Innovations in Tension Control Technology for Multi-material Processing
In the rapidly developing landscape of manufacturing is increasingly characterized by the need to process diverse materials with precision and efficiency. Multi-material processing poses unique challenges, demanding advanced tension control systems capable of adapting to a variety of material properties and processing conditions. Innovations in tension control technology are at the forefront of addressing these challenges, enhancing productivity and ensuring high-quality outcomes across industries.
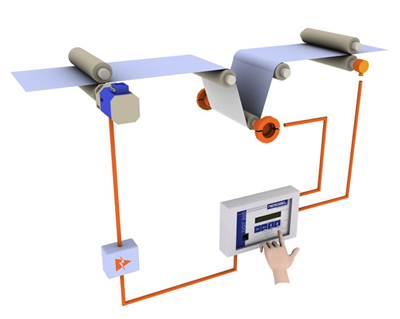
Key Challenges in Tension Control for Multi-material Processing
1. Diverse Material Properties
Different materials possess unique physical and mechanical properties that affect their behavior during processing. These properties include tensile strength, elasticity, thickness, and surface texture. For example:
- Paper: Paper has a relatively low tensile strength and can tear easily if tension is too high.
- Plastic Films: These materials can stretch under high tension, leading to deformation and inconsistencies.
- Metal Foils: Metals can suffer from permanent deformation or breakage if not handled with precise tension control.
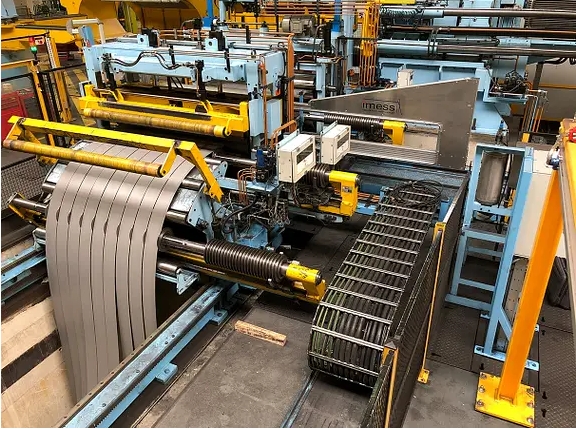
2. Variable Processing Conditions
Multi-material processing often involves different stages, each with distinct requirements and environmental conditions. Factors such as speed, temperature, and humidity can vary significantly between materials and processing stages, affecting tension control. For instance:
- Speed: Variations in processing speed can lead to fluctuating tension levels, requiring real-time adjustments.
- Temperature and Humidity: Changes in temperature and humidity can alter material properties, necessitating adaptive tension control strategies.
3. Complex Machine Setup
Handling multiple materials on the same production line requires complex machine setups with the capability to switch seamlessly between different tension control settings. This complexity includes:
- Equipment Calibration: Frequent calibration is necessary to ensure that tension settings are optimized for each material.
- System Integration: Integrating tension control systems with other machinery and sensors can be challenging, especially when dealing with a variety of materials and processes.
4. Real-time Monitoring and Adjustment
Maintaining consistent tension requires real-time monitoring and adjustment capabilities. However, this can be challenging due to:
Sensor Accuracy: Ensuring that sensors provide accurate and reliable data across different materials and conditions.
Response Time: The system must respond quickly to changes in material behavior to prevent defects.
5. Quality Assurance
Achieving high-quality outcomes in multi-material processing necessitates stringent quality assurance measures. Challenges include:
- Defect Detection: Identifying and correcting defects caused by improper tension control in real-time.
- Uniformity: Ensuring uniform tension across the entire width of the material, especially for wide webs or sheets.
6. Operator Expertise
Effective tension control in multi-material processing demands skilled operators who can manage complex systems and make informed adjustments. Challenges include:
- Training: Providing adequate training for operators to handle advanced tension control systems.
- Experience: Experienced operators are required to troubleshoot issues and optimize settings for different materials.
Key Advancement in Tension Control Systems for Multi-material Processing
1. Adaptive Control Algorithms
Adaptive control algorithms leverage machine learning and artificial intelligence to dynamically adjust tension settings based on real-time data. These algorithms can:
- Learn from historical data to predict the optimal tension settings for different materials.
