How to Maintain and Calibrate Web Guide Sensors Effectively
Web guide systems are essential in industries where materials such as paper, film, or fabric are processed in long, continuous webs. These systems use web guide sensors to detect the position of the web and ensure that it stays aligned during processing. However, like any other machinery, proper maintenance and calibration are crucial to ensure optimal performance and avoid costly downtime. This article provides a guide on how to maintain and calibrate web guide sensors effectively.
Table of Contents
Understanding Web Guide Sensors
Web guide sensors are used to detect the edge or center of a material web and relay this information to a controller. Based on the sensor data, the system can automatically adjust the position of the web, ensuring consistent alignment during the production process. These sensors typically operate using one of the following technologies:
- Ultrasonic edge sensors: These use sound waves to detect the edge position of the web.
- Infrared sensors: The sensors operate by emitting infrared light and detecting its reflection from the web.
- Laser sensors: These use laser beams to detect the position with high precision.
- Optical sensors: These sensors rely on light to detect edges or changes in the web’s position.
- Capacitive sensors: These measure the change in capacitance as the web moves.
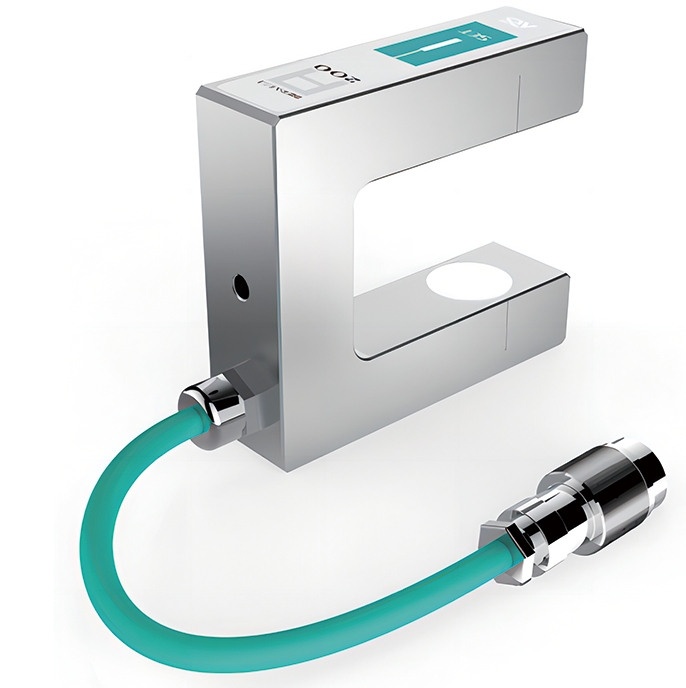
Each of these sensors requires regular maintenance and periodic calibration to ensure accurate readings and prevent misalignment that could disrupt the production process.
Key Steps in Maintaining Web Guide Sensors
1. Regular Cleaning
- Why it matters: Dust, debris, and ink residue can accumulate on sensor lenses or surfaces, which may distort readings and affect performance.
- How to do it: Use a soft, lint-free cloth or compressed air to gently clean the sensor’s lens and surrounding area. Avoid harsh chemicals that could damage the sensor. For ultrasonic and capacitive sensors, ensure that the areas around the transducer are clear of any obstructions.
2. Inspecting for Wear and Tear
- Why it matters: Regular use can cause wear on various parts of the sensor and web guide system, such as wires, housings, and connectors.
- How to do it: Routinely inspect the sensor and all associated wiring and connectors for any visible damage, such as cracks, frays, or signs of corrosion. Replace any worn or damaged components promptly to maintain sensor accuracy.
3. Ensuring Proper Alignment
- Why it matters: If the sensor is misaligned, it may fail to detect the web position accurately, leading to misfeeds and misalignment of the web.
- How to do it: Check the sensor alignment regularly and adjust it to ensure it is positioned properly relative to the web. This should be done whenever the web guide system is moved, or the material type changes. Follow the manufacturer’s guidelines to ensure proper sensor placement.
