How to Prevent Tension Variations in Web Handling
Tension control in web handling is critical for ensuring smooth operations in various industries such as printing, paper manufacturing, packaging, textiles, etc. When tension fluctuations occur in the web, it can lead to material defects, inefficiencies, and even machine malfunctions. Therefore, it is essential to understand how to prevent tension variations in web handling to maintain optimal performance and quality in the production process.
Table of Contents
The Importance of Consistent Tension in Web Handling
In web handling, tension refers to the force exerted on a continuous sheet or roll of material as it moves through a series of processing units, including rollers, web guide systems, and printing units. Maintaining consistent tension is crucial because fluctuations can cause material defects such as wrinkles, breaks, uneven printing, and misalignment. These issues not only degrade the quality of the product but can also lead to machine downtime and increased operational costs.
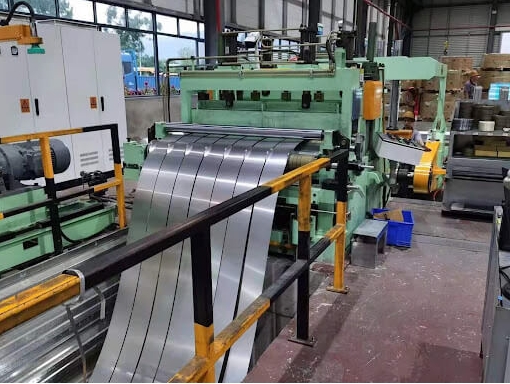
Key Causes of Tension Variations in Web Handling
Cause | Description | Impact |
Material Characteristics | Variations in thickness, elasticity, or stretchability. | Uneven stretching, material deformation, breakage. |
Roller Misalignment | Misaligned rollers cause uneven web movement. | Wrinkles, tracking issues, misregistration in printing. |
Speed Variations | Mismatched speeds between feed and take-up rolls. | Slack or excessive tension, web breaks, inconsistent print quality. |
Inadequate Tension Control Systems | Poorly calibrated or outdated tension control systems. | Over-tensioning or under-tensioning, production downtime. |
Roller Slippage | Lack of proper grip between rollers and web material. | Slipping, inconsistent web movement, misfeeding. |
Environmental Factors | Changes in temperature and humidity affect material properties. | Dimensional changes, curling, tension instability. |
Improper Web Path Design | Sharp turns, excessive friction, or sudden directional changes. | Uneven tension distribution, material distortion. |
Machine Wear and Tear | Aging rollers, belts, motors, or sensors. | Reduced precision, increased downtime, frequent recalibrations. |
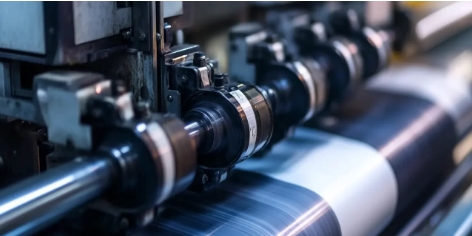
Strategies for Preventing Tension Variations in Web Handling
1. Implement Closed-Loop Tension Control Systems
Closed-loop tension control systems are one of the most reliable methods for maintaining consistent tension. These systems use real-time feedback from tension sensors, load cells, or dancer rolls to monitor tension levels continuously. The tension control system automatically adjusts the drive motors or brakes to maintain a consistent tension, reducing the risk of over-tensioning or under-tensioning. By making real-time adjustments, the system ensures that tension stays within the desired range, even when variables change during production.
