Tension Control Systems: Mastering Precision in Manufacturing Process
Whether in textile production, printing presses, or web handling applications, maintaining the optimal tension in materials is essential for achieving the desired outcomes. This article delves into the intricacies of tension control systems, their significance across industries, and the technologies driving their evolution.
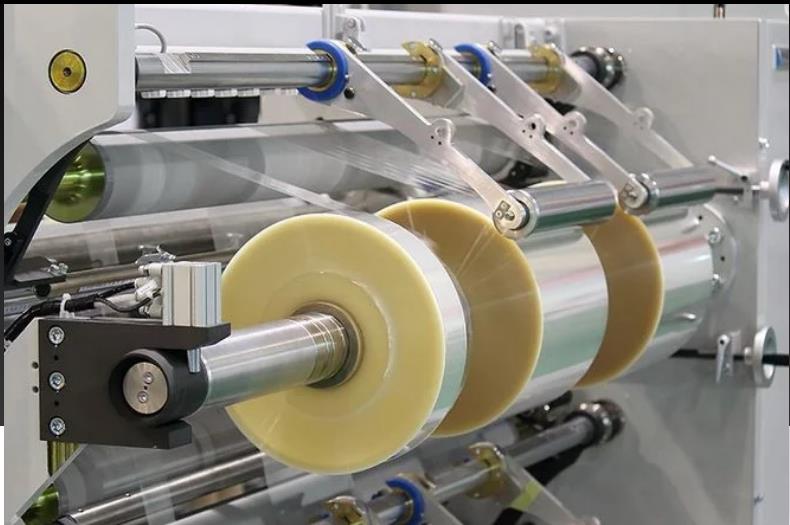
Understanding Tension Control Systems
Tension control systems are engineered mechanisms designed to regulate the amount of tension exerted on a moving material, such as paper, film, fabric, or metal. The objective is to ensure uniform tension throughout the production process, preventing issues like wrinkles, stretching, tearing, or misalignment.
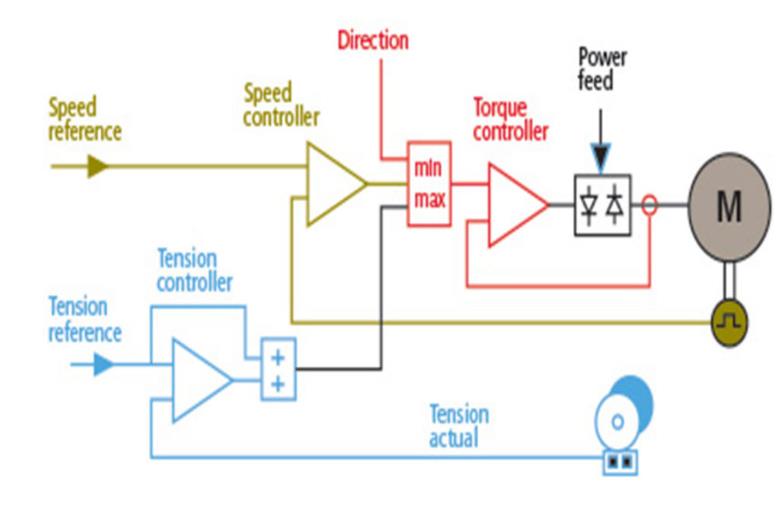
The Dynamics of Tension
The dynamics of tension in materials are complex and multifaceted, influenced by a myriad of factors that interact dynamically throughout the production process.
1. Material Properties
- Different materials exhibit distinct behaviors under tension. For instance, textiles may stretch, while metals may deform or break. Understanding the inherent properties of the material being processed is essential for determining the appropriate tension levels.
- Factors such as elasticity, yield strength, and elongation at break dictate how a material responds to applied forces. Engineers must consider these properties when designing tension control systems to ensure that the material is handled with precision and care.
