Inline vs. Offline Print Inspection Systems: Which Type to Choose
In the printing industry, ensuring high-quality output while maintaining efficiency is crucial. Print inspection systems play a vital role in identifying defects, misprints, and inconsistencies. Two primary types of printing inspection systems are used: inline and offline. Each has its own advantages and limitations, and choosing the right system depends on the specific needs of the printing operation. This article explores the differences between inline and offline print inspection systems, their benefits, and their ideal use cases.
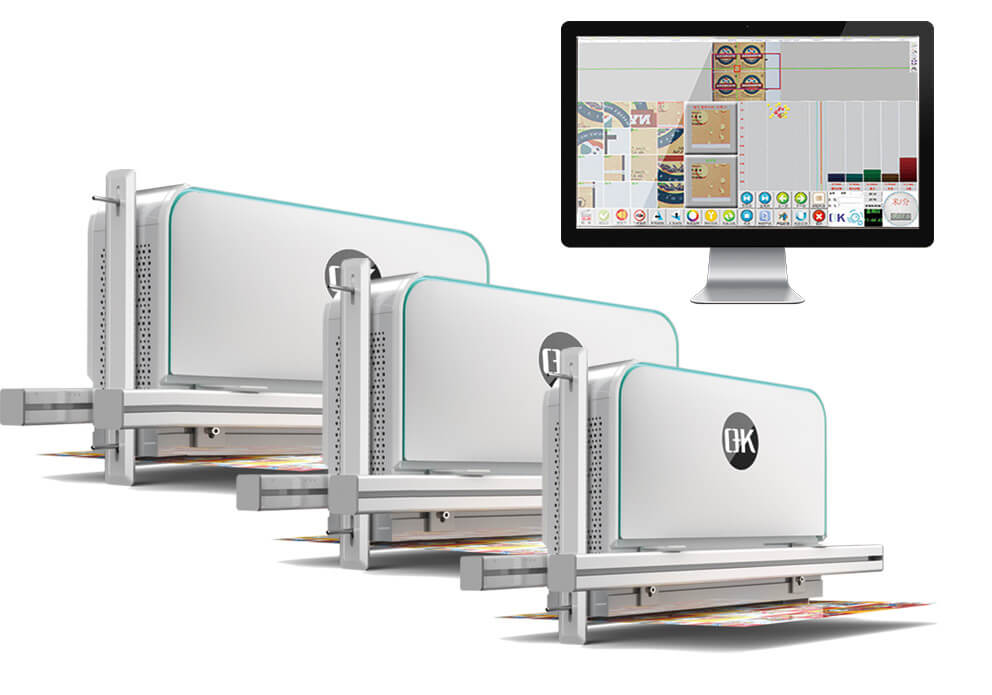
Table of Contents
What are Inline Print Inspection Systems
Inline print inspection systems are integrated directly into the printing press or production line. They perform real-time monitoring and analysis of printed materials as they are being produced. These 100% inspection systems for print quality use advanced technologies such as cameras, sensors, and software algorithms to detect defects, misprints, and color variations instantly.
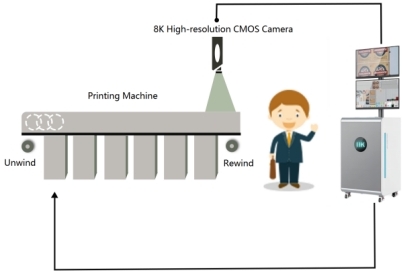
Advantages
- Real-Time Detection: Inline systems identify defects as they occur, allowing for immediate corrective action. This minimizes waste and reduces the risk of producing large quantities of defective prints.
- Increased Efficiency: By automating the inspection process, inline systems eliminate the need for manual checks, speeding up production and reducing labor costs.
- Consistency: Inline systems provide continuous monitoring, ensuring consistent quality throughout the production run.
- Integration with Printing Press: These automated printing quality inspection systems for can often be integrated with the press controls to automatically adjust settings (e.g., color registration) based on inspection results.
Limitations
- Higher Initial Cost: Inline systems are typically more expensive to install and integrate into existing production lines.
- Complexity: They require skilled operators and maintenance to ensure optimal performance.
- Limited Flexibility: Inline systems are designed for specific types of printing presses or materials, making them less adaptable to diverse production needs.