4. Testing Sensor Functionality
- Why it matters: Over time, sensors may lose sensitivity or malfunction, leading to inaccurate readings and operational inefficiencies.
- How to do it: Perform functionality checks to verify that the sensor is providing the correct readings. This can be done by manually adjusting the web’s position and observing the sensor’s response. Many systems offer diagnostic tools that can help detect malfunctioning sensors.
5. Checking Power Supply
- Why it matters: A steady power supply is critical for sensor functionality. Voltage fluctuations can affect the sensor’s readings.
- How to do it: Regularly monitor the power supply to ensure that it is stable and within the recommended range for the sensor. Check for any loose connections or potential issues with the power source.
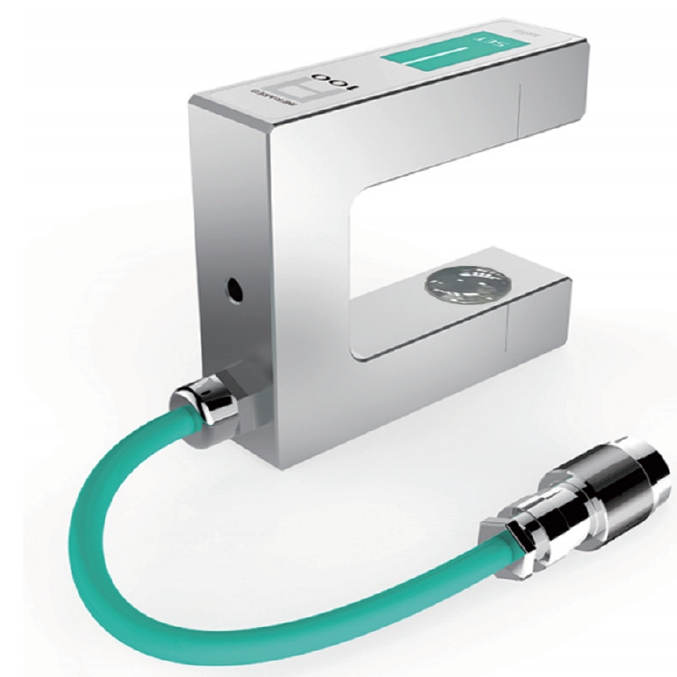
A Step-by-step Guide for Calibrating Web Guide Sensors
Calibrating web guide sensors is crucial to ensure that the web guiding sensor detects the web position accurately, leading to precise adjustments in web alignment system. The process of calibration involves several steps that help maintain the optimal performance of the system.
1. Preparation and Inspection
Before starting the calibration, it’s important to prepare the system and inspect the sensor. Begin by ensuring that the web guide system is properly installed and that the sensor is securely mounted. Inspect the sensor for any visible dirt, dust, or debris that could obstruct its functionality. Clean the sensor if necessary using compressed air or a soft, lint-free cloth. Additionally, ensure the power supply to the sensor is stable and functioning correctly. Check for any loose connections or issues with the voltage, as these can impact sensor performance.
2. Aligning the Sensor
Proper alignment is crucial for accurate calibration. The sensor needs to be positioned correctly to detect the edge or center of the web material. Make sure there are no obstructions in the sensor’s line of sight, as this could interfere with its ability to monitor the web’s position. The sensor should be positioned according to the web’s specific requirements, and its alignment should be checked periodically to ensure that it remains in the correct position.
3. Setting the Reference Point
One of the first steps in calibration is defining the reference or zero point. This is the position from which all measurements will be taken. Typically, the reference point is set to the center or edge of the web, depending on the application. This reference point serves as the baseline for the sensor’s readings. Calibration software or the control panel of the web guide system can be used to initiate the process of defining this zero point. The sensor will then measure deviations from this reference point, allowing the system to make the necessary adjustments to maintain web alignment.
4. Adjusting Sensor Sensitivity
The next step is to fine-tune the sensitivity of the sensor. Different materials require different levels of sensitivity. For example, a thick or opaque material may require the sensor to be more sensitive, while a thin, transparent material may need less sensitivity. By adjusting the sensitivity, the sensor can more accurately detect shifts in the web’s position. This step often involves some testing—move the web through the system and observe how the sensor reacts to changes in position. If the sensor doesn’t detect small shifts, it may be necessary to increase the sensitivity.