2. Speed and Acceleration
- The speed at which the material moves through the production line impacts tension dynamics significantly. Rapid acceleration or deceleration can introduce sudden changes in tension, leading to issues such as wrinkles or material breakage.
- Tension control systems must be capable of responding quickly to changes in speed, maintaining consistent tension levels to prevent production disruptions and ensure product quality.
3. Friction and Drag
- Friction between the material and machine components, such as rollers or guides, can affect tension distribution along the material’s length. High levels of friction may cause uneven tension or material slippage, compromising the quality of the end product.
- Tension control systems often incorporate mechanisms to minimize friction, such as precision bearings, low-friction coatings, or air flotation systems. By reducing frictional forces, these mechanisms help maintain uniform tension and improve process efficiency.
4. Environmental Factors
- Environmental conditions, such as temperature and humidity, can influence material properties and tension dynamics. For instance, changes in temperature may cause materials to expand or contract, affecting tension levels.
- Tension control systems may include sensors to monitor environmental variables and adjust tension accordingly. Additionally, climate-controlled production environments can help minimize the impact of environmental fluctuations on tension regulation.
5. External Forces
- External forces, such as wind or vibrations, can introduce disturbances that affect tension stability. In outdoor applications, such as web handling in printing or construction, wind-induced fluctuations in tension pose significant challenges.
- Tension control systems may incorporate features to mitigate the effects of external forces, such as tension compensators or dynamic tension control algorithms. These features help maintain stability and accuracy in tension regulation, even in challenging operating conditions.
Key Components of Tension Control Systems
1. Tension Sensors
- Tension sensors are devices that measure the tension exerted on the material as it moves through the production line. These sensors can take various forms, including load cells, dancer rollers, ultrasonic sensors, or pneumatic tension sensors.
- Tension sensors provide real-time feedback on tension levels, allowing the control system to make necessary adjustments to maintain the desired tension setpoints.
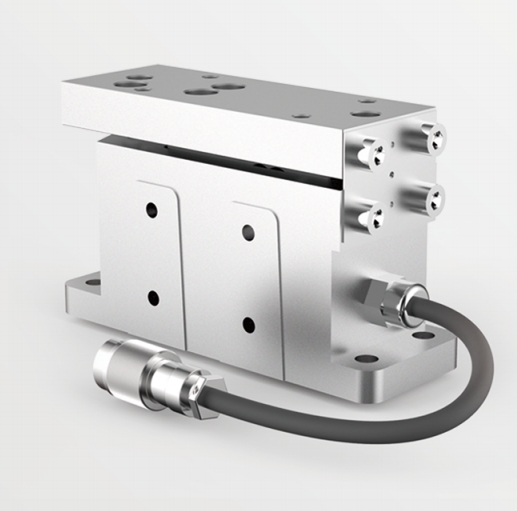
2. Actuators
- Actuators are components responsible for adjusting tension based on feedback from the tension sensors. Common actuators used in tension control systems include electromagnetic brakes, pneumatic clutches, servo motors, and hydraulic tensioners.
- Actuators respond to control signals from the tension control system, either applying or releasing tension as needed to maintain the desired tension levels.
3. Control Algorithms
- Control algorithms form the intelligence behind tension control systems, processing data from tension sensors and issuing commands to actuators to regulate tension. These algorithms can be simple PID (Proportional-Integral-Derivative) controllers or more complex adaptive control systems.
- Control algorithms continuously monitor tension levels and adjust actuator settings to minimize deviations from the target tension, ensuring consistent tension throughout the production process.
4. Rollers and Guides
- Rollers and guides are essential components that guide the material through the production line while minimizing friction and maintaining consistent tension. These components come in various configurations, including idler rollers, nip rollers, dancer rollers, and edge guides.
- Properly designed and positioned rollers and guides ensure that the material remains in contact with the tension sensors and that tension is evenly distributed across the material width.
5. Tension Indicators and Displays
- Tension indicators and displays provide operators with real-time feedback on tension levels, allowing them to monitor the performance of the tension control system and make adjustments as necessary.
