How to Ensure Effective Tension Control in Metal Coil Processing
Tension control is a fundamental aspect that ensures the quality and integrity of the final product in the metal coil processing. From automotive parts to construction materials, the precision with which tension is managed can significantly impact both the efficiency of production and the quality of the output. This article delves into the importance of tension control, the challenges faced, and the technologies employed to maintain optimal tension in metal coil processing.
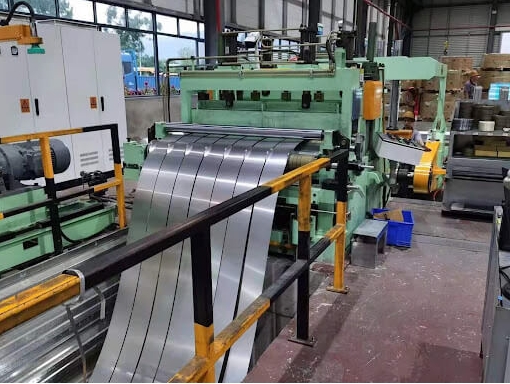
Importance of Tension Control in Metal Coil Processing
Tension control refers to the regulation of the force applied to a metal strip as it moves through various stages of processing such as unwinding, slitting, and rewinding. Proper tension control is crucial for several reasons:
- Quality Assurance: Consistent tension is essential to prevent defects such as wrinkles, scratches, and edge waviness. Maintaining the right tension ensures that the metal strip remains flat and uniform, which is vital for the final product’s performance.
- Process Efficiency: Effective tension control reduces the risk of coil breaks and downtime, leading to a smoother and more efficient production process. It also minimizes waste, thereby lowering production costs.
- Safety: Inadequate tension control can lead to sudden breakages, releasing stored energy that poses significant safety risks to operators and equipment.
- Material Handling: Consistent tension ensures smooth unwinding, slitting, and rewinding of coils.
- Equipment Longevity: Reduces wear and tear on machinery by maintaining optimal tension levels.
Challenges in Tension Control for the Processing of Metal Coils
Below is a detailed examination of these challenges and their impacts.
Challenge | Description | Impact |
Variability in Material Properties | Differences in thickness, hardness, and elasticity between metal coils can make tension control inconsistent. | Inconsistent tension can lead to defects and quality issues. |
Speed Fluctuations | Changes in line speed during processing can introduce tension variations. | Requires real-time adjustments to maintain consistent tension. |
Equipment Wear and Tear | Over time, components like rollers, bearings, and brakes degrade, affecting their performance. | Can lead to uneven tension control and increased maintenance needs. |
Environmental Factors | Temperature and humidity can influence the behavior of the metal and the performance of tension control equipment. | Can introduce variability in tension control, affecting product quality. |
Complexity of Multistage Processes | Managing tension across different stages of processing (e.g., unwinding, slitting, rewinding) adds complexity. | Each stage requires precise control to avoid cumulative errors. |
High-Speed Processing | Maintaining optimal tension at high speeds is challenging due to increased dynamic forces. | Potential for increased defects and safety hazards. |
Operator Skill and Training | The effectiveness of tension control can be heavily influenced by the operator’s skill and understanding of the system. | Insufficient training can lead to poor tension management and increased downtime. |
Integration with Other Systems | Ensuring seamless integration and communication between tension control systems and other machinery in the production line. | Misalignment can cause synchronization issues, leading to tension variability. |
Dynamic Load Changes | Variations in coil diameter and weight as material is processed can affect tension. | Requires continuous monitoring and adjustment to maintain stability. |
Initial Setup and Calibration | Proper initial setup and calibration of tension control systems are critical but can be time-consuming and complex. | Incorrect setup can lead to ongoing tension issues and product defects. |
Cost Constraints | Advanced tension control systems and technologies can be expensive to implement and maintain. | Balancing cost with the need for precise tension control can be challenging for some operations. |
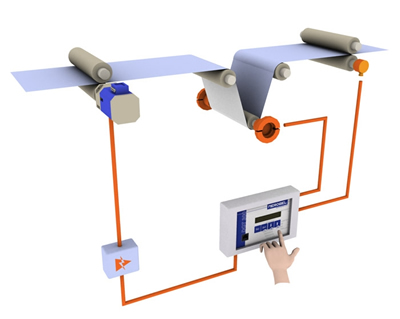
Strategies to Address the Challenges in Tension Control for Metal Coil Processing
Addressing the challenges in tension control involves a combination of technological, procedural, and maintenance strategies.
1. Advanced Control Systems
- Closed-loop Feedback Systems: Implementing closed-loop control systems can dynamically adjust tension by monitoring real-time feedback from sensors and adjusting the tensioning mechanisms accordingly.
- Adaptive Control Algorithms: Use adaptive tension control algorithms that can adjust control parameters in real-time to respond to variations in material properties, line speed, and environmental conditions.
- Predictive Control: Employ model predictive control (MPC) techniques to anticipate future disturbances and adjust tension proactively.
2. High-Precision Sensors
- Load Cells: Utilize high-precision load cells to measure tension accurately across various points of the processing line.
- Tachometers and Encoders: Install tachometers and encoders to monitor the speed of rolls and ensure synchronized movement, preventing tension fluctuations.
