How to Retrofit Tension Control System
Table of Contents
In industries where material processing relies on precise tension control, outdated systems can impede performance and reduce productivity. Retrofitting offers a cost-effective and efficient way to upgrade these systems, leveraging modern technologies without the expense of complete replacements. This article explores practical retrofit solutions for upgrading tension control systems, emphasizing their benefits and implementation strategies.
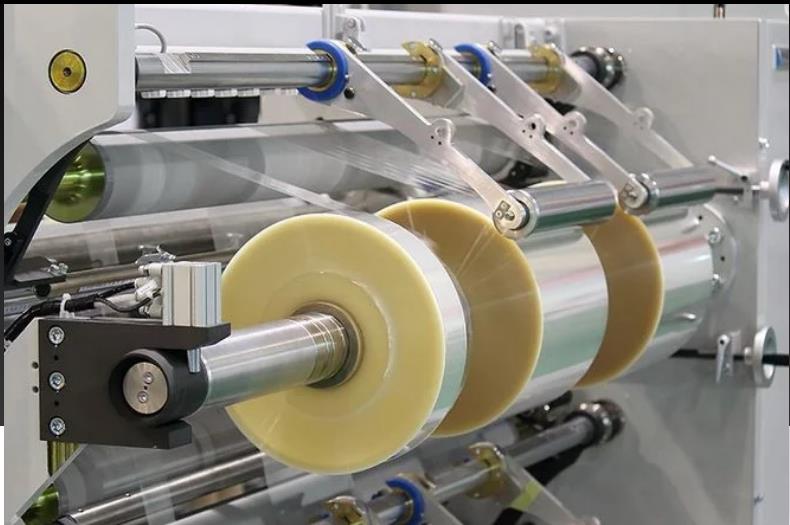
Why Need Refitting Tension Control Systems
Retrofitting tension control systems is necessary to address various challenges and unlock benefits that improve the efficiency, performance, and adaptability of production processes.
- Enhance Performance and Precision: Outdated systems may lack the precision required for modern manufacturing demands. Retrofitting with advanced tension control systems ensures accurate tension regulation, critical for maintaining quality in materials like paper, textiles, or advanced composites.
- Adapt to New Materials: Modern production lines often handle new materials with tension control. Retrofitting enables the integration of advanced control technologies to accommodate these materials without compromising efficiency.
- Improve Reliability: Aging systems are prone to frequent breakdowns and inconsistencies. Upgrading components or adding modern sensors and controllers can significantly reduce downtime and improve operational reliability.
- Increase Production Efficiency: Enhanced tension control reduces material waste, improves process stability, and allows higher production speeds. This translates to improved overall efficiency and cost savings.
- Integrate with Automation and Digitalization: Retrofitting allows older systems to integrate seamlessly with digital control systems, IoT-enabled monitoring, and automated workflows, improving process transparency and control.
- Cost-Effective Alternative to Replacement: Retrofitting is often more economical than replacing an entire system. It extends the lifespan of existing equipment while bringing it up to modern standards.
- Meet Evolving Industry Standards: As regulations and standards become stricter, retrofitting ensures compliance with safety, quality, and environmental requirements.
- Address Wear and Tear: Over time, mechanical and electronic components degrade. Retrofitting replaces or upgrades critical components to restore functionality and optimize performance.
- Custom Solutions for Specific Needs: Retrofitting offers the flexibility to customize tension control systems to suit specific production requirements, such as handling unique materials or addressing specific line configurations.
- Sustainability and Energy Efficiency: Advanced tension control systems are more energy-efficient, contributing to sustainability goals. Retrofitting helps in reducing the carbon footprint of production processes.
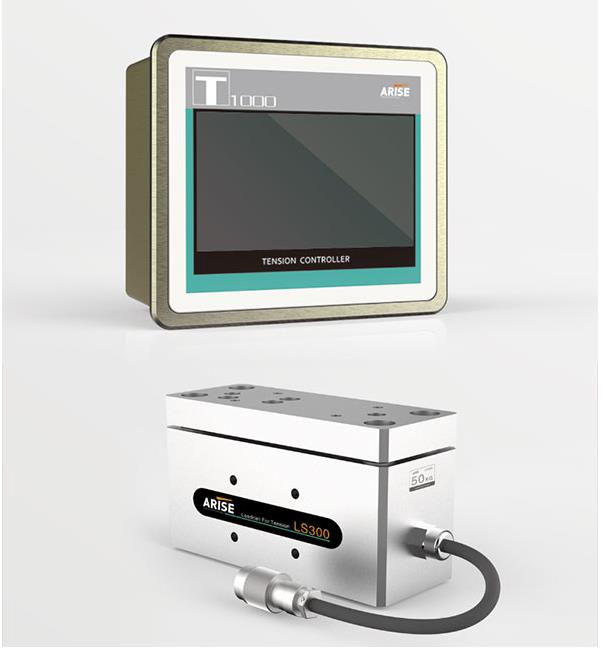
Key Retrofit Solutions for Upgrading Tension Control Systems
Upgrading tension control systems through retrofitting is an efficient approach to enhance precision, reliability, and adaptability without replacing the entire system. Below are the key retrofit solutions for upgrading tension control systems, focusing on the latest technologies and their applications.
