How to Address the Challenges in Printing Inspection of Flexible Packaging
Flexible packaging has become an essential element of modern industries due to its lightweight nature, adaptability, and cost-efficiency. However, ensuring high-quality printing on these materials presents unique challenges, primarily due to their composition, diverse applications, and the demands of fast-paced production environments. Printing inspection plays a pivotal role in maintaining brand integrity, meeting regulatory requirements, and delivering a superior consumer experience.
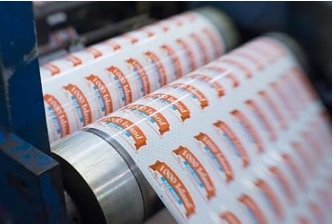
Table of Contents
Challenges in Printing Inspection of Flexible Packaging
1. Material Variability
Flexible packaging is typically made from a combination of materials such as plastic films, foils, and paper. Each material behaves differently during the printing process. For instance, plastic films may expand or contract due to temperature changes during printing, leading to misalignment of colors or design elements. Similarly, foils can reflect light unevenly, complicating the detection of print defects. The variability in material properties demands highly adaptive inspection systems capable of accommodating diverse substrates.
2. Complex Printing Designs
With the increasing need for vibrant and intricate designs to enhance brand recognition, flexible packaging often involves multi-color printing, fine patterns, and high-resolution imagery. These complexities make it challenging to detect imperfections such as color mismatches, blurs, and registration errors. Traditional inspection methods may fail to capture subtle flaws that could compromise the visual appeal of the packaging.
3. High-speed Production
Modern production lines for flexible packaging operate at extremely high speeds to meet market demands. Ensuring thorough inspection without slowing down production is a significant challenge. Inspection systems must strike a balance between speed and accuracy, as missing a defect or halting production for false positives can result in substantial losses.
4. Wrinkles and Deformations
Flexible packaging is prone to wrinkles and deformations during handling and printing. These distortions can obscure defects or create false positives in automated inspection systems. Advanced imaging and pattern recognition algorithms are needed to differentiate between genuine defects and material inconsistencies caused by physical handling.
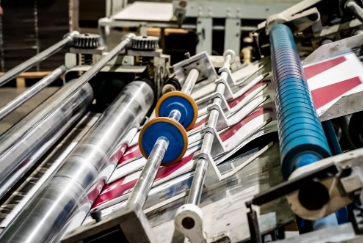
5. Transparency and Opacity Issues
Many flexible packaging materials are transparent or semi-transparent, making it difficult for traditional inspection systems to accurately assess print quality. Similarly, opaque materials may require specialized lighting conditions to reveal defects such as smudges or uneven coatings. Tailored inspection setups with controlled illumination and imaging techniques are often necessary to overcome these challenges.
6. Dynamic Consumer Expectations
Consumers increasingly demand eco-friendly and personalized packaging solutions, which has led to the use of biodegradable materials and custom designs. These trends introduce additional variables into the printing process, requiring inspection systems to adapt to evolving material properties and design complexities.
7. Cost Constraints
Implementing advanced inspection technologies can be costly, particularly for small and medium-sized manufacturers. Many businesses face a dilemma between investing in state-of-the-art inspection systems and maintaining competitive pricing. This trade-off often results in compromises in inspection accuracy, increasing the risk of defective products reaching the market.
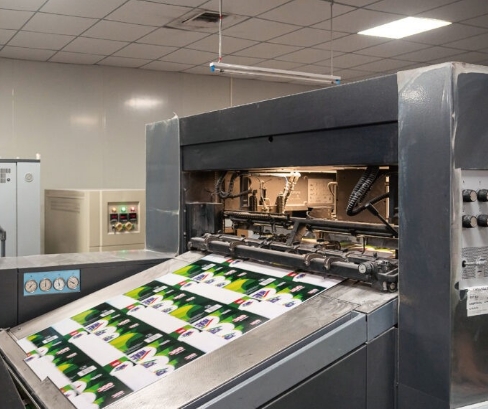
Effective Solutions to Address the Challenges in Printing Inspection of Flexible Packaging
1. Advanced Vision Systems for Defect Detection
High-resolution cameras and machine vision systems are essential for detecting subtle defects such as color inconsistencies, misalignments, and smudges. These print inspection systems use advanced imaging technologies that capture detailed visuals of printed materials, enabling manufacturers to identify and rectify defects in real time. Coupling these systems with machine learning algorithms enhances their ability to recognize patterns, detect anomalies, and adapt to varying print designs and materials.
