How Web Tension Controllers Play A Crucial Role in Nonwoven Production Process
Nonwoven fabric production is a difficult process that necessitates precision and consistency. Web tension control is an important aspect in assuring the quality and efficiency of nonwoven production. Web tension controllers are critical in maintaining optimum material tension throughout the production process. In this post, we will delve into the importance of web tension controllers in the nonwoven manufacturing process.
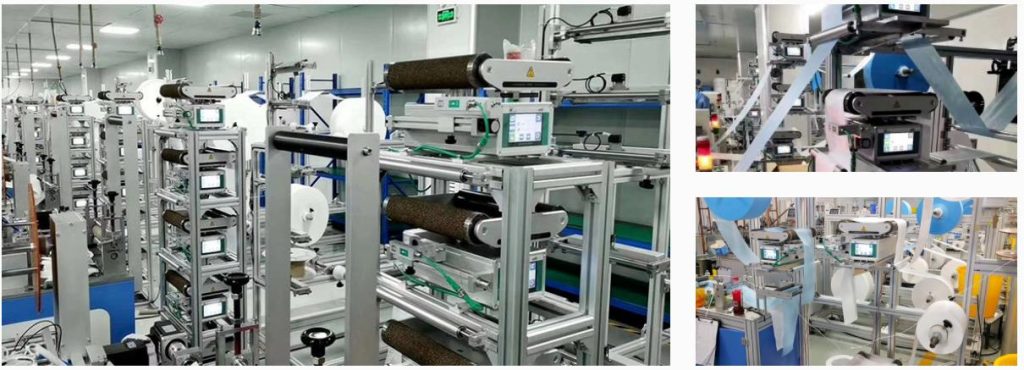
Key Roles and Significance of Web Tension Controllers in Nonwoven Production Process
Web Formation and Fiber Laying
The generation of a loose web of fibers is the initial stage in nonwoven manufacture. A continuous supply of fibers is laid down onto a conveyor belt or a revolving drum at this stage. A uniform web requires an even dispersion of fibers, which is where web tension controllers come in.
Tension Regulation: Web tension controllers helps in the regulation of the speed of the conveyor belt or drum, ensuring that fibers are laid down consistently. This controlled strain prevents the material from overstretching or drooping, which could result in an uneven web.
Web Bonding and Consolidation
After the fiber web is generated, it undergoes a bonding procedure to consolidate the fibers and create a cohesive fabric. Bonding can take place using techniques such as needle punching, thermal bonding, or chemical bonding. For numerous reasons, proper web tension control is critical during this phase:
Uniform Bonding: Consistent web tension ensures that the fibers are held together uniformly during the bonding process, which can be accomplished by mechanical needles, heat, or chemicals. This homogeneous bonding is critical for the overall quality and strength of the fabric.
Preventing Breaks: Web tension control aids in the prevention of material disturbances or breaks during bonding. Sudden variations in tension can cause material breakage or wrinkles, disrupting the process and jeopardizing the fabric’s integrity.
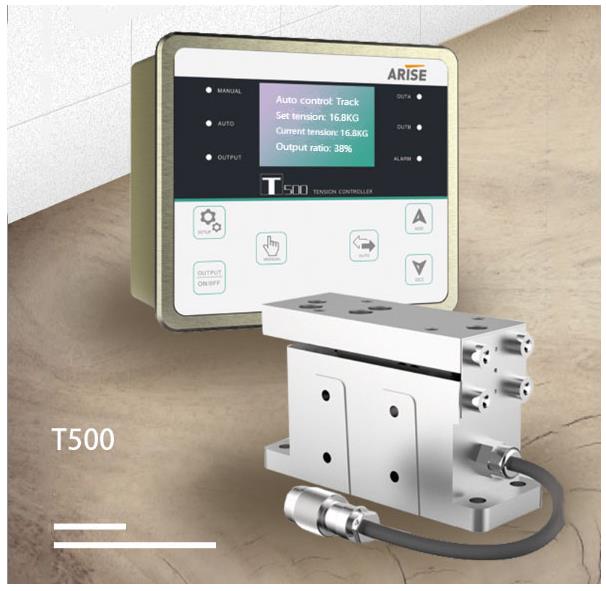
Web Finishing and Additional Processes
Nonwoven fabrics are frequently treated after bonding, such as calendering (where the fabric is run through rollers to obtain a smoother texture and thickness), drying, coating, or other finishing procedures. Web tension control is still an important aspect in these stages:
Quality Enhancement: Web tension controllers ensure that the fabric is processed evenly and at the correct tension during finishing processes. This enhances the quality of the final product, resulting in nonwoven fabrics with consistent characteristics.
Preventing Defects: Proper tension control helps prevent defects such as wrinkles, creases, or uneven coating during the finishing stages. This reduces waste and enhances the efficiency of the production process.