5. Performing Functional Testing
Once the sensor has been calibrated and sensitivity has been adjusted, it’s time to perform functional testing. This involves moving the web through the system while monitoring how the sensor responds to the changes in position. The goal is to verify that the sensor is accurately detecting the web’s position and making necessary adjustments to the web guide system. If discrepancies are found between the sensor readings and the actual web position, further adjustments may be needed.
6. Environmental Adjustments
Environmental factors, such as temperature, humidity, or dust, can affect the sensor’s performance. If these factors are present in the operating environment, recalibration may be required more frequently to account for changes in the sensor’s behavior. In some cases, it might be necessary to adjust the sensor’s settings to compensate for environmental influences. If the material type changes—such as switching from a thin film to a thicker material—recalibration is also necessary to maintain accurate readings.
7. Routine Calibration and Monitoring
Even after calibration, it’s essential to monitor the sensor’s performance regularly. Web guide sensors may experience drift over time due to wear and environmental changes. For this reason, routine calibration should be scheduled at regular intervals. Depending on the operational environment, this could be monthly, quarterly, or based on usage patterns. Many modern systems come with diagnostic software that helps monitor sensor performance and identify when recalibration is needed.
8. Documentation of Calibration Settings
To ensure consistency and track any changes, it’s important to document all calibration settings and adjustments. Keep a log that records the calibration parameters used and any environmental factors that may have impacted the process. This information can be valuable when troubleshooting future issues or comparing past calibrations to identify trends or changes in system performance.
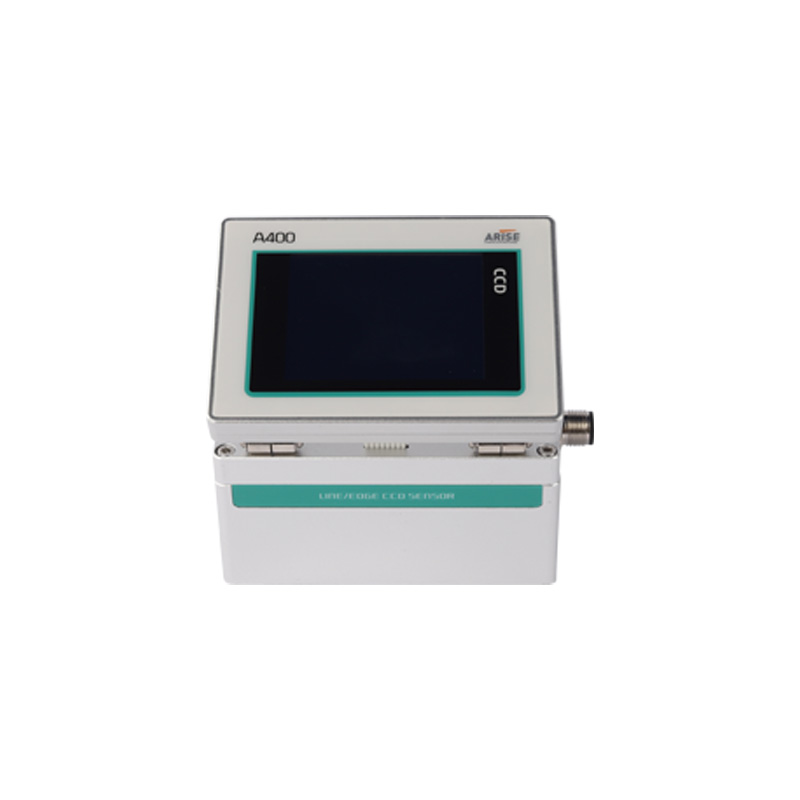
Troubleshooting Common Issues in Web Guide Sensors
This chart provides an overview of common issues with sensors and steps to resolve them to maintain accurate and reliable performance in web guide sensors.
