How to Improve Printing Inspection Accuracy in the Packaging and Label Industry
Table of Contents
Printing errors, such as color deviations, misregistration, and missing details, can lead to costly recalls and dissatisfied customers. To address these challenges, innovative solutions have emerged to improve the accuracy of printing inspections. In this article, we explore key strategies and technologies that enhance printing inspection precision in the packaging and label industry.
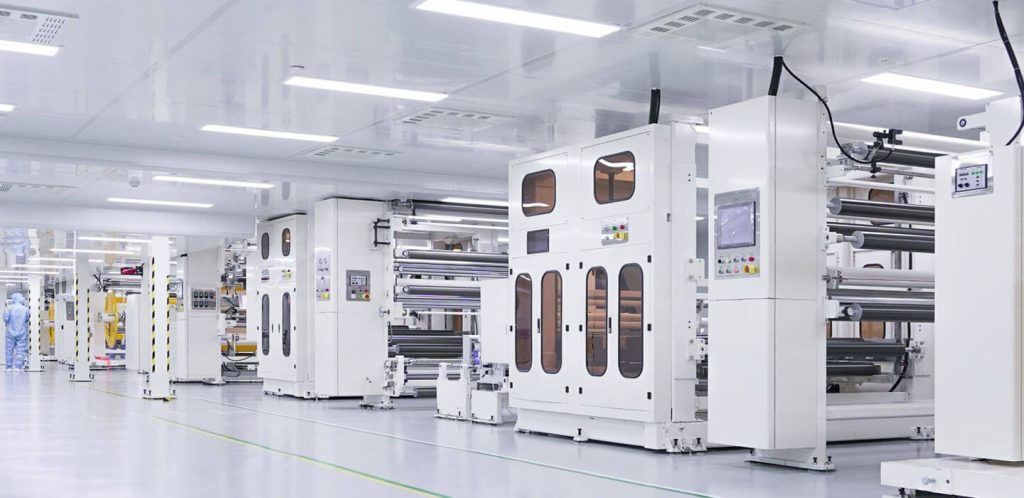
Why Need Improving Printing Inspection Accuracy in the Packaging and Label Industry
Improving printing inspection accuracy in the packaging and label industry is crucial for several key reasons:
- Regulatory Compliance: The packaging and labeling of products often involves strict regulations, especially for food, pharmaceuticals, and consumer goods. High-quality and accurate printing ensures compliance with these regulations, preventing costly penalties or product recalls.
- Brand Reputation: Packaging is a key element of a brand’s identity. Poor print quality, such as color misalignment or misprints, can negatively impact consumer perceptions and trust in the brand. Accurate printing inspection helps maintain the integrity of the brand image.
- Consumer Safety: In industries like pharmaceuticals and food, incorrect labeling could lead to serious consumer safety issues, such as incorrect dosage instructions or allergens not being properly listed. Ensuring printing accuracy helps mitigate these risks.
- Cost Efficiency: Errors in printing can result in significant waste, whether through misprinted packaging being discarded or costly rework. Improved inspection accuracy reduces the likelihood of these errors, leading to lower material and operational costs.
- Supply Chain Efficiency: Packaging is an integral part of the supply chain, and mistakes can cause delays, disruptions, or inventory shortages. High-accuracy inspection ensures that packaging meets specifications, helping to maintain smooth operations and timely product distribution.
- Technological Advancements: As the packaging industry embraces new technologies such as digital printing, the need for precise inspection systems becomes more critical to ensure the consistent quality of the printed output. Automation and AI-based inspection tools are becoming increasingly important for achieving these high standards.
- Competitive Advantage: In a highly competitive market, companies that can consistently deliver high-quality, accurate printed packaging have a distinct advantage over competitors. Improving inspection accuracy helps companies stay ahead in terms of quality and customer satisfaction.
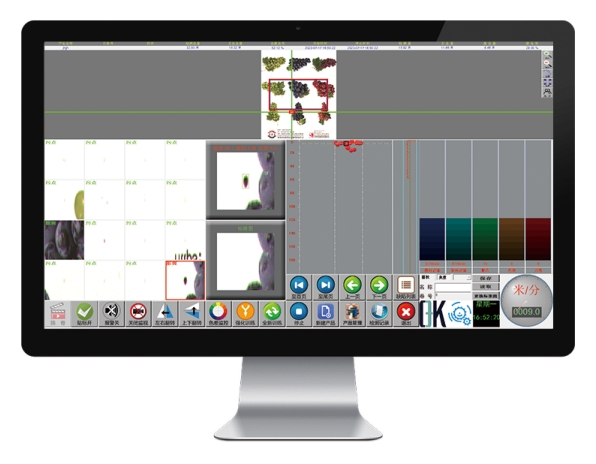
What are the Key Factors affecting Printing Inspection Accuracy in the Packaging and Label Industry
This chart emphasizes the critical factors specific to the packaging and label industry, where both visual aesthetics and functional precision play a vital role in maintaining high inspection standards.
