How Customized Printing Inspection Systems are Tailored for Personalized Products
Table of Contents
Customized printing inspection systems are emerging as a vital solution to ensure that each personalized item maintains consistent quality while meeting customer specifications. This article explores how customized printing inspection systems are tailored to address the specific demands of personalized products, detailing the key features, benefits, applications and the importance of advanced technologies in delivering precise and reliable inspection.
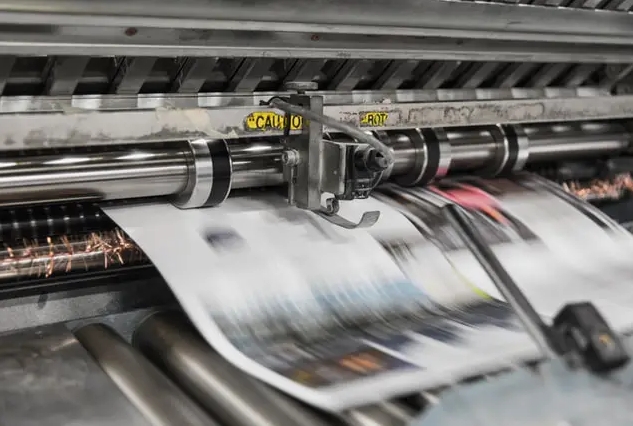
The Need for Customization in Printing Inspection
As personalized products become more popular, the demand for reliable and adaptable printing quality inspection systems increases. Traditional inspection systems, designed for high-volume, uniform production, often lack the flexibility required for unique, one-off items or limited-run batches. Customized printing inspection systems are built to manage the nuances of individual designs, different color schemes, and even unique dimensions or materials.
Personalized items require an inspection approach that can adjust dynamically, accommodating variations in design and ensuring each product meets stringent quality criteria. Such systems empower manufacturers to deliver a flawless final product, essential to building customer trust and brand loyalty.
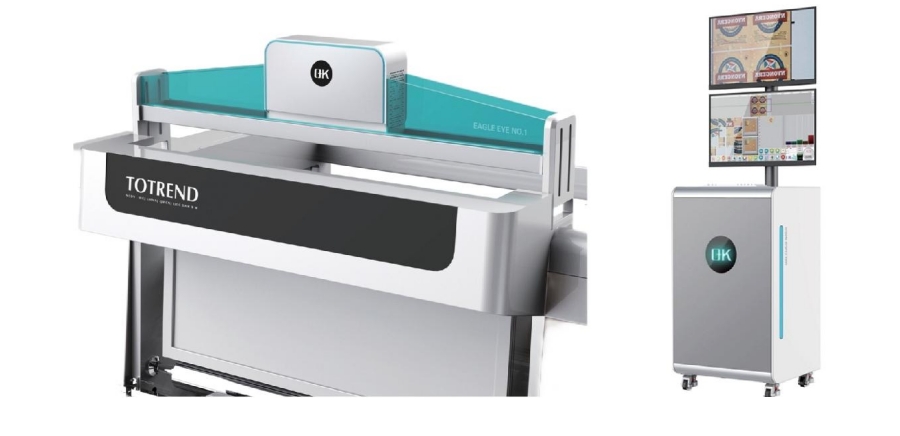
Key Features of Customized Printing Inspection Systems
The essential features that make custom print inspection systems effective in maintaining high-quality standards for diverse, individualized items.
1. Advanced Pattern Recognition
- AI-Driven Analysis: Equipped with artificial intelligence, these systems can identify complex patterns and shapes, adapting to a wide variety of designs without requiring manual intervention.
- Customization Adaptability: Pattern recognition algorithms allow the system to “learn” new designs and apply inspection parameters to unique layouts, making it suitable for one-off or limited-run products.
2. Dynamic Color Calibration and Consistency Monitoring
- Real-Time Color Detection: For personalized products with specific color schemes, these systems include precise color calibration tools that detect any deviation in hues, brightness, or saturation.
- Consistency Across Units: By ensuring uniformity across all products, dynamic color calibration helps maintain brand standards and customer expectations for color fidelity.
