How to Customize Printing Inspection Systems for Different Substrates
In the printing industry, ensuring high-quality output across diverse substrates such as paper, plastic, metal, textiles, and glass, etc, requires adaptable inspection systems. Each substrate presents unique challenges in ink adhesion, color consistency, texture, and defect detection. Customizing printing inspection systems to accommodate these variations is essential for maintaining precision, reducing waste, and improving efficiency. This article delves into how printing inspection systems can be tailored to different substrates for achieving optimal results.
Table of Contents
Challenges in Printing Inspection Across Different Substrates
Customizing printing inspection systems based on these challenges ensures accurate defect detection and improved print quality across different substrates.
Substrate Type | Challenges | Possible Solutions |
Glossy & Reflective | Glare and reflections interfere with defect detection. | Use polarized lighting and advanced filtering techniques. |
Transparent & Translucent | Background interference makes defects harder to detect. | Apply backlighting and contrast enhancement methods. |
Textured & Embossed | Variations in surface height can cause false defect detection. | Use 3D surface scanning and multi-angle imaging. |
Flexible Films & Foils | Material movement during inspection affects accuracy. | Implement real-time tracking and web stabilization. |
Highly Absorbent (e.g., Paper, Textiles) | Ink bleeding can alter expected print quality. | Adjust ink application parameters and customize defect tolerance. |
Non-Absorbent (e.g., Plastics, Metalized Foils) | Ink adhesion issues may cause smudging. | Use UV or infrared inspection to verify ink bonding. |
Security & Specialty Prints | Invisible inks and coatings require specialized detection. | Integrate multi-spectral and UV inspection systems. |
Curved & Uneven Surfaces | Standard cameras struggle to capture complete details. | Utilize high-resolution multi-angle or 3D imaging. |
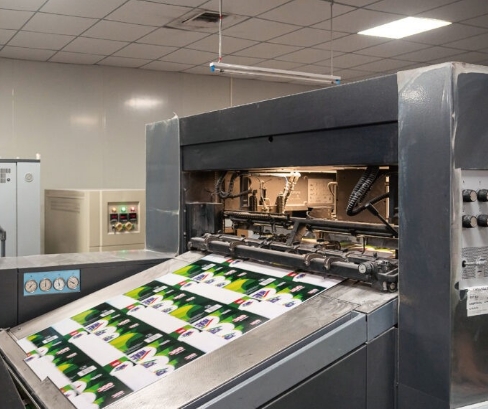
Key Customization Factors for Different Substrates in Printing Inspection
- Lighting Optimization
Different substrates interact with light in unique ways. Glossy and reflective materials, such as metalized films and high-gloss plastics, can create glare, making defect detection challenging. Using polarized lighting or specialized filters helps minimize reflections. For transparent materials like PET films and glass, backlighting enhances contrast and makes defects more visible.
- Camera and Sensor Selection
The choice of cameras and sensors must be adapted to the substrate type. High-resolution cameras are necessary for detecting fine details, while multi-angle imaging helps inspect textured or curved surfaces. For 3D objects or highly uneven materials, 3D surface scanning improves defect detection.
- Ink Absorption and Adhesion
Different materials have varying levels of ink absorption and adhesion. Absorbent materials like uncoated paper and textiles may experience ink bleeding, requiring customized color inspection algorithms. Non-absorbent surfaces, such as plastics and foils, may suffer from smudging, necessitating UV or infrared inspection to detect adhesion issues.
- Material Flexibility and Stability
Flexible substrates, such as thin films and foils, tend to shift during printing, making consistent inspection more difficult. Implementing real-time tracking and dynamic stabilization technology ensures that the system compensates for material movement, maintaining inspection accuracy.
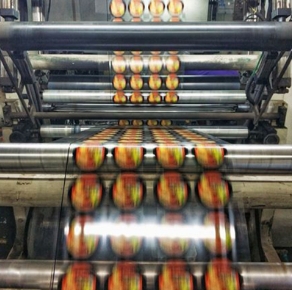
- Transparency and Opacity
Transparent and translucent materials pose a challenge due to background interference. Specialized contrast enhancement techniques and customized lighting configurations help improve defect visibility. Opaque materials, such as cardboard and metal, typically require standard lighting but may need multi-angle imaging for accurate inspection.