- Laser and Ultrasonic Sensors: Use laser or ultrasonic sensors for non-contact measurement of strip position and tension, especially for high-speed lines.
3. Mechanical Improvements
- Tension Brakes and Clutches: Ensure that tension brakes and clutches are of high quality and properly maintained to provide consistent control over coil tension.
- Dancer Rolls: Implement dancer roll systems to absorb tension variations and provide a buffer that maintains consistent tension throughout the process.
- Proper Alignment: Regularly check and adjust the alignment of rollers and other mechanical components to prevent uneven tension distribution.
4. Process Optimization
- Material Handling Procedures: Optimize material handling procedures to minimize disturbances in the coil processing line. This includes smooth start-ups, stops, and transitions between different processing stages.
- Automation and Integration: Integrate automation systems to reduce human error and enhance consistency in tension control across different processing stages.
- Line Speed Management: Optimize line speed to balance productivity with tension stability, avoiding speeds that may induce excessive tension variations.
5. Maintenance and Calibration
- Regular Maintenance: Implement a rigorous maintenance schedule for all mechanical and control system components to prevent wear and tear that can lead to tension control issues.
- Calibration: Regularly calibrate tension sensors and control devices to ensure accurate tension measurement and control.
- Inspection: Conduct frequent inspections to identify and rectify any potential sources of tension variation, such as worn-out parts or misaligned components.
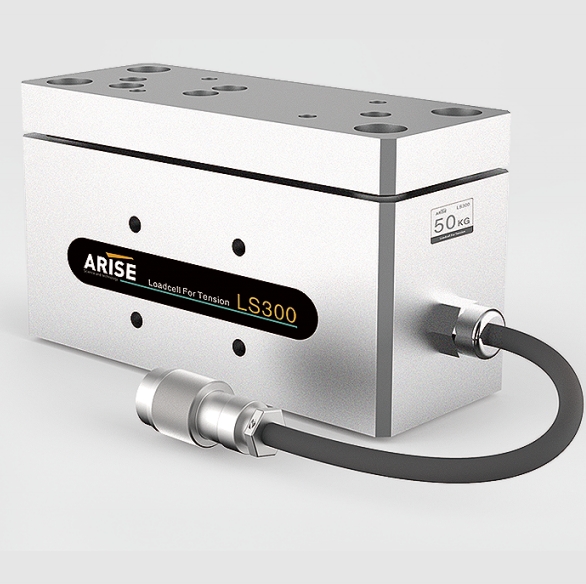
6. Operator Training
- Technical Training: Provide thorough technical training for operators on the importance of tension control and the functioning of control systems and sensors.
- Troubleshooting Skills: Equip operators with troubleshooting skills to quickly identify and address tension-related issues during production.
- Best Practices: Train operators on best practices for material handling and line management to maintain consistent tension.
7. Data Analysis and Continuous Improvement
- Data Logging: Implement data logging systems to record tension levels, speed, and other relevant parameters throughout the processing line.
- Data Analysis Tools: Use data analysis tools to identify patterns and root causes of tension variations, enabling continuous improvement in tension control strategies.
- Feedback Loops: Establish feedback loops where operators and maintenance personnel can report issues and suggest improvements based on their observations and data analysis.
8. Material-Specific Strategies
- Tailored Control Settings: Customize tension control settings based on the specific properties of different materials being processed, such as thickness, strength, and elasticity.
- Material Testing: Conduct thorough material testing to understand the behavior of different metals under various tension levels and adjust control parameters accordingly.
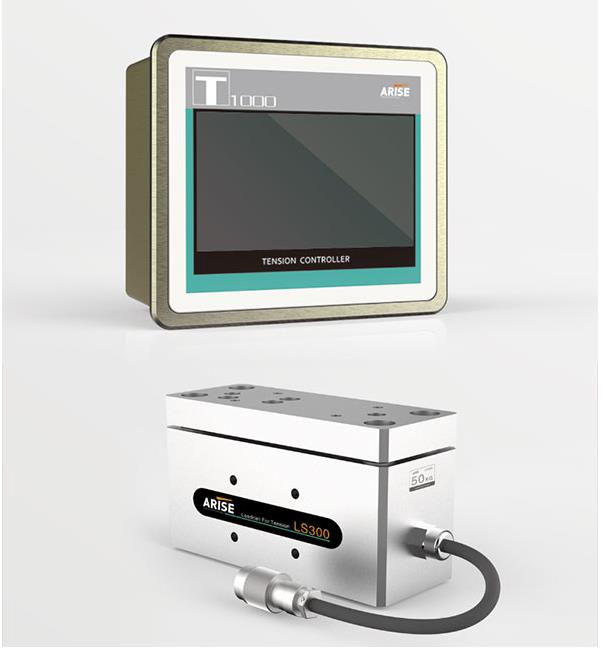
Conclusion
Despite the challenges posed by material variability, speed fluctuations, equipment wear, and environmental factors, modern technologies offer robust solutions for maintaining optimal tension. Through integrating advanced sensors, tension controllers, and drives, and ensuring regular maintenance and operator training, manufacturers can achieve precise tension control, leading to superior product quality and operational efficiency.