Exploring the In-line Width/Thickness Measurement System: Enhancing Precision
Whether producing paper, plastic, metal, textiles, or countless other materials, ensuring uniformity in width and thickness is paramount. This is where the in-line width/thickness measurement system comes into play, offering real-time monitoring and control of dimensional parameters during the production process. In this article, we delve into the workings, benefits, and applications of this in-line width/thickness measurement system.
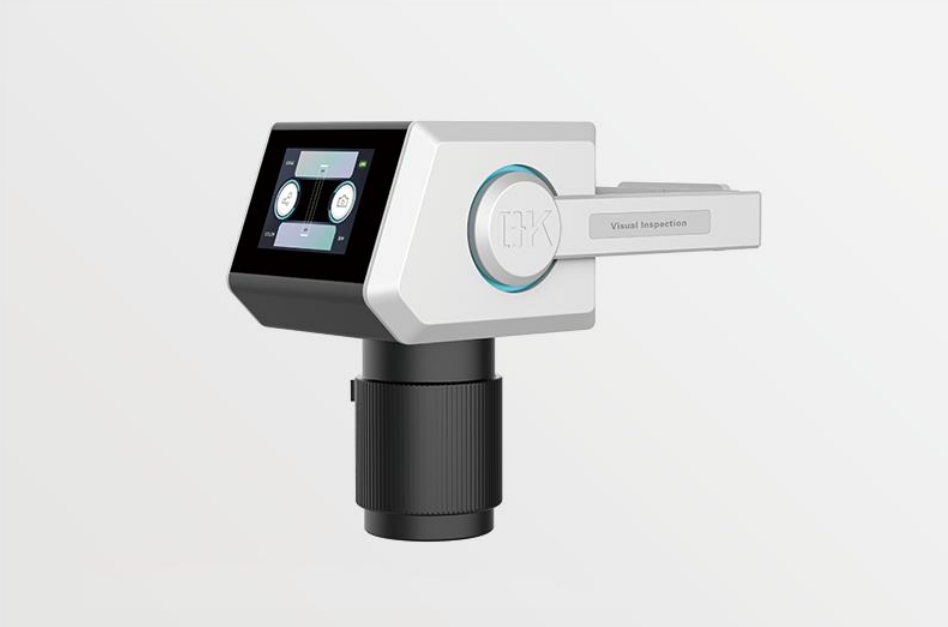
What is an In-line Width/Thickness Measurement System
The in-line width/thickness measurement system is a sophisticated piece of equipment designed to accurately measure the width and thickness of materials as they move through a production line. It employs a variety of sensing technologies, including lasers, cameras, ultrasonic sensors, or contact sensors, to capture precise dimensional data. This data is then processed using advanced algorithms to calculate the exact width and thickness of the material in real-time.
How In-line Width/Thickness Measurement System Works
1. Material Inspection
- The process begins as the material travels along the production line, passing through a designated measurement zone.
- The material may be in the form of sheets, rolls, coils, or other configurations, depending on the specific manufacturing process.
2. Sensor Deployment
- In-line measurement systems utilize a variety of sensing technologies, including lasers, cameras, ultrasonic sensors, or contact sensors, to capture dimensional data.
- These sensors are strategically positioned within the measurement zone to ensure comprehensive coverage of the material.
3. Data Acquisition
- As the material passes through the measurement zone, the sensors capture detailed images or measurements of its width and thickness.
- For example, cameras may capture high-resolution images of the material’s surface, while lasers or ultrasonic sensors may emit signals and measure the time it takes for them to reflect back, allowing for precise distance calculations.
4. Data Processing
- The captured data is then processed using advanced algorithms and software to analyze and interpret the dimensions of the material.
- Sophisticated image processing techniques may be employed to identify edges, contours, or features of interest, enabling accurate measurement of width and thickness.
5. Dimensional Analysis
Based on the processed data, the system calculates the exact width and thickness of the material.
Algorithms may take into account factors such as material properties, surface irregularities, and measurement uncertainties to ensure accurate results.
6. Real-time Feedback and Control
- The calculated width and thickness measurements are provided as real-time feedback to the production line.
- This feedback enables operators to make immediate adjustments to the manufacturing process to maintain optimal dimensional parameters.
- For example, automated control systems may adjust rollers, cutters, or other machinery to ensure uniformity in width and thickness across the material.
7. Continuous Monitoring
- The in-line measurement system operates continuously, monitoring width and thickness variations as the material progresses through the production line.
- Any deviations from specifications are detected in real-time, allowing for timely corrective action to be taken to maintain product quality and consistency.
8. Integration with Production Systems
- In-line measurement systems can be seamlessly integrated with other production systems and control mechanisms, enabling automated feedback and adjustments.
- Integration with data logging and reporting systems facilitates documentation and analysis of dimensional data for quality control and process optimization purposes.
