Remote Monitoring and Diagnostics in Web Inspection Systems
Web inspection systems, which monitor continuous materials like paper, plastic, textiles, and metals for defects and irregularities, are essential for ensuring product quality. Remote monitoring and diagnostics enhance the capabilities of these systems, providing real-time oversight, improving maintenance, and reducing downtime. This article explores the importance, benefits, and implementation of remote monitoring and diagnostics in web inspection systems.
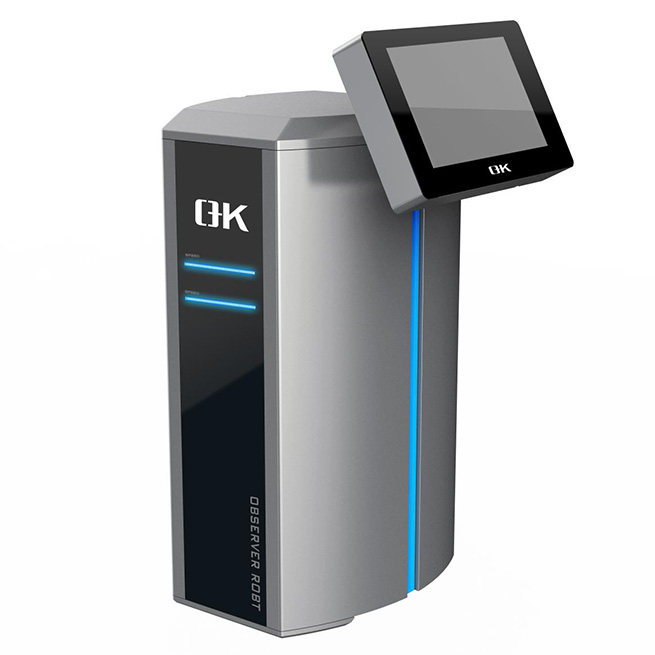
Importance and Benefits of Remote Monitoring and Diagnostics in Web Inspection Systems
Aspect | Importance | Benefits |
Continuous Monitoring | Ensures ongoing quality and performance checks | Detects issues in real-time, maintaining product quality |
Reduced Downtime | Quick identification and resolution of problems | Minimizes production interruptions and increases uptime |
Cost Savings | Reduces the need for on-site inspections | Lowers labor and travel costs, saves on repairs through early detection |
Efficiency Improvement | Enhances overall process efficiency | Optimizes production flow and resource utilization |
Data-Driven Insights | Collects comprehensive data for analysis | Facilitates informed decision-making and continuous improvement |
Predictive Maintenance | Anticipates equipment failures before they happen | Prevents unplanned outages and extends equipment lifespan |
Enhanced Safety | Reduces the need for manual inspections in hazardous areas | Protects workers by minimizing exposure to dangerous conditions |
Scalability | Easily scalable to multiple sites or systems | Allows for centralized monitoring of multiple facilities |
Remote Accessibility | Enables monitoring from any location | Offers flexibility and convenience for management and technicians |
Compliance and Reporting | Helps in maintaining compliance with industry standards | Simplifies the reporting process with accurate, automated logs |
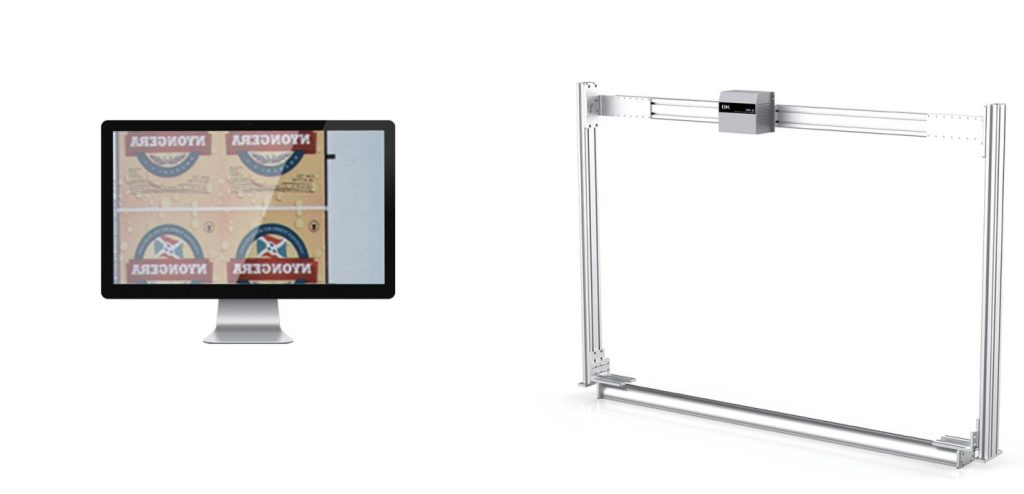
Implementation of Remote Monitoring and Diagnostics in Web Inspection Systems
Implementing remote monitoring and diagnostics in web inspection systems involves integrating various technologies and methodologies to enable real-time monitoring, fault detection, and diagnostics of web inspection processes from remote locations.
