How to Address the Challenges in Web Guides for Handling Flexible and Stretchable Materials
Table of Contents
Web guides ensure that flexible materials such as films, fabrics, and foils are accurately fed through production lines without misalignment or distortion. However, handling flexible and stretchable materials presents unique challenges, as these materials are prone to movement, stretching, and deformation during high-speed operations. In this article, we focus on the key challenges faced in web guiding for handling flexible and stretchable materials and discuss the solutions that are currently being implemented to address these issues.
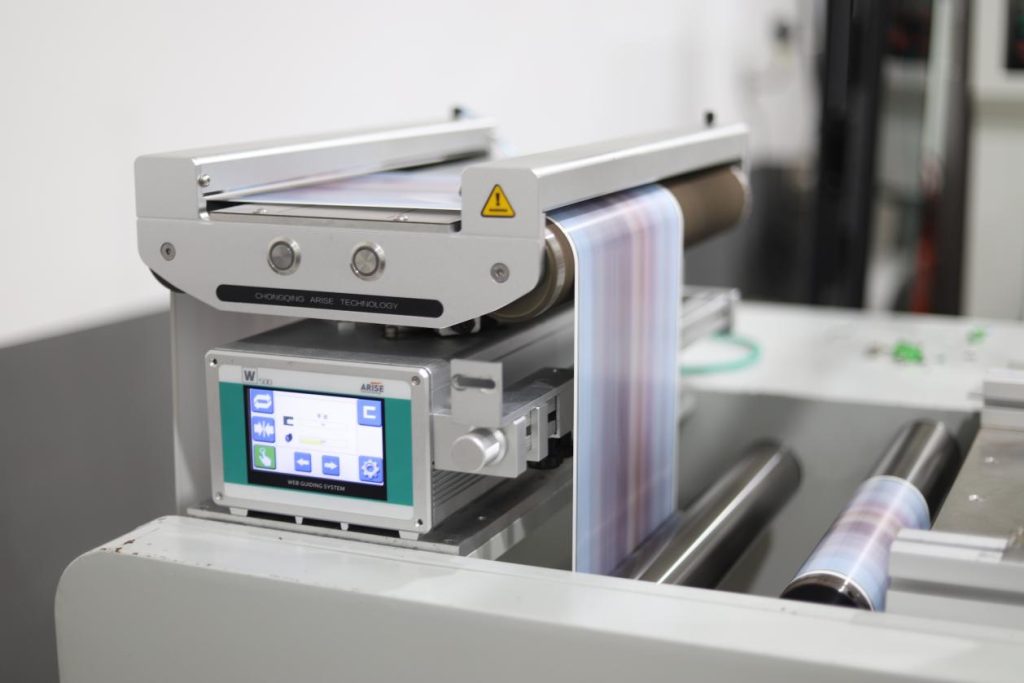
Why Web Guides for Handling Flexible and Stretchable Materials are Important
This chart illustrates why web guide equipment is crucial for managing flexible and stretchable materials, offering solutions that enhance efficiency, product quality, and operational reliability across various industries.
