How to Optimize Web Tension Control with Web Guide Systems
Table of Contents
Web tension, the force applied to a web as it moves through a process line, must be maintained within a specific range to avoid defects like wrinkling, tearing, or misalignment. Achieving consistent tension across the entire width of the web is challenging, especially at high speeds or with delicate materials. This is where web guide systems play an essential role in optimizing web tension control.
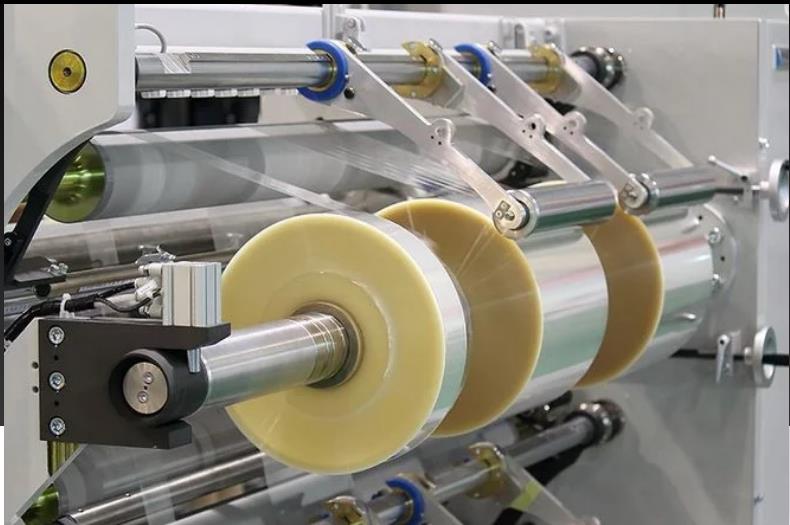
Understanding Web Tension Control and Its Importance
Web tension control is vital in processes involving continuous rolls of materials like paper, film, foil, or textiles. Proper tension ensures:
- Smooth transportation of the material through various process stages.
- Prevention of issues like web breakage, edge weave, or improper alignment.
- Consistency in product quality across all production runs.
- Reduction in downtime and material waste, leading to lower operational costs.
Uncontrolled or fluctuating web tension can result in costly defects, necessitating the use of sophisticated control mechanisms such as web guide systems to regulate tension effectively.
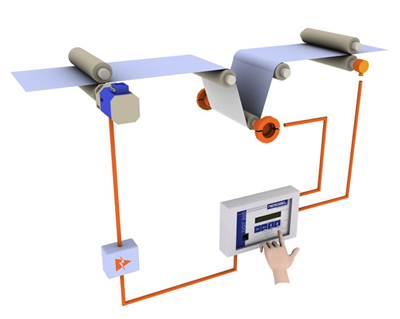
Role of Web Guide Systems in Web Tension Optimization
Web guiding systems are engineered solutions that automatically align the web as it moves through the production line. These systems are designed to monitor the position of the web and make real-time adjustments to keep it centered and tensioned correctly.
Key Components of Web Guide Systems
This chart outlines the essential components of web guide systems and their respective functions, providing a quick reference for understanding how each part contributes to web tension control.
Component | Function | Example Technology |
Sensors | Detect the position and movement of the web, providing real-time feedback. | Ultrasonic, Infrared, Optical, Laser |
Controller | Processes sensor data and sends corrective signals to the actuators. | PLC (Programmable Logic Controller) |
Actuators | Physically adjust the guide rollers or frames to correct web alignment. | Servo Motors, Pneumatic Actuators |
Guide Rollers | Support the material and guide its movement along the production line. | Aluminum, Rubber-Coated, Stainless Steel |
Feedback Systems | Provides information on web tension and performance for real-time adjustment. | Load Cells, Tension Sensors |
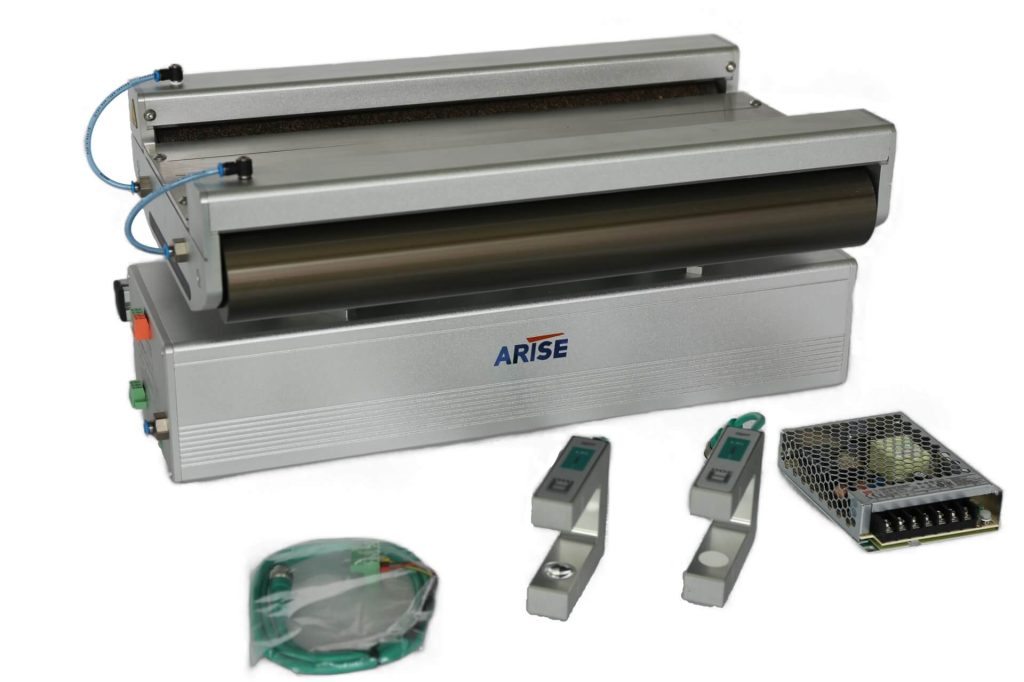
Benefits of Web Guide Systems for Web Tension Control
This chart presents the key benefits of using web guide systems for optimizing web tension control, leading to improved efficiency, quality, and cost savings.
