How to Maintain and Calibrate Tension Control Systems Effectively
Tension control systems manage the tension of materials like paper, film, foil, textiles, and wire during winding, unwinding, or intermediate processing, ensuring product consistency, quality, and efficiency. For these systems to function accurately and reliably, regular maintenance and precise calibration are essential. This article explores the importance, methods, and best practices for maintaining and calibrating tension control systems.
The Importance of Maintenance and Calibration for Tension Control Systems
- Ensuring Consistent Product Quality
One of the primary reasons maintenance and calibration are so critical is their direct impact on product consistency. Variations in tension, even by a small margin, can lead to stretching, wrinkling, or tearing of materials. In precision-driven industries such as flexible packaging or electronics, such inconsistencies can result in defective products or complete batch rejections. A well-maintained and correctly calibrated system delivers stable tension control, ensuring that each roll or sheet produced meets exacting standards.
- Minimizing Downtime and Operational Disruptions
Unplanned machine stoppages are costly and disruptive, particularly in high-speed or continuous production environments. Often, these issues stem from neglected wear and tear on mechanical components or from sensor inaccuracies that have gone unchecked. Routine maintenance helps identify and address early signs of mechanical failure, such as deteriorating brakes, misaligned rollers, or loose couplings. In parallel, calibration ensures that tension readings remain accurate, enabling the control system to respond appropriately under varying load conditions. Together, these efforts reduce the risk of unexpected failures and extend the service life of critical equipment.
- Enhancing Process Efficiency
When tension is precisely managed, production lines operate more smoothly. Materials flow without interruption, and machines work at their designed speed and capacity. Calibration plays a key role in aligning the system’s response with actual physical conditions, allowing for optimized automation and minimal manual intervention. Maintenance further supports this by keeping all components in peak condition, eliminating performance bottlenecks that arise from friction, contamination, or part degradation.
- Supporting Safety and Compliance
Beyond operational efficiency, well-maintained and calibrated tension control systems contribute to workplace safety and regulatory compliance. Malfunctions caused by excessive tension or sudden release of material can create hazards for operators and nearby equipment. Moreover, industries governed by quality assurance standards, such as ISO or GMP, often require documented maintenance and calibration records. Staying compliant not only helps avoid penalties but also builds confidence with customers and stakeholders in the reliability of your manufacturing process.
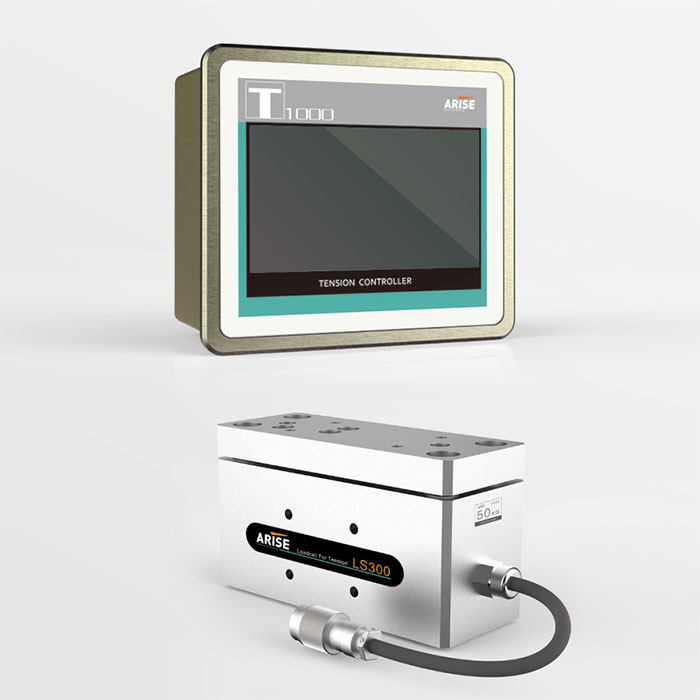
Key Steps in Maintaining Tension Control Systems
1. Visual and Physical Inspection of Mechanical Components
The first essential step in maintaining tension control systems involves regular visual and tactile inspection of the mechanical components. Rollers, brakes, motors, and dancer arms are constantly in motion and exposed to environmental and operational stress. Over time, these components may show signs of wear such as misalignment, surface degradation, or the accumulation of debris. Checking for looseness, abnormal vibrations, or surface scoring can help identify potential issues before they escalate. Maintaining proper lubrication and alignment during inspections is crucial to ensure smooth operation.
