How to Inspect Complex Graphics in Packaging Printing
Table of Contents
In the dynamic world of packaging printing, the demand for intricate and visually captivating designs has grown exponentially. These complex graphics not only enhance brand appeal but also communicate critical product information, making them an essential component of packaging. However, ensuring the accuracy and quality of these intricate designs presents unique challenges that require advanced inspection technologies and methodologies for packaging printing materials.
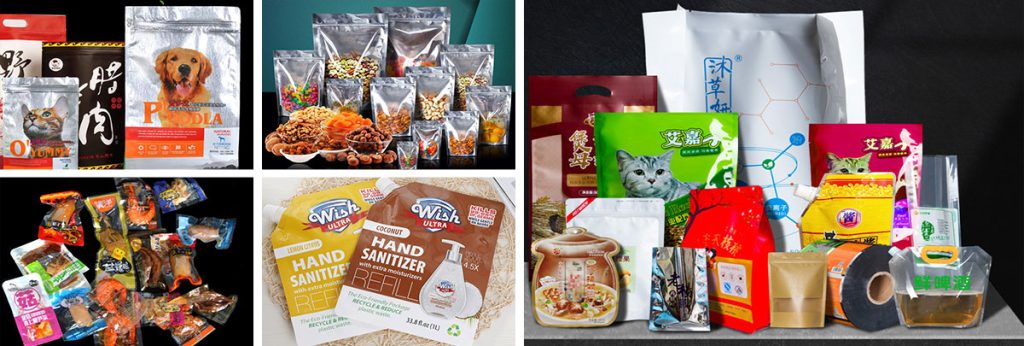
The Role of Graphics in Packaging Printing
Complex graphics serve multiple purposes in packaging:
- Brand Recognition: Detailed and unique designs set brands apart in a crowded market.
- Consumer Engagement: Eye-catching visuals attract attention and influence purchasing decisions.
- Regulatory Compliance: Graphics often include essential information, such as barcodes and warnings, which must be clear and legible.
Given these roles, even minor defects in graphics can have significant consequences, from damaging a brand’s reputation to causing product recalls.
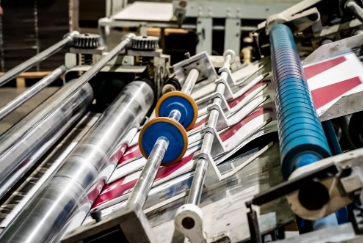
Challenges of Inspecting Complex Graphics in Packaging Printing
This table provides a structured view of the challenges, making it easy to reference and analyze.
Challenge | Description | Impact |
High Design Complexity | Intricate designs with gradients, fine lines, metallic finishes, and holographic elements. | Increased difficulty in distinguishing design elements from defects. |
Color Accuracy | Ensuring consistent reproduction of colors across various packaging printing batches. | Variations in color can affect brand consistency and consumer trust. |
Diverse Materials and Textures | Packaging uses paper, plastic, metallic foils, and other materials with unique inspection needs. | Reflective or textured surfaces complicate defect detection. |
Real-Time Processing | High-speed production lines require instant defect identification and correction. | Print inspection systems must be fast and precise to avoid production delays. |
Small Tolerances for Errors | Micro-level details like fine text and patterns demand high sensitivity. | Defects can be overlooked or misclassified, affecting quality. |
Integration with Advanced Techniques | Techniques such as embossing, foil stamping, and UV coatings add layers of complexity. | Specialized inspection technologies are required to ensure accuracy. |
Lighting and Environmental Factors | Variations in lighting, temperature, or humidity can affect inspection outcomes. | May lead to inconsistent defect detection and false positives. |
Regulatory Compliance | Graphics often include mandatory barcodes, warnings, and symbols. | Defective prints can result in non-compliance fines or recalls. |
High False Positive Rates | Advanced designs can trigger inspection systems to flag acceptable variations as defects. | Slows down production and increases operational costs. |
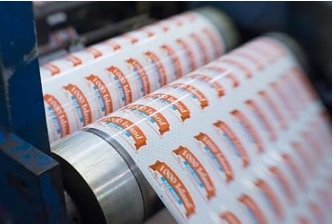
Technologies for Inspecting Complex Graphics in Packaging Printing
1. Machine Vision Systems
Machine vision systems are the backbone of modern inspection processes. Equipped with high-resolution cameras and powerful image processing algorithms, these web inspection vision systems for printing quality can detect a wide range of defects, including:
- Smudges and streaks.
