How Printing Inspection Systems Handle Different Materials
Printing inspection systems are crucial for ensuring that printed products across various industries meet the highest standards of quality. As different materials have unique characteristics, printing inspection systems are designed to adapt to these properties, maintaining accuracy and efficiency throughout the printing process.
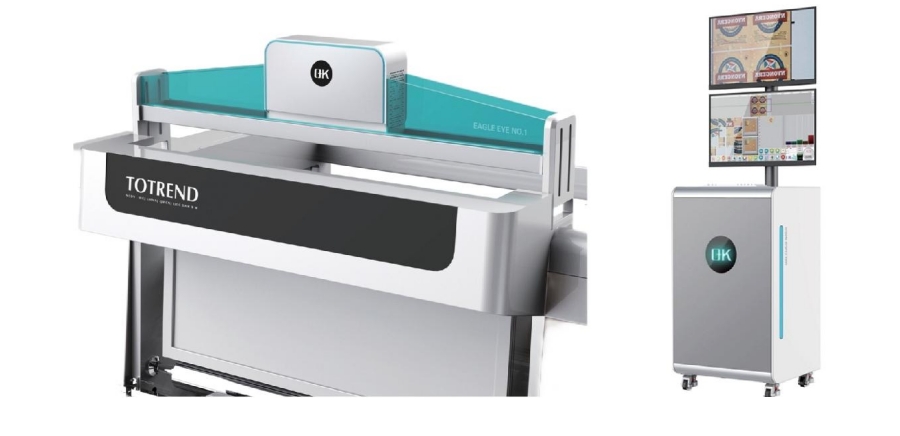
Challenges in Handling Different Materials During the Printing Process
The printing process, especially in industrial and commercial settings, involves a wide range of materials, each presenting its own unique challenges. Whether it’s paper, plastic, metal, or textiles, printing systems must adapt to ensure that print quality remains consistent and defect-free.
This chart provides an overview of the specific challenges encountered when handling different materials during the printing process.
Material | Challenges | Details |
Paper | Ink Absorption Variability | Different paper types absorb ink at varying rates, leading to inconsistent print quality. |
Curling and Warping | Paper can curl or warp due to humidity, affecting ink application and alignment. | |
Fragility | Thin or low-quality paper can tear or crumple during high-speed printing. | |
Plastic and Film | Flexibility and Stretching | Plastic stretches during printing, causing misalignment in complex designs. |
Surface Properties | Glossy or smooth surfaces require precise control to ensure even ink application. | |
Static Electricity | Plastic materials can attract dust or cause ink smearing due to static buildup. | |
Metal | Reflective Surface Issues | The reflectivity of metal surfaces creates glare, complicating inspection and defect detection. |
Ink Adhesion | Special inks are required for metals to ensure long-lasting adhesion without smudging or peeling. | |
Surface Imperfections | Irregularities like dents or scratches in metal surfaces can interfere with smooth ink application. | |
Textiles | Stretch and Movement | Fabric stretching during printing leads to misalignment or uneven color application. |
Surface Texture | Textured surfaces, such as woven fabrics, make even ink absorption challenging. | |
Ink Saturation | Managing the correct amount of ink to prevent bleeding or fading on fabric is difficult. | |
Glass and Ceramics | Surface Fragility | These materials are prone to damage from excessive pressure during printing. |