2. Monitoring Sensor and Load Cell Performance
Tension control systems rely heavily on the accurate performance of tension sensors. These components translate physical force into electronic signals, forming the backbone of feedback control. Over time, sensor output may drift due to aging, temperature changes, or mechanical strain. It is important to routinely monitor these outputs for inconsistencies or anomalies. Verifying that sensor cables are properly shielded, securely connected, and free from interference is also key to ensuring accurate data transmission within the control system.
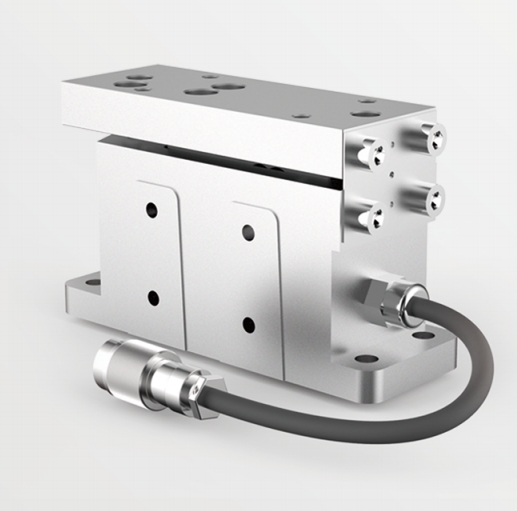
3. Evaluating the Electronic Control System
Another step in tension system maintenance includes evaluating the performance of the electronic controllers and drives. These units process sensor signals and issue commands to actuators and motors. Dust accumulation, overheating, or software glitches can cause delays or incorrect outputs. Periodic evaluation should include checking system response times, firmware integrity, and power supply stability. Ensuring the system’s electronic components remain within the manufacturer’s recommended parameters contributes significantly to control accuracy and system health.
4. Checking Brake and Clutch Functionality
In many systems, brakes and clutches are responsible for modulating tension by controlling the resistance applied to moving webs. Over time, friction surfaces wear down, leading to uneven or delayed responses. Ensuring that the braking force is consistent and within design specifications is necessary to maintain control reliability. Regular testing of torque response, as well as replacement of worn friction plates, helps to preserve smooth operation and avoids costly damage to material or equipment.
5. Validating System Integration and Communication
Tension control systems are typically part of larger automation setups. Ensuring that communication between programmable logic controllers (PLCs), human-machine interfaces (HMIs), and tension control units is functioning correctly is another key aspect of maintenance. Latency, data loss, or communication errors can disrupt control loops and reduce efficiency. Confirming the accuracy of parameter settings and verifying synchronization across all integrated components ensures that the entire system works harmoniously.
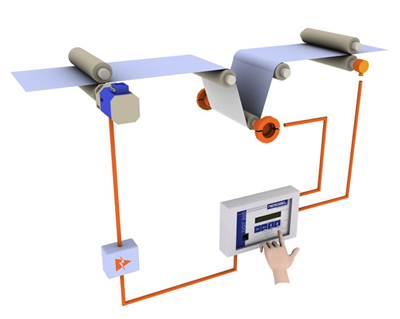
Steps for Effective Calibration of Tension Control Systems
1. Establishing a Baseline for Performance
Before initiating any calibration procedure, it is important to establish a performance baseline. This involves documenting the current tension levels under standard operating conditions and identifying any discrepancies between expected and actual outputs. The baseline provides a reference point for evaluating improvements post-calibration and helps in identifying drift in sensor readings or system inconsistencies. Baseline data also serve as a foundation for setting calibration goals and determining acceptable error margins.