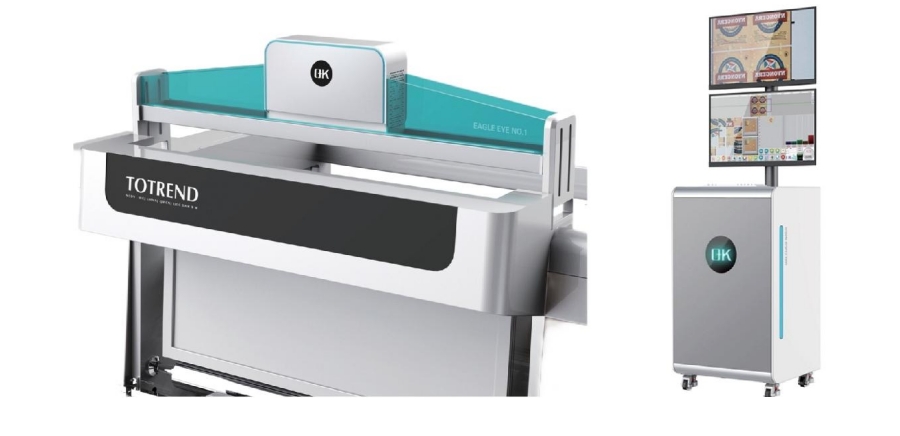
2. Dynamic Color Management Systems
Flexible packaging often features complex, multicolor designs that require precise color accuracy. To address this, dynamic color management systems have been developed to monitor and adjust colors throughout the printing process. These systems compare printed colors against predefined standards and automatically make corrections, ensuring that brand guidelines are consistently met.
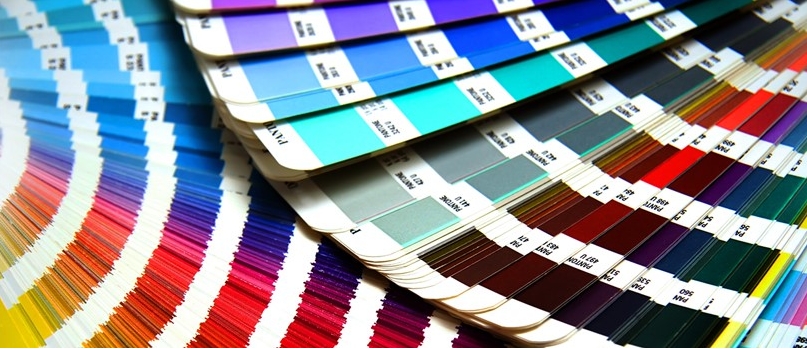
3. Lighting Solutions for Diverse Materials
Reflective, transparent, and opaque materials used in flexible packaging pose significant challenges for inspection. To overcome this, inspection systems integrate specialized lighting setups, such as polarized, diffuse, and multi-angle illumination. These lighting solutions minimize glare, enhance the visibility of defects, and ensure accurate inspection across various substrates.
4. Real-Time Monitoring and Feedback Systems
Integrating web inspection systems for printing with production lines enables real-time monitoring and feedback. Smart sensors and data analytics tools analyze printing quality and provide immediate alerts for defects. This allows operators to take corrective actions without halting production, minimizing downtime and reducing waste.
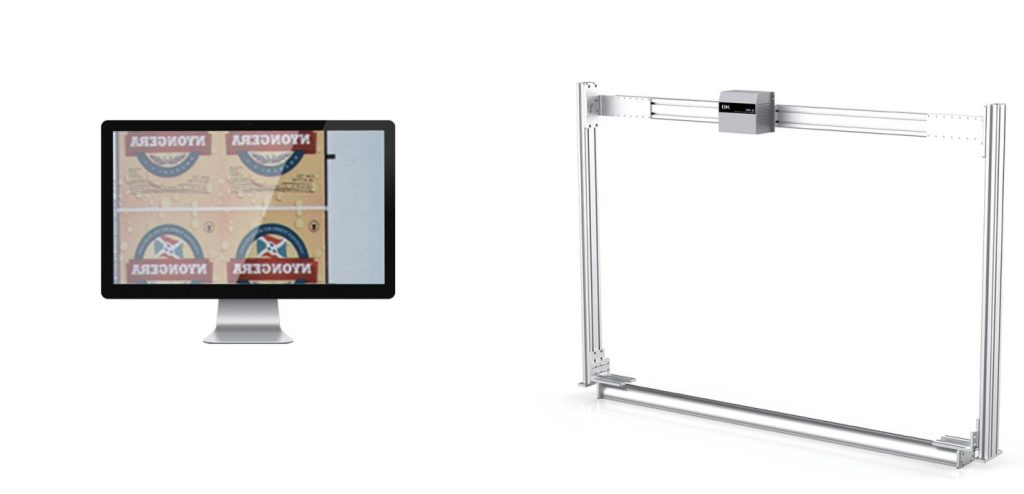
5. Adaptable Inspection for Sustainable Packaging
As the industry shifts towards eco-friendly and biodegradable materials, inspection systems must adapt to the unique characteristics of these substrates. Advanced software algorithms and flexible hardware configurations are being developed to accommodate the variability of sustainable materials, ensuring reliable defect detection and print quality assurance.