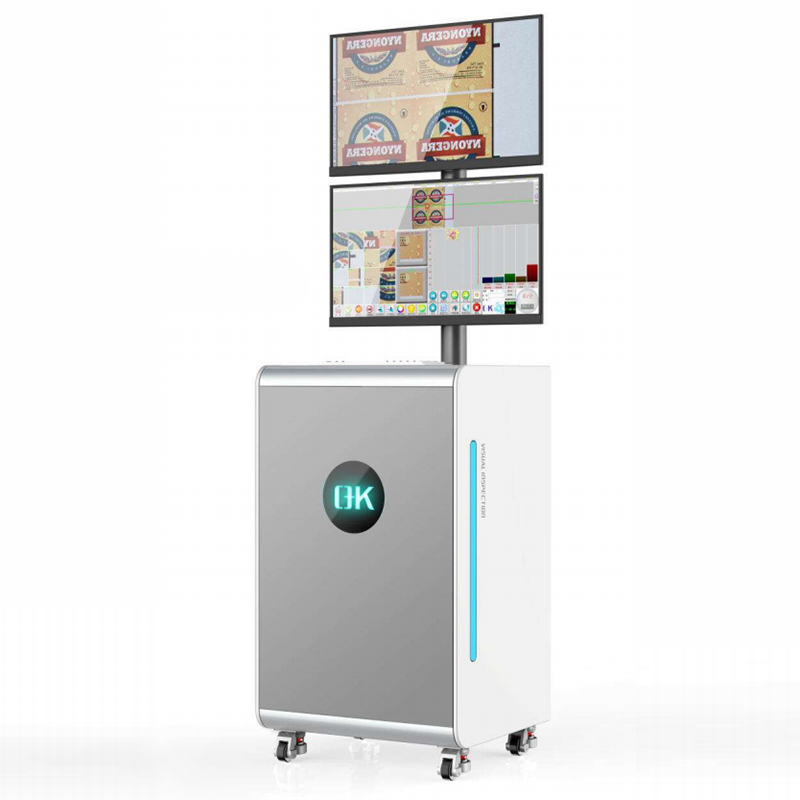
What are Offline Print Inspection Systems
Offline print inspection systems operate separately from the printing press. Printed materials are collected and inspected after the production process is complete. These systems are often used for detailed analysis and quality assurance before final delivery.
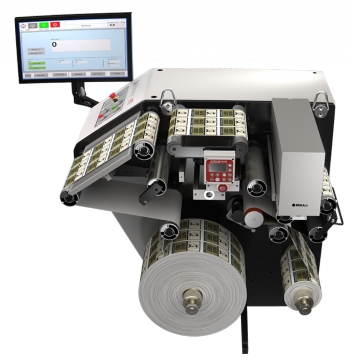
Advantages
- Detailed Analysis: Offline systems can perform more thorough inspections, including higher-resolution scans and advanced color analysis.
- Flexibility: They can be used across multiple production lines or for different types of printed materials.
- Lower Initial Cost: Offline systems are generally less expensive to implement compared to inline systems.
- Ease of Use: They are often simpler to operate and maintain, requiring less technical expertise.
Limitations
- Delayed Detection: Defects are identified after production, which can lead to higher waste and rework costs.
- Slower Process: Offline inspection adds an additional step to the production workflow, potentially slowing down overall throughput.
- Manual Handling: Printed materials must be transported to the inspection system, increasing the risk of damage or contamination.
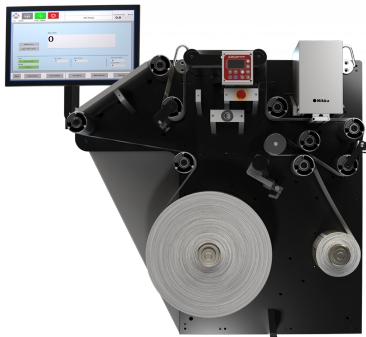
Key Differences Between Inline and Offline Print Inspection Systems
This comparison highlights the distinct features, advantages, and limitations of each system to help businesses make informed decisions.
Feature | Inline Print Inspection Systems | Offline Print Inspection Systems |
Inspection Timing | Real-time, during production | Post-production |
Integration | Integrated directly into the printing press | Operates separately from the production line |
Speed | Faster, no interruption to workflow | Slower, requires additional step |
Defect Detection | Immediate, reduces waste | Delayed, may result in higher waste |
Cost | Higher initial investment | Lower initial cost |
Flexibility | Less flexible, press-specific | More adaptable to different materials |
Complexity | Requires skilled operators and maintenance | Easier to operate and maintain |
Detail of Analysis | Good for real-time monitoring | Better for detailed, high-resolution scans |
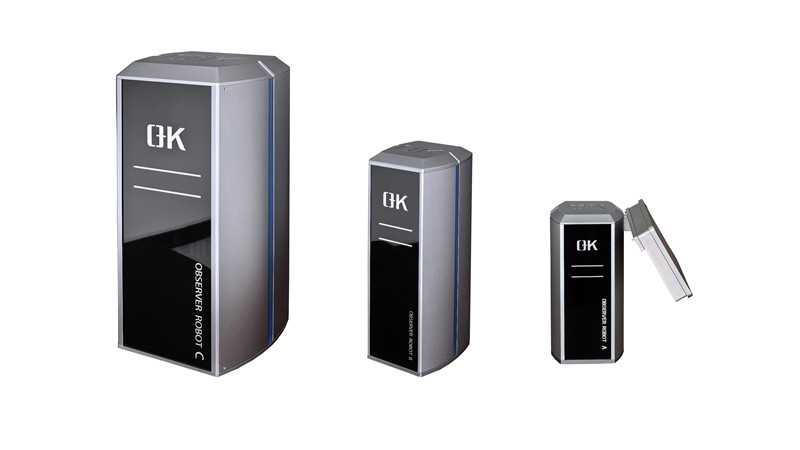
Key Considerations for Choosing the Right Type Between Inline and Offline Print Inspection Systems
This chart provides a quick reference to help businesses evaluate their needs and choose the right printing inspection system for their operations.