Smoothness and Ink Adhesion | Smooth surfaces like glass require specialized inks and techniques for proper adhesion. | |
Heat Resistance | Excessive heat during post-print curing may cause glass or ceramics to crack or break. | |
Multilayer & Composite Materials | Layered Construction | Ensuring accuracy across multiple layers without distorting or damaging them is challenging. |
Material Mismatch | Printing on mixed material layers (e.g., plastic, foil, paper) requires different adhesion techniques across layers. | |
Environmental Factors | Temperature and Humidity | Varying temperatures and humidity levels can cause materials like paper to shrink or curl, affecting print consistency. |
Ink Drying Time | Non-porous materials like plastic and metal require longer drying times, making ink smudging more likely without proper control. |
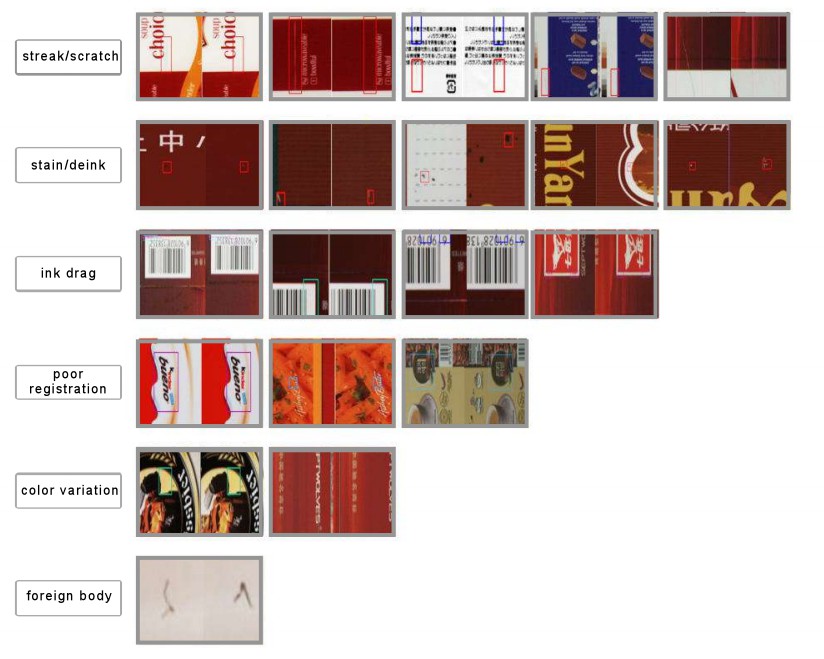
Handling Different Materials Using Printing Inspection Systems
1. Paper
Paper is the most traditional printing medium, commonly used in packaging, books, and advertising. Printing inspection systems for paper are equipped to detect issues such as misalignment, ink smudging, color deviations, and incomplete prints. High-speed cameras and sophisticated algorithms ensure that these defects are identified in real-time, even in high-speed production environments like newspaper printing or packaging factories.
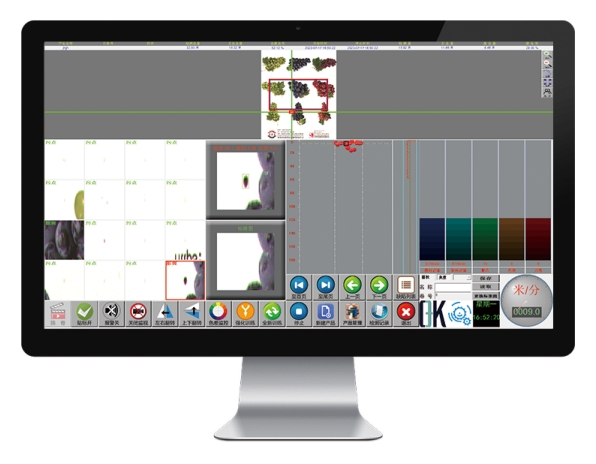
2. Plastic and Film
Printing on plastic and film materials, which are often used for packaging and labels, poses challenges due to their flexibility, transparency, and reflectiveness. Inspection systems must utilize UV or infrared light to detect scratches, fading, and uneven ink distribution, overcoming the limitations of traditional visible light inspection. These systems can also adjust for material stretching, ensuring that print alignment and color quality remain consistent even at high production speeds.
3. Metal
Metal surfaces, such as those used in can printing or metal packaging, present unique challenges due to their reflective properties and thickness variations. To handle metals, inspection systems use specialized lighting techniques and high-resolution cameras to minimize glare and accurately detect defects like print misalignment, surface scratches, and color imperfections. Metal printing often involves intricate designs and high precision, making defect detection critical for maintaining product quality.
