How to Achieve Precision Tension Control in High-Speed Processes
Table of Contents
In high-speed manufacturing and processing industries such as the textile industry, metal processing, paper production, advanced material fabrication, etc, precision tension control is a critical factor that ensures product quality, operational efficiency, and machinery longevity. This article explores the importance of precision tension control in high-speed processes, the challenges faced, and the innovative solutions that are driving improvements in tension control for high-speed processes.
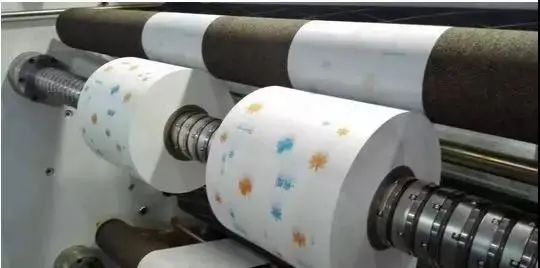
The Importance of Precision Tension Control in High-speed Processes
Here’s a chart summarizing the importance of precision tension control in high-speed processes by highlighting its effects on product quality, operational efficiency, and machinery longevity.
Key Aspect | Description | Impact |
Product Quality | Ensures consistent product characteristics by preventing defects like wrinkles, stretching, or tearing in high-speed operations. | Higher quality output, reduced waste. |
Operational Efficiency | Reduces machine downtime by preventing disruptions caused by tension fluctuations. | Increased productivity, lower operational costs. |
Machinery Longevity | Balances the forces on machinery components, reducing wear and tear and preventing damage from excessive or insufficient tension. | Extended machinery life, lower maintenance costs. |
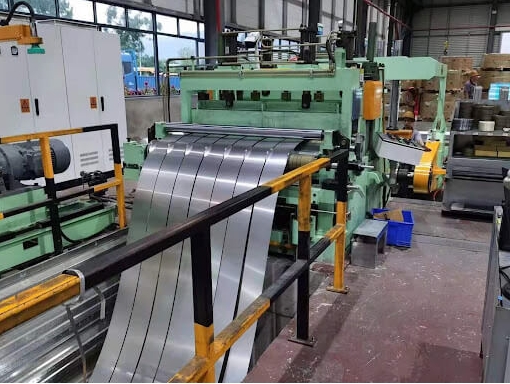
Challenges in Precision Tension Control for High-speed Processes
1. High-Speed Dynamics
- Description: Maintaining consistent tension becomes increasingly difficult as the speed of the process increases. Rapid acceleration, deceleration, and the high inertia of moving parts can cause sudden fluctuations in tension.
- Impact: These fluctuations can lead to instability in the process, resulting in defects, material breakage, or machine malfunctions.
2. Material Variability
- Description: Different materials have varying properties such as elasticity, thickness, and surface texture, which all influence tension. This variability becomes more pronounced when processing composite materials or dealing with inconsistent material batches.
- Impact: Inconsistent tension due to material variability can result in product defects, such as wrinkles, uneven surface finishes, or structural weaknesses.
3. Environmental Factors
- Description: External conditions like temperature, humidity, and air pressure can affect both the material being processed and the machinery. These environmental factors can cause the material to expand, contract, or behave unpredictably.
- Impact: Fluctuations in environmental conditions can lead to variations in tension, making it difficult to maintain stability and consistency in the process.
4. Integration with Digital Systems
- Description: As industries move towards greater automation and smart manufacturing, integrating tension control systems with digital platforms and IoT devices becomes crucial. However, achieving real-time data collection, analysis, and automatic adjustment presents technical challenges.
- Impact: Inadequate integration can result in delayed or inaccurate adjustments, compromising precision and potentially causing disruptions in high-speed processes.
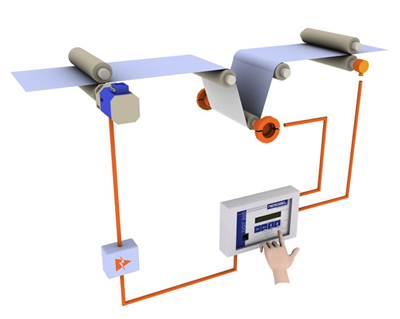
5. Wear and Tear on Equipment
- Description: The mechanical components involved in tension control, such as rollers, bearings, and actuators, experience significant wear and tear due to continuous high-speed operation. Over time, this can lead to reduced performance and increased maintenance requirements.
