How to Optimize Tension Control in Web Handling Applications
One of the key challenges in web handling is maintaining proper tension throughout the procedure. Tension control is critical in avoiding issues such as wrinkles, creases, tears, and misalignment, all of which can jeopardize the final product’s integrity. This article delves into the significance of tension control in web handling and explores various techniques and technologies employed to achieve optimal tension control.
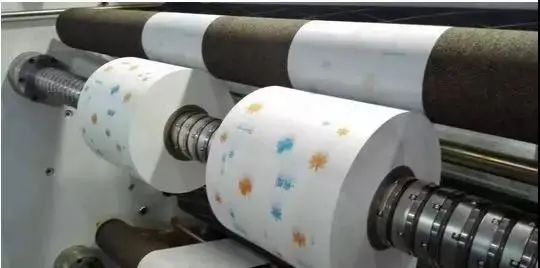
The Importance of Tension Control in Web Handling
The Definition of Tension Control
Tension control refers to the ability to modulate the force exerted to a web of material as it passes through several phases of production. It entails maintaining a constant amount of tension to keep the web from sagging or being overly stretched. Proper tension management guarantees regular speed and alignment, which is essential for processes like as printing, coating, laminating, slitting, and winding.
Benefits of Effective Tension Control in Web Handling
Benefit | Description |
Consistent Product Quality | Maintains uniform tension throughout the web handling process, resulting in consistent product dimensions, surface finish, and quality. |
Reduced Material Waste | Minimizes material waste caused by wrinkles, tears, creases, or misalignment due to improper tension, leading to cost savings. |
Enhanced Process Reliability | Improves overall process reliability by preventing web breaks, snags, and other handling issues, reducing downtime and disruptions. |
Improved Productivity | Optimizes production efficiency by enabling higher line speeds, faster throughput, and smoother operation of web handling equipment. |
Extended Equipment Lifespan | Reduces wear and tear on equipment components such as rollers, bearings, and drives, resulting in longer service life and reduced maintenance. |
Enhanced Print and Coating Quality | Ensures uniform ink coverage, coating thickness, and adhesion, leading to improved print quality and surface finish of the final product. |
Enhanced Customer Satisfaction | Consistent product quality and reliability lead to increased customer satisfaction and loyalty, enhancing the reputation of the manufacturer. |
Compliance with Specifications | Enables adherence to tight tolerance requirements, specifications, and regulatory standards, ensuring product compliance and market acceptance. |
Flexibility in Material Handling | Facilitates handling of a wide range of materials, substrates, and thicknesses with varying tension requirements, enhancing process flexibility. |
Improved Safety | Minimizes safety risks associated with web breaks, snags, or handling issues, creating a safer working environment for operators and personnel. |
Factors Influence Tension Control in Web Handling
Understanding and addressing these factors are essential for achieving precise and reliable tension control in web handling systems.
Factor | Description |
Material Properties | Material characteristics such as elasticity, thickness, width, and surface friction affect how the material behaves under tension. |
Web Speed | Faster web speeds can increase tension due to inertia effects and require faster response times in tension control systems. |
Roll Diameter | Changes in roll diameter affect the amount of material being fed or wound, impacting tension levels in the web handling system. |
Web Tension Variations | Variations in tension caused by uneven winding, splices, or process fluctuations require precise tension control to maintain uniformity. |
Web Handling Equipment | The design and condition of rollers, guides, tension control devices, and drives play a significant role in controlling tension. |
Friction and Slip | Friction between the web and rollers, as well as slip between layers, can influence tension levels and require compensation mechanisms. |
Web Path Configuration | The layout of the web path, including the number and arrangement of rollers and guides, affects tension distribution and control. |
Environmental Conditions | Factors such as humidity, temperature, and air drafts can impact material properties and tension control accuracy. |
Machine Dynamics | Vibrations, machine alignment, and mechanical wear can introduce fluctuations in tension and affect control system performance. |
Control System Parameters | Control parameters such as gain, proportional, integral, and derivative values, as well as response times, impact tension control. |
Operator Skill and Training | The knowledge and expertise of operators in adjusting and maintaining tension control systems are crucial for optimal performance. |
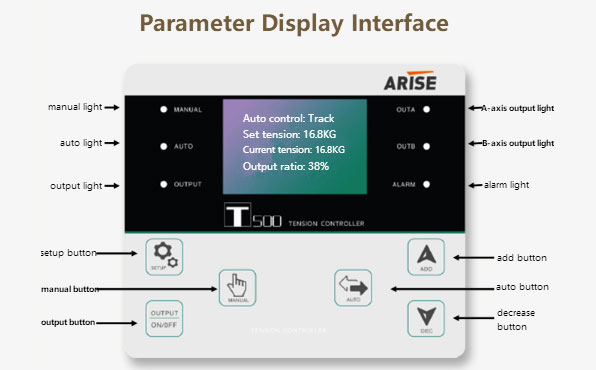
Techniques for Tension Control in Web Handling
Using these strategies, producers can successfully regulate tension in web handling systems, assuring constant product quality, production efficiency, and equipment reliability.
1. Manual Tension Control
Description: Operators manually adjust tension using mechanical devices such as brakes, clutches, or dancer rollers in response to visual observations or feedback from tension indicators.
Application: Manual tension control is appropriate for simple web handling processes that allow workers to quickly monitor and modify tension levels.
