Real-time Defect Detection in Printing: Technologies and Trends
Printing quality control is essential to ensure flawless production and minimize waste. With high-speed printing processes, the occurred defects such as smudges, color inconsistencies, misalignment, have led to costly reprints and customer dissatisfaction. Real-time defect detection systems have revolutionized the industry by enabling immediate identification and correction of errors. This article explores the the significance of real-time defect detection, key technologies involved and emerging trends shaping the future of print quality control.
Table of Contents
Common Defects in Printing
This chart provides a comprehensive overview of common printing defects, their causes, and their impact on print quality. Addressing these issues is essential for maintaining high standards in printing operations.
Defect Type | Description |
Misregistration | Occurs when the colors do not align properly, leading to blurry or double images. |
Color Variations | Differences in color tone or hue, causing prints to look inconsistent. |
Smudging | Happens when ink or toner is not properly set, leading to blurred or smeared images/text. |
Paper Jamming | The paper gets stuck in the printer, causing production delays and potential damage. |
Streaking | Horizontal or vertical streaks appear on the printed material due to clogged or misaligned printheads. |
Ghosting | A faint image or text appears from a previous print, caused by excess ink on rollers or improperly cleaned parts. |
Ink Bleeding | Ink spreads beyond the intended area, especially on porous paper, leading to blurred edges. |
Dot Gain | Occurs when halftone dots spread during printing, causing dark or uneven areas on the print. |
Uneven Ink Distribution | Inconsistent ink coverage, leading to areas of lighter or darker print. |
Over/Under Saturation | Areas of the print being either too saturated (too dark) or insufficiently saturated (too light). |
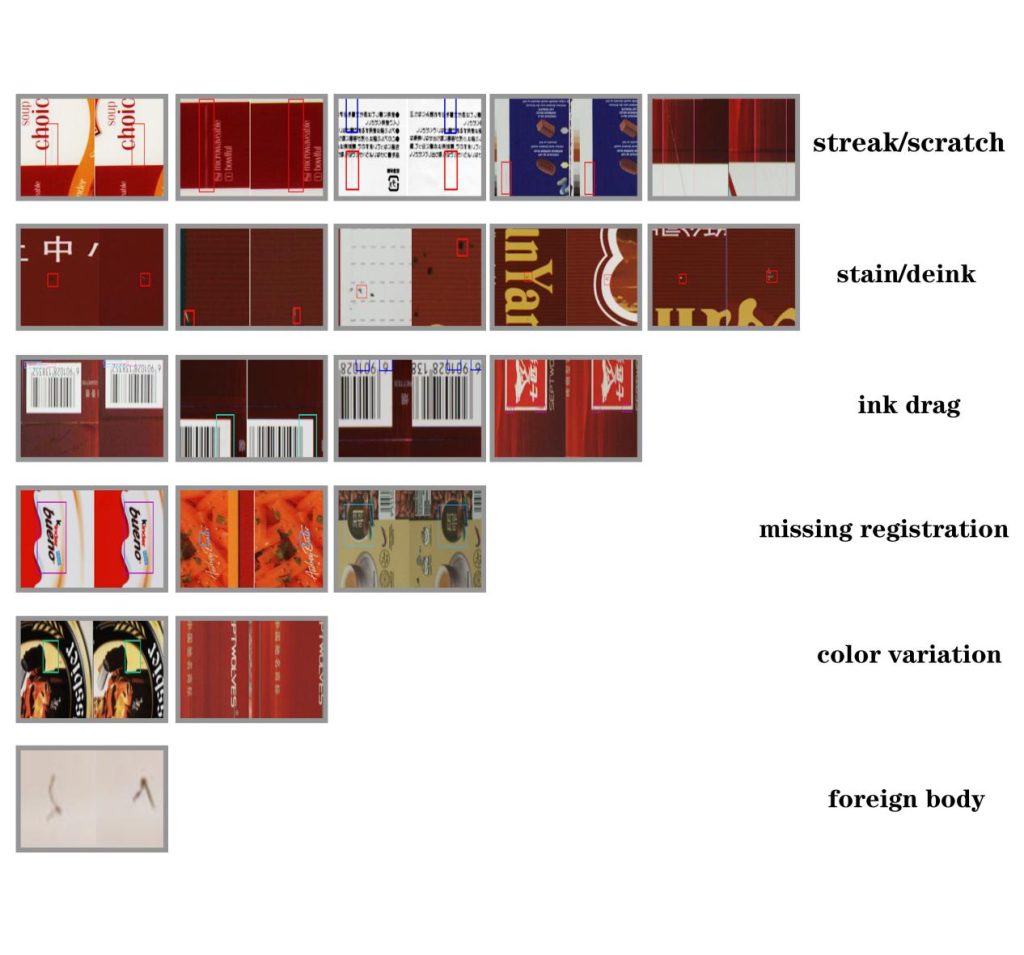
Importance of Real-time Defect Detection in Printing
Real-time defect detection is crucial for maintaining print quality and efficiency. Without an automated defect detection system, errors can go unnoticed, leading to extensive material waste and increased production costs. By identifying defects instantly, printing companies can:
- Ensures High Print Quality: Detects defects such as smudging, misalignment, and color inconsistencies, ensuring consistent and accurate prints.
