The Pivotal Role of Automated Printing Quality Inspection Systems in Print Production
Whether producing packaging materials, labels, newspapers, or textiles, keeping consistent print quality is critical to satisfying customer expectations and regulatory standards. To accomplish this, the use of Automated Printing Quality Inspection Systems has emerged as a game changer, altering how print quality is checked and guaranteed. In this article, we delve into the key components, benefits, applications of Automated Printing Quality Inspection System and the latest advancements shaping the printing industry, highlighting on their pivotal role in the modern printing industry.
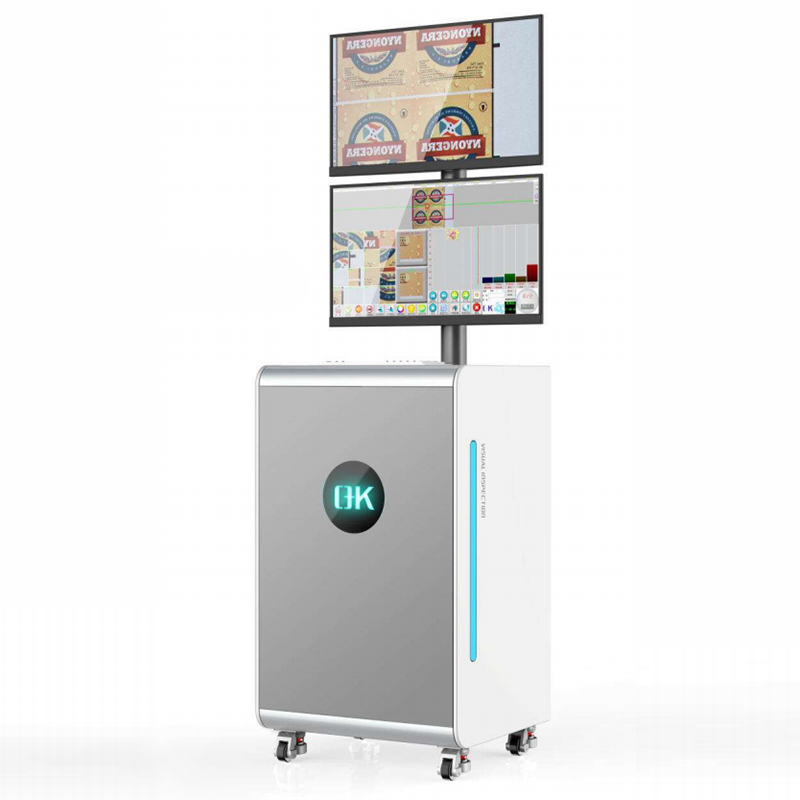
The Evolution of Automated Printing Quality Inspection Systems
Traditionally, print quality inspection relied heavily on manual inspection techniques, which were time-consuming, labor-intensive, and prone to human mistake. However, as technology advanced, automated systems became more complex, allowing for real-time monitoring, analysis, and repair of print problems.
How Automated Printing Quality Inspection Systems Work
Automated Printing Quality Inspection Systems use sensors, cameras, and software algorithms to examine many features of printed materials. These systems can detect defects such as misprints, color variations, streaks, smudges, registration errors, and missing or misplaced elements with remarkable accuracy.
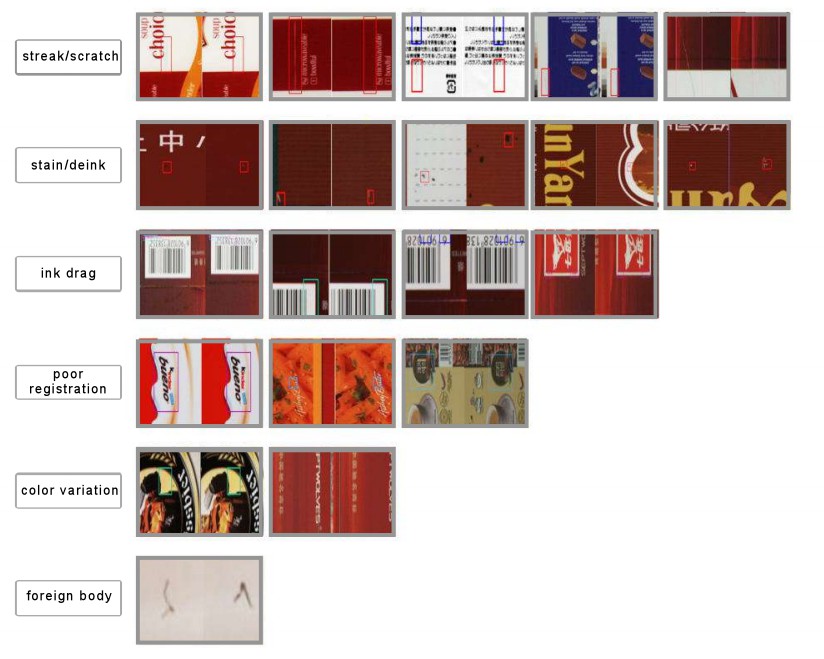
Key Components
This chart outlines the key components involved in automated printing quality inspection systems, from image acquisition to integration with manufacturing processes.