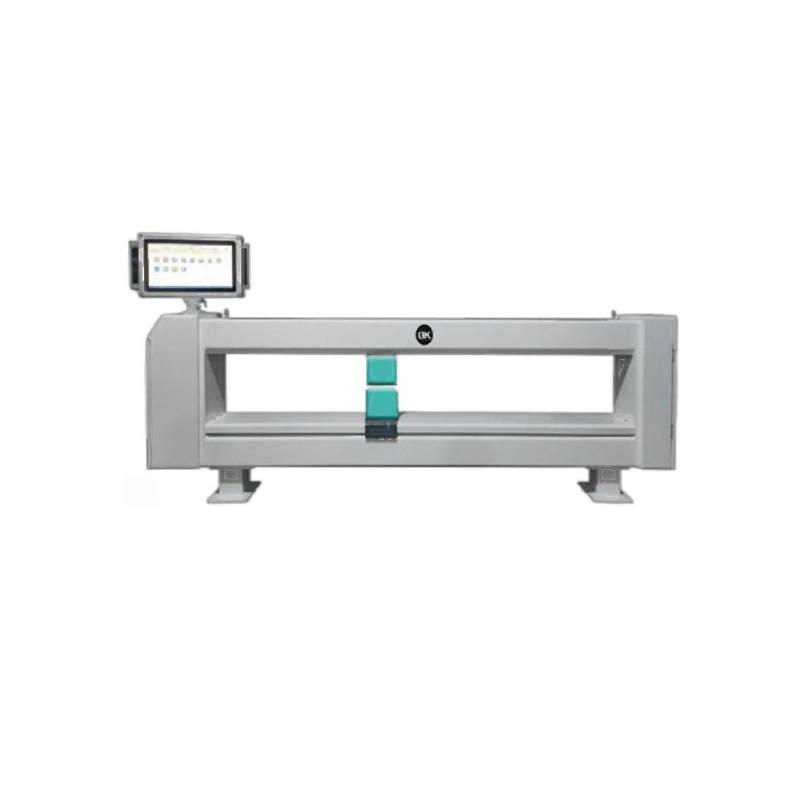
Benefits of In-line Width/Thickness Measurement Systems
1. Enhanced Quality Control
- Real-time monitoring of width and thickness allows manufacturers to detect deviations from specifications immediately.
- Early detection of dimensional variations enables prompt corrective action to be taken, minimizing the production of non-conforming products and reducing waste.
2. Improved Product Quality
- By maintaining precise control over dimensional parameters, in-line measurement systems ensure that manufactured products meet stringent quality standards.
- Consistent width and thickness result in products with uniform appearance, performance, and functionality, enhancing customer satisfaction and brand reputation.
3. Increased Production Efficiency
- Automated measurement reduces the need for manual inspection, saving time and labor costs associated with traditional quality control methods.
- Real-time feedback enables operators to make immediate adjustments to the production process, optimizing throughput and minimizing downtime.
4. Cost Savings
- Minimizing material waste and rework through accurate dimensional control leads to significant cost savings for manufacturers.
- Reduced scrap and rejections result in lower production costs and improved overall profitability.
5. Compliance with Standards and Regulations
- In-line measurement systems ensure that manufactured products comply with industry standards, specifications, and regulatory requirements.
- Documentation of dimensional data facilitates traceability and provides evidence of compliance for audits and certifications.
6. Process Optimization
- Continuous monitoring of width and thickness variations allows manufacturers to identify trends and patterns in production processes.
- Data analysis enables process optimization, leading to increased yield, reduced variability, and enhanced overall productivity.
7. Enhanced Customer Satisfaction
- Consistently delivering products with precise dimensions and high quality improves customer satisfaction and loyalty.
- Meeting customer requirements and expectations fosters long-term relationships and promotes repeat business.
8. Data-driven Decision Making
- In-line thickness measurement systems generate valuable data on thickness variations, which can be used for analysis, optimization, and decision-making.
- Data-driven insights help manufacturers identify root causes of dimensional deviations and implement preventive measures to improve process reliability and efficiency.
Applications across A Wide Range of Industries of In-line Width/Thickness Measurement System
1. Paper and Pulp Industry
- Monitoring paper thickness and width in paper mills to ensure uniformity for consistent print quality and packaging performance.
- Measuring the thickness and width of paper rolls, sheets, and cardboard for various printing, packaging, and paper product applications.
2. Plastic Extrusion Industry
- Measuring the thickness and width of plastic films, sheets, and profiles in the plastics industry for packaging, construction, and automotive applications.
- Monitoring the extrusion process to ensure precise dimensions of plastic products such as pipes, tubes, and extruded profiles.
3. Metal Processing Industry
- Ensuring uniform thickness and width of metal coils, strips, and sheets in metalworking industries such as automotive, aerospace, and construction.
- Monitoring the rolling and stamping processes to achieve precise dimensional control of metal components and products.
4. Textile Manufacturing Industry
- Monitoring fabric thickness and width in textile mills for apparel, upholstery, and industrial applications.
- Ensuring consistent dimensions of woven or knitted fabrics for garment manufacturing, home textiles, and technical textiles.
5. Packaging Industry
- Measuring the thickness and width of packaging materials such as films, foils, and laminates to ensure uniformity in packaging performance and barrier properties.
- Monitoring the production of packaging containers, boxes, and cartons to maintain dimensional accuracy and structural integrity.
5. Printing Industry
- Ensuring consistent thickness and width of printing substrates such as paper, cardboard, and plastic films for high-quality printing results.
- Monitoring the printing process to achieve precise registration and alignment of printed materials on substrates of varying dimensions.
6. Converting Industry
- Measuring the thickness and width of converted products such as tapes, labels, and adhesive films to meet customer specifications and performance requirements.
- Ensuring dimensional accuracy of converted materials during cutting, slitting, and laminating processes for various industrial and consumer applications.
7. Construction Industry
- Monitoring the thickness and width of construction materials such as insulation boards, membranes, and roofing materials for building envelope performance.
- Ensuring precise dimensions of concrete, asphalt, and other construction materials during mixing, casting, and curing processes.
8. Automotive Industry
- Measuring the thickness and width of automotive components such as gaskets, seals, and trim materials for optimal performance and fit.
- Ensuring uniformity in the dimensions of stamped, molded, or extruded parts used in vehicle assembly and manufacturing.
Conclusion
The in-line width/thickness measurement system plays a vital role in modern manufacturing, enabling manufacturers to achieve precise control over dimensional parameters and ensure product quality. By harnessing advanced technology and automation, manufacturers can achieve higher levels of quality, efficiency, and cost-effectiveness in their production processes.