Importance | Explanation |
Improved Material Handling Precision | Web guides provide accurate control over the web’s path, ensuring that flexible and stretchable materials stay aligned during high-speed processing, which is crucial for maintaining product quality. |
Prevents Material Distortion | By controlling tension and alignment, web guides prevent unwanted stretching, deformation, and material distortion, ensuring the web remains stable throughout the production process. |
Increases Production Speed and Efficiency | With real-time adjustments and automation, web guides reduce the need for manual intervention, allowing for faster, more consistent production of flexible and stretchable materials. |
Minimizes Material Damage | Gentle handling mechanisms, like air flotation or vacuum rollers, prevent surface damage, tears, or scratches, crucial for delicate materials like films and fabrics. |
Reduces Operational Downtime | Automated web guides prevent common issues like misalignment, web breaks, and tension-related problems, reducing the likelihood of production stoppages and enhancing uptime. |
Ensures Consistent Product Quality | Web guides ensure uniformity in material flow, preventing defects such as wrinkles or misprints, which is especially important in industries like packaging, textiles, and electronics. |
Optimizes Material Utilization | By maintaining proper alignment and tension, web guides reduce material waste and ensure efficient use of resources, making the process more cost-effective. |
Adapts to Material Variability | Web guides equipped with sensors can adjust for changes in material properties, such as elasticity or thickness, ensuring consistent handling despite variability in the material. |
Supports High-Speed Operations | Web guides facilitate the smooth handling of flexible and stretchable materials at high speeds, maintaining material integrity and production efficiency. |
Ensures Safety in High-Precision Applications | In sectors like electronics and advanced manufacturing, web guides ensure that sensitive materials are processed without compromising safety, quality, or product integrity. |
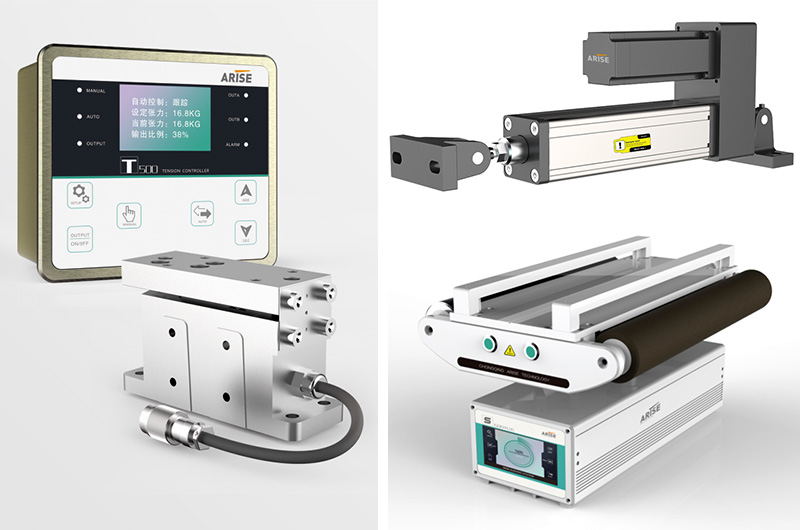
Challenges and Solutions in Web Guides for Handling Flexible and Stretchable Materials
1. Material Stretching and Deformation
Challenge
Flexible and stretchable materials are inherently more susceptible to deformation under tension. This can lead to misalignment or even tearing of the material. The challenge is to control the web tension in such a way that the material does not stretch excessively, while still maintaining a steady flow through the production line. Stretching, in particular, can lead to uneven material characteristics and defects, such as wrinkles, elongation, or thinning.
Solution
One of the key solutions to this problem is the use of differential speed rollers. These rollers are designed to vary the speed of the web’s movement in different areas of the machine. This ensures that the web remains under controlled tension, minimizing unwanted stretching. In addition, pre-stretching techniques, where the web is slightly stretched before being processed, can help to normalize the material’s elasticity. Moreover, closed-loop tension control systems that adjust the tension dynamically in response to real-time changes in the material’s properties can prevent over-stretching and maintain the integrity of the web.
