How to Achieve Effective Tension Control in Applications with Rapid Speed Changes
Table of Contents
In industrial processes that require precise handling of materials, such as printing, textile manufacturing, film processing, and packaging, maintaining precision tension control is critical. Rapid speed changes in these applications pose a significant challenge as they can lead to material defects, reduced efficiency, or machine damage. This article explores advanced solutions for tension control in environments where rapid speed variations are a constant challenge.
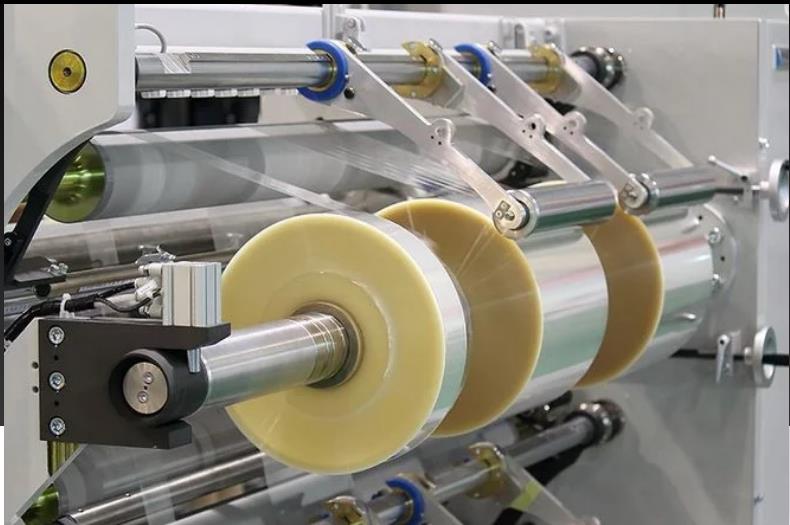
Why Effective Tension Control is Important in Applications with Rapid Speed Change
Effective tension control is crucial in applications involving rapid speed changes because it ensures the stability, quality, and efficiency of the process.
- Prevents Material Breakage or Damage: Rapid speed changes can cause sudden fluctuations in tension. Without effective tension control, this can lead to material breakage, stretching, or distortion, especially in delicate materials like films, textiles, or paper. Consistent tension ensures materials remain intact under varying speeds.
- Maintains Process Stability: In high-speed applications, like printing or web handling, rapid changes in speed can lead to uneven tension distribution. Effective tension control systems continuously adjust to ensure that tension remains within optimal limits, preventing disruptions and maintaining smooth operation.
- Improves Product Quality: In processes like coating, laminating, or printing, maintaining consistent tension is key to ensuring uniformity and quality. Fluctuating tension during speed changes can result in defects such as wrinkles, uneven coatings, or misalignment, which can compromise the product’s quality.
- Reduces Equipment Stress and Wear: Machines operating at varying speeds without proper tension control experience additional stress. This increases the wear on components such as rollers, motors, and gears. Effective tension control reduces this stress, helping to prolong the lifespan of the equipment.
- Enhances Safety: Rapid speed changes without tension control can create hazards, such as equipment failure or accidents. For instance, excess tension can lead to snapping or jerking motions, posing risks to operators and machinery. Effective tension control ensures that the system operates within safe limits, reducing the likelihood of dangerous situations.
- Maximizes Efficiency: When tension is properly controlled during speed changes, it minimizes downtime and reduces the need for rework caused by material defects or misalignments. This leads to more efficient production processes, maximizing throughput while minimizing waste.
- Ensures Continuous Operation: In industries like textiles or manufacturing, continuous operations are crucial. Effective tension control ensures that changes in speed do not interrupt the workflow, allowing the system to keep running without disruptions that could cause delays or defects.
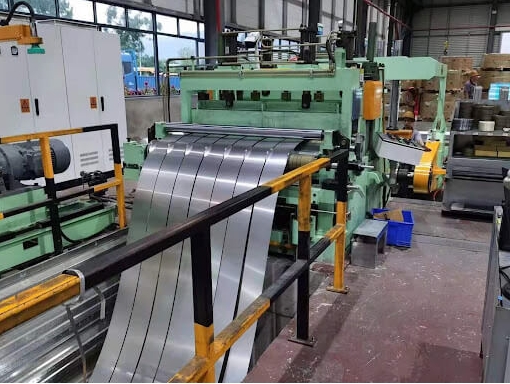
Challenges of Tension Control During Rapid Speed Changes
This chart highlights the key challenges that arise in tension control during rapid speed changes in manufacturing processes.
