The Crucial Role of Tension Amplifiers in High-temperature and Harsh Environments
In various industrial sectors, accurate tension measurement is crucial for maintaining operational efficiency and safety. High-temperature and harsh environments present unique challenges that standard tension measurement devices cannot withstand. Tension amplifiers, specifically designed for such conditions, offer robust solutions to ensure precise and reliable tension measurement even under extreme stress.
Understanding Tension Amplifiers
Tension amplifiers serve to enhance the electrical signals generated by tension sensors or load cells. These sensors detect the force exerted on materials or components and convert this mechanical tension into an electrical signal. The amplifier’s job is to magnify this signal for accurate measurement and interpretation by control systems. This process must remain stable and accurate despite external stresses, which is particularly challenging in high-temperature and harsh environments.
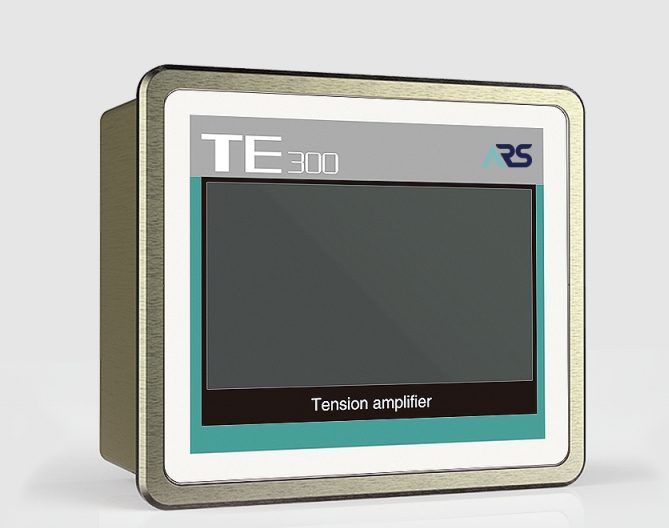
Challenges and Strategies of Tension Amplifiers Used in High-temperature and Harsh Environments
1. Thermal Stress
Impact on Materials and Components: High temperatures can cause thermal expansion and contraction, affecting both the physical structure and the electronic components of tension amplifiers. This can lead to:
- Signal Drift: Changes in temperature can cause fluctuations in the electronic signals, leading to inaccurate tension measurements.
- Material Fatigue: Repeated thermal cycling can weaken materials, potentially causing mechanical failure over time.
Mitigation Strategies
- Use of heat-resistant materials such as ceramics and specialized alloys.
- Incorporation of thermal management systems like heat sinks and cooling fans.
2. Corrosion and Contamination
Exposure to Harsh Substances: Industrial environments often expose tension amplifiers to chemicals, moisture, and dust, which can lead to:
- Corrosion: Chemical reactions with moisture and pollutants can degrade metals and electronic components.
- Contamination: Dust and debris can infiltrate sensitive parts, leading to malfunction or inaccurate readings.
Mitigation Strategies
- Application of anti-corrosive coatings and sealants.
- Design of sealed housings to protect internal components from contaminants.
3. Mechanical Stress
Vibrations and Shocks: High-temperature environments are often accompanied by mechanical stressors such as vibrations and shocks, which can:
- Disrupt Signal Integrity: Mechanical movements can cause noise and errors in signal processing.
- Damage Components: Prolonged exposure to vibrations and shocks can physically damage the amplifier and its components.
Mitigation Strategies
- Use of vibration-dampening materials and reinforced housings.
- Design improvements to absorb and distribute mechanical stresses.
4. Electromagnetic Interference (EMI)
High Electromagnetic Fields: Industrial environments can have strong electromagnetic fields that interfere with electronic devices, causing:
- Noise in Signals: EMI can introduce noise, leading to distorted or inaccurate readings.
- Component Failure: Prolonged exposure to EMI can degrade or damage electronic components.
Mitigation Strategies
- Incorporation of EMI shielding in the design.
- Advanced filtering techniques to separate the signal from noise.
5. Calibration and Maintenance
Difficulties in Calibration: Maintaining accuracy in high-temperature and harsh environments can be challenging due to:
- Accessibility Issues: Environments such as deep-sea locations or high-altitude areas can be difficult to access for regular maintenance and calibration.
- Dynamic Conditions: Constant changes in temperature and mechanical load can necessitate frequent recalibration to ensure accuracy.
Mitigation Strategies
- Design of self-calibrating systems that adjust automatically to changing conditions.
- Development of remote monitoring and calibration technologies.
6. Longevity and Reliability
Durability Concerns: The extreme conditions can significantly shorten the lifespan of tension amplifiers, leading to:
- Frequent Replacements: Reduced reliability can necessitate more frequent replacements, increasing operational costs.
- Downtime: Failure of tension amplifiers can lead to unplanned downtime, affecting overall productivity.
Mitigation Strategies
- Use of durable, high-quality materials designed to withstand extreme conditions.