- Indicators may include analog gauges, digital displays, or graphical user interfaces (GUIs) that visualize tension data and provide insights into system operation.
6. Control Interface
- The control interface enables operators to interact with the tension control system, set parameters, and adjust settings as needed. This interface may consist of physical controls, such as knobs or buttons, or software-based interfaces accessible via a computer or touchscreen.
- Advanced control interfaces may offer features such as preset tension profiles, automatic tension adjustments based on production parameters, and remote monitoring capabilities.
7. Safety Mechanisms
- Safety mechanisms are crucial components of tension control systems, designed to prevent accidents and protect both equipment and personnel. These may include emergency stop buttons, overload protection devices, interlocks, and safety guards.
- Safety mechanisms ensure that tension control systems operate reliably and securely, minimizing the risk of injury or damage in the event of system malfunctions or operator errors.
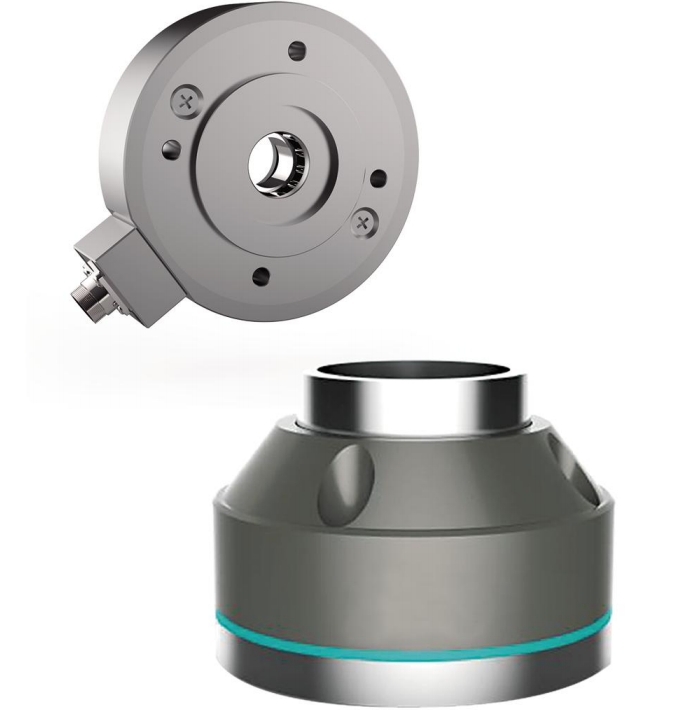
Applications Across Industries of Tension Control Systems
Industry | Applications |
Textiles | Weaving, knitting, yarn processing, fabric stretching, dyeing |
Printing | Offset printing, flexographic printing, gravure printing |
Packaging | Flexible packaging, pouch making, bag making, lamination |
Paper Processing | Paper converting, corrugated board production, sheet feeding |
Film Manufacturing | Extrusion coating, blown film extrusion, cast film production |
Metal Processing | Rolling mills, wire drawing, coil winding, stamping |
Converting | Slitting, sheeting, rewinding, coating, laminating |
Wire & Cable | Cable extrusion, wire winding, cable stranding, insulation coating |
Construction | Web handling in roofing materials, insulation manufacturing |
Automotive | Tire cord manufacturing, seatbelt production, airbag fabric handling |
Challenges and Future Solutions in Tension Control Systems
Addressing the challenges faced by tension control systems requires innovative solutions that leverage advancements in technology, engineering, and automation.
1. Material Variability
- Challenge: Different materials exhibit varying levels of elasticity, friction, and other properties, posing challenges for maintaining consistent tension levels.
- Future Solution: Advanced sensor technologies and machine learning algorithms can be employed to dynamically adapt tension control parameters based on the specific characteristics of each material. Real-time feedback loops can continuously adjust tension settings to compensate for material variability, ensuring uniform quality across production runs.