- Adjust tension in real-time to accommodate changes in material properties and processing conditions.
- Reduce the need for manual adjustments, thus increasing efficiency and consistency.
2. Multi-sensor Integration
Advanced tension control systems now integrate a variety of sensors to provide comprehensive monitoring of the material state. These sensors include:
- Load Cells: Measure the tension force directly and provide precise feedback.
- Ultrasonic Sensors: Monitor the position and speed of materials without physical contact.
- Laser Sensors: Offer high-precision measurements of material dimensions and alignment.
- The integration of these tension sensors allows for a more accurate and responsive control system, capable of handling a wide range of materials.
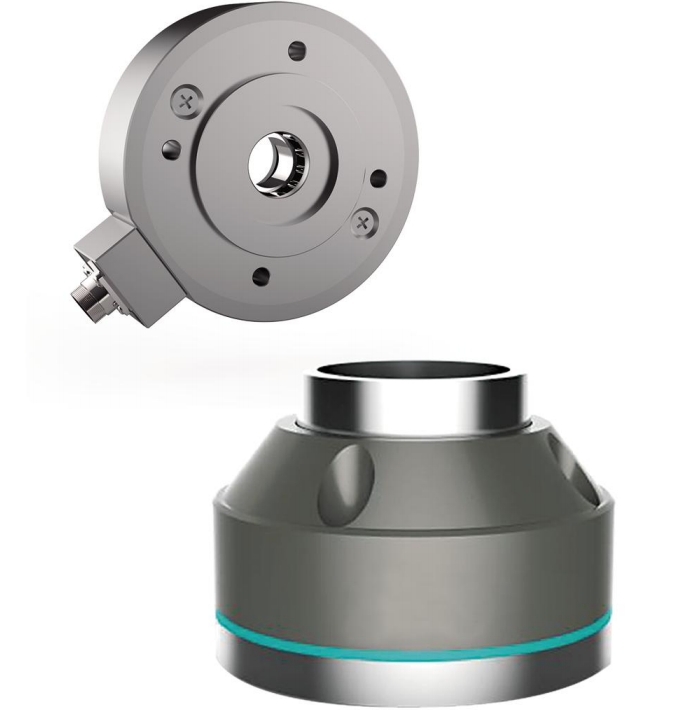
3. Intelligent Feedback Systems
Intelligent feedback systems use data from multiple sensors to make real-time adjustments to tension settings. These systems:
- Detect deviations from the desired tension levels and correct them instantaneously.
- Ensure consistent tension across different materials and processing stages.
- Minimize defects such as wrinkles, breaks, and misalignment.
4. Modular Design
Modular tension control systems provide flexibility and scalability, allowing manufacturers to customize their setups according to specific needs. Key features include:
- Plug-and-play Modules: Easily add or remove components to adapt to different materials and processing stages.
- Interoperability: Seamlessly integrate with existing production lines and other control systems.
- This modular approach enables quick reconfiguration and reduces downtime during material changes.
5. Digital Twin Technology
Digital twin technology creates virtual replicas of physical tension control systems, enabling simulations and optimizations. Benefits include:
- Process Simulation: Test different tension settings and processing scenarios in a virtual environment before applying them on the production line.
- Predictive Analytics: Identify potential issues and optimize tension control strategies proactively.
- Performance Monitoring: Continuously monitor and improve system performance based on real-time data and virtual simulations.
6. Predictive Maintenance
Advanced tension control systems utilize predictive maintenance techniques to ensure continuous operation. Key aspects include:
- Data Analysis: Analyze sensor data to predict when components will require maintenance or replacement.
- Scheduled Interventions: Plan maintenance activities to avoid unexpected downtime and ensure the system operates at peak efficiency.
- This proactive approach reduces downtime and extends the lifespan of equipment.