Issue | Potential Cause | Solution |
Misalignment of Web | Incorrect sensor alignment or calibration | Recheck and adjust the sensor’s alignment according to the web’s position. |
Erratic or Inconsistent Sensor Readings | Dust, debris, or ink residue on the sensor’s lens or surface | Clean the sensor with a soft, lint-free cloth or compressed air to remove dirt or residue. |
Web Tracking Loss | Miscalibrated sensor, or obstruction in the sensor’s line of sight | Recalibrate the sensor and ensure there are no obstructions near the sensor or web. |
Inaccurate Web Position Detection | Faulty sensor or sensitivity issues | Test the sensor’s functionality using a known reference point and adjust sensitivity if necessary. |
Power Supply Issues | Voltage fluctuations or unstable power source | Ensure stable and consistent power to the sensor, checking for loose connections or voltage irregularities. |
Frequent Sensor Drift | Mechanical wear or environmental factors (e.g., temperature, humidity) | Recalibrate the sensor more frequently, especially in environments with fluctuating conditions. |
Overheating or Malfunctioning | Sensor hardware failure or excessive heat | Inspect the sensor for overheating or visible damage, and replace any malfunctioning components. |
Incorrect Readings Due to Material Change | The sensor may not be adjusted for different materials or web types | Recalibrate the sensor according to the new material’s characteristics (e.g., transparency, thickness). |
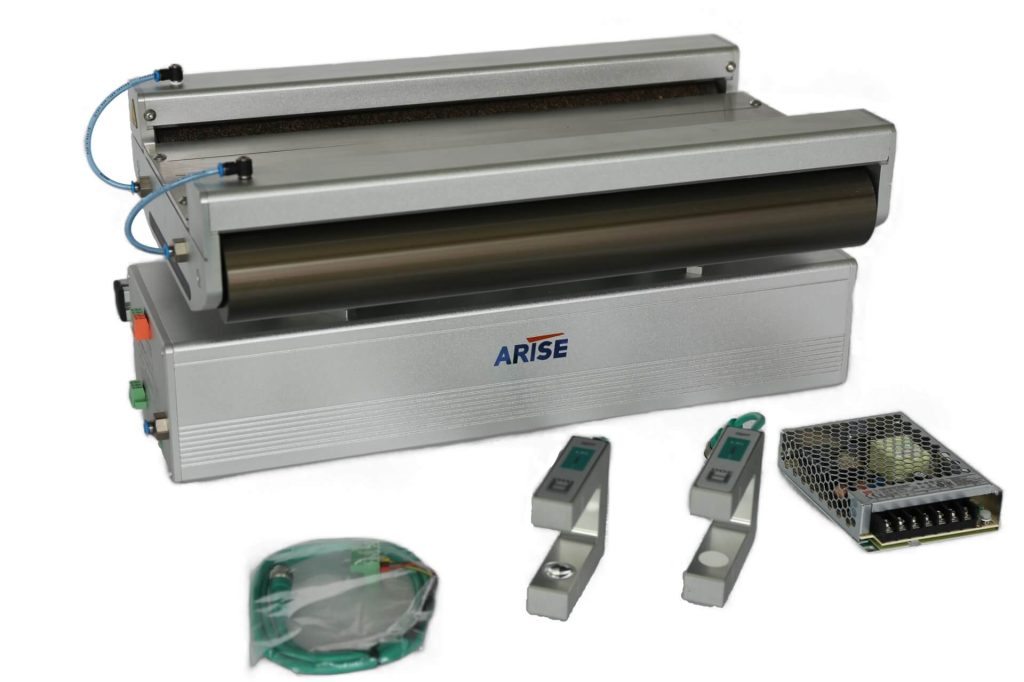
Final Thoughts
Maintaining and calibrating web guide sensors is essential to ensuring the accuracy and efficiency of web processing operations. Through performing regular cleaning, inspecting for wear, aligning the sensors, conducting periodic calibrations,etc, you can extend the lifespan of the web guiding sensors, maintaining optimal performance and improving the quality of your end products.