Challenge | Description |
Inertia Effects | Sudden speed changes cause delays in tension adjustments due to the inertia of moving rolls and materials. |
Material Deformation | Rapid speed fluctuations can cause stretching, slipping, or tearing of delicate materials. |
Dynamic Load Variability | Speed changes lead to fluctuations in mechanical loads, making tension stabilization more complex. |
Synchronization Issues | Coordinating the speed of multiple components (motors, rollers, etc.) during speed changes can be difficult. |
Heat Generation | Rapid transitions in speed generate heat, which may alter the properties of materials, affecting tension. |
Control Lag | The time delay in adjusting tension after a speed change leads to inconsistent tension control. |
Misalignment | Speed variations may cause material misalignment, resulting in uneven tension distribution across the width. |
Machine Wear and Tear | Continuous rapid speed changes increase mechanical strain on machines, leading to accelerated wear and potential breakdowns. |
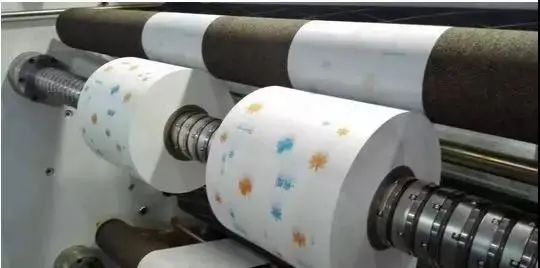
Key Solutions for Effective Tension Control in Applications with Rapid Speed Changes
1. High-Precision Tension Sensors
Accurate, real-time monitoring is fundamental for maintaining tension consistency during speed changes. High-precision tension sensors can detect even small variations in tension, enabling quick adjustments to the control system. Types of sensors include:
- Load Cells: Measure the direct force applied to the material, providing immediate feedback on tension levels.
- Ultrasonic or Laser Sensors: Detect material position and alignment, indirectly assessing tension and ensuring uniformity across the material.
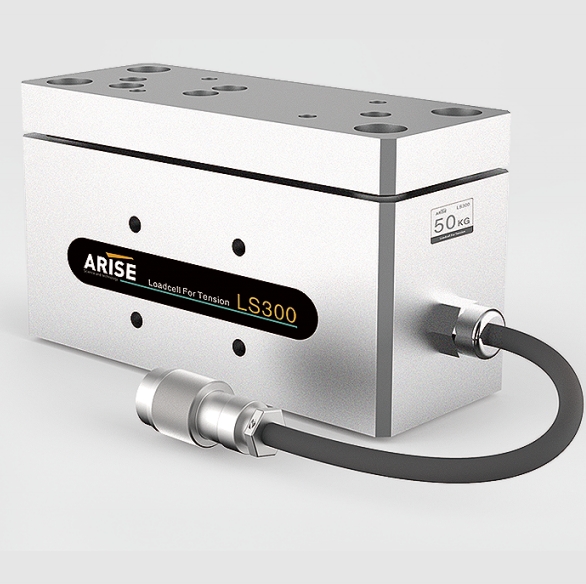
2. Adaptive Control Systems
Traditional controllers may struggle to adjust to rapid changes in machine speed. Adaptive tension control systems, including Model Predictive Control (MPC) and Fuzzy Logic, are designed to respond dynamically to fluctuations:
- PID Controllers: These are widely used for steady operations, but can also be adapted for dynamic conditions to stabilize tension.
- Model Predictive Control (MPC): This advanced algorithm predicts future changes in tension based on real-time feedback, proactively adjusting system parameters.
- Fuzzy Logic Control: Ideal for non-linear processes, fuzzy logic controllers can handle complex, unpredictable changes in tension during speed shifts.
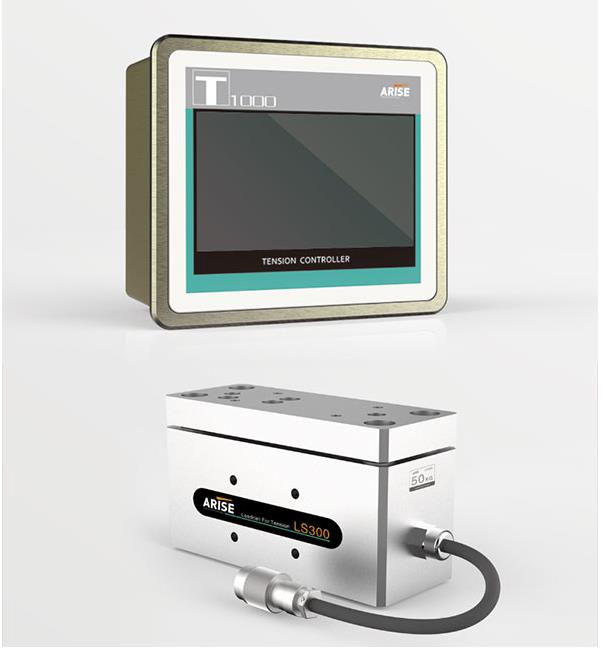
3. Servo Motors and Actuators
Servo-driven actuators offer precise control over tensioning devices, such as rollers and brakes. These systems adjust tension quickly in response to changes in speed and are particularly effective in high-speed, high-precision environments. Servo motors, when combined with encoders, ensure accurate positioning and torque control, allowing for smooth, consistent tension even during rapid speed transitions.