- Reduces Material Waste: Prevents defective prints from continuing through production, saving ink, paper, and other printing resources.
- Enhances Production Efficiency: Eliminates manual inspections, speeds up the printing process, and reduces the chances of bottlenecks.
- Minimizes Downtime: Identifies issues early, preventing machine failures and reducing production stoppages.
- Improves Cost Savings: Lowers costs associated with reprints, waste, and customer complaints, making printing operations more cost-efficient.
- Ensures Compliance with Industry Standards: Helps meet regulatory and quality requirements, reducing the risk of non-compliance penalties.
- Boosts Customer Satisfaction: Delivers high-quality, defect-free prints that enhance brand reputation and build customer trust.
- Facilitates Automation and Smart Printing: Integrates with AI and IoT to enable adaptive quality control and self-correcting mechanisms.
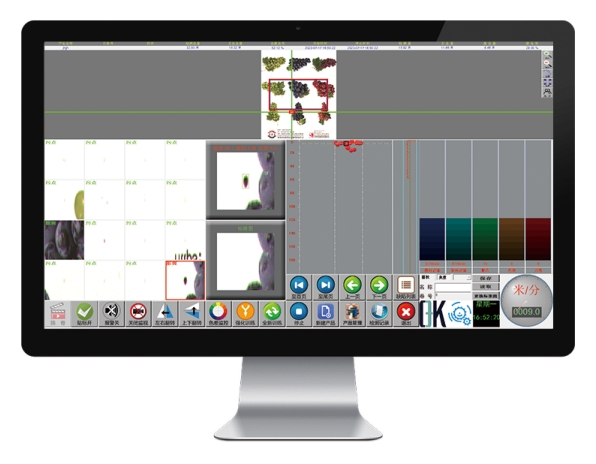
Key Technologies Used in Real-time Defect Detection
1. Machine Vision Systems
Machine vision technology utilizes high-speed cameras and image processing software to capture and analyze printed materials in real-time. These web inspection vision systems detect defects such as misalignment, smudging, missing prints, and streaks by comparing prints against reference standards. Machine vision ensures rapid and precise inspection at high production speeds.
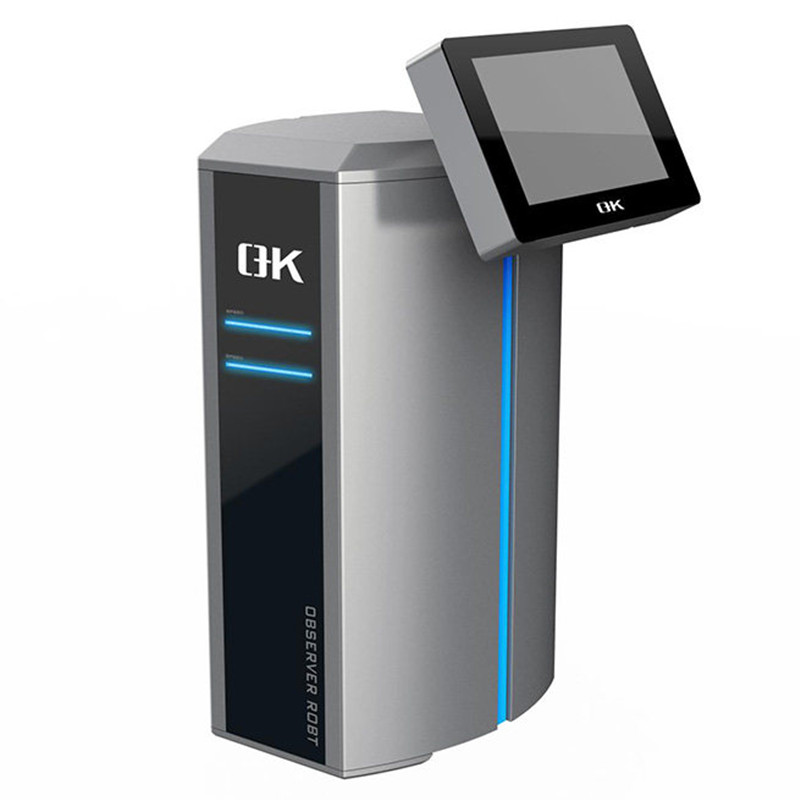
2. Artificial Intelligence (AI) and Deep Learning
AI-driven defect detection systems use deep learning algorithms to identify and classify defects with high accuracy. By training on vast datasets, these systems differentiate between acceptable variations and actual defects. AI continuously improves over time, making it highly effective in handling complex print patterns and colors.
