The Revolutionary Role of 100% Inspection Systems in Printing Quality Control
Table of Contents
In the printing industry, where accuracy and consistency are important, ensuring the quality of printed materials is a critical aspect. Traditional sample-based quality inspections, while effective in some cases, are often inadequate for high-speed, large-scale printing operations. This is why 100% inspection systems are used in printing industry. This article mainly explores the role of 100% inspection systems in the printing industry, including their technological advantages, and their importance in maintaining flawless print quality.
What are 100% Inspection Systems in Printing
100% inspection systems in printing are automated solutions that examine every sheet or roll of printed material as it comes off the production line. The printing quality inspection system adopts advanced technologies like machine vision, color analysis, and pattern recognition to detect even the smallest defects. By continuously monitoring print quality, they ensure that any deviation from the desired specifications is caught immediately, allowing operators to correct the issue before large quantities of defective products are produced.
Unlike random sampling, where only a fraction of the prints are checked, 100% inspection systems leave no room for errors, making them ideal for high-volume, high-speed printing environments such as packaging, labels, newspapers, and commercial printing.
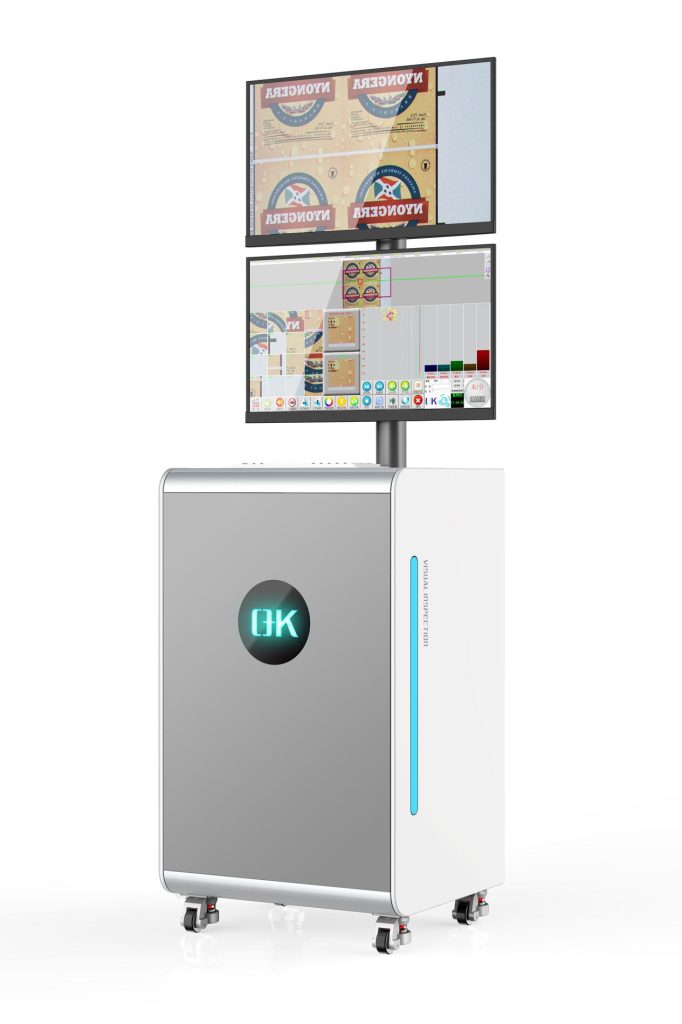
Key Features of 100% Inspection Systems in Printing
- High-Resolution Cameras: Equipped with high-resolution cameras, these systems capture detailed images of the printed material at ultra-fast speeds. This allows the detection of minute defects such as smudges, misalignment, missing text, or color deviations, even when the printing process is moving rapidly.
- Real-Time Image Processing: The captured images are processed in real time using powerful algorithms that compare each print to a reference image or pre-set standard. This rapid processing ensures that defects are detected immediately, allowing for quick corrections to minimize waste.
- Color Management: One of the most critical aspects of print quality is color accuracy. 100% inspection systems use color analysis tools to monitor consistency, ensuring that each print meets the specified color standards. These systems detect subtle changes in hue, saturation, and brightness that might otherwise go unnoticed in manual inspection.
- Pattern and Text Recognition: In addition to checking for physical defects, the system can also inspect printed text for legibility and completeness. It can recognize missing characters, incorrect fonts, or even incorrect layouts, which is especially useful in printing applications such as packaging or marketing materials, where accurate text and branding are vital.
- Defect Classification: The inspection systems can classify defects based on their severity, whether they are minor issues that can be tolerated or major defects that require the print run to stop for correction. This helps operators make informed decisions on how to handle detected issues.
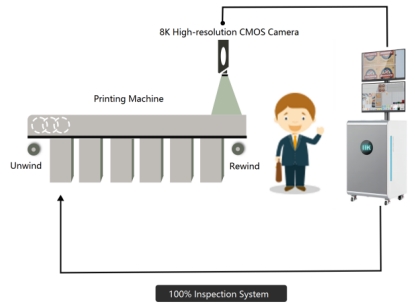
Common Printing Defects Detected by 100% Inspection Systems
This chart highlights the most common defects detected by inspection systems to ensure consistent, high-quality printing.