- Impact: Deterioration of equipment can lead to inconsistent tension control, increasing the likelihood of process interruptions and quality issues.
6. Complexity in Multi-stage Processes
- Description: In processes involving multiple stages, such as in textiles or film production, maintaining consistent tension across different stages is complex. Each stage may require different tension settings, and transitions between stages can introduce variations.
- Impact: Inconsistent tension across stages can lead to defects that are not immediately apparent, resulting in significant material waste and rework.
These challenges highlight the complexity of maintaining precise tension control in high-speed processes and underscore the need for advanced solutions to mitigate these issues.
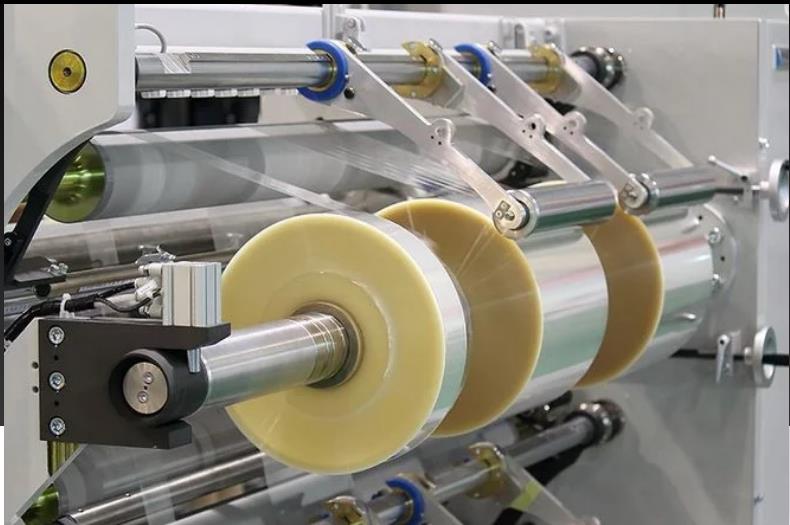
Innovative Solutions for Precision Tension Control in High-speed Processes
Innovative solutions for precision tension control are continuously evolving to address the challenges of maintaining stability and consistency in high-speed processes.
1. Advanced Sensing Technologies
- Description: Modern tension control systems are equipped with high-precision tension sensors that can detect minute changes in tension with exceptional accuracy. These sensors, including load cells, laser displacement sensors, and strain gauges, provide real-time feedback on tension levels.
- Benefit: Immediate detection of tension variations allows for prompt adjustments, ensuring consistent control even in high-speed processes.
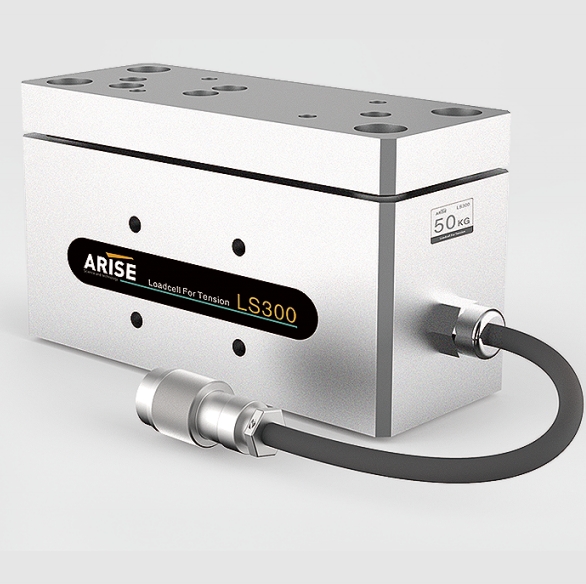
2. Closed-Loop Control Systems
- Description: Closed-loop systems continuously monitor tension and automatically adjust it based on real-time data. These systems use feedback loops to compare the actual tension with the desired setpoint and make instant corrections.
- Benefit: By minimizing human intervention, closed-loop systems enhance precision and responsiveness, crucial for maintaining stability in high-speed operations.