Factor | Description | Impact on Accuracy |
Resolution of Inspection Systems | The resolution of cameras and scanners used to identify printing defects. | Higher resolution detects fine defects such as text misalignments or subtle color variations. |
Color Consistency | Ability to maintain color uniformity across batches using spectrophotometers. | Inaccurate color reproduction leads to mismatched branding and quality issues. |
Material Properties | Characteristics of packaging materials, such as reflectivity, transparency, or texture. | Reflective or uneven surfaces can obscure defect detection by optical systems. |
Production Line Speed | The rate at which labels and packaging move through the inspection process. | Faster speeds may reduce the accuracy if inspection systems are not optimized for high throughput. |
Lighting Conditions | Quality and stability of light in the inspection area (e.g., LED vs. ambient lighting). | Poor lighting can result in missed defects or false positives. |
Environmental Stability | Factors like temperature, humidity, and static affecting the printing and inspection process. | Fluctuations can cause ink spreading or distortions that are hard to detect consistently. |
Barcode and Text Verification | Accuracy in verifying text, barcodes, and QR codes using OCR (Optical Character Recognition). | Undetected errors in regulatory or product information can lead to compliance issues. |
Feedback and Control Systems | Systems that provide real-time feedback to correct defects during production. | Lack of feedback delays correction, resulting in increased material wastage. |
Regular Calibration | Scheduled maintenance of cameras, spectrophotometers, automated self-calibration, and other equipment. | Poorly calibrated equipment reduces reliability and precision of inspections. |
Operator Expertise | Training and skill level of personnel managing and interpreting inspection systems. | Human error in setup or data interpretation can compromise the accuracy of defect detection. |
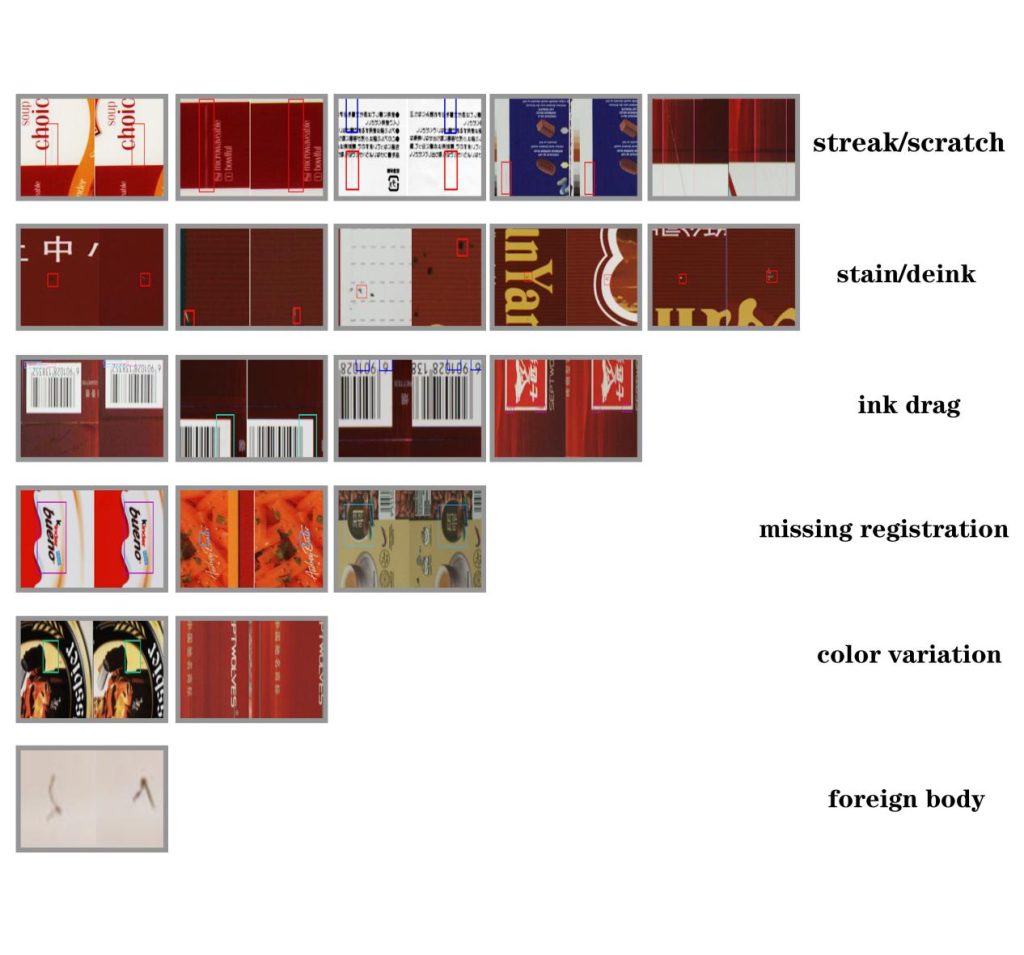
Key Strategies for Improving Printing Inspection Accuracy in the Packaging and Label Industry
1. Adoption of Advanced Vision Systems
Advanced web inspection vision systems equipped with high-resolution cameras and machine learning algorithms offer unmatched accuracy in detecting defects. These systems can:
- Identify subtle color shifts and inconsistencies.