Defect Type | Description | Impact on Print Quality |
Color Variation | Inconsistent color across the print run, leading to visible differences in tone. | Reduces aesthetic appeal and may fail color standards. |
Registration Errors | Misalignment between different colors or layers. | Causes blurry or offset visuals, reducing clarity. |
Smudging or Streaking | Ink smears or streaks on the printed material. | Results in an untidy appearance, especially on text. |
Text and Graphic Errors | Missing, incomplete, or incorrectly placed text or images. | Affects legibility and branding accuracy. |
Ink Spillage | Excess ink spread beyond intended print areas. | Leads to a messy and unprofessional appearance. |
Poor Print Resolution | Low-quality printing with visible pixelation or jagged edges. | Reduces sharpness and overall print quality. |
Scratches or Marks | Unintended lines or marks on the surface of the printed material. | Creates a damaged or inconsistent appearance. |
Die-Cutting Errors | Incorrect cutting of materials, leading to size or shape discrepancies. | Results in non-standard product sizes or shapes. |
Folding Misalignment | Improper folding or creasing of materials in packaging or brochures. | Leads to faulty folding lines and misaligned layouts. |
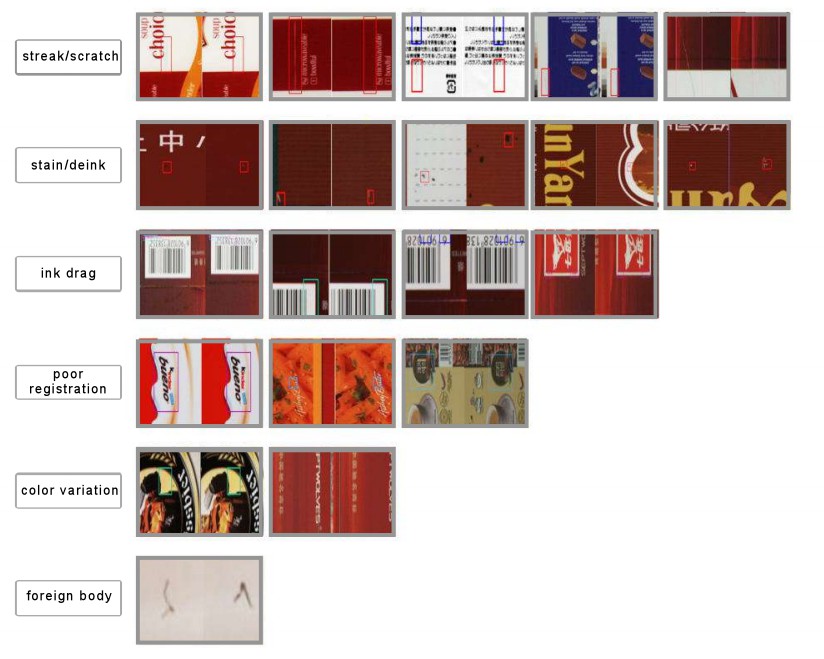
Advantages of Implementing 100% Inspection Systems in Printing
This chart highlights the key advantages of implementing 100% inspection systems, making them crucial for ensuring print quality in modern printing operations.
Advantage | Description | Impact |
Elimination of Defective Prints | Ensures every print is inspected, preventing defective prints from reaching customers. | Reduces waste and customer complaints, enhancing satisfaction. |
Increased Production Efficiency | Real-time feedback allows for immediate correction of issues during production. | Minimizes downtime and material wastage. |
Improved Customer Satisfaction | Delivers consistently high-quality products, meeting or exceeding customer expectations. | Enhances reputation and customer loyalty. |
Cost Reduction | Reduces costs associated with reprints, material waste, and product recalls. | Long-term savings despite initial system investment. |
Enhanced Data Collection | Collects comprehensive data on print quality for analysis and process improvement. | Enables continuous quality improvement and trend analysis. |
Reduction of Human Error | Automated systems eliminate errors that can occur in manual inspections. | Increases accuracy and consistency in quality control. |
Compatibility with High-Speed Production | Designed to inspect at high speed printing without slowing down production lines. | Supports large-scale, high-speed printing operations. |
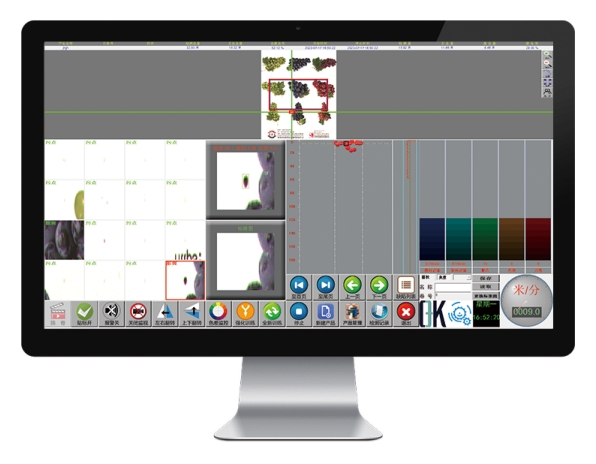
Challenges of Implementing 100% Inspection Systems in Printing
- High Initial Investment: The cost of purchasing and installing advanced inspection systems can be significant, especially for small and mid-sized printing companies. However, the long-term savings through quality improvement and waste reduction can justify the investment.