1. Advanced Tension Sensors
Upgrade Focus: Replace older tension sensors with modern load cells, ultrasonic sensors, or torque sensors.
Benefits:
- Higher accuracy in measuring tension.
- Faster response times for real-time adjustments.
- Improved reliability, especially in harsh industrial environments.
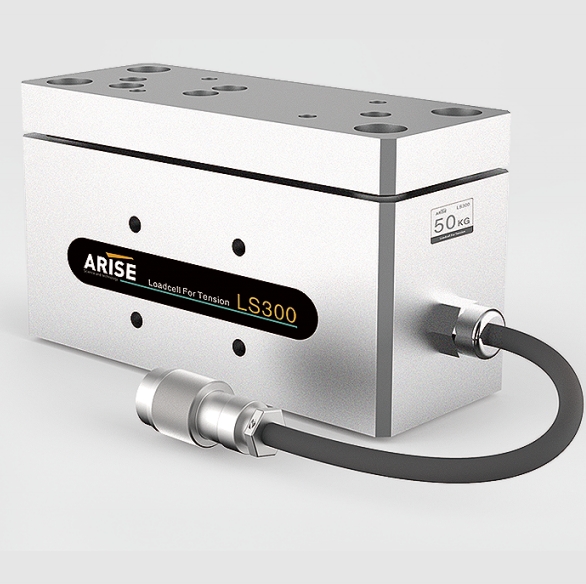
2. Digital Tension Controllers
Upgrade Focus: Transition from analog to automatic tension controllers.
Benefits:
- Programmable settings for multiple materials and processes.
- Enhanced control precision using adaptive algorithms.
- Seamless integration with automated systems for centralized monitoring.
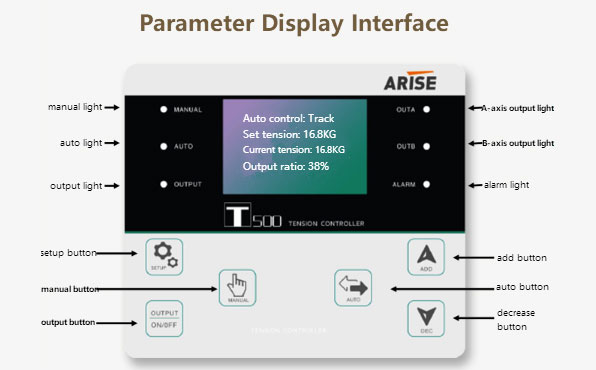
3. Variable Frequency Drives (VFDs)
Upgrade Focus: Integrate VFDs for motor control.
Benefits:
- Dynamic adjustment of motor speed and torque for consistent tension.
- Reduced energy consumption and improved system efficiency.
- Prolonged lifespan of mechanical components due to smoother operations.
4. Modern Brake Systems
Upgrade Focus: Replace traditional pneumatic or mechanical brakes with electromagnetic or servo-driven systems.
Benefits:
- Faster and more accurate tension adjustments.
- Reduced wear and maintenance requirements.
- Enhanced performance in high-speed or heavy-duty applications.
5. IoT-Enabled Systems
Upgrade Focus: Incorporate IoT devices for data-driven operations.
Benefits:
- Real-time monitoring and control through connected devices.
- Predictive maintenance using advanced analytics.
- Improved decision-making via historical data trends.
6. Advanced Software Solutions
Upgrade Focus: Install updated software for system optimization.
Benefits:
- Enhanced process automation and control.
- User-friendly interfaces for simplified operation.
- Integration with production management systems for end-to-end process visibility.
7. Feedback and Closed-Loop Control Systems
Upgrade Focus: Shift from open-loop to closed-loop tension control systems.
Benefits:
- Real-time corrections based on tension deviations.
- Minimized variations in tension for better product quality.