1. System Architecture
Hardware Components
- Sensors and Cameras: Install high-resolution cameras and various sensors (e.g., thickness, temperature, tension) along the web inspection line to capture detailed data.
- Edge Devices: Use edge computing devices to preprocess data locally before sending it to the cloud or remote servers.
- Connectivity: Ensure reliable connectivity using wired or wireless networks (e.g., Ethernet, Wi-Fi, 4G/5G).
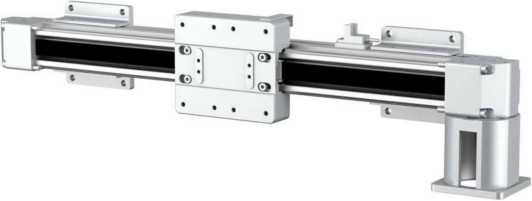
Software Components
- Data Acquisition System (DAS): Implement a DAS to collect and process data from sensors and cameras in real time.
- Remote Monitoring Software: Develop or integrate software platforms that allow remote access to inspection data, visual feeds, and system status.
- Cloud Storage and Computing: Utilize cloud services for data storage, processing, and analytics.
2. Data Transmission and Storage
Secure Data Transmission
- Encryption: Use encryption protocols (e.g., SSL/TLS) to ensure data security during transmission.
- VPN: Implement Virtual Private Networks (VPNs) for secure remote access.
Data Storage
- Cloud Storage: Store inspection data in the cloud for easy access and scalability.
- Redundancy: Implement data redundancy strategies to prevent data loss.
3. Real-Time Monitoring
Dashboard Development
- Custom Dashboards: Develop customizable dashboards that display key performance indicators (KPIs), real-time data, and alerts.
- Visualization Tools: Use graphical tools to visualize data trends, anomalies, and inspection results.
Alerts and Notifications
- Automated Alerts: Set up automated alerts for deviations, anomalies, and faults.
- Notification Channels: Use multiple notification channels (e.g., email, SMS, mobile apps) to ensure timely alerts.
4. Diagnostics and Analysis
Machine Learning and AI
- Predictive Analytics: Implement machine learning algorithms to predict potential faults based on historical and real-time data.
- Anomaly Detection: Use AI techniques to detect anomalies that indicate potential issues.
Diagnostic Tools
- Root Cause Analysis: Develop tools for root cause analysis to identify and address the underlying causes of faults.
- Decision Support Systems: Use decision support systems to provide actionable insights and recommendations.
5. Remote Control and Intervention
Remote Control Capabilities
- Remote Adjustments: Allow remote adjustments of inspection system parameters (e.g., camera focus, sensor calibration) to optimize performance.
- Automated Corrections: Implement automated correction mechanisms that can be triggered remotely based on diagnostic results.
Security Measures
- Access Control: Implement robust access control mechanisms to restrict remote access to authorized personnel only.
- Audit Trails: Maintain audit trails of remote access and interventions for accountability.
6. Integration with Enterprise Systems
ERP and MES Integration
- Data Integration: Integrate inspection data with Enterprise Resource Planning (ERP) and Manufacturing Execution Systems (MES) for comprehensive workflow management.
- Real-Time Updates: Ensure real-time updates and synchronization between inspection systems and enterprise systems.
7. Training and Support
Training Programs
- Remote Training: Develop remote training programs for operators and technicians to familiarize them with the remote monitoring and diagnostics system.