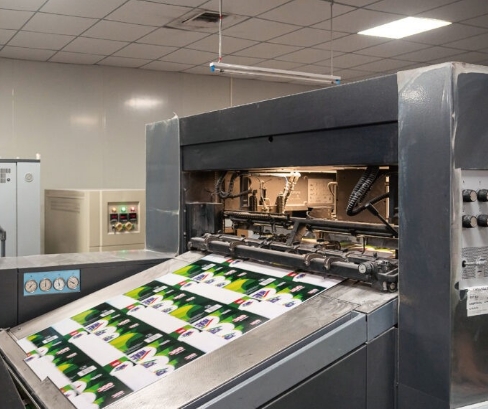
3. Variable Size and Format Adjustment
- Adaptive Sizing Parameters: Customized web inspection systems can automatically adjust to inspect products of varying sizes, accommodating everything from small labels to larger surfaces.
- Format Flexibility: These systems can inspect different product formats (e.g., flat, rounded, or textured surfaces), making them versatile for a wide range of custom items.
4. High-Resolution Imaging and 3D Vision
- Enhanced Detail Detection: High-resolution cameras capture intricate details in patterns, logos, and text, which is crucial for personalized items with fine or complex designs.
- 3D Vision Technology: For products with embossed or textured surfaces, 3D imaging technology provides a comprehensive view, identifying flaws that might be missed in 2D inspections.
5. Automated Defect Classification and Sorting
- Automatic Sorting Capabilities: Custom printing quality inspection systems can classify detected defects and automatically sort defective items, improving efficiency by reducing the need for manual sorting.
- Defect Tracking and Reporting: These systems provide real-time data on defect types and frequency, allowing manufacturers to identify patterns and take proactive measures to reduce recurring issues.
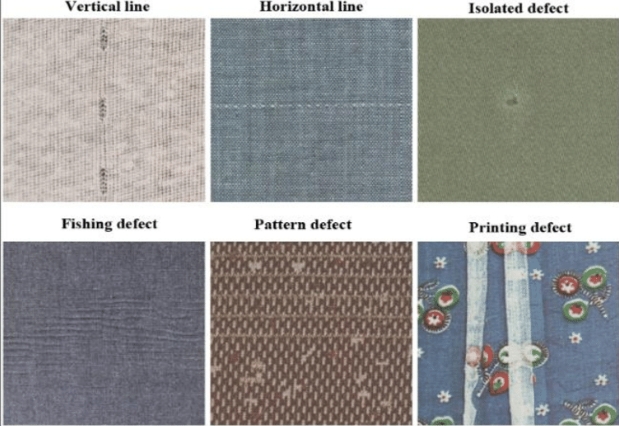
6. Internet of Things (IoT) Connectivity
- Real-Time Monitoring and Alerts: IoT-enabled inspection systems offer real-time status updates and alerts, allowing quick responses to any detected issues.
- Data Integration and Analysis: By connecting inspection data with other manufacturing systems, IoT connectivity provides valuable insights into production quality, enabling continuous improvement.
7. User-friendly Interface and Customization Options
- Intuitive Dashboard: A user-friendly interface makes it easy for operators to monitor inspection parameters, view real-time metrics, and adjust settings as needed.
- Customizable Inspection Settings: The system allows customization of printing inspection parameters, such as color thresholds, defect tolerance levels, and inspection frequency, to meet the specific requirements of each unique product.
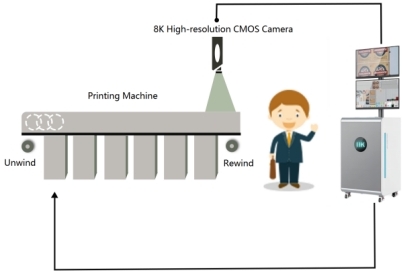
Benefits of Customized Printing Inspection Systems for Personalized Products
- Reduced Errors and Waste: Customized printing inspection systems are programmed to detect even minor defects, such as slight misalignments or color inconsistencies, that would detract from the final product. This precision minimizes production errors, reducing rework, and waste.
- Enhanced Productivity: By automating the print inspection process, these systems allow for rapid, accurate evaluations without manual labor, thereby increasing throughput. Manufacturers can meet tight deadlines without sacrificing quality, a crucial benefit in competitive markets.