2. Closed-Loop Tension Control
Description: Automated systems use feedback from tension sensors strategically placed along the web path to automatically alter tension in real time.
Application: A closed-loop web tension controller is ideal for complicated web handling procedures that require exact tension regulation regardless of material qualities, speed, or ambient conditions.
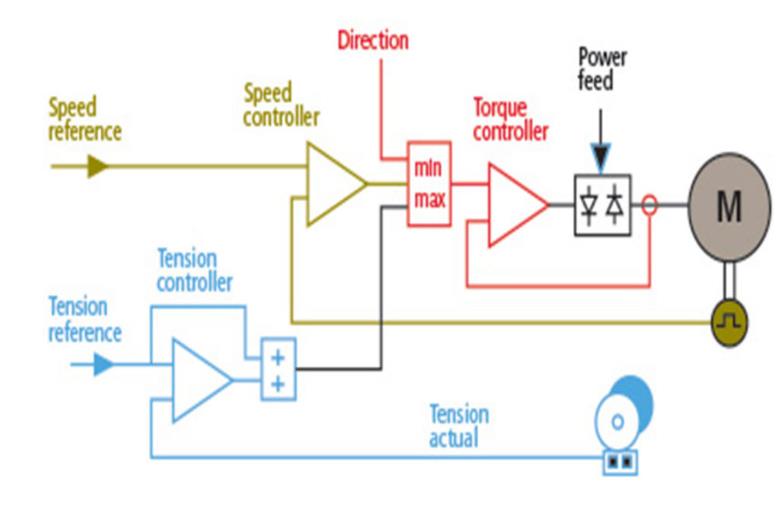
3. Tension Zones
Description: By dividing the web handling system into multiple tension zones, tension may be controlled independently at various phases of the process.
Application: Tension zones are beneficial when different sections of the web handling process require varying tension levels, such as in multi-stage printing or coating operations.
4. Load Cells and Tension Sensors
Description: Load cells and tension sensors measure the force exerted on the web, providing data for feedback control systems to make precise tension adjustments.
Application: Load cells and tension sensors are integral components of closed-loop tension control systems, offering accurate tension monitoring and adjustment capabilities.
5. Inertia Compensation
Description: Advanced tension control systems incorporate algorithms to compensate for the inertia of moving components, ensuring rapid response to changes in tension requirements.
Application: Inertia compensation is essential in high-speed web handling processes where quick adjustments are necessary to maintain consistent tension levels during acceleration or deceleration.
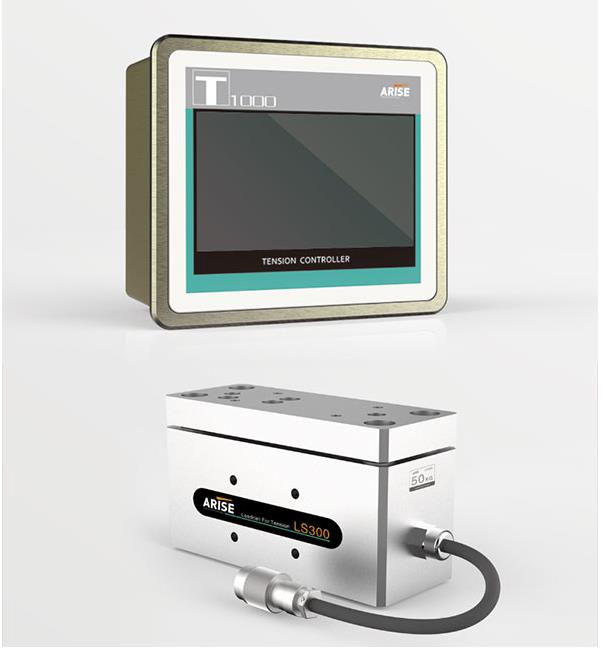
6. Web Accumulators
Description: Web accumulators temporarily store excess web material during tension fluctuations, releasing or absorbing material as needed to maintain consistent tension.
Application: Web accumulators are particularly useful in intermittent web handling processes or when tension variations occur due to equipment start-up, stoppage, or speed changes.
7. Pneumatic Tension Control
Description: Pneumatic tension control systems use air pressure to adjust tension, typically through pneumatic brakes or clutches.
Application: Pneumatic tension control is suitable for applications where precise tension regulation is required, such as in film or foil processing.
8. Electromagnetic Particle Brakes and Clutches
Description: To manage friction between rotating components, electromagnetic particle brakes and clutches alter tension by varying the strength of the magnetic field.
Application: Electromagnetic particle brakes and clutches provide accurate and responsive tension control, making them ideal for high-precision web handling applications such as printing and laminating.
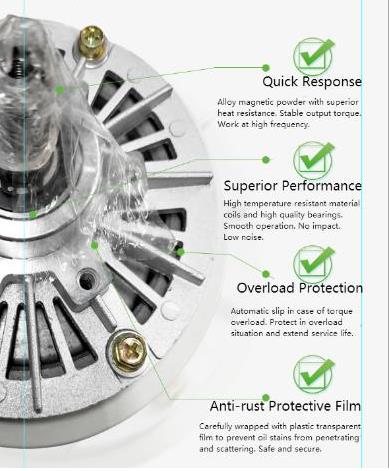
Conclusion
Tension control is a critical aspect of web handling in manufacturing processes, as it affects product quality, efficiency, and overall performance. Manufacturers can improve the performance of their web handling systems by applying effective tension control techniques and employing new technologies.