Benefit | Description | Outcome |
Improved Tension Stability | Maintains consistent tension by correcting web alignment in real time. | Reduces the risk of material stretch, slack, or breakage. |
Enhanced Product Quality | Ensures precise web positioning, preventing wrinkles, tears, and misalignment. | Results in higher-quality finished products. |
Increased Production Efficiency | Automates tension control adjustments, enabling faster production speeds with fewer disruptions. | Boosts throughput and reduces downtime. |
Reduced Material Waste | Minimizes errors such as misregistration and improper alignment, lowering defective output. | Decreases material costs and rework due to fewer defects. |
Less Operator Intervention | Automatically controls and adjusts web tension, reducing the need for manual adjustments. | Enhances operational efficiency and reduces human error. |
Compatibility with Various Materials | Adapts to different material types, including delicate or high-speed webs, without compromising tension. | Ensures optimal tension control across diverse applications. |
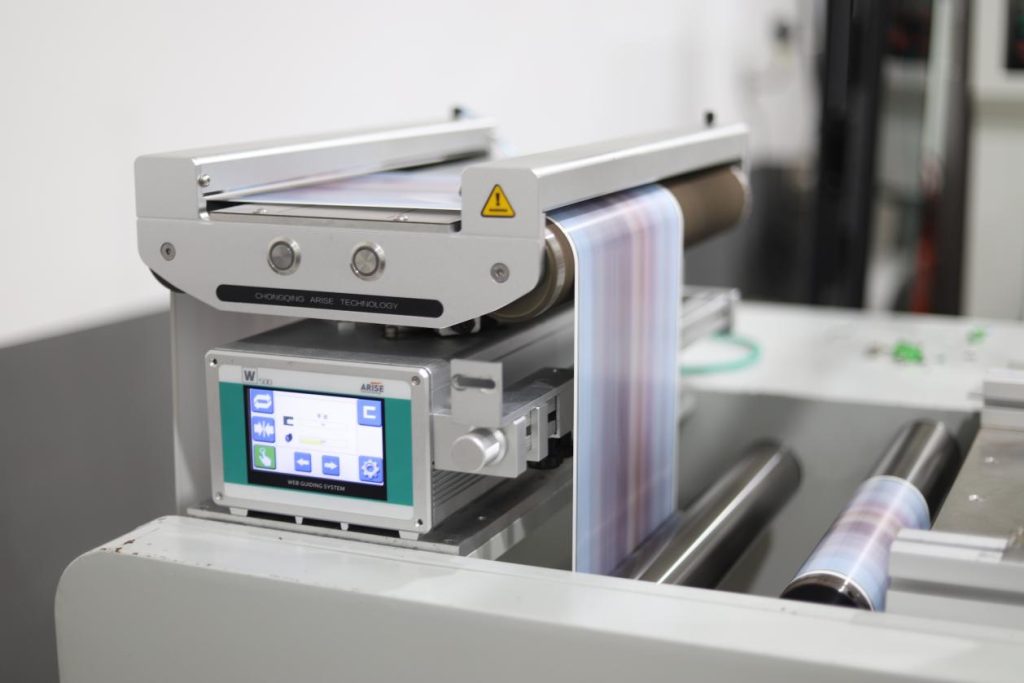
Best Practices for Optimizing Web Tension Control with Web Guide Systems
Implementing a web guide system is a proven method for improving web tension control. However, to get the best results, it is important to follow best practices that ensure the system operates efficiently and optimally.