2. Verifying and Preparing Load Cells and Sensors
Load cells and tension sensors are at the heart of any tension control system. Their performance must be verified before calibration can proceed. This involves checking for mechanical damage, confirming proper mounting, and inspecting wiring for wear or signal interference. If any sensor shows erratic behavior or deviation from expected response patterns, it should be repaired or replaced. Ensuring that the sensors are free from external disturbances and properly aligned prepares the system for accurate calibration.
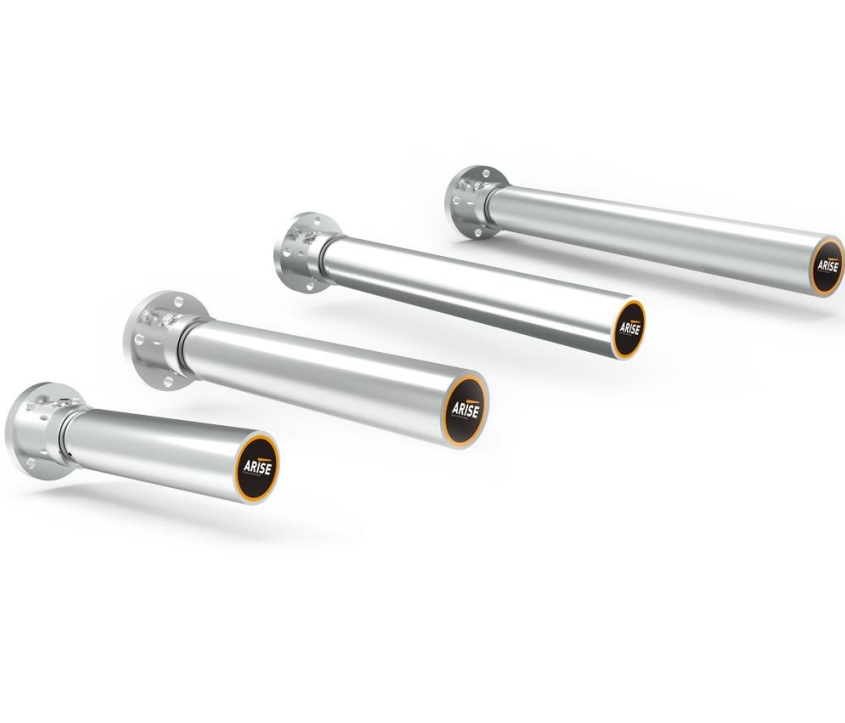
3. Applying Known Weights or Tension Forces
To begin the calibration process, a known weight or force is applied to the system in a controlled manner. This creates a reliable reference that can be compared to the system’s sensor output. The applied load must closely match the typical operational tension range to ensure meaningful calibration. The sensor’s response is then recorded and compared with the known values. Any differences observed guide the adjustment of the sensor’s output signal, scaling factor, or zero-offset parameters.
4. Adjusting Controller Settings and Feedback Loops
Once sensor outputs are aligned with known forces, attention turns to the system’s control unit. The tension controller interprets sensor input and manages the output to brakes, motors, or clutches. If the controller’s interpretation of sensor data is off, it can result in delayed or overcompensated responses. Calibration at this stage may involve updating software parameters, adjusting gain settings, or refining PID (proportional-integral-derivative) control loops to achieve a stable and responsive system behavior under varying loads.
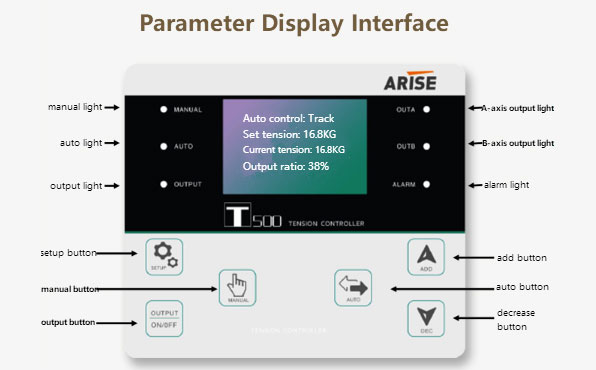
5. Conducting Live Operational Testing
Following adjustments, the system must be tested in a live production scenario or simulated environment. This step verifies that the calibration holds under real-time conditions and that tension remains stable across different speeds and loads. Observing material flow, tracking tension consistency, and confirming quick recovery from process disturbances are essential during this phase. Operators should monitor system feedback and responses to validate that the calibration translates effectively into practical improvements.