- Integration with Existing Systems: Seamless integration of inspection systems with existing printing equipment and workflows can be challenging. It may require customization or modification of current systems to ensure compatibility.
- Processing Speed: For very high-speed printing operations, the inspection system must be capable of processing images and detecting defects without slowing down production. While modern systems are designed for fast processing, choosing the right solution for high-speed environments is essential.
- System Calibration and Maintenance: As with any precision system, regular calibration and maintenance are necessary to ensure accurate defect detection. Downtime for maintenance may be necessary, but it is critical for long-term performance.
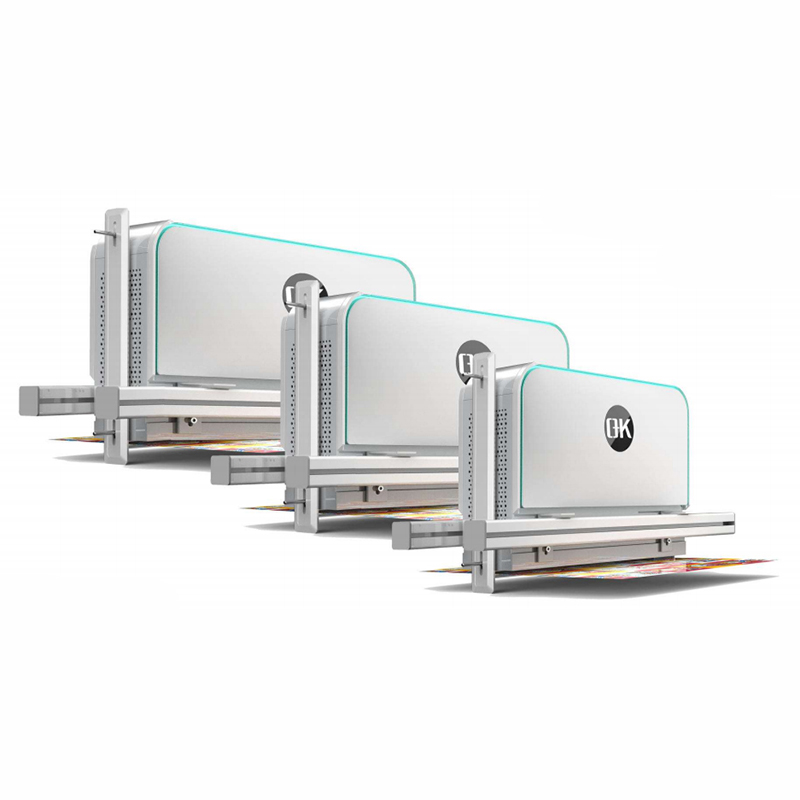
Applications of 100% Inspection Systems in the Printing Industry
100% inspection systems are used across a wide range of printing applications.
- Packaging Printing: Ensuring that labels and packaging materials are printed with accurate colors, text, and images, and that barcodes and QR codes are readable.
- Commercial Printing: Guaranteeing high-quality prints for marketing materials, brochures, and catalogs, where brand image and design consistency are crucial.
- Security Printing: Inspecting security documents such as banknotes, ID cards, or checks to ensure that anti-counterfeiting features are properly implemented and free of defects.
- Newspaper and Magazine Printing: Verifying that high-speed print runs maintain quality from the first page to the last, without misalignment, smudging, or color shifts.
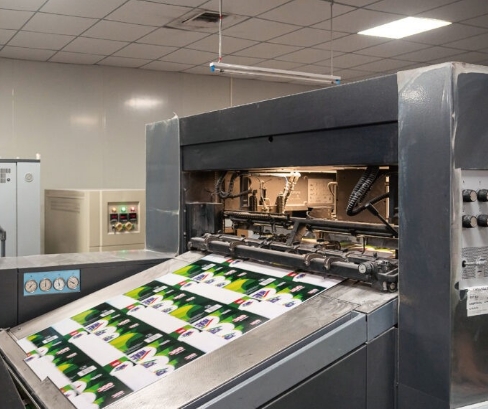
In summary, 100% inspection systems provide a robust solution for detecting defects in real time, ensuring that every product meets the exact specifications required in printing industry. From packaging to security printing, these systems are revolutionizing how businesses approach quality control, offering advantages such as cost savings, customer satisfaction, production efficiency, etc.