4. Textiles
Textiles present another challenge for printing inspection systems due to their varying textures and flexibility. These materials, used for clothing, upholstery, and home decor, require systems that can handle surface irregularities and stretching during the printing process. Motion-compensating cameras and sensors are used to monitor print quality, ensuring that patterns are consistently aligned and that colors are applied uniformly. Textile printing systems must accommodate variations in fabric texture while maintaining high-quality results.
5. Glass and Ceramics
Printing on glass and ceramics is common in industries such as automotive, electronics, and decor. These materials require non-invasive inspection systems that use lasers, optical sensors, and imaging technology to detect surface flaws, misprints, or design inconsistencies. Due to the fragility of glass and ceramics, the inspection systems are designed to handle the materials carefully, ensuring accurate results without causing damage.
6. Multilayer and Composite Materials
In industries such as advanced packaging or pharmaceuticals, multilayer and composite materials are frequently used. These materials require specialized inspection systems that can analyze each layer without compromising overall structure. 3D imaging and multi-spectral scanning technologies are commonly used to inspect multiple layers for print defects such as misalignment or inconsistencies across the layers.
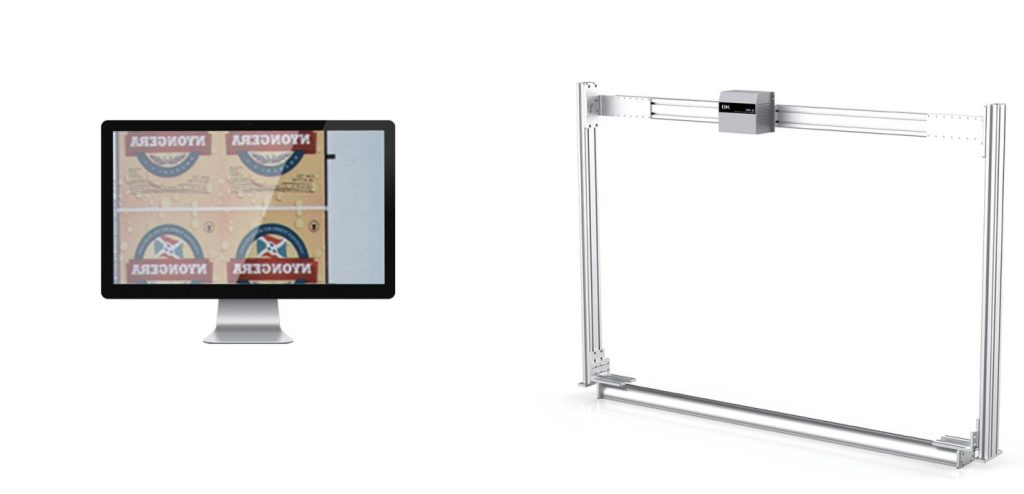
Key Technologies in Printing Inspection Systems for Various Materials
- High-Resolution Cameras: Central to all inspection systems, these cameras capture fine details on a range of materials, allowing the system to detect imperfections and anomalies with precision.
- UV and Infrared Sensors: These ultrasonic sensors are crucial when inspecting materials like plastic and film, which can have reflective or transparent properties that traditional visible light cameras cannot accurately capture.
- 3D Imaging Systems: Used particularly in complex or multilayer materials, 3D imaging allows the inspection system to analyze the depth and multiple layers of the material to identify flaws that may not be visible on the surface.
- Lighting Solutions: Proper lighting is vital for effective inspection, especially for reflective or textured materials. These solutions minimize glare and shadows, improving the detection of defects.
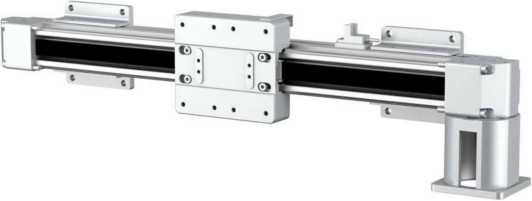
Overall, handling different materials requires printing inspection systems to be adaptable, technologically advanced, and highly precise. From paper and plastic to metal and textiles, these systems ensure that no matter the material, defects are identified early, and quality is maintained throughout the production process.