How to Address the Challenges of Tension Control in Printing Inspection
In high-speed printing operations, maintaining precise tension control is critical for ensuring print quality and reliable inspection accuracy. Even minor fluctuations in web tension can lead to registration errors, print distortions, and inconsistencies that impact the final product. Proper tension control helps prevent common issues like misalignment, wrinkles, and print defects, thereby enhancing the overall quality of printed materials. However, managing tension during the printing process comes with several challenges. In this article, we will explore the key challenges in tension control for printing inspection and offer effective solutions to mitigate these issues.
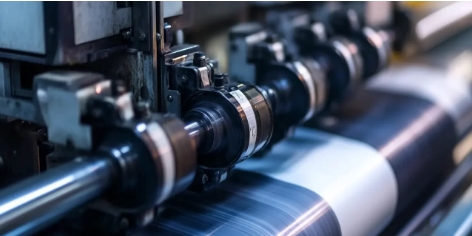
Table of Contents
The Role of Tension Control in Printing Inspection
Print inspection systems rely on stable material handling to accurately identify defects such as misalignment, color inconsistencies, and print smudging. Proper tension control ensures that the substrate moves smoothly through the inspection system without wrinkles, stretching, or slack that could distort the printed images. This stability allows vision-based web inspection systems and other quality control tools to function optimally.
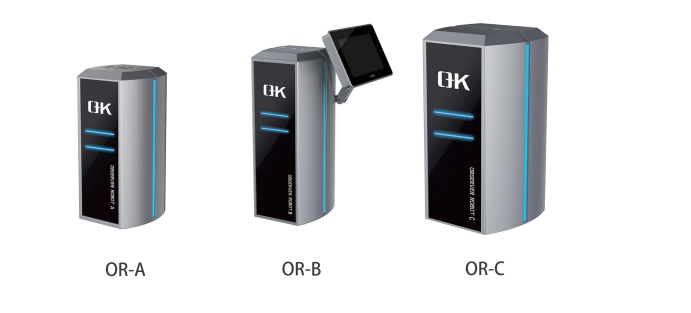
Challenges and Solutions in Tension Control for Printing Inspection
1. Variability in Substrate Properties
Challenge:
Substrates such as paper, plastic films, and textiles are used extensively in printing processes, but their properties can vary greatly. Factors like thickness, stiffness, elasticity, and moisture content affect how substrates behave during printing. These variations often cause fluctuations in tension, leading to inconsistent feeding and potential defects like wrinkles, skewing, or misprints.
Solution:
To tackle this challenge, advanced printing inspection systems utilize advanced tension control systems with real-time sensors. These sensors can detect the physical properties of the material and adjust the tension dynamically. Automated adjustments help optimize the feed tension for varying substrate properties, ensuring that printing quality remains consistent, regardless of material variations.
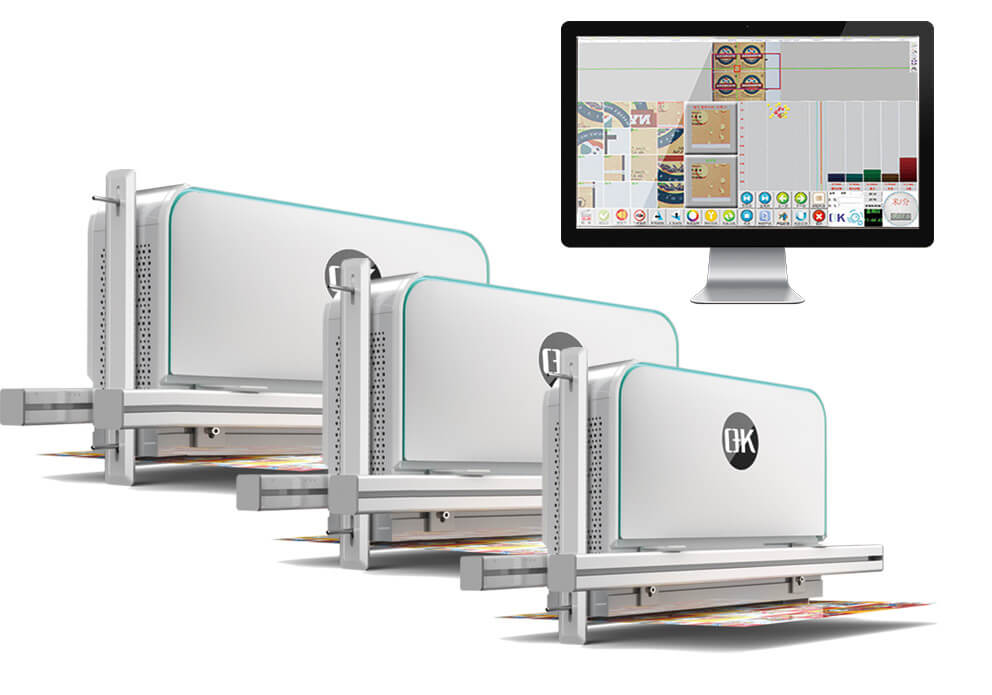
Automated web guide systems help maintain precise substrate alignment, reducing lateral movement that could affect print registration. These systems use sensors and actuators to make fine adjustments, keeping the web path stable and minimizing the risk of misalignment during high-speed printing.
