How to Troubleshoot Common Issues of Web Guide Systems in Industrial Applications
When functioning optimally, web guide systems ensure that materials move along a designated path without deviation, preventing defects and material wastage in wide industrial applications. However, like any complex machinery, web guide systems can experience issues that compromise their performance. Troubleshooting these problems promptly and accurately is critical to maintaining production efficiency and quality.
Table of Contents
Understanding the Role of Web Guide Systems in Industrial Applications
Before diving into troubleshooting, it’s important to recognize the core function of a web guide system in various industrial applications. These systems detect and correct the lateral position of a moving web, ensuring it stays within specified tolerances. A typical web guiding control system includes sensors, actuators (such as pneumatic or electromechanical devices), a control unit, and guiding mechanisms.
When any component malfunctions or becomes misaligned, the system may fail to guide the web accurately, leading to edge wandering, wrinkling, or tension issues, all of which can reduce product quality and increase downtime.
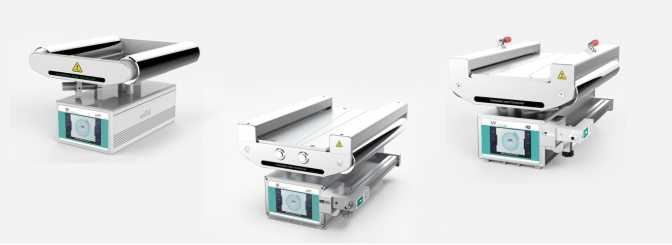
Different Industrial Applications of Web Guide Systems
Industry | Application Description | Purpose of Web Guiding |
Printing and Packaging | Used in flexographic, gravure, and offset printing lines to guide paper or film. | Ensures precise print registration and prevents edge misalignment. |
Textile Manufacturing | Applied in weaving, dyeing, and coating processes for continuous fabric alignment. | Maintains consistent fabric tracking and avoids material wrinkling. |
Plastic Film Production | Guides thin films during extrusion, slitting, or laminating processes. | Prevents web drifting and ensures edge trimming accuracy. |
Paper and Pulp Industry | Integrated into paper winding and coating systems. | Preserves sheet integrity and roll formation quality. |
Battery Manufacturing | Used in the production of electrode and separator films in lithium-ion battery lines. | Ensures tight tolerances and proper layer alignment. |
Nonwoven Fabric Processing | Found in hygiene product lines and filtration media production. | Helps in accurate folding, cutting, and bonding of web materials. |
Flexible Electronics | Used in roll-to-roll processing of OLED, solar film, and printed electronics. | Maintains micro-scale alignment for precision applications. |
Labeling and Converting | Guides labels and adhesive materials through die-cutting and rewinding stations. | Prevents skew and ensures accurate positioning. |
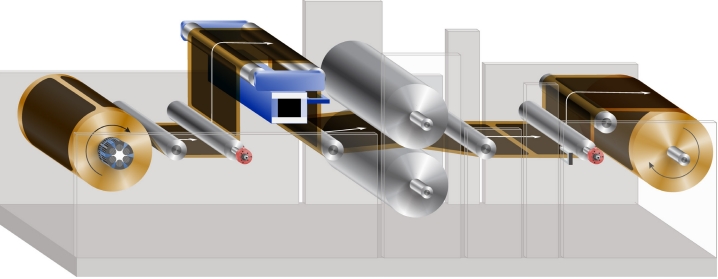
Common Issues and Troubleshooting Approaches in Web Guide Systems
1. Web Misalignment or Drifting
Symptoms:
In this scenario, the web begins to shift gradually from its intended path. Over time, the material might veer off-track, resulting in one side touching the machine frame or producing uneven winding. Operators may also notice skewed prints or visible edge wrinkles as the roll becomes increasingly off-center.
Causes:
This issue is often attributed to misaligned or unclean sensors failing to detect the web edges accurately. Improper threading during setup or uneven mechanical tension across the web can also lead to instability. Additionally, loose or worn guide rollers and incorrect calibration may contribute to a drifting effect.
Solutions:
To resolve the problem, the first step is to ensure that all web guide sensors are clean and correctly aligned according to manufacturer’s specifications. Re-threading the material path to meet the system’s layout and confirming that tension is consistent can also help. Mechanical components like rollers and actuators should be checked for stability, and system calibration should be verified or re-executed using reference materials.