6. Integration of Digital Printing and Inspection
Digital printing technologies, combined with automated 100% print quality inspection systems, offer unmatched precision and flexibility for flexible packaging. This integration allows for instant adjustments, such as correcting misprints or modifying designs on the fly. The synergy between digital printing and inspection ensures a seamless production process with minimal waste.
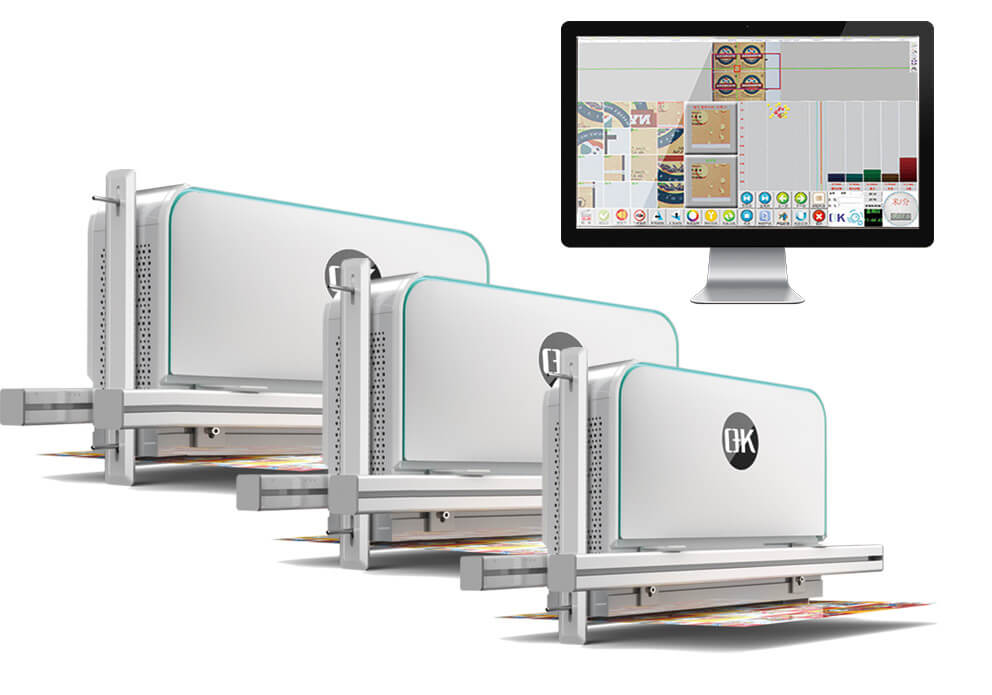
7. Collaboration Between Technology Providers and Manufacturers
A collaborative approach between inspection technology providers and flexible packaging manufacturers is essential for developing tailored solutions. Customizing inspection systems to align with specific production needs ensures optimal performance, cost-efficiency, and scalability.
Future Trends in Printing Inspection of Flexible Packaging
Trend | Description | Benefits |
AI and Machine Learning | Leveraging AI to detect patterns, classify defects, and predict potential issues. | Improves defect detection accuracy and enables predictive maintenance. |
Cloud-Based Quality Management | Centralized data storage and real-time analysis through cloud technology. | Facilitates collaboration, trend analysis, and quality consistency across production sites. |
Augmented Reality (AR) | AR tools providing visual overlays to identify defects and their root causes. | Enhances operator efficiency and reduces downtime during inspections. |
Advanced Imaging Systems | High-resolution cameras, 3D vision, and multi-spectral imaging for improved defect detection. | Enables accurate inspection across diverse materials and intricate designs. |
Blockchain Integration | Using blockchain for traceability and compliance in quality assurance. | Enhances transparency, trust, and accountability across the supply chain. |
Predictive and Prescriptive Analytics | Data-driven approaches to forecast and prevent defects. | Reduces waste and optimizes production efficiency. |
Automation and Robotics | Robotic systems equipped with advanced sensors and cameras for automated inspection. | Increases speed and consistency in high-volume production lines. |
Customization for Variable Data Printing | Custom printing Inspection system tailored for personalized designs and variable data, like QR codes and barcodes. | Ensures precision in customized and short-run productions. |
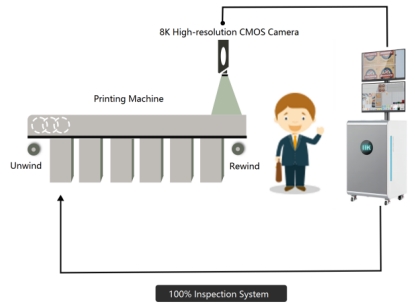
Overall, through adopting these advanced solutions, the flexible packaging industry can overcome the challenges of printing inspection, ensuring high-quality output while meeting the demands of modern consumers.