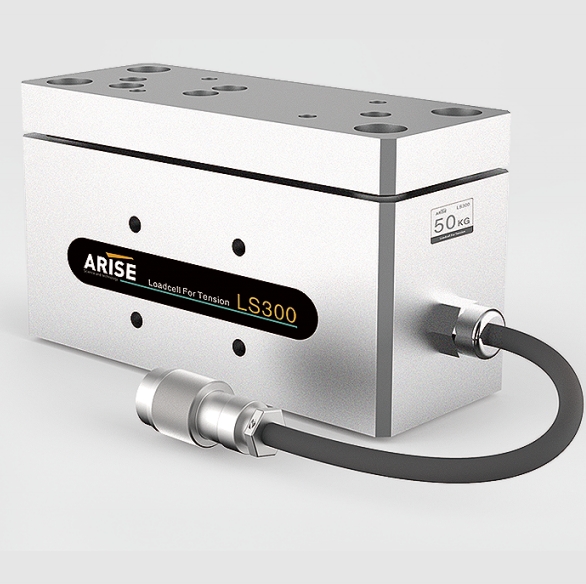
Applications Across Industries of Tension Control for Multi-material Processing
Industry | Application | Benefits |
Printing and Packaging | Ensures smooth operation and high-quality output when switching between different substrates (e.g., paper, plastic films, foils). Maintains print registration and prevents material damage. | Enhanced print quality Reduced material waste Increased operational efficiency |
Textile Manufacturing | Maintains consistent tension during weaving, knitting, and dyeing processes. Adapts to different types of fibers and fabrics. | Uniform fabric quality Reduced defects Improved production consistency |
Automotive and Aerospace | Optimizes tension control in the production of composite materials and lightweight components. Ensures structural integrity and performance of parts. | Enhanced safety and functionality Improved material performance Increased reliability of components |
Electronics Manufacturing | Maintains appropriate tension levels for delicate materials like thin metal foils and flexible circuits. Prevents damage and ensures the reliability of electronic devices. | Increased product reliability 2. Reduced material damage 3. Improved precision in electronic component production |
Paper Production | Controls tension during rolling, cutting, and finishing processes. Ensures uniform thickness and prevents tearing. | Enhanced product uniformity 2. Reduced downtime due to tearing Improved efficiency in paper handling |
Metal Processing | Manages tension during rolling, stamping, and forming processes. 2. Prevents material distortion and ensures precise dimensions. | 1. Enhanced dimensional accuracy 2. Reduced material waste 3. Improved product consistency |
Plastic Film Extrusion | Controls tension during extrusion, cooling, and winding processes. Ensures consistent thickness and prevents wrinkles or tears. | Improved product quality Reduced defects Increased efficiency in plastic film production |
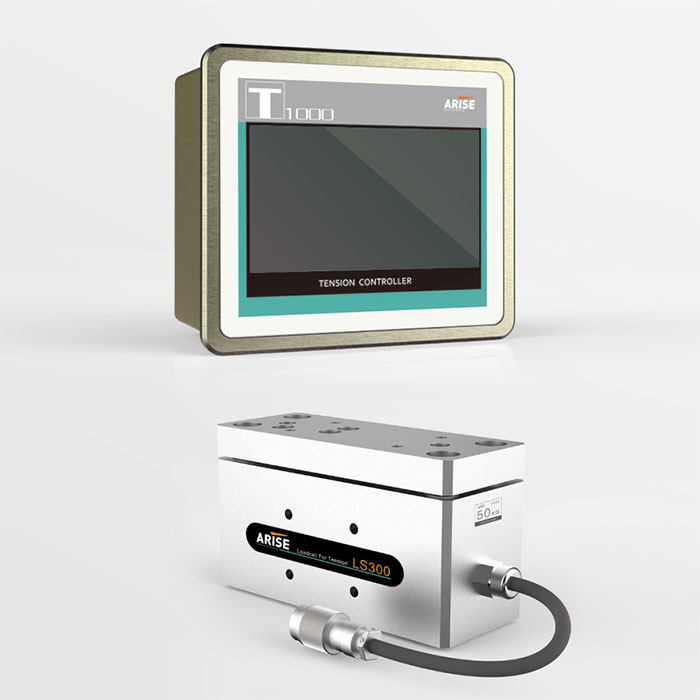
Innovations in tension control systems are revolutionizing multi-material processing, providing the precision, adaptability, and efficiency needed to meet modern manufacturing demands. Advanced tension control technology do a great favor in maintaining competitive advantage and achieving high quality standards.