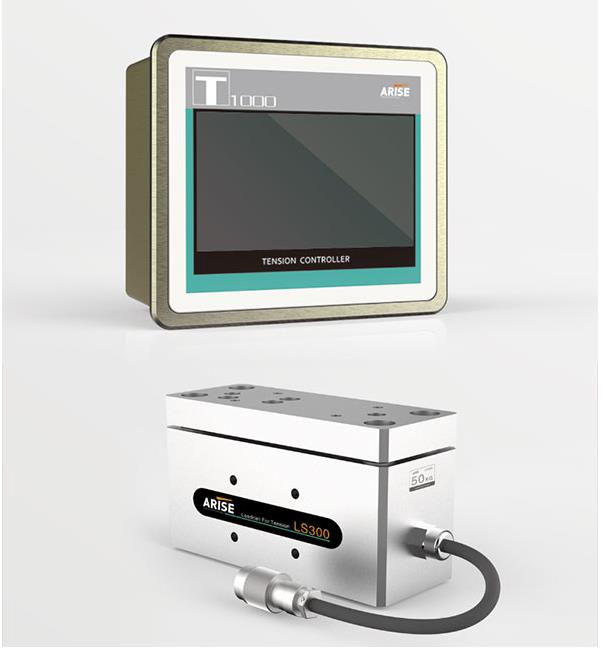
Overall, through addressing the unique challenges of tension control posed by new materials and processes in emerging industries, the advanced tension control systems will play a pivotal role in shaping the future of manufacturing. Adopting cutting-edge tension control technologies is not just a necessity but a strategic move toward staying competitive in a dynamic manufacturing industries.