Factor | Inline Print Inspection Systems | Offline Print Inspection Systems |
Production Volume | Ideal for high-volume, high-speed production. | Suitable for low to medium-volume production. |
Defect Detection | Immediate detection, reduces waste. | Delayed detection, may result in higher waste. |
Initial Cost | Higher upfront investment. | Lower initial cost. |
Flexibility | Less flexible, often press-specific. | More adaptable to different materials and processes. |
Quality Requirements | Best for industries with strict quality standards. | Suitable for detailed, high-resolution analysis. |
Scalability | Ideal for large-scale operations with potential for expansion. | Better for smaller or diverse operations. |
Industry Use Cases | Packaging, labels, newspapers, pharmaceuticals. | Fine art printing, custom packaging, prototyping. |
Final Decision: Which System to Choose
Choose Inline Inspection if:
- You need real-time quality control for high-speed, large-scale printing.
- Reducing material waste and immediate error correction is a priority.
- Your production line is heavily automated and requires seamless integration.
Choose Offline Inspection if:
- You work with smaller batches, variable jobs, or high-precision printing.
- You need in-depth analysis and high-resolution defect detection.
- You prefer a cost-effective solution without complex integration.
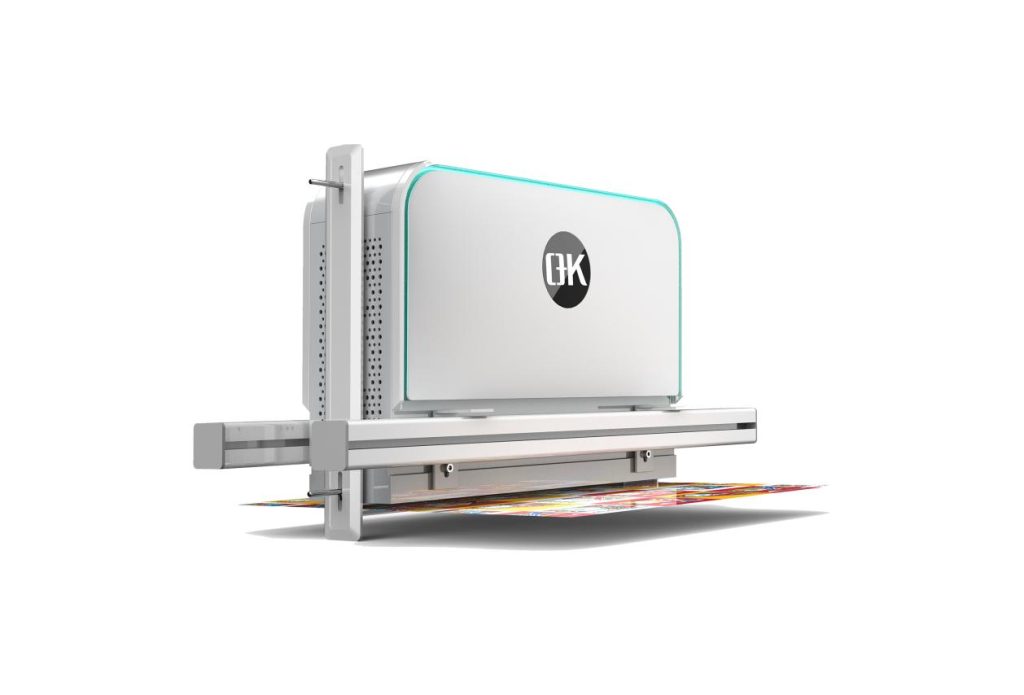
Future Trends in Print Inspection Systems
As technology advances, the line between inline and offline systems is beginning to blur. Hybrid solutions that combine the real-time capabilities of inline systems with the detailed analysis of offline systems are emerging. Additionally, advancements in artificial intelligence (AI) and machine learning are enabling more sophisticated defect detection and predictive maintenance, further enhancing the efficiency and accuracy of print inspection systems.
Conclusion
Both inline and offline print inspection systems play crucial roles in maintaining print quality and ensuring customer satisfaction. While inline systems excel in real-time monitoring and efficiency, offline systems offer flexibility and detailed analysis. Through understanding the strengths and limitations of each type, printing businesses can make informed decisions that align with their production goals and quality standards.