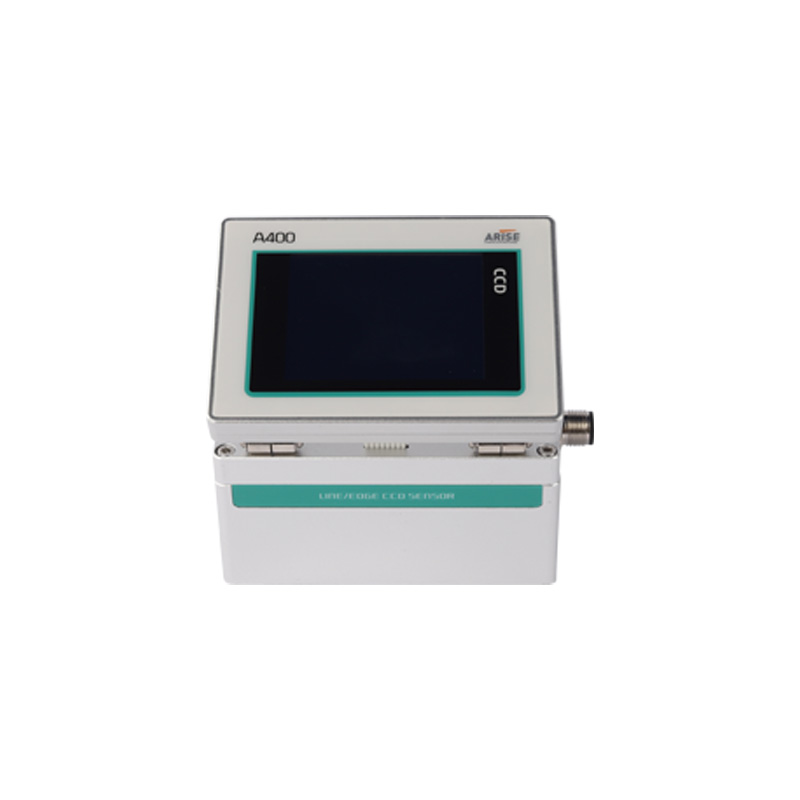
2. Sluggish or Delayed Guiding Response
Symptoms:
When the system is slow to correct the web’s position, it causes the material to wander before the actuator engages. Corrections feel unresponsive, leading to poor control, especially during fast runs or when material properties vary slightly.
Causes:
This is typically due to poorly tuned controller settings that do not react promptly to sensor input. An underpowered or aging actuator may also be to blame, or there could be excessive friction within mechanical elements like bearings or rails. Communication delays between sensors, controllers, and actuators can further reduce system reactivity.
Solutions:
Technicians should review and adjust control parameters such as proportional and integral gain settings. The actuator’s performance must be evaluated, and if it shows signs of fatigue, replacement may be necessary. Inspecting the mechanical path for friction points and ensuring reliable communication links among components will help restore proper system dynamics.
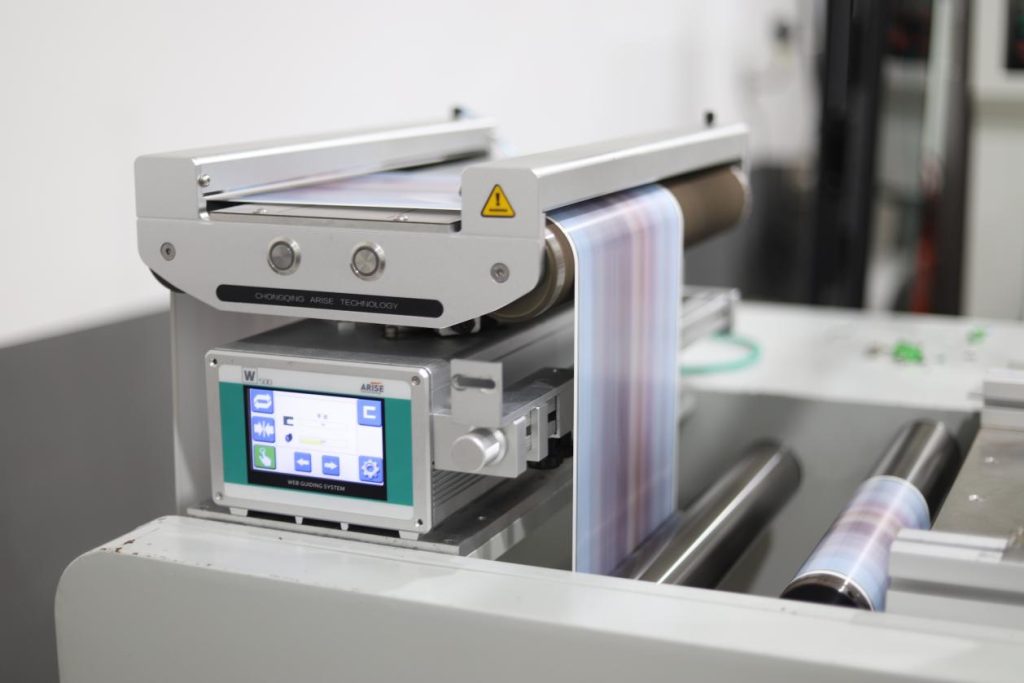
3. No Guiding Action Detected
Symptoms:
In this case, the web guide system appears inactive. Despite misalignment of the material, the actuator does not move, and there is no correction occurring during operation.