- Defect Tolerance Settings
Different industries and applications have specific quality standards. For example, the packaging industry may allow minor color variations, while pharmaceutical printing requires near-perfect accuracy. Customizing defect tolerance settings ensures that the inspection system meets industry-specific quality requirements without unnecessary rejections.
- Multi-Spectral and UV Inspection
Certain substrates require specialized inspection beyond visible light. Security markings, invisible coatings, and specialty inks can only be detected using multispectral or UV imaging. Integrating these technologies ensures that hidden defects or security features are accurately inspected.
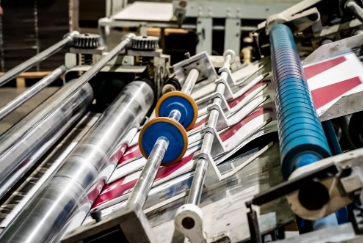
Advanced Technologies for Customized Print Inspection System
1. High-Resolution Imaging Systems
Advanced 100% print inspection systems use ultra-high-resolution cameras that capture fine details, enabling precise defect detection. Multi-camera setups allow for multi-angle imaging, ensuring complete coverage, especially for textured or curved substrates.
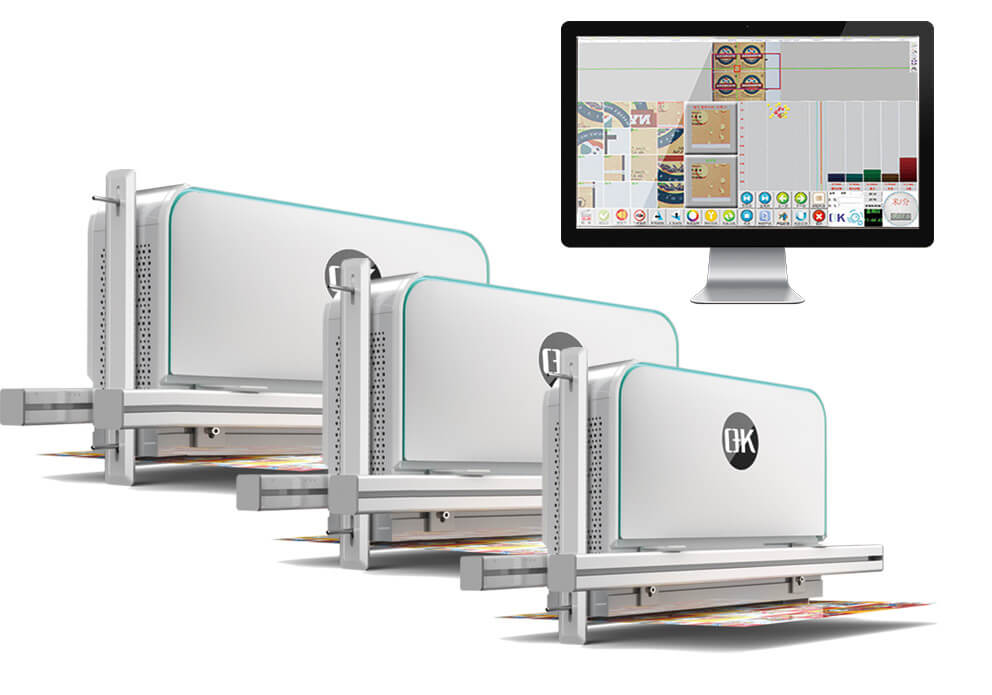
2. Substrate-Specific Inspection Adjustments
Different materials, such as glossy, matte, transparent, or textured surfaces, require distinct inspection setups. Polarized lighting reduces glare on reflective substrates, while backlighting improves contrast for transparent films. High-resolution imaging ensures defect detection on fine-textured or embossed materials.