- Misaligned prints.
- Missing elements.
- Variations in texture or material.
Advantages
- Operates in real-time at high speeds.
- Offers consistent performance without fatigue, unlike manual inspection.
- Highly customizable to different packaging materials and designs.
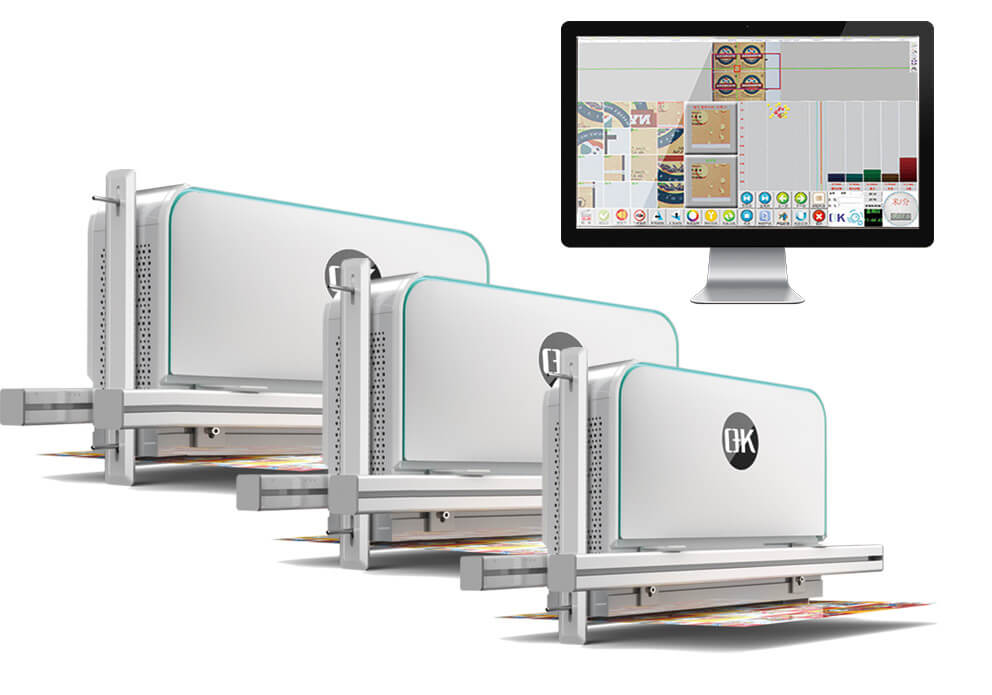
2. Artificial Intelligence (AI) and Machine Learning
AI-powered inspection systems use machine learning models to analyze complex graphics. By training on large datasets of acceptable and defective samples, these systems can adapt to design variability and identify defects that traditional methods might miss.
Applications:
- Differentiating intentional design elements (e.g., gradients or textures) from defects.
- Adapting to new designs without extensive reconfiguration.
- Reducing false positives by learning from historical inspection data.
3. Spectrophotometers and Colorimeters
Color consistency is crucial in packaging printing. Spectrophotometers and colorimeters ensure precise color matching by measuring light reflectance and absorption across the visible spectrum.
Key Features:
- Detect even slight variations in color.
- Monitor consistency across different printing batches and materials.
- Provide data for continuous quality improvement.
4. 3D Inspection Systems
For packaging that includes embossing, foil stamping, or other textured elements, 3D inspection systems are essential. These systems analyze depth and surface features to ensure uniformity.
Benefits:
- Detects irregularities in embossed or textured designs.
- Verifies the alignment and placement of foil or coatings.
- Useful for quality control in premium packaging applications.
5. High-Speed Line-Scan Cameras
Line-scan cameras are designed for high-speed production environments. They capture detailed, continuous images of packaging as it moves along the production line.