- Detect micro-level defects in text and graphic elements.
- Operate at high speeds, ensuring seamless integration with high-volume production lines.
Solution Highlight: Multi-camera setups with 360° views are particularly effective for inspecting cylindrical or irregularly shaped packaging.
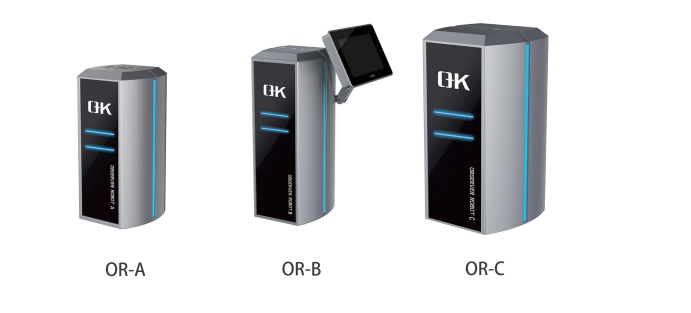
2. Using Artificial Intelligence (AI) and Machine Learning
AI-driven inspection systems can analyze patterns and learn from historical data to improve detection capabilities over time. This includes:
- Differentiating between acceptable variations and actual defects.
- Reducing false positives and negatives.
- Offering predictive analytics to identify potential quality issues before they occur.
Benefit: Continuous learning capabilities ensure that inspection systems adapt to evolving production challenges.
3. Integration of Spectrophotometers for Color Accuracy
Color consistency is crucial in branding. Spectrophotometers integrated into inspection systems provide:
- Precise color measurement against predefined standards.
- Alerts for color deviations in real-time.
- Compatibility with color management software for consistent results across batches.
Solution Highlight: Inline spectrophotometers eliminate the need for manual sampling, ensuring 100% print inspection coverage.
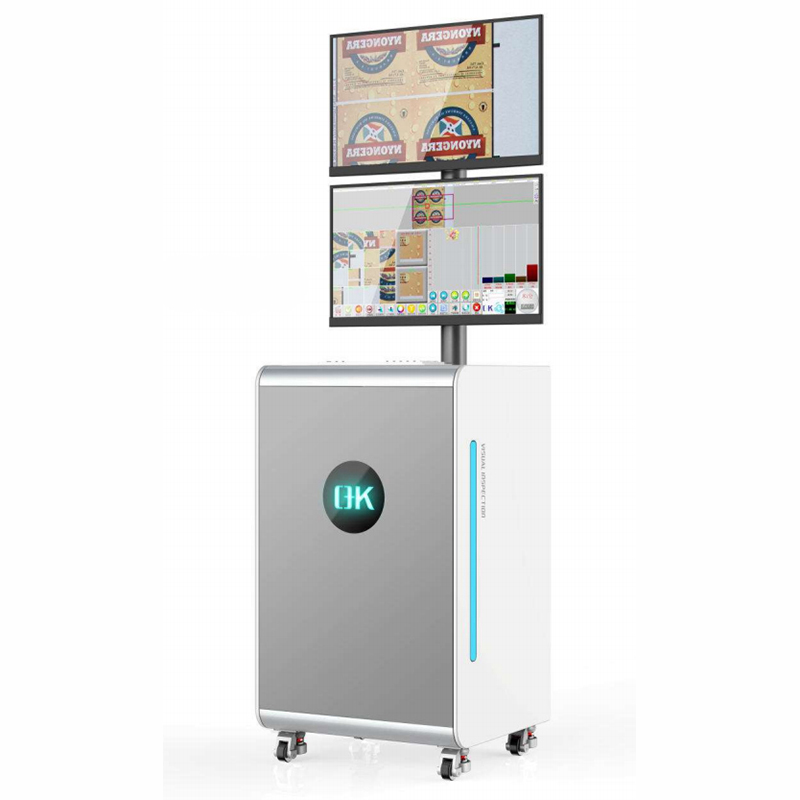
4. Implementation of Digital Twin Technology
Digital twins replicate the production process in a virtual environment, enabling real-time monitoring and analysis. Benefits include:
- Simulating print runs to predict and rectify potential issues.