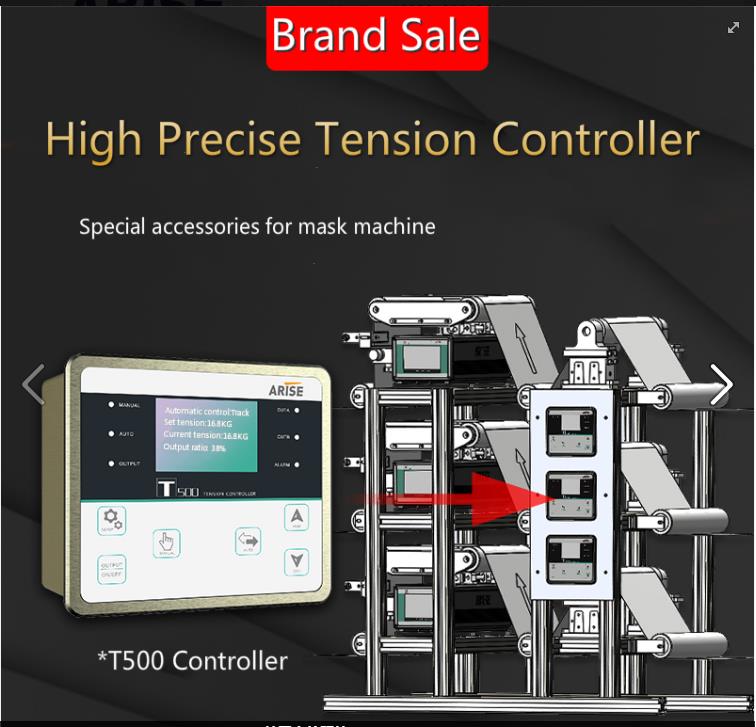
Advantages of Web Tension Controllers in Nonwoven Production Process
Quality Control
It is critical to maintain consistent web tension while making high-quality nonwoven materials. It ensures that the fabric’s qualities, such as thickness and strength, are consistent along its whole length.
Efficiency
Web tension controllers aid in the prevention of material waste caused by wrinkles, creases, and other flaws that might emerge when tension is not effectively handled. This leads to more effective manufacturing processes and cost savings.
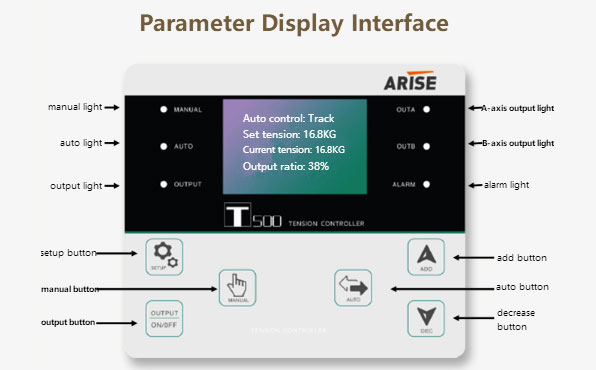
Reduced Downtime
Proper web tension control minimizes the risk of breaks or tears in the material, reducing downtime for repairs and adjustments.
Product Variety
Nonwoven fabric manufacturers often produce a range of products with varying properties. Web tension controllers allow for easy adjustments to accommodate different materials and production requirements.
Safety
Consistent tension control enhances workplace safety by reducing the risk of accidents caused by sudden material movements or breaks.
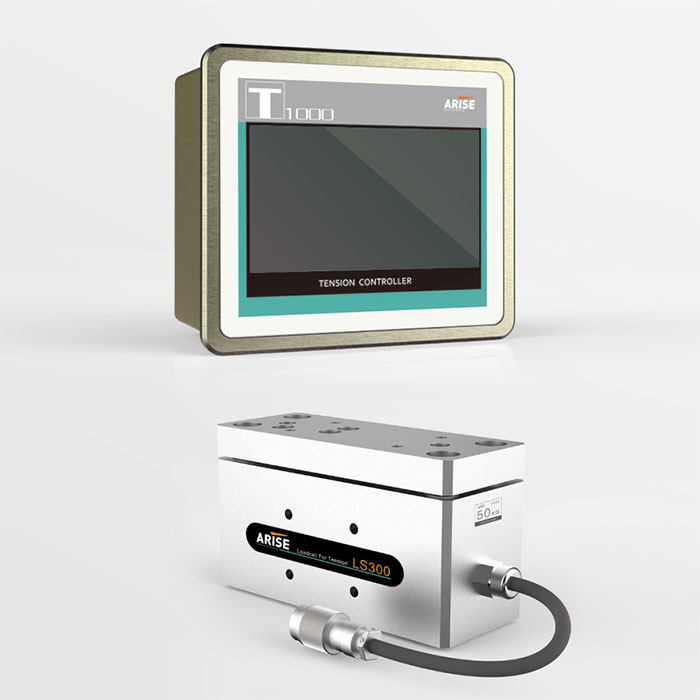
Conclusion
Tension control is essential in nonwoven manufacturing processes. Web tension controllers are critical to the quality, efficiency, and safety of nonwoven fabric manufacturing. As the need for nonwoven items grows in numerous industries, the function of web tension controllers will become even more important in satisfying these demands while maintaining high quality standards.