2. High-Speed Processing
- Challenge: High-speed production lines require rapid response times and precise control to maintain tension levels, minimizing the risk of defects or production stoppages.
- Future Solution: Integration of advanced actuators, such as servo motors and electromagnetic brakes, coupled with digital control systems, enables ultra-fast response times and precise tension control at high speeds. Digital control systems have replaced analog counterparts in many tension control applications, offering greater flexibility, reliability, and performance. Automatic tension controllers leverage microprocessors and advanced algorithms to process sensor data and execute control strategies with enhanced precision. Predictive algorithms can anticipate changes in tension requirements and preemptively adjust control parameters to maintain stability.
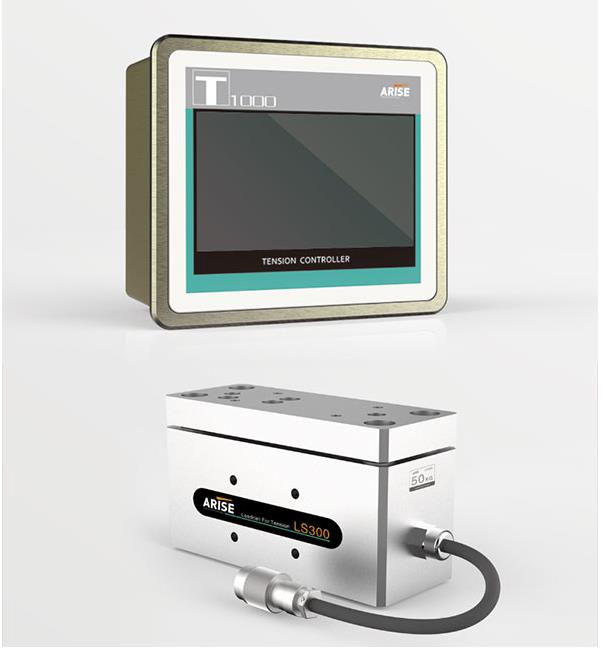
3. Environmental Factors
- Challenge: Environmental conditions, such as temperature, humidity, and air currents, can affect material properties and tension dynamics, leading to fluctuations in tension levels.
- Future Solution: IoT-enabled tension control systems equipped with environmental sensors can monitor and analyze environmental data in real-time. Adaptive tension control algorithms can use this information to dynamically adjust tension settings, compensating for changes in ambient conditions and ensuring consistent performance regardless of external factors.
4. Integration with Industry 4.0
- Challenge: Tension control systems must seamlessly integrate with other components of Industry 4.0-enabled manufacturing ecosystems, such as MES, ERP, and IoT platforms.
- Future Solution: Standardization of communication protocols and data exchange formats facilitates interoperability between tension control systems and other industrial automation systems. Cloud-based analytics platforms enable centralized monitoring, predictive maintenance, and optimization of tension control processes across distributed manufacturing networks.
5. Energy Efficiency and Sustainability
- Challenge: Traditional tension control systems may consume significant amounts of energy, contributing to operational costs and environmental impact.
- Future Solution: Adoption of energy-efficient components, such as regenerative braking systems and low-power actuators, reduces energy consumption while maintaining performance. Integration of renewable energy sources, such as solar or wind power, further enhances sustainability by minimizing reliance on fossil fuels.
6. Maintenance and Reliability
- Challenge: Ensuring the reliability and uptime of tension control systems requires proactive maintenance practices and robust fault detection mechanisms.
- Future Solution: Predictive maintenance techniques leverage sensor data and machine learning algorithms to detect early warning signs of component degradation or failure. Condition monitoring systems continuously assess the health of critical components, enabling timely interventions to prevent unplanned downtime and reduce maintenance costs.
Conclusion
Tension control systems are indispensable tools in modern manufacturing, enabling industries to achieve high levels of quality, productivity, and reliability in their production processes. As industries continue to demand higher standards of quality and efficiency, the mastery of tension control remains an indispensable asset, driving innovation and excellence across the manufacturing landscape.