- Ensuring alignment between the design and final product.
- Facilitating remote diagnostics and support.
Industry Use Case: Label printers can simulate intricate designs to verify accuracy before initiating production.
5. Leveraging Real-Time Data Analytics
Video inspection systems that provide real-time data feedback empower operators to make immediate adjustments. Features include:
- Live dashboards with actionable insights.
- Historical data analysis to identify recurring defects.
- Automated reporting for compliance documentation.
Impact: Reduced waste and downtime through faster decision-making.
6. High-Speed Scanning and Optical Character Recognition (OCR)
OCR technology ensures the accuracy of text elements, barcodes, and QR codes on labels and packaging. Benefits include:
- Verifying text alignment, size, and spelling.
- Ensuring barcode readability under various lighting conditions.
- Supporting compliance with industry regulations.
Key Application: Pharmaceutical and food packaging industries rely heavily on OCR for regulatory label accuracy.
7. Enhancing Environmental Control
Environmental factors such as lighting, temperature, and humidity can affect inspection accuracy. Solutions include:
- Enclosed inspection environments to eliminate ambient light interference.
- Temperature-controlled systems to stabilize ink behavior.
- Anti-static mechanisms to prevent material deformation.
Recommendation: Pairing controlled environments with precision inspection systems ensures consistent results.
8. Automation and Robotic Integration
Automated print inspection systems reduce human error and improve consistency. Advanced robotics can:
- Handle materials with delicate or complex structures.
- Provide precise positioning for thorough inspection coverage.
- Enable seamless integration with production lines for uninterrupted workflow.
Example: Robots equipped with AI-driven vision systems can identify defects in intricate label designs more efficiently than manual inspections.
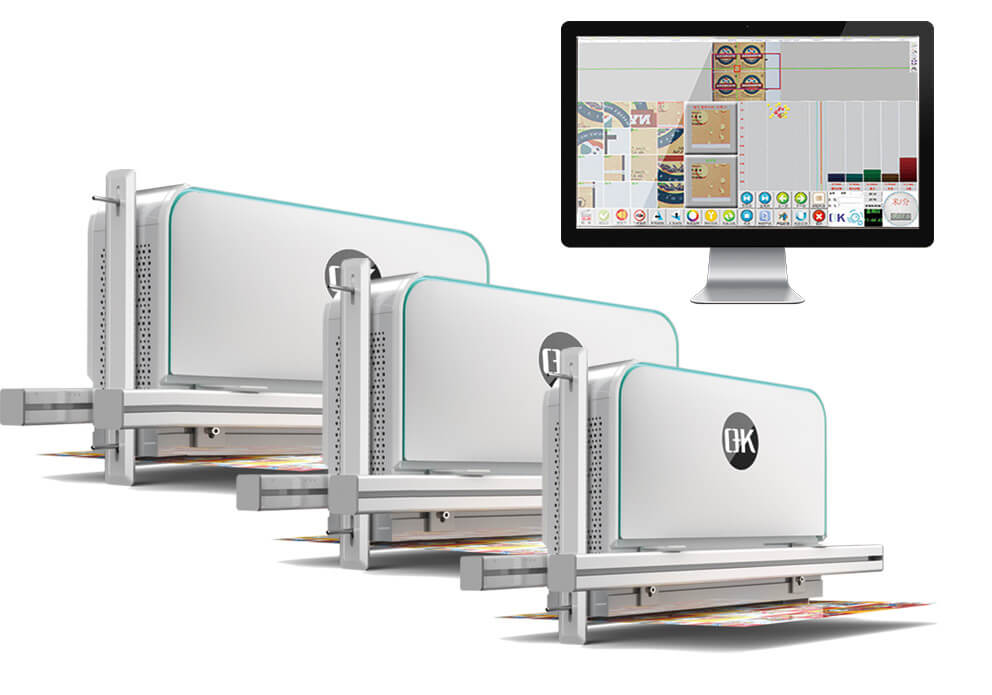
To sum up, improving printing inspection accuracy in the packaging and label industry involves a combination of cutting-edge technologies, environmental control, real-time monitoring, etc. Through adopting these strategies, manufacturers can ensure defect-free products, minimize waste and maintain customer trust.