- Improved Customer Satisfaction: When each product is inspected meticulously and meets high standards, customers receive exactly what they ordered. High satisfaction rates translate into positive reviews, repeat business, and enhanced brand loyalty.
- Flexible Production Capabilities: With the ability to inspect a diverse range of products, manufacturers can easily expand into new markets, creating customized items for different customer segments without reconfiguring or replacing inspection systems.
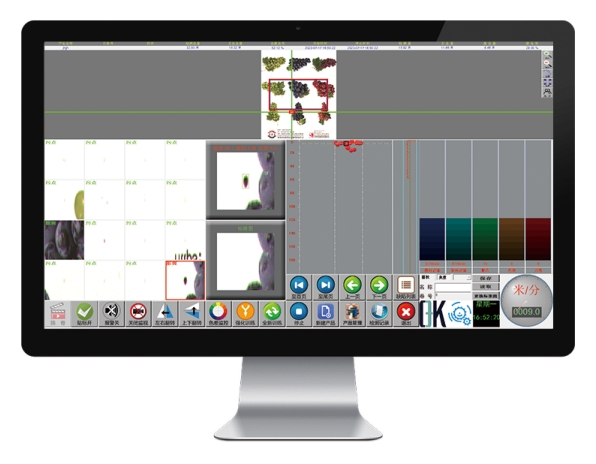
Application Scenarios of Customized Printing Inspection Systems
This chart shows how customized printing inspection systems provide industry-specific quality control, meeting the unique requirements of personalized products in each sector.
Industry | Applications | Quality Control Focus |
Apparel and Accessories | Custom clothing, bags, accessories | Pattern accuracy, color consistency, stitching quality |
Consumer Electronics | Personalized phone cases, laptop covers | Print quality, color accuracy, durability checks |
Promotional Merchandise | Branded items, logos on products | Brand color fidelity, logo placement, print clarity |
Customized Packaging | Unique designs for product packaging | Consistent color, logo placement, text accuracy |
Luxury Goods | Custom engraved or printed items | Precision in detail, high-resolution inspection |
Stationery and Printing | Custom notebooks, cards, labels | Text clarity, ink color consistency, margin precision |
Automotive and Industrial | Customized decals, labels for parts | Adhesion quality, resistance to wear, accuracy in dimensions |
Home Decor | Customized wallpapers, fabrics | Color calibration, pattern alignment, material consistency |
Health and Beauty | Personalized packaging for cosmetics, skincare | Label clarity, logo accuracy, ingredient list readability |
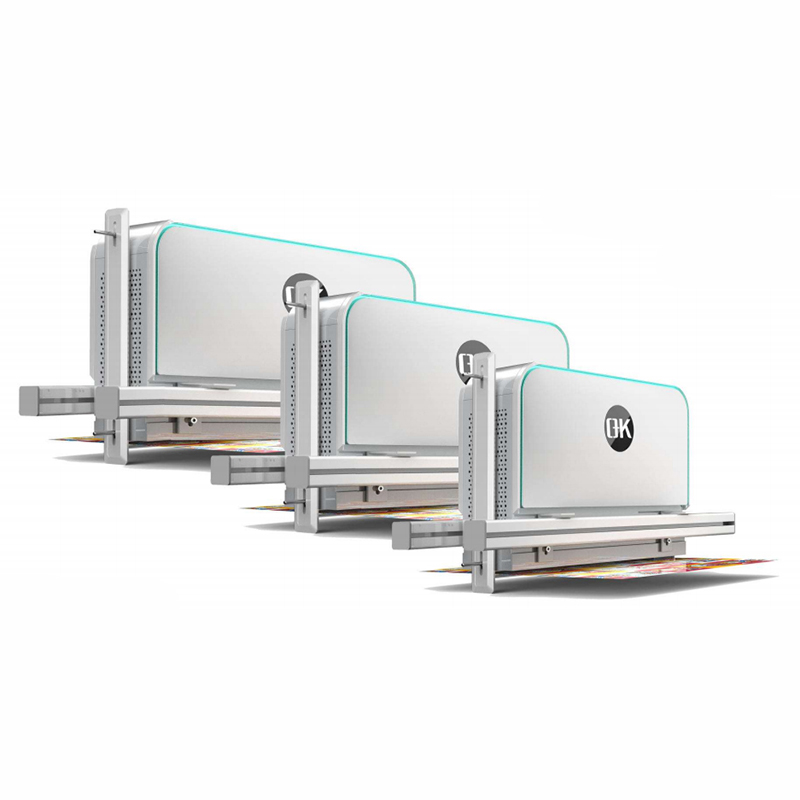
Steps to Implement Customized Printing Inspection Systems Effectively
This chart provides a step-by-step approach to implementing customized printing inspection systems, ensuring they are well-suited to meet the demands of personalized products while maintaining quality control efficiency.