Component | Explanation |
1. Image Acquisition | Utilizes high-resolution cameras or scanners to capture images of printed materials. Images are captured from multiple angles to ensure comprehensive inspection. |
2. Image Processing | Applies algorithms to analyze images and detect defects such as misprints, smudges, or color variations. Advanced image processing techniques enhance accuracy and reliability in defect detection. |
3. Decision Making | Compares detected defects with predefined quality standards and tolerances. Determines whether printed materials meet quality criteria and are acceptable for further processing or require rework. |
4. Defect Classification | Classifies detected defects based on severity and type (e.g., minor misalignment, major color inconsistency). Allows for prioritization of defects and appropriate corrective actions. |
5. Automated Feedback Loop | Provides feedback to printing systems for real-time adjustments and corrections. Enables continuous improvement and optimization of printing processes. |
6. Integration with Manufacturing | Seamlessly integrates with printing equipment and production lines. Facilitates automated quality control within the manufacturing workflow. |
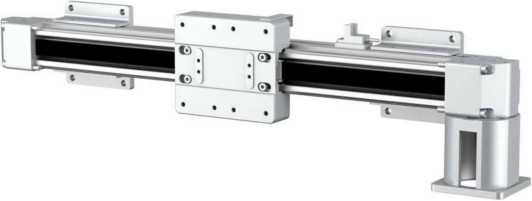
Benefits of Automated Printing Quality Inspection Systems
Aspect | Explanation |
1. Improved Quality Control | Ensures consistency and accuracy in printed materials, reducing the risk of defects and errors. |
2. Cost Savings | Reduces waste and rework by detecting defects early in the production process, leading to cost savings. |
3. Increased Efficiency | Streamlines inspection processes, resulting in faster production cycles and improved overall efficiency. |
4. Real-Time Feedback | Provides immediate feedback to printing systems, allowing for quick adjustments and corrections. |
5. Enhanced Customer Satisfaction | Ensures that printed materials meet quality standards, enhancing customer satisfaction and loyalty. |
Applications of Automated Printing Quality Inspection Systems
Application | Explanation |
Packaging | Verifies the quality and accuracy of packaging materials, ensuring they meet branding and regulatory requirements. Inspection may include checking for print clarity, color consistency, and label placement. |
Publishing | Validates the print quality and accuracy in books, magazines, newspapers, and other printed publications. Inspection may include checking for ink coverage, text alignment, and image clarity. |
Labeling | Ensures the accuracy of labels, including barcodes, product information, and regulatory compliance. Inspection may include checking for barcode readability, text accuracy, and label adherence. |
Textiles | Inspects printed designs on textiles, ensuring they meet design specifications and quality standards. Inspection may include checking for print consistency, color accuracy, and pattern alignment. |
Industrial Printing | Verifies the quality of printed materials used in industrial applications, such as circuit boards, electronic components, and automotive parts. Inspection may include checking for print accuracy, component alignment, and surface finish. |

Advancements and Trends in Automated Printing Quality Inspection Systems
1. Integration of Artificial Intelligence (AI) and Machine Learning (ML)
The combination of AI and ML algorithms is transforming automated printing quality inspection systems. These clever algorithms can sift through massive volumes of data, discover trends, and adjust to changing printing conditions. AI-powered systems can now detect minor flaws, anticipate prospective problems, and optimize inspection procedures for greater accuracy and efficiency.