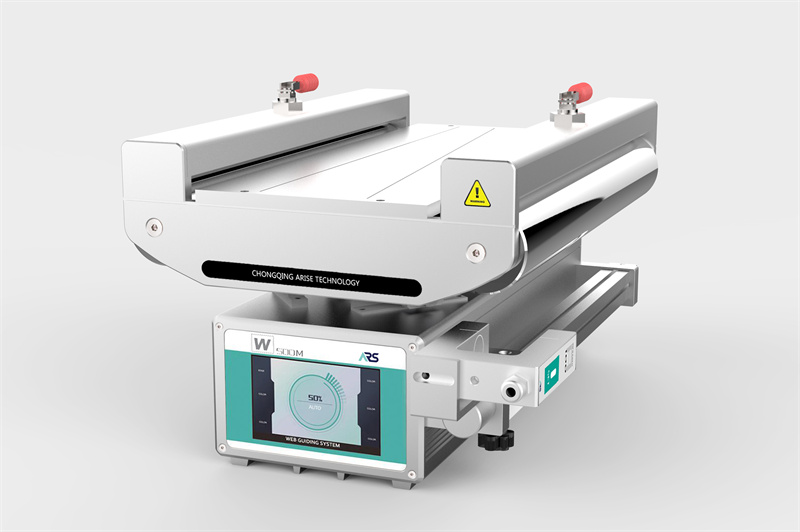
2. Environmental Factors
Challenge:
Environmental conditions, including temperature and humidity, can significantly affect the performance of printing materials. For example, paper may expand under high humidity, altering its tensile strength, while temperature fluctuations can change the viscosity of inks and adhesives. Such environmental shifts can cause tension irregularities, resulting in print defects.
Solution:
One of the most effective ways to address environmental impacts is through climate control. Printing facilities can install heating, ventilation, and air conditioning (HVAC) systems to stabilize temperature and humidity levels. Additionally, tension control systems can be designed to adapt to these changes by incorporating humidity and temperature sensors, allowing for real-time compensation to ensure optimal tension across varying environmental conditions.
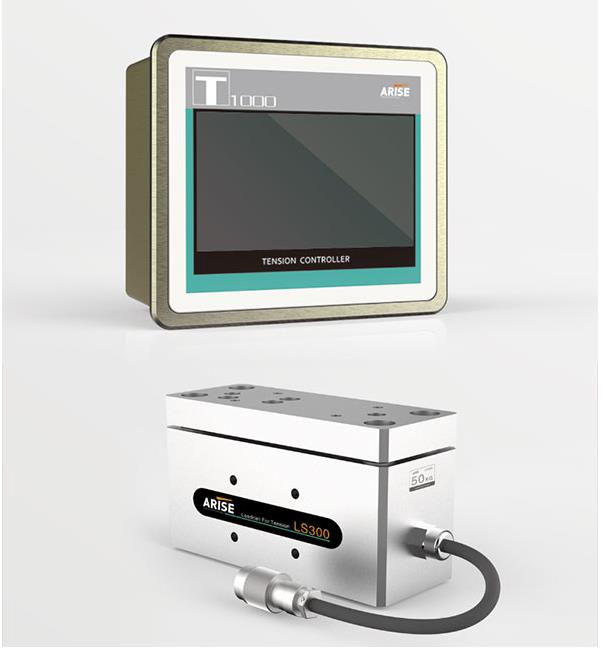
3. High Machine Speeds and Complexity
Challenge:
In modern printing, particularly with high-speed presses, maintaining consistent tension becomes increasingly difficult as speed increases. Rapid acceleration and deceleration of materials can create tension variations that lead to feed issues, misprints, or even equipment damage. The complexity of modern printing machines, with their multiple rollers and web paths, adds another layer of difficulty to achieving precise tension control.