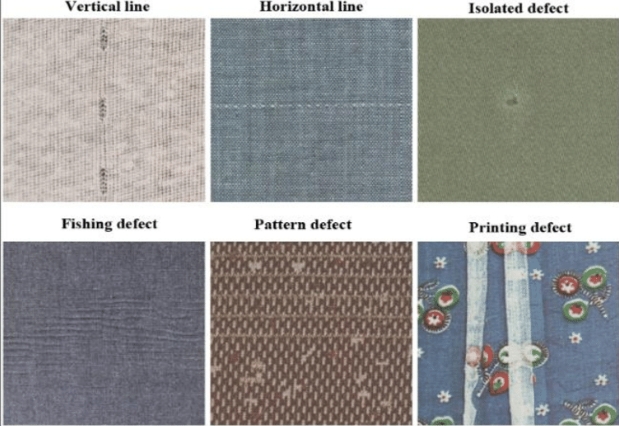
3. Spectral Imaging and Color Inspection
Maintaining color accuracy is essential in printing. Spectral imaging technology analyzes different wavelengths of light to ensure consistent color reproduction. Real-time color inspection systems detect even minor variations in hue, saturation, and brightness, preventing costly reprints and ensuring brand consistency.
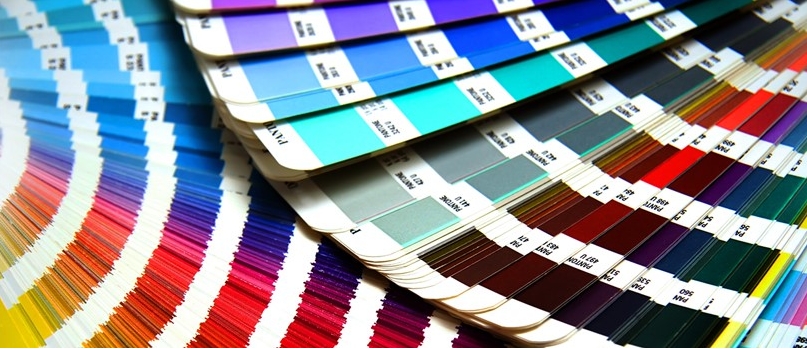
4. Optical Sensors and Laser Scanning
Optical sensors detect surface irregularities, gloss variations, and missing prints. Laser scanning technology provides high-precision inspection by identifying defects such as scratches, uneven ink distribution, and misaligned text. These technologies enhance defect detection in both conventional and high-speed digital printing.
5. Edge Computing for Instant Processing
Edge computing enables defect detection systems to process data directly at the source, reducing latency and enabling immediate corrective actions. This allows printing machines to adjust ink flow, realign printheads, or halt operations in real time, preventing defective prints from progressing through production.
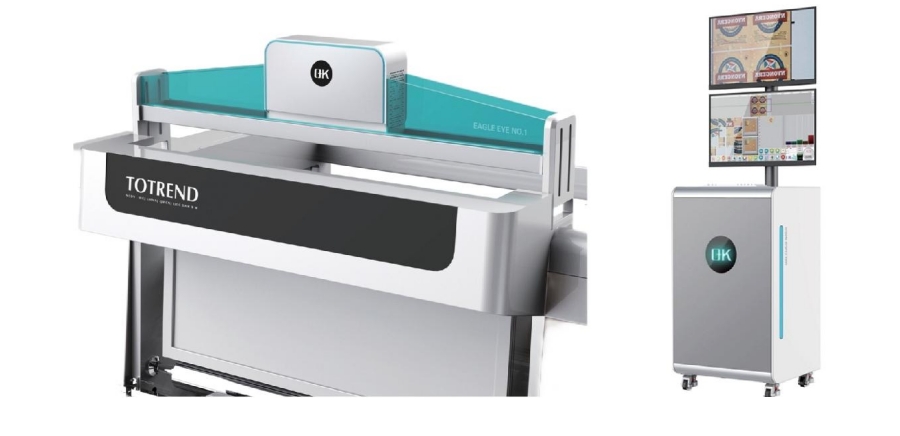
Future Trends in Real-time Defect Detection
As printing technology evolves, real-time defect detection is becoming more advanced, efficient, and intelligent. Innovations in machine learning and automation are driving the next generation of defect detection systems.