3. Adaptive Lighting Solutions
Proper lighting is critical for accurate inspection. Multi-angle LED lighting enhances defect visibility on uneven surfaces, while UV and infrared lighting help detect invisible markings, ink adhesion issues, and security features. Customizing lighting configurations based on substrate properties ensures consistent inspection quality.
4. AI-Powered Image Processing and Defect Classification
Artificial intelligence (AI) and machine learning algorithms enable real-time defect detection and classification. By continuously learning from inspection data, AI can reduce false positives, differentiate between acceptable variations and true defects, and improve overall inspection accuracy.
5. Real-Time Web Tracking and Stabilization
For high-speed printing on flexible materials like films and labels, real-time tracking and stabilization systems adjust inspection parameters dynamically. These web inspection vision systems for compensate for substrate movement, ensuring consistent defect detection without compromising production speed.
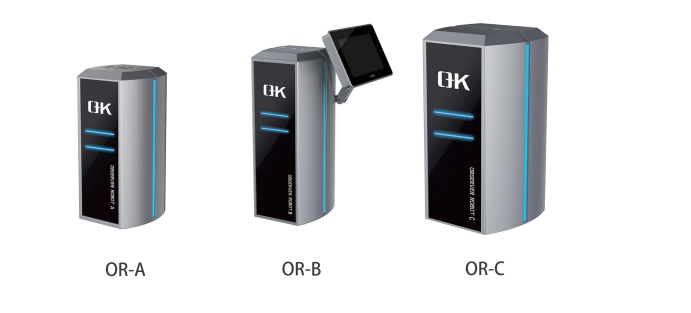
6. Custom Defect Tolerance Levels
Different industries have varying quality requirements. Packaging and label printing may allow slight variations, while pharmaceutical and security printing demand near-perfect accuracy. Customizing defect tolerance settings prevents unnecessary rejections while maintaining compliance with industry standards.
7. 3D Surface Scanning Technology
For substrates with raised textures, embossed designs, or uneven surfaces, 3D scanning technology enables precise inspection. It ensures accurate defect detection even when surface variations impact ink application.
8. Multi-Spectral and UV Inspection for Special Applications
Multi-spectral imaging detects print quality beyond the visible spectrum, making it essential for security printing, specialty coatings, and invisible inks. UV inspection enhances defect detection on materials where standard lighting is insufficient.
9. Automated Sorting and Defect Handling