- Increased adaptability to changes in material properties or process conditions.
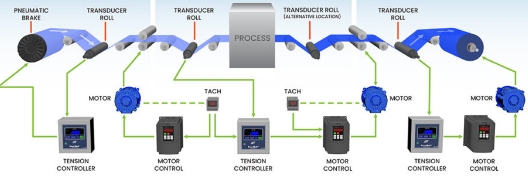
8. Integration with Industry 4.0 Technologies
Upgrade Focus: Connect retrofitted systems with smart factory solutions.
Benefits:
- Enhanced interoperability with other automated systems.
- Centralized control and diagnostics across the production line.
- Future-proofing to accommodate further technological advancements.
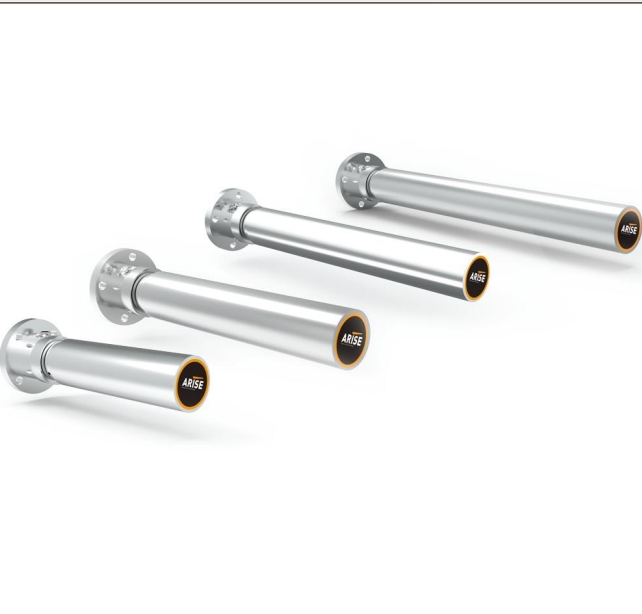
Steps to Implement a Successful Retrofit for Upgrading Tension Control Systems
This chart provides a systematic approach to implementing a retrofit, ensuring efficiency and reliability while minimizing potential risks during the upgrade process.
Step | Description | Key Considerations |
1. System Assessment | Evaluate the existing tension control system to identify inefficiencies and areas for improvement. | Conduct a thorough inspection of mechanical, electrical, and software components. |
2. Define Objectives | Establish clear goals for the retrofit, such as improving precision, reducing downtime, or enhancing integration. | Align objectives with operational requirements and future scalability needs. |
3. Component Selection | Choose suitable components like advanced sensors, digital controllers, and VFDs. | Ensure compatibility with the existing system and select reliable, high-quality parts from trusted suppliers. |
4. Develop a Retrofit Plan | Create a detailed plan outlining the installation process, timelines, and budget. | Consider potential disruptions to production and schedule retrofitting during downtime or low-demand periods. |
5. Installation | Install the selected components and integrate them with the existing system. | Follow manufacturer guidelines and industry standards to ensure proper installation and safety compliance. |
6. System Integration | Connect the retrofitted components to control and automation systems, including IoT platforms if applicable. | Test integration with existing software and communication protocols. |
7. Testing and Calibration | Perform rigorous testing to ensure optimal performance and precise tension control. | Verify the accuracy and responsiveness of the upgraded system under various operational conditions. |
8. Training | Train operators and maintenance teams on the upgraded system’s functionality and troubleshooting. | Provide clear documentation and hands-on demonstrations for effective knowledge transfer. |
9. Monitoring and Feedback | Monitor the system’s performance post-retrofit and gather feedback for further optimization. | Use real-time data and analytics to fine-tune settings and ensure long-term reliability. |
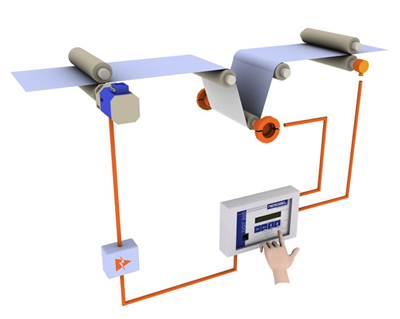
In summary, retrofitting tension control systems is a cost-effective solution for industries seeking to enhance precision, reliability, and efficiency. Through adopting advanced technologies such as modern sensors, digital tension controllers, advanced software, IoT integration, etc, manufacturers can transform their existing systems into high-performing assets. These upgrades not only improve operational performance but also align with sustainability objectives and long-term competitiveness.