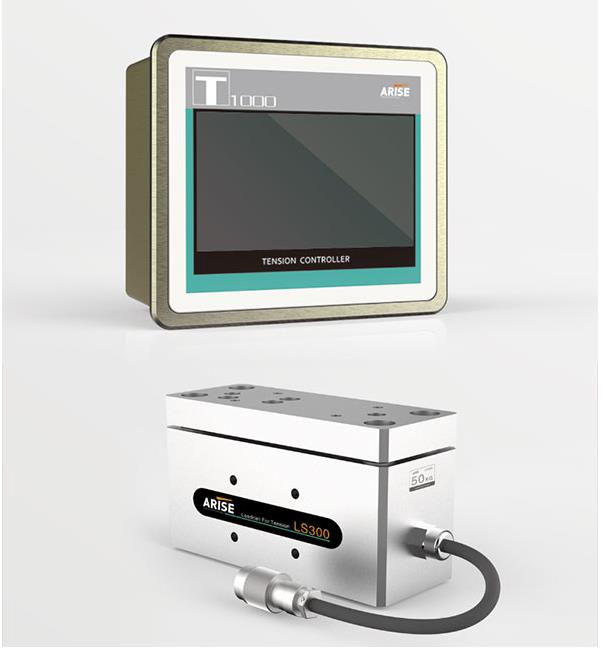
2. Web Misalignment and Tracking Issues
Challenge
Tracking flexible materials through a production line can be difficult. Unlike rigid webs, which are relatively stable, flexible and stretchable materials are prone to veering off course due to their low rigidity and tendency to distort. Misalignment can result in a host of issues, including wrinkles, uneven coatings, and poor-quality finishes.
Solution
Web guiding systems equipped with precision sensors and actuators are commonly used to address alignment issues. These systems detect deviations in the position of the web and automatically adjust rollers or other guiding components to keep the material on track. Edge guides and line sensors can also be integrated into the system to monitor the position of the web and provide real-time feedback for precise alignment. Additionally, active web guiding systems, which use vision or laser-based sensors to track the edges of the web, have proven effective in ensuring alignment at high speeds.
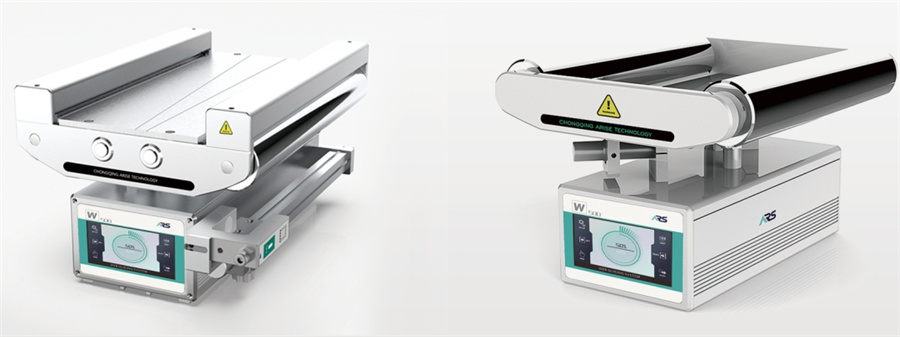
3. Surface Damage and Contamination
Challenge
Flexible and stretchable materials, particularly thin films and delicate fabrics, are highly susceptible to surface damage. Scratches, marks, or contamination caused by contact with handling equipment can result in defects or product failure, especially in industries like electronics, where precision is crucial. Any imperfection on the surface of the material can negatively impact its functionality, aesthetic appearance, or structural integrity.
Solution
To reduce surface damage, many web guide systems incorporate gentle handling mechanisms, such as air flotation or vacuum-assisted rollers. These systems support the web without making direct contact, thus reducing the risk of surface damage. Soft-touch rollers and non-abrasive materials are also used to minimize wear on the web. Additionally, cleanroom environments with strict contamination control measures are employed in industries like electronics and packaging to ensure the material’s surface remains pristine during handling.
4. Web Tension Control and Stability
Challenge
Maintaining a consistent web tension is crucial when handling flexible and stretchable materials. If the tension is too high, the web may stretch or tear, while too low tension may cause slippage, leading to misalignment or operational downtime. Achieving a balance between sufficient tension to maintain control and preventing overstretching is one of the most significant challenges in web guiding.
Solution
Real-time web tension control systems, often based on load cells or force sensors, are used to measure and adjust the tension as the web moves through the production process. These systems feed data into a central control system that can dynamically adjust the tension to keep it within optimal limits. Closed-loop control systems also ensure that adjustments are made instantaneously to compensate for any variations in the web’s properties, such as changes in thickness or elasticity. Furthermore, servo-driven rollers and high-precision motor control systems provide finer control over tension, allowing for greater flexibility in managing delicate webs.