- Implementation of predictive maintenance techniques to anticipate and prevent failures.
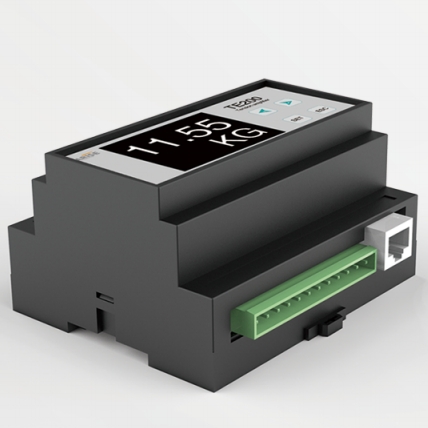
Applications of Tension Amplifiers in High-temperature and Harsh Environments
1. Aerospace
Structural Health Monitoring: In aerospace, tension amplifiers are used to monitor the structural integrity of aircraft and spacecraft components. These environments often involve:
- High Temperatures: Components, especially those near engines and exhaust systems, experience extreme heat.
- Vibrations and Mechanical Stress: Continuous vibrations and mechanical loads during flight.
Applications
- Wing and Fuselage Monitoring: Ensuring the structural integrity of critical components to prevent failures.
- Engine Components: Monitoring tension in engine parts subjected to high temperatures and mechanical stress.
2. Automotive Industry
Engine and Exhaust Systems: Tension amplifiers are vital in the automotive industry, particularly for monitoring components within engines and exhaust systems where conditions can be extreme.
- High Heat: Engines and exhaust systems operate at high temperatures.
- Vibrations: Continuous mechanical stress due to engine vibrations.
Applications
- Tension Measurement in Belts and Chains: Ensuring proper tension in timing belts and drive chains to prevent engine malfunctions.
- Exhaust System Monitoring: Maintaining structural integrity and performance of exhaust components.
3. Manufacturing
High-Temperature Processing: In manufacturing processes such as metal forming, extrusion, and molding, tension amplifiers are crucial for precise control and measurement.
- Thermal Conditions: Processes often involve high temperatures.
- Mechanical Forces: High mechanical loads and vibrations during manufacturing operations.
Applications
- Metal Forming: Monitoring and controlling tension in metal sheets to ensure quality and uniformity.
- Plastic Extrusion: Ensuring consistent tension in extruded plastic products.
4. Energy Sector
Power Generation and Oil & Gas: Tension amplifiers are extensively used in power plants and the oil and gas industry where equipment is exposed to extreme conditions.
- High Temperatures: Environments such as turbines, reactors, and drilling sites experience high thermal stress.
- Harsh Mechanical Conditions: Mechanical loads, vibrations, and potential corrosive substances.
Applications
- Turbine Monitoring: Measuring tension in turbine blades to prevent failures and optimize performance.
- Oil Rig Monitoring: Ensuring the integrity of drilling equipment and pipelines under harsh conditions.
5. Mining and Heavy Equipment
Robust Machinery Operation: Tension amplifiers help in monitoring and maintaining heavy machinery used in mining and construction.
- Harsh Environmental Conditions: Exposure to dust, moisture, and mechanical stress.
- High Mechanical Loads: Heavy equipment operation involves significant mechanical forces.
Applications
- Conveyor Belt Monitoring: Ensuring proper tension in conveyor belts to avoid disruptions and downtime.
- Heavy Machinery Components: Monitoring tension in critical components to prevent failures and extend equipment life.
6. Marine and Offshore
Subsea and Marine Operations: In marine and offshore environments, tension amplifiers are essential for monitoring the integrity of subsea equipment and structures.
- High Pressure and Corrosion: Subsea environments involve high pressures and exposure to corrosive seawater.
- Mechanical Stress: Continuous mechanical loads from waves and underwater currents.
Applications
- Subsea Pipeline Monitoring: Ensuring the structural integrity of pipelines and risers under extreme conditions.
- Marine Cables and Mooring Systems: Monitoring tension in cables and mooring systems to prevent failures and ensure safety.
7. Industrial Robotics
Precision Control in Harsh Conditions: Industrial robots often operate in environments where precision and reliability are crucial despite harsh conditions.
- Thermal and Mechanical Stress: Robots in manufacturing processes may encounter high temperatures and mechanical loads.
- Environmental Exposure: Exposure to dust, chemicals, and moisture.
Applications
- Robotic Arm Tension Control: Ensuring precise movement and operation of robotic arms under various conditions.
- Automated Assembly Lines: Monitoring tension in components handled by robots to maintain quality and efficiency.
Conclusion
Tension amplifiers designed for high-temperature and harsh environments are crucial for ensuring accurate, reliable measurements in industries where precision is non-negotiable despite extreme conditions. Through innovative materials, robust construction, and advanced technology, these devices provide the resilience and performance needed to meet the demanding requirements of modern industrial applications.