1. Select the Appropriate Sensor Technology
Choosing the correct sensor technology is crucial for accurately detecting the web’s position. Different materials require different types of sensors to achieve reliable performance:
- Ultrasonic edge guide sensors: Ideal for non-reflective materials such as paper or opaque films.
- Infrared and optical sensors: Best suited for transparent or highly reflective materials.
- Laser sensors: Provide high precision for delicate or thin materials where slight misalignments can impact quality.
Matching the sensor to the material’s characteristics ensures accurate web guidance and optimal tension control.
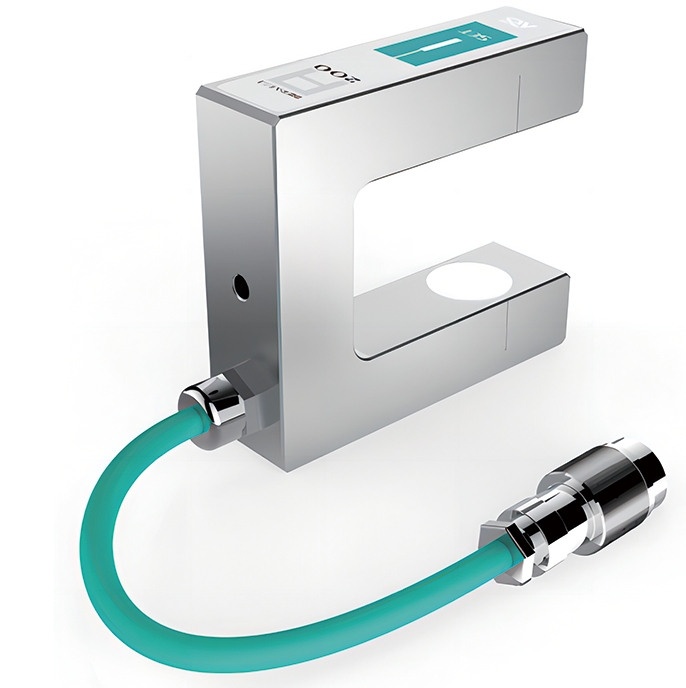
2. Adopt Automatic Tension Adjustment
Modern web guiding systems often feature automatic tension control, which continuously monitors and adjusts web tension in real-time. This capability is particularly valuable for high-speed production lines or multi-stage processes. Automatic tension adjustment eliminates the need for manual intervention, maintaining consistent tension across the entire material length.
Benefits include:
- Increased precision: Automated systems provide fast and accurate corrections to deviations, minimizing defects.
- Improved efficiency: Maintaining optimal tension ensures smoother material handling and faster throughput.
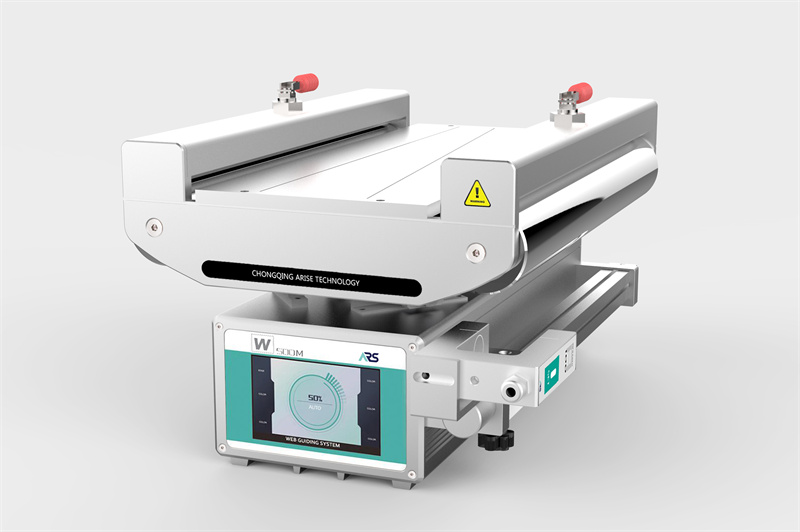
3. Integrate Digital and IoT Technologies
Incorporating digital technologies, such as IoT (Internet of Things) integration, into web guide systems allows for real-time data monitoring and analysis.
- Optimize settings: Use data insights to fine-tune the system for specific materials or production conditions.
- Predict maintenance needs: Analytics can identify patterns in system performance, allowing for predictive maintenance and minimizing downtime.
- Enhance traceability: Track performance metrics throughout production to ensure consistency and quality.
Digital integration also enables the remote monitoring of web tension control systems, allowing operators to make adjustments from anywhere.
4. Maintain Proper Roller Alignment
The alignment of guide rollers plays a key role in ensuring smooth web movement and accurate tension control. Misaligned rollers can introduce additional friction or drag, leading to tension imbalances that result in defects like wrinkling or tearing.