6. Documenting Calibration Results
The final step in the calibration process is thorough documentation. All calibration activities, including methods used, equipment involved, and results obtained, should be recorded for quality assurance purposes. This documentation not only ensures traceability for audits and compliance but also supports future maintenance and troubleshooting efforts. Regular calibration intervals should be established based on system usage, environmental conditions, and criticality of the application.
Challenges and Best Practices in Maintenance and Calibration of Tension Control Systems
To ensure the continued accuracy and reliability of tension control systems, it is essential to identify common challenges and adopt best practices tailored for calibration and maintenance activities.
Challenges | Description | Best Practices |
Sensor drift over time | Load cells and tension sensors lose accuracy as they age, leading to unreliable readings | Schedule routine sensor calibration and replace aging components when needed |
Inconsistent tension feedback due to mechanical wear | Wear on rollers, clutches, or brakes can create uneven tension distribution | Inspect moving parts regularly and replace or lubricate worn components |
Electrical noise affecting sensor accuracy | EMI from nearby equipment can interfere with sensor signals | Use shielded cables, maintain proper grounding, and separate power/signal lines |
Difficulty aligning load cells correctly | Incorrect mounting positions cause inaccurate tension measurements | Follow manufacturer’s alignment guidelines and use calibration weights to verify |
Inadequate documentation of calibration history | Without records, troubleshooting and trend analysis become difficult | Keep detailed logs of calibration values, dates, personnel, and procedures |
Process disruption during calibration procedures | Calibration can halt production and affect throughput | Plan calibrations during low-production hours and use built-in system simulations |
Misconfigured PID or control parameters | Poor tuning leads to unstable or lagging tension control | Adjust PID settings using real-time tuning software and expert guidelines |
Environmental factors such as temperature or humidity | Fluctuating conditions can affect sensor performance and material behavior | Use environmental-resistant sensors and monitor ambient conditions regularly |
Lack of skilled personnel for maintenance and calibration | Missteps during calibration can degrade system accuracy | Train personnel regularly and develop standardized checklists and workflows |
Integration errors with broader automation systems | Poor synchronization causes data mismatches and control errors | Test communication protocols and perform system-level calibrations post-updates |
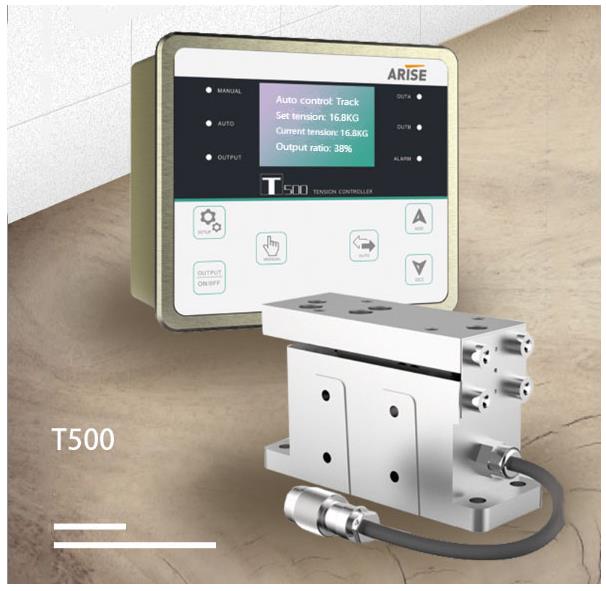
Final Thoughts
Effective maintenance and calibration of tension control systems are foundational to achieving consistent, high-quality production. By implementing a structured approach, manufacturers can reduce downtime, minimize waste, and extend the life of their tension control equipment.