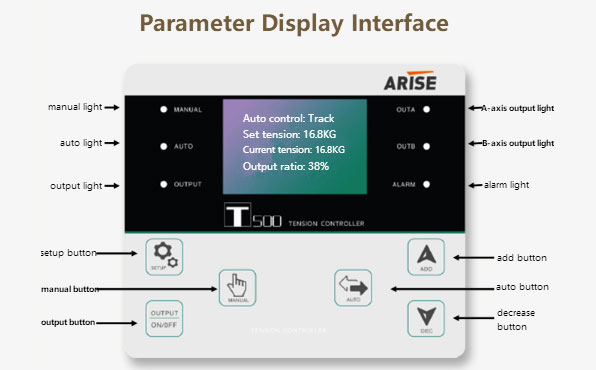
5. Web Breaks and Downtime
Challenge
Web breaks are a common and costly issue in manufacturing, particularly when dealing with flexible materials that are prone to stretching or tearing. These breaks can lead to significant downtime, requiring manual intervention to restart the production line. For stretchable webs, breaks can occur due to excessive tension, misalignment, or even minor damage to the material during handling.
Solution
To minimize the risk of web breaks, automated fault detection systems are being integrated into web guide systems. These systems use sensors, such as cameras or acoustic sensors, to detect irregularities in the web’s movement and can trigger automatic adjustments to prevent breaks. In some cases, automatic tension release mechanisms are employed to relieve pressure in the event of a potential break. Additionally, redundant systems, such as backup rollers or emergency stops, are in place to minimize downtime and allow for rapid recovery when breaks do occur.
6. High-speed Processing
Challenge
In many modern manufacturing processes, flexibility and stretchability must be managed at high speeds. The faster the web moves, the more challenging it becomes to maintain control over tension, alignment, and material integrity. At high speeds, even minor deviations can result in significant defects, which may be difficult or impossible to correct.
Solution
To address the challenges posed by high-speed operations, high-frequency feedback systems are employed. These systems use sensors and advanced algorithms to monitor and adjust the web’s position, tension, and other parameters in real-time, ensuring consistent material handling even during rapid processing. Advanced actuators and servo-driven systems are used to make fine adjustments at high speeds, while adaptive control algorithms continuously fine-tune the settings to accommodate varying web properties and conditions.
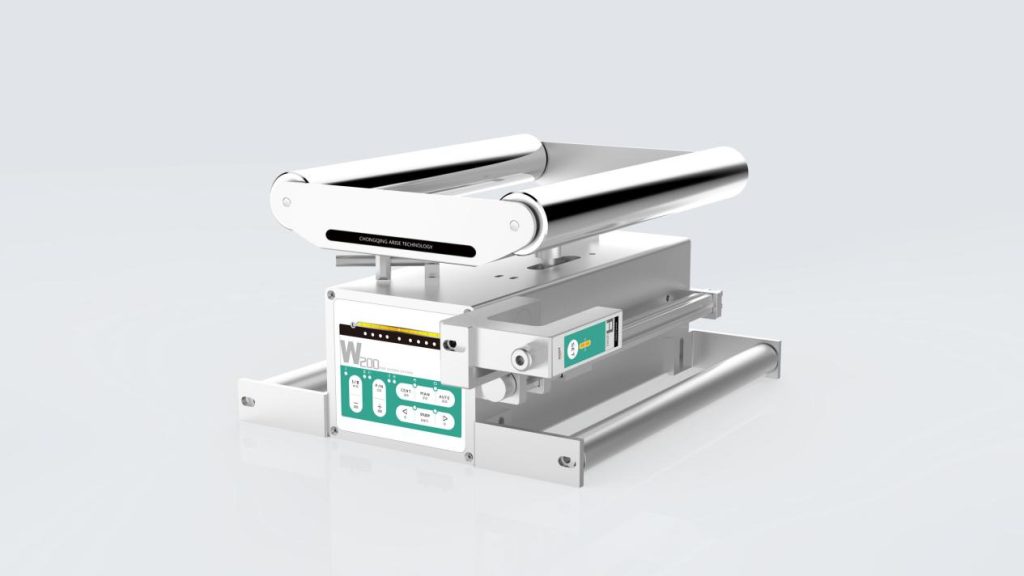
7. Material Variability
Challenge
Flexible and stretchable materials often exhibit variability in terms of thickness, elasticity, and composition. This can make it difficult to predict how the material will behave under tension or in different processing conditions. Variations in material properties can result in inconsistent web handling, leading to defects or production delays.