Best practices for roller alignment
- Regular inspections: Frequently check the alignment of rollers to prevent uneven tension distribution.
- Correct roller positioning: Ensure that the rollers are placed strategically to support the web and prevent it from veering off course.
5. Calibrate Sensors and Actuators Regularly
To ensure the web guide system continues to operate at peak performance, regular calibration of the sensors and actuators is essential. Calibration ensures that the sensors detect the web’s position accurately and that the actuators respond correctly to any misalignment.
- Periodic recalibration: Set up a maintenance schedule for recalibration, especially in environments where conditions may change frequently (e.g., temperature fluctuations or varying material thickness).
- Sensor cleanliness: Ensure that sensors are kept clean to avoid signal interference or misreadings due to dust, debris, or material residues.
6. Employ Advanced Control Algorithms
Web guide control systems often come equipped with advanced control algorithms that optimize web tension control by learning from the material’s behavior and production conditions. These adaptive algorithms anticipate tension fluctuations and make adjustments proactively.
Benefits
- Improved adaptability: The system can automatically adjust to variations in material thickness or tension, ensuring a consistent production quality.
- Enhanced precision: Advanced algorithms allow for finer adjustments, particularly in high-speed or multi-material processes.
7. Choose the Right Web Guide Configuration
Different applications and materials require different web guide system configurations. Consider the following when choosing your system:
- Lateral guiding systems: Effective for centering and edge guiding, suitable for narrow webs or materials requiring high precision.
- Pivoting frame guides: Ideal for high-speed lines or wide materials where more significant corrections may be necessary.
- Steering guides: Used in applications where correcting skewed webs is essential to prevent misalignment across the entire production run.
Selecting the proper configuration will ensure the system fits the production process and enhances web tension control.
8. Train Operators Thoroughly
Well-trained operators are critical for optimizing web tension control. Ensure that staff are familiar with the web guide system’s features and how to operate it effectively.
- Troubleshooting: Train operators to quickly identify and resolve issues such as sensor misalignment, calibration problems, or roller adjustments.
- Regular monitoring: Encourage operators to monitor web tension throughout the production run to catch potential issues early.
- Understanding system capabilities: Operators should be aware of the full capabilities of the system, including advanced features like automatic tension adjustment or data analytics integration.
9. Implement Predictive Maintenance Practices
Web guiding systems are mechanical devices that require regular maintenance to ensure long-term performance. By implementing predictive maintenance strategies, manufacturers can prevent unexpected breakdowns or malfunctions.
- Use data analytics: Monitor system performance over time to predict when components like sensors, actuators, or guide rollers may need maintenance or replacement.
- Schedule preventive maintenance: Regular maintenance tasks, such as cleaning sensors or lubricating moving parts, should be scheduled to prevent gradual wear from affecting performance.
10. Monitor and Adjust System Settings Based on Material Behavior
Different materials react differently under tension, and their behavior can change throughout the production process. Monitoring how each material responds to the web guide system and adjusting the settings accordingly can optimize tension control.
- Material-specific settings: Use historical data to set the ideal tension levels for each type of material processed.
- Adaptive control: Utilize adaptive algorithms that adjust the tension based on the material’s response in real time.
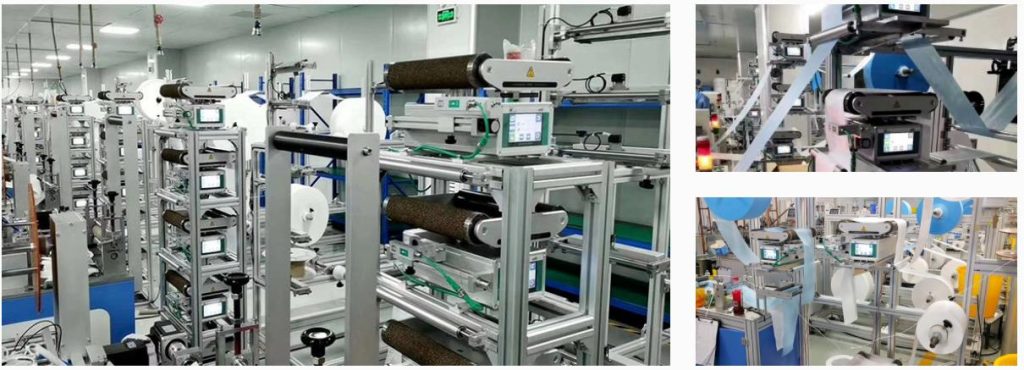
In summary, optimizing web tension control with web guide systems is critical for improving efficiency, reducing waste and enhancing product quality in any industry that involves continuous material rolls. Adhering the best practices and adopting advanced innovative technologies, companies can maximize the performance of their web guiding control systems and gain a competitive edge in their respective industries.