Advantages:
- Handles ultra-high-speed printing processes.
- Offers superior resolution for inspecting fine details.
- Ideal for wide-format printing applications.
6. Infrared and UV Inspection Systems
These systems are used to inspect invisible elements such as UV coatings, security marks, or tamper-evident features, which are often included in packaging for branding or regulatory purposes.
Applications:
- Detects defects in coatings and laminations.
- Verifies the presence of security features.
- Ensures consistency in specialty printing techniques.
7. Automated Defect Detection Software
Automated defect detection software integrates with inspection systems to analyze captured images or data. Advanced algorithms identify defects, categorize them, and generate actionable reports.
Capabilities:
- Identifies defects such as registration errors, uneven ink application, and missing details.
- Provides real-time alerts for immediate corrective action.
- Stores inspection data for traceability and compliance audits.
8. Multi-Spectral Imaging Systems
Multi-spectral imaging systems use multiple wavelengths of light to inspect complex graphics. They excel in identifying subtle defects that might not be visible under standard lighting conditions.
Advantages:
- Works across a variety of substrates, including reflective or transparent materials.
- Identifies defects in intricate designs with gradients or metallic finishes.
- Enhances detection accuracy for challenging materials.
9. Integrated Quality Control Platforms
Modern packaging facilities often use integrated quality control platforms that combine multiple technologies into a single 100% inspection system. These platforms streamline the inspection process and provide centralized data management.
Features:
- Synchronization with printing machines for inline defect detection.
- Comprehensive reporting and analytics for process optimization.
- Scalability to accommodate different packaging formats and production volumes.
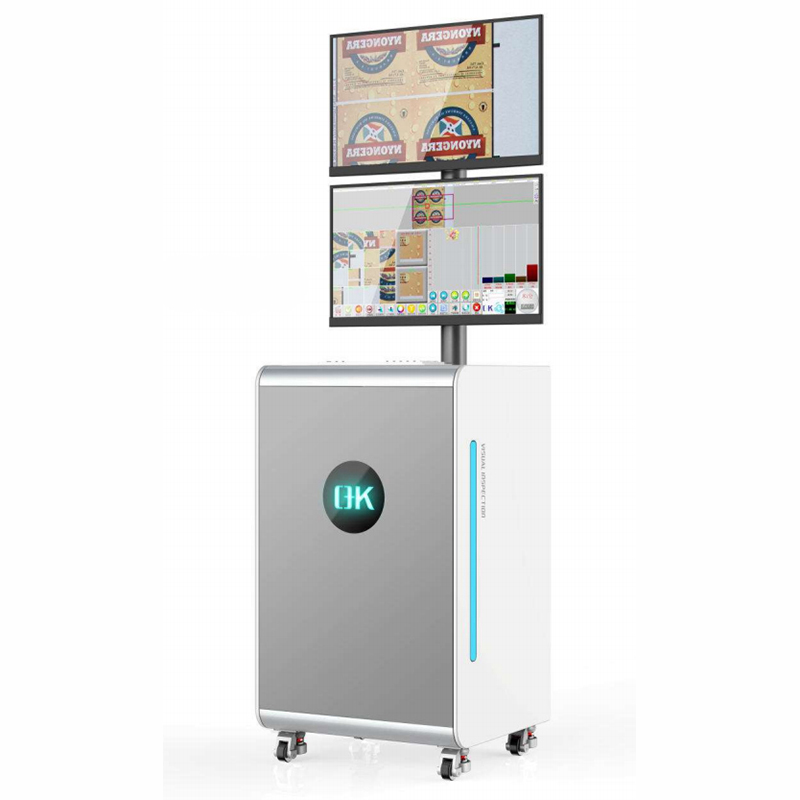
Conclusion
Inspecting complex graphics in packaging printing is no longer just about identifying defects; it’s about maintaining brand integrity, meeting consumer expectations, and ensuring operational efficiency. By adopting advanced technologies like machine vision, AI, and multi-spectral imaging, manufacturers can overcome challenges and deliver flawless packaging that meets both consumer expectations and industry standards.