Causes:
This situation may result from a complete power loss to the web guiding controller. Signal cables could be disconnected or damaged. Hardware failure within the sensors, actuators, or controller may also be responsible, as well as improper initialization of the system or a software error.
Solutions:
The troubleshooting process involves confirming that power is being properly supplied to all system components. All wiring connections should be checked for continuity and secure placement. If hardware faults are suspected, diagnostic tools or substitute modules may be used to isolate the failing part. Reinitializing the software or resetting the controller may also restore function if the issue is firmware-related.
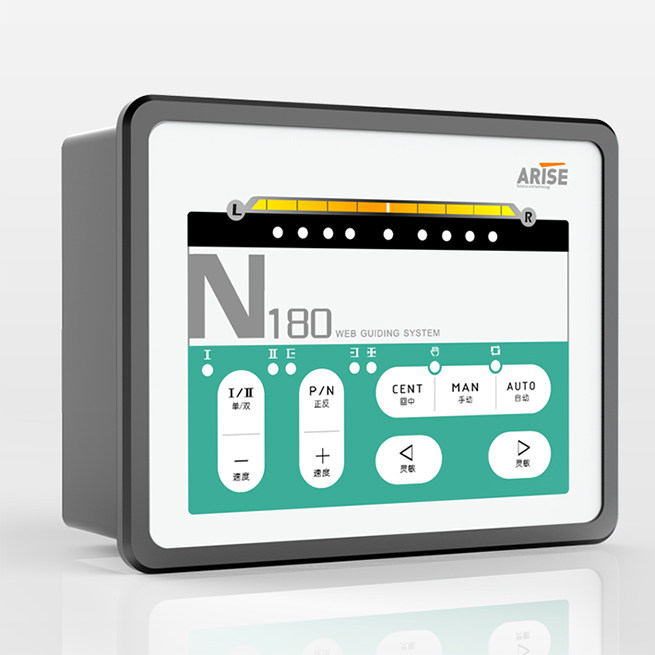
4. Erratic or Overreactive Guiding Movements
Symptoms:
The web guide actuator moves erratically or jitters, leading to overcorrections or oscillations. Instead of smooth adjustments, the system appears overly aggressive or unstable, sometimes causing mechanical strain or web tension issues.
Causes:
This behavior often results from incorrect controller tuning, particularly when gain values are set too high. It may also be triggered by external environmental factors such as vibration, inconsistent lighting on sensors, or electrical interference. Some sensors may struggle with certain web materials, especially reflective or semi-transparent surfaces.
Solutions:
Improved system tuning is essential to achieve balanced, damped motion. Environmental shielding should be introduced if light, vibration, or electromagnetic interference are influencing sensor output. In some cases, sensor replacement with more material-compatible technology (e.g., ultrasonic or contrast-based sensors) can stabilize detection and reduce erratic response.
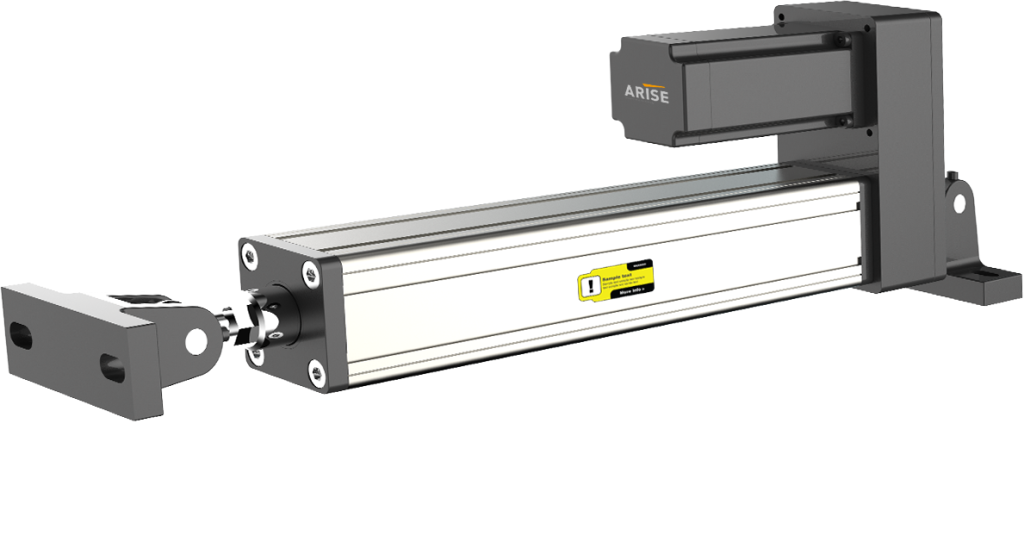
5. Material Tearing or Edge Damage
Symptoms:
During operation, the material tears or exhibits visible edge damage. This problem usually appears at higher speeds, where the guide corrections are more frequent and forceful.