4. Variable Frequency Drives (VFDs)
Variable Frequency Drives (VFDs) are used to regulate the speed of electric motors, offering flexibility in handling rapid speed changes. By adjusting motor speed in real-time, VFDs ensure synchronization between machine speed and material tension. Regenerative VFDs can also capture and reuse energy during deceleration, improving energy efficiency while maintaining consistent tension.
5. Flywheel Energy Storage Systems
Flywheels store kinetic energy during speed changes and release it when needed, smoothing out rapid fluctuations in speed. This system is especially beneficial in high-speed operations where sudden accelerations or decelerations would otherwise cause significant tension variations. By acting as an energy buffer, flywheels help maintain a stable tension profile, reducing the risk of material stretching or breaking.
6. Web Guide Systems
Web guide systems are critical for keeping materials properly aligned during rapid speed changes, preventing tension fluctuations due to misalignment. These systems use edge sensors, motors, and actuators to monitor and adjust the material’s position continuously, ensuring that tension is evenly distributed across the material width. Proper alignment is essential to prevent wrinkles, tears, or inconsistent processing.
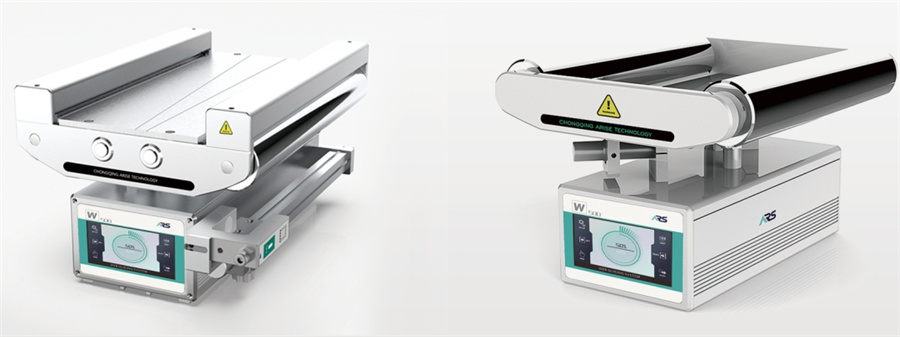
7. Non-Contact Tensioning Systems
For delicate or sensitive materials, non-contact tensioning systems, such as pneumatic or magnetic tensioners, offer a precise and gentle approach. These systems use air pressure or magnetic fields to adjust tension without physically touching the material, minimizing the risk of damage during high-speed operations. Non-contact systems are especially valuable for fragile films, textiles, or other materials that are easily deformed.
8. Integration of IoT and Data Analytics
The integration of Internet of Things (IoT) devices and data analytics enhances real-time monitoring and decision-making. IoT sensors continuously gather data on tension, speed, and other operational parameters, feeding this information into cloud-based systems for analysis. Predictive analytics and machine learning can then be used to anticipate tension changes, optimize settings, and improve overall system performance, particularly during rapid speed changes.
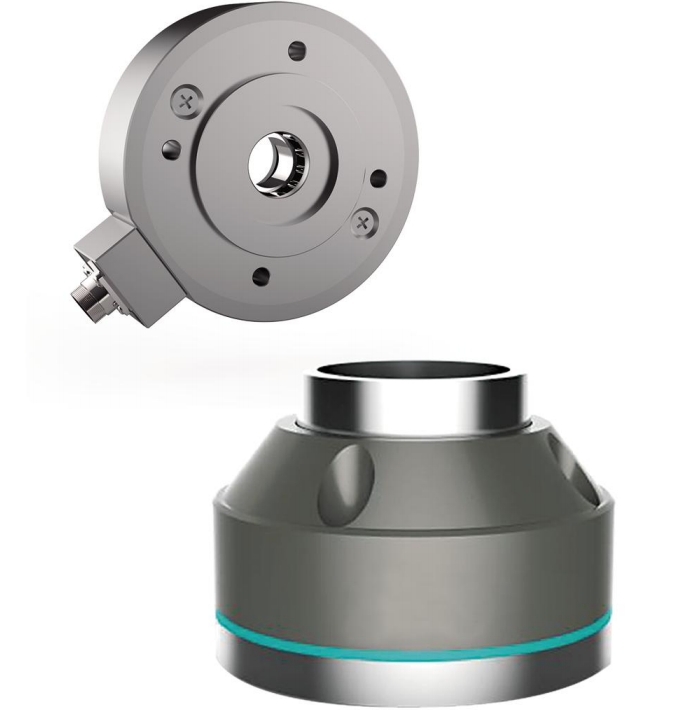
In summary, achieving effective tension control in applications involving rapid speed changes requires a combination of advanced technologies and precise control mechanisms. High-precision sensors, adaptive control systems, servo motors and VFDs are key components in managing tension during dynamic speed transitions. Additionally, emerging technologies like IoT integration and flywheel systems are further enhancing tension control capabilities, ensuring optimal material handling, quality, and efficiency in fast-paced industrial environments.