Solution:
Advanced automated tension control systems are designed to work seamlessly at high speeds. These systems incorporate high-precision sensors, motorized adjustments, and real-time feedback loops that allow for rapid correction of tension discrepancies. Such systems continually monitor the tension across the printing press, dynamically adjusting to match the varying speeds, ensuring that tension remains stable throughout the process.
Ensuring seamless integration between tension control systems and a modern 100% printing inspection system is crucial for accurate defect detection. Synchronizing tension management with inspection cameras and sensors prevents misalignment issues that could lead to false defect identification or overlooked quality concerns.
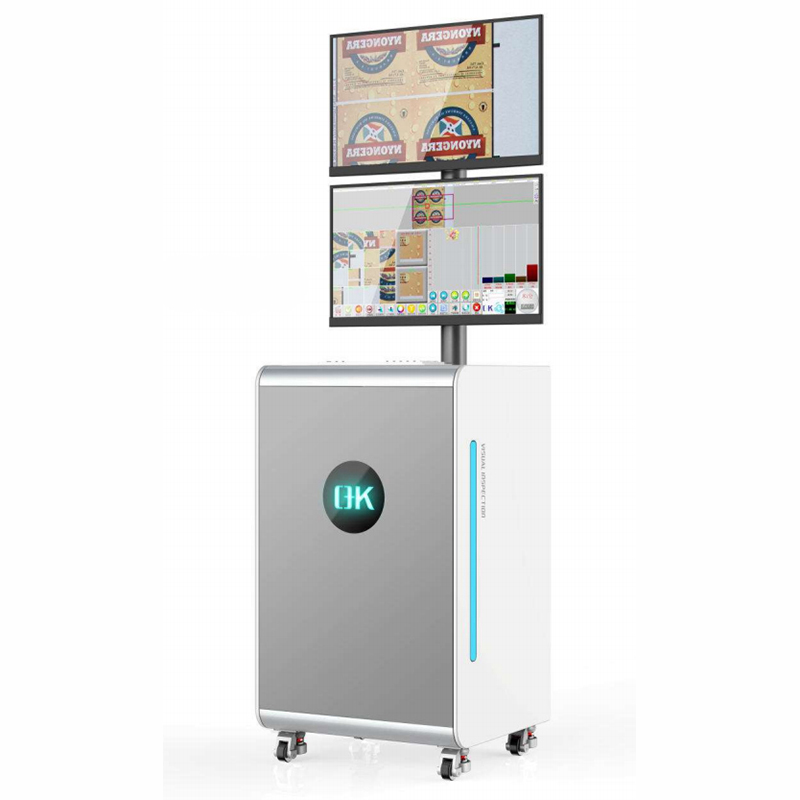
4. Inconsistent Roll Characteristics
Challenge:
As rolls of substrate material are consumed during printing, their diameter decreases, altering the tension that is applied to the material. The initial tension settings may no longer be accurate as the roll’s diameter changes, leading to uneven material feeding and potentially causing issues like misregistration or material wastage.
Solution:
To mitigate this challenge, tension control systems are equipped with automatic roll diameter measurement capabilities. These systems adjust the tension based on the changing roll diameter, ensuring that the material is fed through the machine with consistent tension, even as the roll depletes. This dynamic adjustment helps avoid tension imbalances and ensures uniform print quality.
5. Sensor Limitations
Challenge:
Tension sensors, while crucial for accurate tension control, are not infallible. They can suffer from calibration errors, wear and tear, or drift over time, leading to inaccurate readings. Miscalibrated sensors may result in improper tension adjustments, affecting the quality of the print job and the integrity of the material.