Implementation Step | Description | Key Actions |
1. Assess Product Requirements | Identify the specific inspection needs based on product types and customization level. | Review types of customizations (color, texture, design) and inspection standards. |
2. Select the Right Technology | Choose inspection technologies suitable for personalized products, such as AI-driven pattern recognition and high-resolution imaging. | Research vendors, compare technologies (AI, 3D imaging, IoT). |
3. Customize Inspection Parameters | Configure parameters to suit product-specific requirements, including color calibration, defect tolerance, and size adjustments. | Work with the provider to set calibration standards, tolerances, and dimensions. |
4. Integrate with Existing Systems | Ensure seamless integration with other manufacturing and quality systems for a cohesive workflow. | Connect to IoT, data analytics, and production tracking systems. |
5. Train Personnel | Train operators on using the customized system and interpreting inspection data. | Conduct training sessions on system operation and data analysis. |
6. Conduct Test Runs | Run initial inspections to test and adjust system settings for accuracy and efficiency. | Perform sample inspections, collect feedback, and make necessary adjustments. |
7. Monitor and Optimize | Continuously monitor inspection results and optimize settings for ongoing quality improvement. | Analyze data reports, adjust parameters, and address recurring defects. |
8. Maintain and Update | Regularly maintain the system and update software for optimal performance. | Schedule maintenance, apply software updates, and assess emerging needs. |
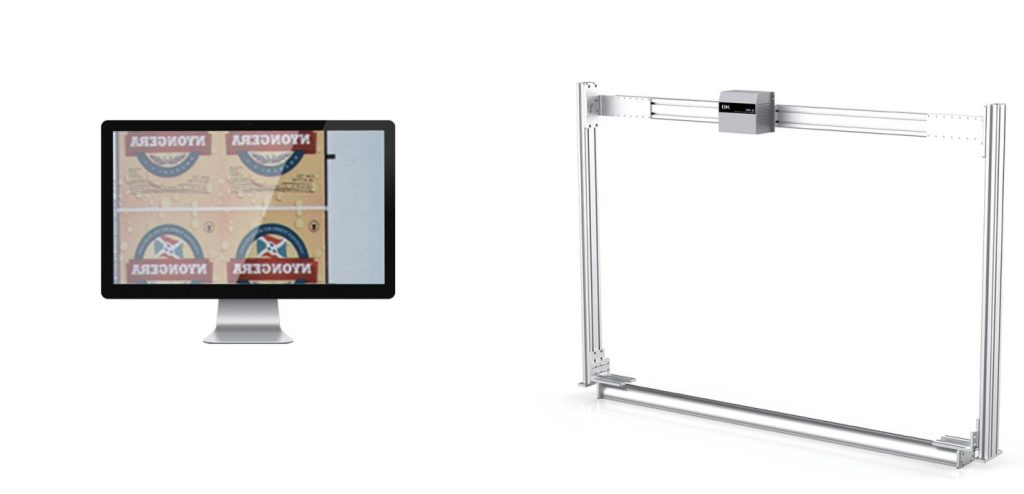
In summary, as personalized products continue to grow in demand, customized printing inspection systems are essential for maintaining high standards of quality. With tailored features and advanced technology, these 100% printing inspection systems empower manufacturers to deliver individualized products with consistency and accuracy. The investment in a custom print inspection solution ensures a competitive advantage in a marketplace increasingly defined by personalized experiences.