2. Real-Time Defect Classification and Correction
Modern automated inspection systems provide real-time flaw classification, allowing for prompt corrective action. By categorizing faults based on severity and kind, these systems may automatically alter printing settings such as ink levels, registration, and pressure to resolve difficulties as they arise. This proactive strategy reduces waste while ensuring uniform print quality across production runs.
3. Multi-Modal Inspection Capabilities
To address the diverse needs of various printing applications, automated inspection systems are incorporating multi-modal inspection capabilities. This allows them to inspect printed materials using a combination of imaging technologies, such as visible light, ultraviolet (UV), infrared (IR), and hyperspectral imaging. Multi-modal inspection provides comprehensive defect detection across different materials, substrates, and printing processes.
4. Enhanced Color Management and Calibration
Color accuracy is critical in printing, especially for industries like packaging, labels, and branding, where brand consistency is paramount. Automated inspection systems now offer advanced color management and calibration features, ensuring precise color reproduction across different substrates and printing conditions. These systems can detect color variations, match predefined color standards, and adjust color profiles in real-time to maintain consistency.
5. Cloud-Based Solutions for Remote Monitoring and Analytics
Cloud-based automated inspection system enables remote monitoring, data storage, and analytics, offering greater flexibility and scalability. Printers can access inspection results in real-time from anywhere, collaborate with remote teams, and leverage cloud-based analytics tools to gain insights into production performance, defect trends, and quality metrics. This facilitates data-driven decision-making and continuous improvement initiatives.
6. Integration with Industry 4.0 Technologies
Automated printing quality inspection systems are becoming more connected with other Industry 4.0 technologies, including the Internet of Things (IoT), robotics, and data analytics. This integration provides interconnected smart factories in which inspection data is seamlessly exchanged with other production systems, allowing for predictive maintenance, production optimization, and adaptive manufacturing strategies.
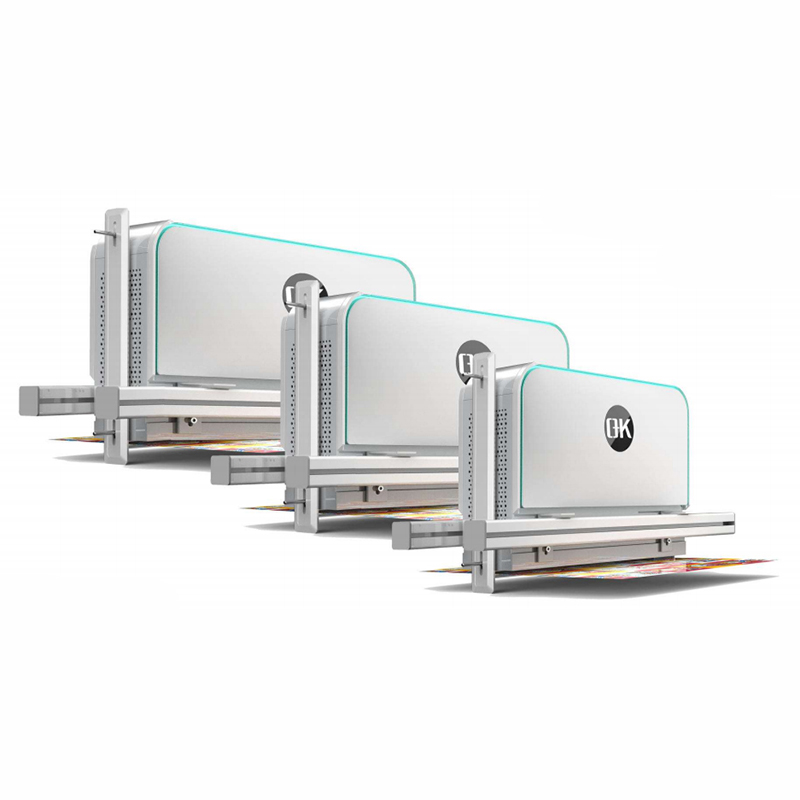
Conclusion
Automated Printing Quality Inspection Systems are a key innovation in the printing industry, providing unprecedented precision, efficiency, and control. As technology advances, these systems will play a critical role in creating the future of print production by fostering innovation and guaranteeing consistent quality across a wide range of printing applications. Embracing automated inspection technology is more than simply a competitive advantage; it is a must for printers seeking to succeed in an increasingly demanding business context.