Solution
To handle material variability in web guiding, advanced sensor technologies are increasingly being used to gather real-time data about the web’s properties. Smart web guides equipped with these sensors can detect changes in thickness, elasticity, or surface characteristics and make instantaneous adjustments to ensure consistent handling. AI and machine learning algorithms can be used to predict how the material will behave in different conditions, allowing for proactive adjustments to the web guide system.
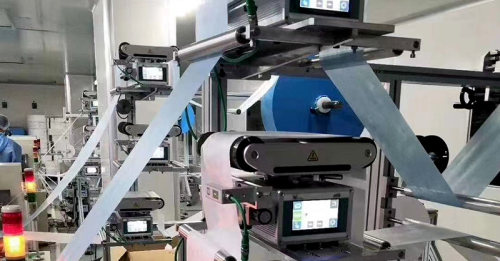
Applications of Web Guides in Flexible Material Industries
This chart demonstrates the versatility of web guides across multiple industries, emphasizing their critical role in enhancing precision and efficiency when working with flexible materials.
Industry | Application |
Packaging | Ensures precise alignment and tension control for consistent printing, lamination, and sealing processes on films and foils. |
Textiles | Maintains proper alignment of fabrics during processes like dyeing, printing, and finishing to prevent wrinkles and distortions. |
Printing | Prevents misalignment, wrinkles, and smudging during high-speed printing on flexible and stretchable materials. |
Laminates | Maintains uniformity during the bonding of multiple layers, such as adhesives and protective films. |
Medical Products | Guides flexible materials used in medical devices or packaging, ensuring sterile and precise handling during production. |
Food Processing | Aligns and controls food-grade films for packaging and wrapping applications in automated systems. |
Photovoltaics | Manages thin, flexible solar panels and films during manufacturing processes, maintaining integrity and alignment. |
Construction Materials | Guides flexible membranes and films used in waterproofing, roofing, and insulation during production. |
Labeling | Handles stretchable or thin label materials to ensure proper alignment and application on products or packaging. |
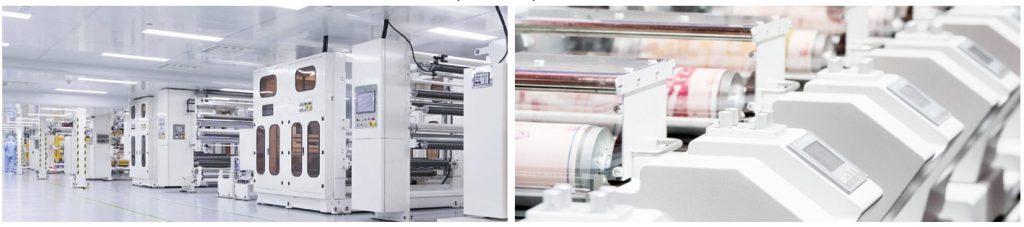
In summary, handling flexible and stretchable materials in web guiding applications presents a range of challenges, including material stretching, misalignment, surface damage, tension instability etc. However, with advancements in automation and web guide sensor technology, gentle handling mechanisms, high-frequency feedback systems, smart control systems, etc, these challenges can be effectively addressed and manufacturing industries can enhance the accuracy, efficiency and reliability of their web guide systems, ensuring high-quality products and minimizing operational downtime.