3. Digital Twins and Predictive Analytics
- Description: Digital twins are virtual replicas of physical systems that allow manufacturers to simulate tension behavior under various conditions. By analyzing this data, predictive analytics can anticipate potential issues and adjust the tension control system preemptively.
- Benefit: This predictive approach reduces the likelihood of disruptions and defects, optimizing the tension control process and improving overall efficiency.
4. Smart Rollers and Actuators
- Description: Innovations in roller and actuator technology have led to the development of smart components that can dynamically adjust tension in real-time. These components are embedded with sensors and control mechanisms that respond to changes in load conditions.
- Benefit: Smart rollers and actuators provide a more adaptive and responsive tension control solution, reducing the risk of tension-related defects and enhancing process stability.
5. Integration with Industry 4.0 Platforms
- Description: As part of the Industry 4.0 movement, tension control systems are increasingly being integrated with IoT devices, cloud-based platforms, and AI-driven analytics. This integration enables more sophisticated monitoring, remote control, and optimization of tension across various stages of the manufacturing process.
- Benefit: Enhanced connectivity and data analysis capabilities lead to more efficient tension control, reduced downtime, and improved product quality.
6. Adaptive Control Algorithms
- Description: Adaptive control algorithms are designed to adjust tension control parameters dynamically based on real-time process conditions. These algorithms learn from historical data and adapt to changes in material properties, environmental conditions, and machine performance.
- Benefit: By continuously optimizing the control parameters, adaptive algorithms ensure that tension remains consistent even in the face of variability, leading to more reliable and efficient high-speed processes.
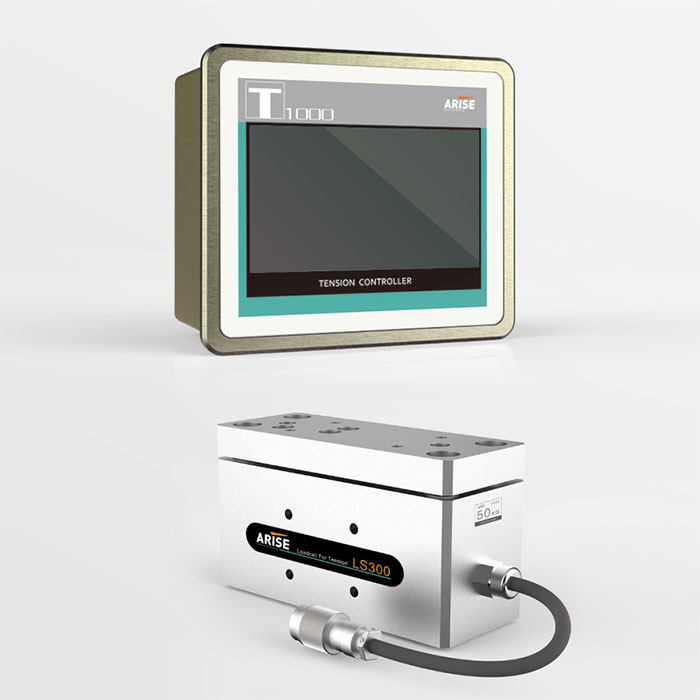
7. Automated Tension Calibration Systems
- Description: Automated calibration systems can regularly recalibrate tension control settings without interrupting the production process. These systems use precise measurements and adjustments to maintain optimal tension levels.
- Benefit: Regular calibration ensures long-term accuracy and consistency in tension control, reducing the risk of drift and associated defects.
8. Multi-Zone Tension Control
- Description: Multi-zone tension control systems divide the process into different zones, each with its own tension control settings. These zones can be individually monitored and adjusted to maintain the correct tension at every stage of the process.
- Benefit: This approach is particularly useful in complex, multi-stage processes, ensuring that tension is optimized at every point, leading to higher-quality output and reduced waste.
Overall, Precision tension control is a linchpin in the success of high-speed manufacturing and processing operations. The challenges are significant, but the solutions are rapidly advancing, driven by advancements in sensing technologies, automation, and digital integration. These innovative solutions are helping industries achieve greater precision in tension control, enhancing the quality and efficiency of high-speed processes.