- Cloud-based Quality Control Systems
Cloud computing enables remote monitoring and analysis of defect detection data. Cloud-based platforms store inspection data, track defect trends, and provide real-time alerts to operators. These systems allow printing companies to centralize quality control, access data from multiple locations, and improve decision-making through data analytics.
- Integration with Industrial Internet of Things (IIoT)
The Industrial Internet of Things (IIoT) is revolutionizing defect detection by connecting inspection systems, sensors, and printing machines in a smart production environment. IIoT-enabled defect detection allows for real-time data sharing, remote diagnostics, and automated process adjustments, improving efficiency and reducing waste.
- Advanced 3D Inspection Technology
Traditional 2D defect detection is being replaced with high-resolution 3D imaging technology. 3D inspection systems analyze surface textures, embossing, and raised prints with greater precision. This technology is particularly useful in high-end packaging, security printing, and specialty prints where texture consistency is critical.
- Automated Self-Correction Mechanisms
Future defect detection systems will not only identify defects but also correct them automatically. Automated self-correction mechanisms can adjust ink flow, printhead alignment, and roller pressure in real time to ensure consistent print quality. The 100% printing inspection systems will minimize human intervention and improve production efficiency.
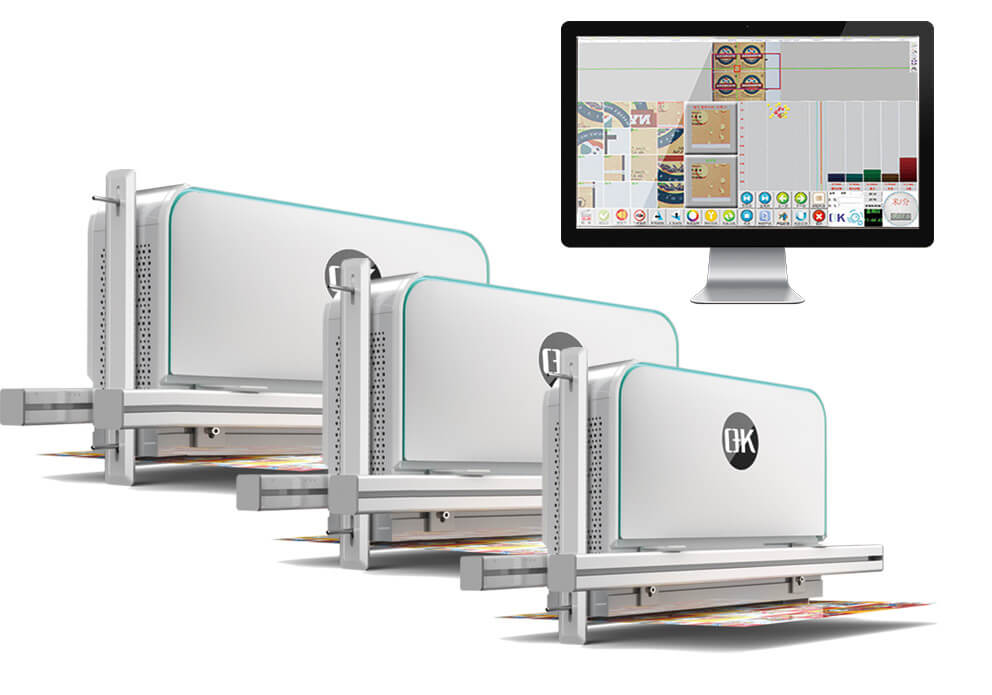
- Augmented Reality (AR) for Quality Control
Augmented reality is emerging as a tool for real-time defect visualization and analysis. AR-enabled inspection systems allow operators to overlay defect detection data onto printed materials, making it easier to identify and assess defects. This technology enhances manual quality control while improving accuracy and efficiency.
- AI-powered Adaptive Inspection
AI-driven adaptive inspection systems can adjust inspection criteria dynamically based on production conditions. These print inspection systems learn from printing variations and modify defect detection thresholds to optimize accuracy without flagging acceptable variations as defects. This reduces false positives and increases productivity.