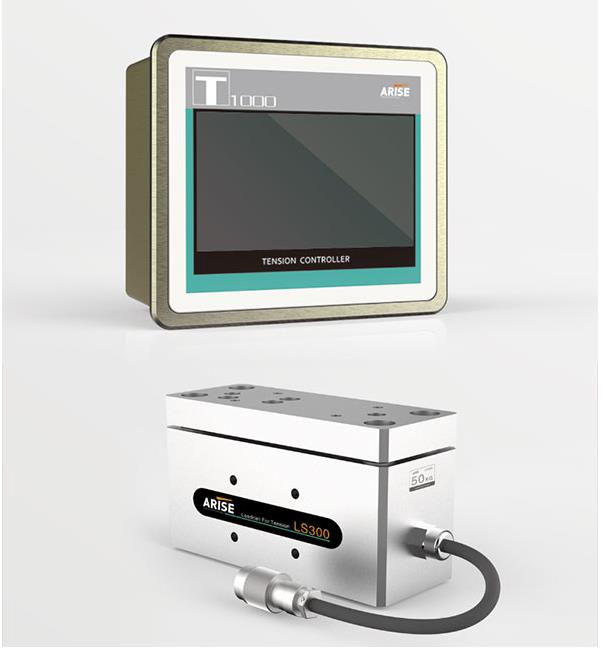
2. Use Dancer Rolls
Dancer rolls are movable rollers placed in the web handling path to provide mechanical feedback that helps regulate tension. As the web moves through the system, the dancer rolls adjust their position based on the web’s tension, which allows for dynamic adjustments to the tension levels. These rolls act as a buffer and help prevent tension variations by providing continuous feedback to the control system, ensuring that the web stays under the correct tension at all times.
3. Ensure Proper Roller Alignment
Misalignment of rollers is one of the most common causes of tension variations. When rollers are not properly aligned, the web can shift, causing uneven tension. Regularly inspecting and adjusting roller alignment is essential for maintaining consistent tension. Additionally, optimizing the web path by minimizing sharp turns and friction can prevent tension fluctuations caused by misalignment.
4. Maintain Speed Synchronization
In web handling systems, it is crucial for the feed and take-up rolls to operate at synchronized speeds. If the speed of the material feed does not match the machine speed, it can cause tension fluctuations. To avoid this, variable frequency drives (VFDs) can be used to dynamically adjust the speed of the rollers to maintain synchronization. This ensures that the web moves consistently through the system without tension variations caused by speed mismatches.
5. Use High-quality Anti-slip Rollers
Slipping rollers can lead to tension variations, especially if they do not provide enough grip on the web. To prevent this, it is important to use high-quality rollers that feature anti-slip coatings or materials. These rollers ensure a secure grip on the web, reducing the risk of slippage and maintaining consistent tension. Regular maintenance and timely replacement of worn-out rollers are also essential for ensuring optimal performance.
6. Pre-Treat or Condition Materials
Material properties, such as thickness, stretchability, and moisture content, can affect tension stability. To prevent tension variations caused by inconsistent material behavior, pre-treating or conditioning the material before it enters the web handling system can help. Pre-stretching the material can reduce its tendency to stretch unevenly during processing, while maintaining controlled environmental conditions (e.g., humidity and temperature) can minimize moisture-related variations in materials, such as paper and textiles.
7. Regular Maintenance and Calibration
Routine maintenance and calibration of tension control systems, rollers, sensors, and other equipment are essential to preventing tension variations. Over time, components such as sensors can become miscalibrated, and rollers may wear out, affecting the overall tension stability. Regular inspections and calibrations ensure that all equipment operates as expected and helps identify potential issues before they result in tension fluctuations. Utilizing data logging systems can also help monitor trends in tension, providing valuable information to make necessary adjustments.
8. Monitor and Adjust Environmental Factors
Environmental conditions, such as temperature and humidity, can influence the material’s behavior and contribute to tension variations. For example, some materials, like paper or textiles, may expand or contract due to changes in moisture levels. Monitoring and controlling the environmental conditions in the production area can help minimize these effects. Installing climate control systems can prevent excessive moisture absorption, ensuring that the material’s properties remain consistent during processing.
9. Adopt Tension Sensors for Real-Time Feedback
Tension sensors are invaluable tools for monitoring and adjusting tension in real time. These sensors can be installed at various points along the web handling path to provide constant feedback on the tension levels. By using load cells, capacitance-based sensors, or optical sensors, manufacturers can obtain precise readings and make timely adjustments to the tension. Integrating these sensors with automated control systems ensures that any tension variations are corrected immediately, preventing defects and inefficiencies.