- User Manuals and Documentation: Provide detailed user manuals and documentation for troubleshooting and system operation.
Technical Support
- 24/7 Support: Offer round-the-clock technical support to address any issues that may arise with the remote monitoring system.
- Remote Assistance: Use remote assistance tools to provide real-time support and troubleshooting.
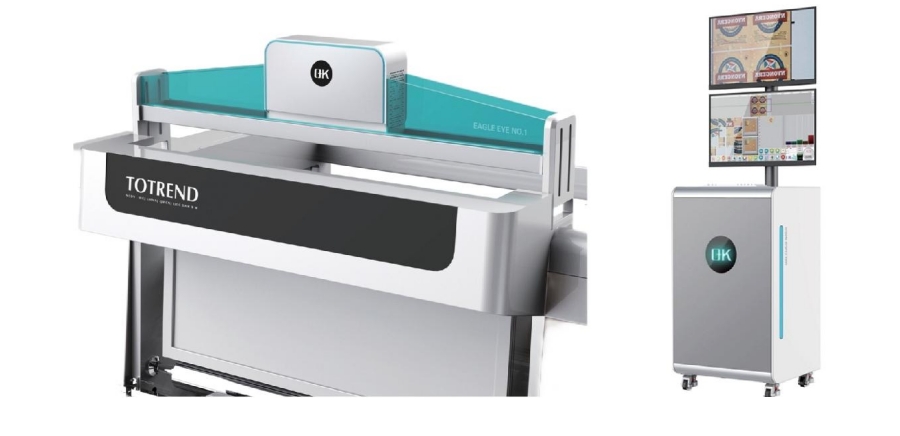
Case Studies of Remote Monitoring and Diagnostics in Web Inspection Systems
Here’s a chart summarizing the case studies of remote monitoring and diagnostics in web inspection systems and demonstrate the significant benefits of web inspection systems across various industries.
Industry | Problem | Solution | Results |
Paper Manufacturing Company | Frequent production stoppages due to undetected defects | Remote monitoring and diagnostics system that continuously scanned the paper rolls for defects. | Reduced downtime by 25%, waste reduced by 15%, improved product quality |
Plastic Film Production Company | Inconsistent quality in plastic films | Remote monitoring system with advanced diagnostics to monitor film quality throughout the production process. | Production efficiency improved by 20%, unplanned maintenance reduced by 30%, data-driven process optimization |
Textile Industrial Company | Slow, labor-intensive manual inspection processes | Remote monitoring and diagnostics system to automate the web inspection process and provide continuous oversight. | Increased productivity by 15%, reduced defective products by 40%, reduced travel costs by 50% |
Metal Sheet Production Company | Inconsistencies in sheet thickness and surface defects | Remote monitoring and diagnostics system to continuously check thickness and surface quality during production. | Reduced rework and scrap by 30%, improved customer satisfaction, enhanced operational efficiency by 18% |
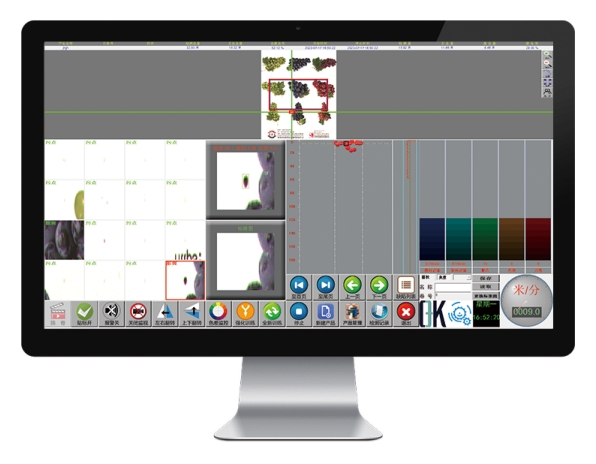
Conclusion
Remote monitoring and diagnostics for web inspection systems represent a significant advancement in manufacturing technology. By leveraging real-time data collection, advanced analytics, and predictive maintenance, companies can enhance product quality, increase operational efficiency, and achieve substantial cost savings. As industries continue to evolve, the integration of remote monitoring and diagnostics will undoubtedly become a standard practice, driving innovation and competitiveness in the manufacturing industries.