Customized rejection mechanisms sort defective prints based on severity, reducing manual intervention. Automated defect categorization ensures that minor variations are flagged differently from critical defects, optimizing production efficiency and minimizing material waste.
10. Cloud-based Quality Monitoring and Data Analytics
Integrating cloud-based inspection systems enables remote monitoring and real-time quality analysis across multiple production sites. Data analytics help identify recurring defects, allowing manufacturers to adjust printing processes and improve long-term quality control.
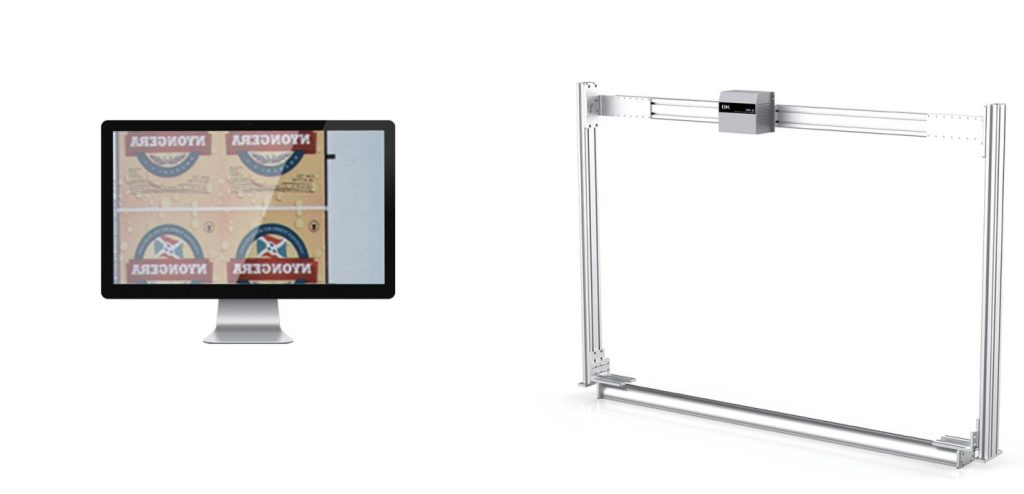
Industry-specific Applications of Customized Print Inspection Systems
Industry | Application | Customization Features |
Packaging & Labeling | Ensuring print quality on flexible films and cartons. | Real-time web tracking, adaptive lighting, AI defect detection. |
Pharmaceutical | Verifying labels, barcodes, and dosage information. | High-resolution imaging, OCR/OCV verification, UV inspection. |
Security Printing | Detecting counterfeit features in banknotes, passports. | Multi-spectral imaging, UV detection, AI-driven authentication. |
Textile Printing | Identifying ink inconsistencies on fabric surfaces. | 3D scanning, AI-based color consistency analysis. |
Electronics & PCB | Inspecting circuit boards for printing accuracy. | High-magnification cameras, defect classification, real-time analysis. |
Metal & Automotive | Checking logos, safety markings, and serial numbers. | Glare reduction technology, multi-angle imaging. |
Glass & Transparent Films | Ensuring print clarity on bottles, screens, and packaging. | Backlighting, contrast enhancement, UV ink verification. |
Flexible Packaging | Monitoring print accuracy on shrink sleeves and pouches. | Dynamic stabilization, distortion correction, AI-driven pattern recognition. |
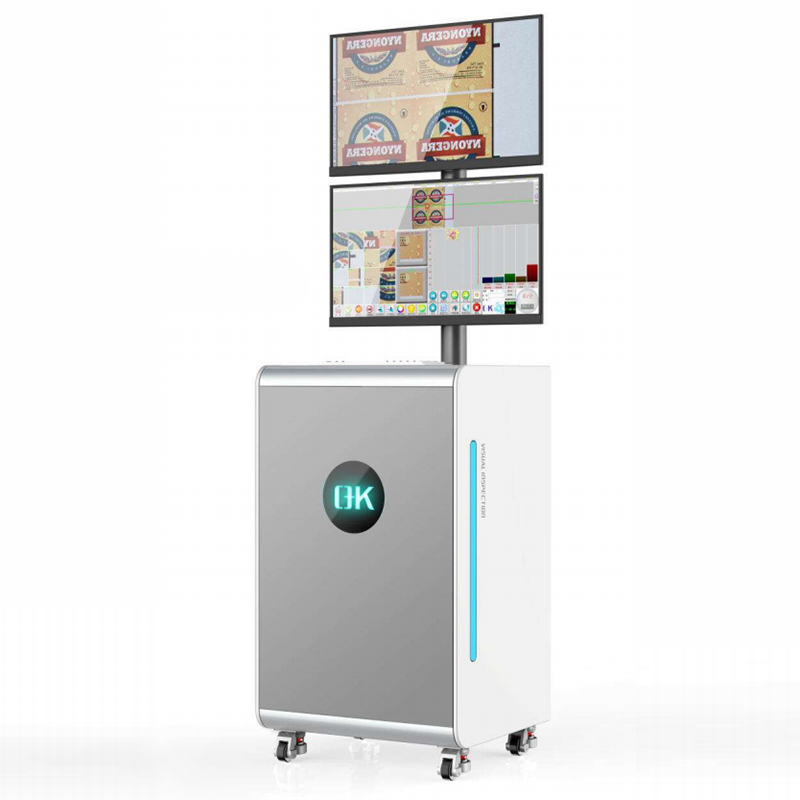
Summary
Customizing printing inspection systems for different substrates and materials is essential for maintaining quality and efficiency in modern printing operations. By tailoring inspection methods to account for surface reflectivity, transparency, ink absorption, and material flexibility, manufacturers can reduce errors, minimize waste, and improve overall production output.