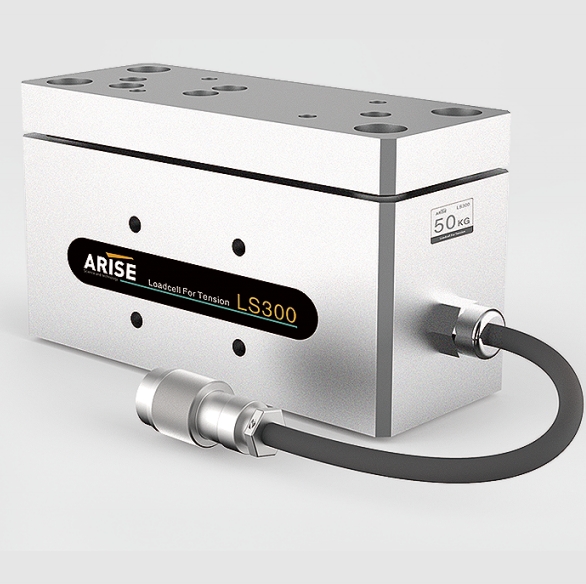
10. Optimize Web Path Design
The design of the web path plays a crucial role in tension control. Minimizing sharp turns, reducing friction, and ensuring smooth transitions from one roller to another help to maintain consistent tension. A well-designed web path prevents unnecessary stress on the material and reduces the risk of tension fluctuations. Regularly reviewing and optimizing the layout of the web path can lead to better tension management and improved overall system performance.
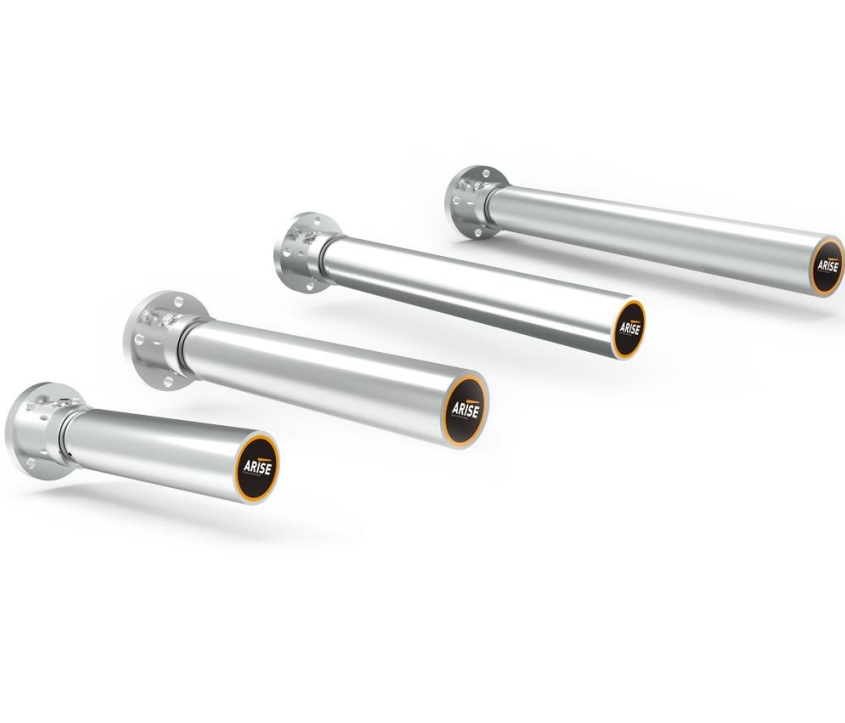
Summary
Through understanding the causes of tension variations and implementing strategies such as automated tension control systems, proper roller alignment, speed synchronization, regular maintenance, etc, manufacturers can maintain consistent tension throughout the web handling process. These measures help prevent material defects, reduce downtime and enhance overall production efficiency, leading to a smoother and more reliable web processing operation.