Causes:
Edge damage is commonly caused by excessive lateral force from the actuator or sudden guiding movements. If web tension is not maintained evenly, it can compound the risk of tearing. Misaligned rollers and harsh mechanical contact can also damage delicate web edges.
Solutions:
Limiting the actuator’s range of motion and softening correction parameters can reduce stress on the material. Verifying and adjusting web tension to appropriate specifications is also critical. Mechanical inspections should focus on roller alignment and surface conditions to eliminate abrasive or misaligned components.
6. Inconsistent Performance with Different Materials
Symptoms
The web guide system functions properly with one type of material but fails to maintain alignment when a different substrate is introduced. This may include difficulty detecting transparent, reflective, or dark-colored webs.
Causes:
Sensor incompatibility with specific material properties is often to blame. Changes in light reflection, opacity, or thickness can interfere with consistent edge detection. Systems not recalibrated for different materials will misinterpret edge positions.
Solutions:
Operators should use sensors designed for versatile detection, such as ultrasonic edge sensors or Infrared-based web guide sensors that handle a wide range of material types. Calibrating the sensor sensitivity for each material type is recommended before production starts. A programmable control system with stored material profiles can help streamline the switching process.
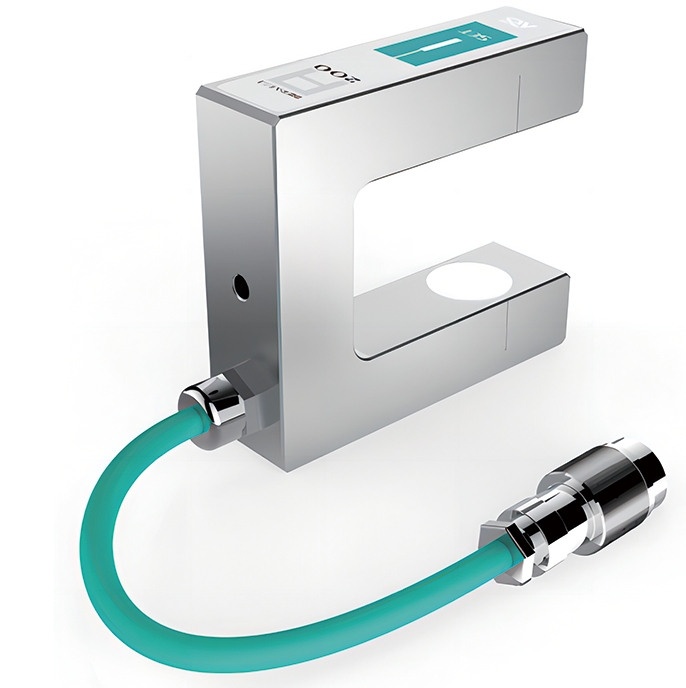
Preventive Maintenance Tips for Web Guide Systems
Maintenance Area | Tip | Frequency | Purpose |
Sensor Cleaning and Inspection | Clean optical/ultrasonic sensors with a lint-free cloth and check alignment. | Weekly or as needed | To ensure accurate edge detection and prevent signal errors. |
Actuator Lubrication | Lubricate moving mechanical parts following the manufacturer’s guide. | Monthly | To maintain smooth motion and reduce mechanical wear. |
Control System Check | Inspect connections, firmware updates, and run diagnostics. | Quarterly | To ensure control accuracy and prevent signal lag. |
Roller and Guide Inspection | Examine for wear, buildup, or misalignment. Clean and adjust if necessary. | Biweekly | To maintain stable web tension and reduce tracking errors. |
Tension System Verification | Check web tension controllers and adjust for web type and width. | With every material change | To avoid edge tearing and inconsistent alignment. |
Cable and Connector Check | Inspect for loose or damaged cables and secure all connections. | Monthly | To prevent communication failures between system components. |
Environmental Control | Keep sensors free of dust, shield from vibration and lighting variations. | Continuous monitoring | To reduce false signals and erratic guiding behavior. |
Operator Training | Refresh on calibration steps, software use, and safety protocols. | Every 6 months | To ensure correct operation and reduce handling-related issues. |

Summary
Troubleshooting web guide systems requires a systematic approach, beginning with identifying symptoms, isolating the root cause, and applying the appropriate corrective solutions. Most issues stem from mechanical misalignment, sensor errors, actuator wear, or controller configuration problems. By maintaining the web guide system properly and addressing issues proactively, manufacturers can ensure reliable guiding performance, enhance product quality and reduce costly downtime in industrial applications.