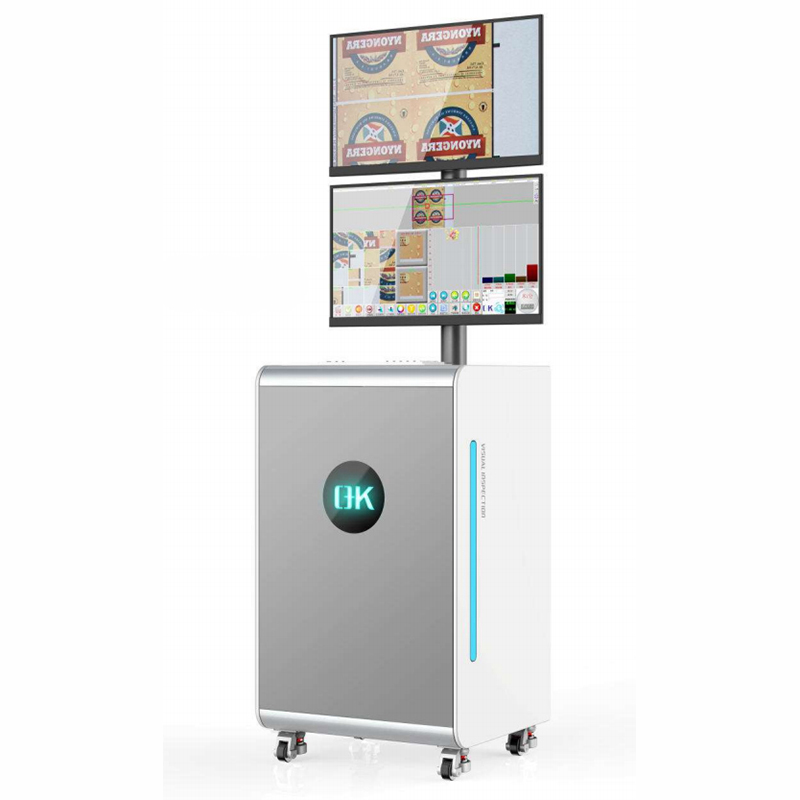
- Blockchain for Quality Assurance
Blockchain technology is being explored for secure defect tracking and traceability. In industries like packaging and security printing, blockchain can provide an immutable record of quality control data, ensuring transparency and compliance with industry standards.
- Sustainable and Energy-efficient Defect Detection
Future defect detection technologies will focus on sustainability by optimizing energy consumption and reducing material waste. AI-powered inspection systems will improve defect detection accuracy, reducing the number of unnecessary reprints and promoting more eco-friendly printing practices.
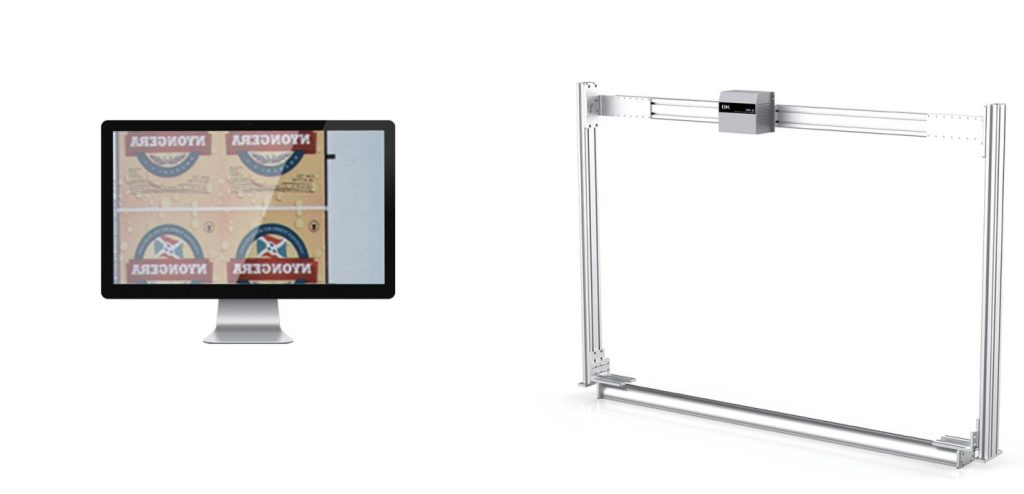
Summary
With the integration of AI, machine vision and automated inspection technologies, printing companies can detect and correct defects in real-time, improving overall productivity and customer satisfaction. As new innovations emerge, defect detection systems will become even more intelligent, helping businesses maintain flawless print quality in an increasingly competitive market.