Solution:
Regular calibration and maintenance are essential to ensuring the accuracy and longevity of tension sensors. Additionally, the integration of redundant sensors—such as multiple sensors placed along the web path—can help improve the reliability of readings and provide more accurate data. This redundancy ensures that if one sensor fails, others can take over, minimizing the risk of tension-related issues.
6. Lack of Operator Expertise
Challenge:
Despite advances in automation, the expertise of the operator still plays a significant role in achieving optimal tension control. Operators must be familiar with the nuances of tension settings, machine operation, and substrate behavior. Lack of training or inexperience can result in improper tension adjustments, causing defects like warping, misalignment, or inconsistent print quality.
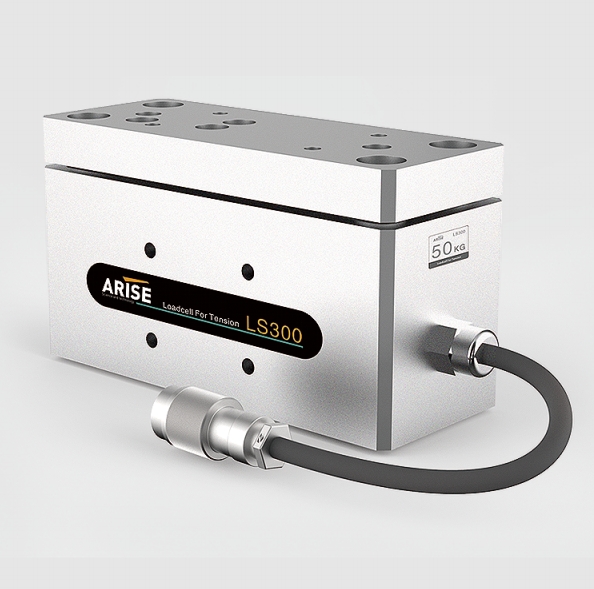
Solution:
To address this challenge, it is essential to invest in operator training and create user-friendly interfaces for the tension control systems. Training programs should cover not only the mechanics of tension control but also how to interpret sensor data and make adjustments. In addition, implementing intuitive, automated tension control systems that require minimal manual intervention can reduce the reliance on operator expertise while maintaining optimal performance.
7. Material Stress and Strain
Challenge:
During the printing process, materials such as paper or plastic are subjected to stress and strain. If the material is stretched too much, it can lead to distortions, stretching, or shrinking, which negatively affects the print quality. This is especially problematic in high-speed printing applications, where the material is under constant motion.
Solution:
Dynamic tension control systems equipped with stress and strain detection capabilities can help monitor the condition of the material in real-time. By adjusting the tension to minimize excessive stress, these systems can prevent the material from becoming overstretched or distorted. This ensures that the material maintains its integrity throughout the printing process, resulting in high-quality prints.
Benefits of Optimized Tension Control for Printing Inspection
Benefit | Description | Example |
Improved Print Quality | Consistent tension ensures precise print alignment and clarity. | Reduced registration errors in multi-color printing processes. |
Reduced Material Waste | Optimized tension prevents material slack and misprints, reducing waste. | Less paper or film wastage in flexographic printing. |
Increased Productivity | Stable tension reduces downtime and allows for continuous operation. | Faster setup and fewer pauses for re-adjustment in packaging printing. |
Cost Efficiency | Minimizes the need for reprints and ensures better material usage efficiency. | Reduction in cost due to less ink and paper wastage in commercial printing. |
Enhanced Process Control | Real-time adjustments of tension provide tighter process control. | Tension control systems allow for precision in rotary screen printing. |
Minimized Equipment Wear | Reduced strain on machinery, extending the lifespan of printing equipment. | Less wear on rollers and motors in high-speed inkjet printers. |
Higher Reliability | Reduces fluctuations in tension, ensuring consistent output. | Consistent print results on long production runs for labels. |
Wrap Up
Achieving accurate printing inspection depends on precise tension control throughout the high-speed printing process. Managing tension consistently across varying substrates, speeds, and environmental conditions presents several challenges. Through adopting advanced technologies such as automated tension control systems, real-time sensors, climate control measures, etc, can effectively address these challenges, enhancing quality assurance, ensuring smooth, high-quality production.