Enhancing Durability of Web Guide Systems: Key Innovations in Rollers and Actuators
Table of Contents
Rollers and actuators are critical components in web guide systems, which play pivotal roles in guiding and correcting the lateral positioning of the material as it moves through production lines. In recent years, innovations in these components have focused on enhancing the durability, accuracy, and efficiency of web guiding systems. This article explores the latest advancements in rollers and actuators that contribute to longer-lasting, more reliable web guide systems.
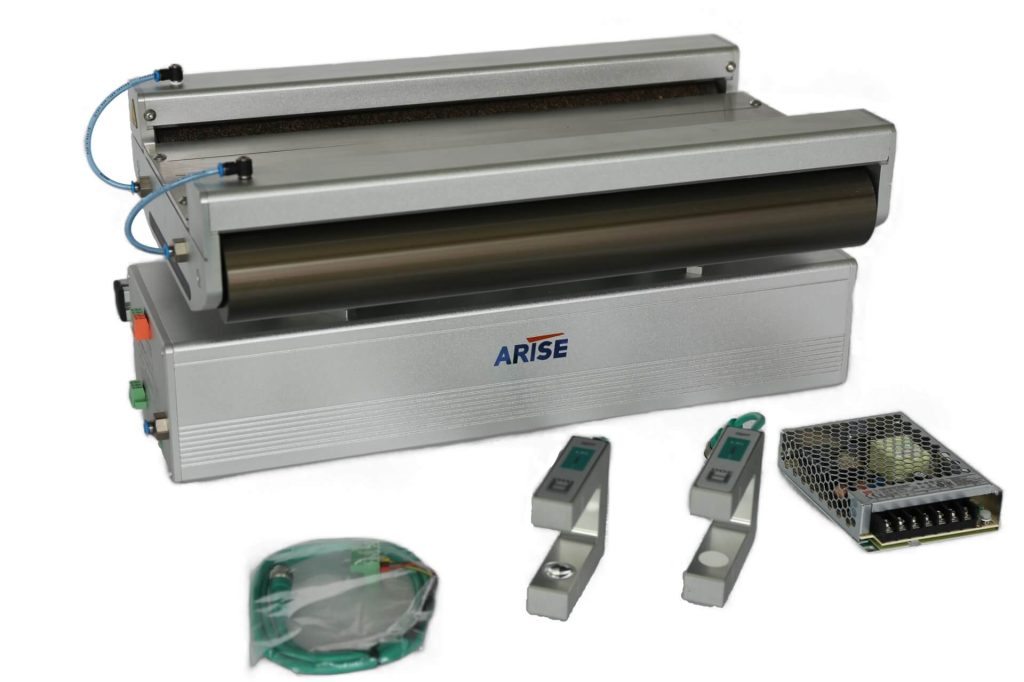
The Role of Rollers and Actuators in Web Guide Systems
How Rollers and Actuators Work in Web Guide Systems
Rollers and actuators are working together to ensure precise alignment and smooth movement of materials during production processes such as printing, packaging, and textiles. Rollers provide stable support and guide the web material through various stages, while actuators control the lateral adjustments needed to keep the web properly aligned. Actuators respond to sensor feedback, making real-time corrections to maintain accuracy, reduce waste, and ensure high-quality output. Together, they enhance the efficiency and precision of web guiding operations, especially in high-speed and complex production environments.
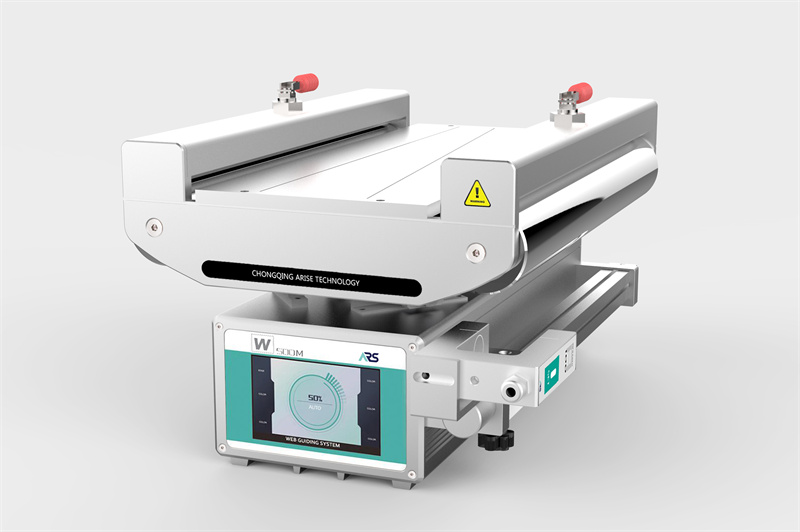
What are Common Used Rollers and Actuators in Web Guide Systems
This chart summarizes the essential rollers and actuators used in web guiding systems, emphasizing their roles and benefits.
Component | Type | Function | Advantages |
Rollers | Idler Rollers | Guide and support the web without applying power. | Low maintenance, smooth web guidance. |
Tension Rollers | Maintain consistent tension in the web material. | Helps prevent slack and wrinkling, ensures even flow. | |
Drive Rollers | Pull the web through the system. | Provides controlled movement, essential for automation. | |
Steering Rollers | Align and correct the web’s position dynamically. | Essential for precision in high-speed applications. | |
Actuators | Pneumatic Actuators | Use compressed air for rapid adjustments. | Quick response, good for lightweight systems. |
Hydraulic Actuators | Use fluid pressure for fine, forceful movements. | High force, and precision for heavy-duty operations. | |
Electric Actuators | Use electric motors for precise adjustments. | Energy efficient, easy digital integration, precise. |
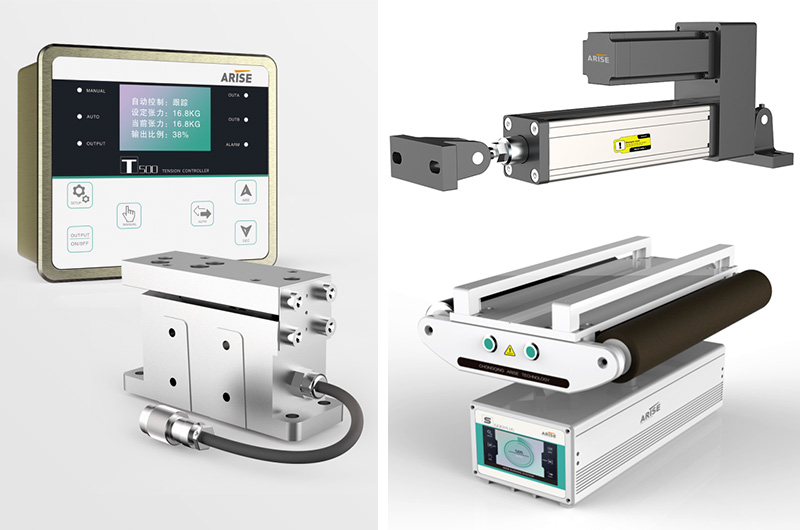
Enhanced Rollers in Web Guide Systems
Recent innovations in roller technology have focused on improving durability, precision and performance in web guide control system, making them better suited for high-demand industrial environments.
1. Advanced Roller Materials
Enhanced materials are now used in web guide rollers to improve their wear resistance and longevity:
- High-Density Polyurethane Coatings: These rollers offer excellent resistance to wear and abrasions, ensuring longer service life, especially in industries where materials are tough on roller surfaces.
- Ceramic-Coated Rollers: Ceramic coatings reduce friction and increase resistance to wear, providing a smooth surface that minimizes material damage and extends roller life.
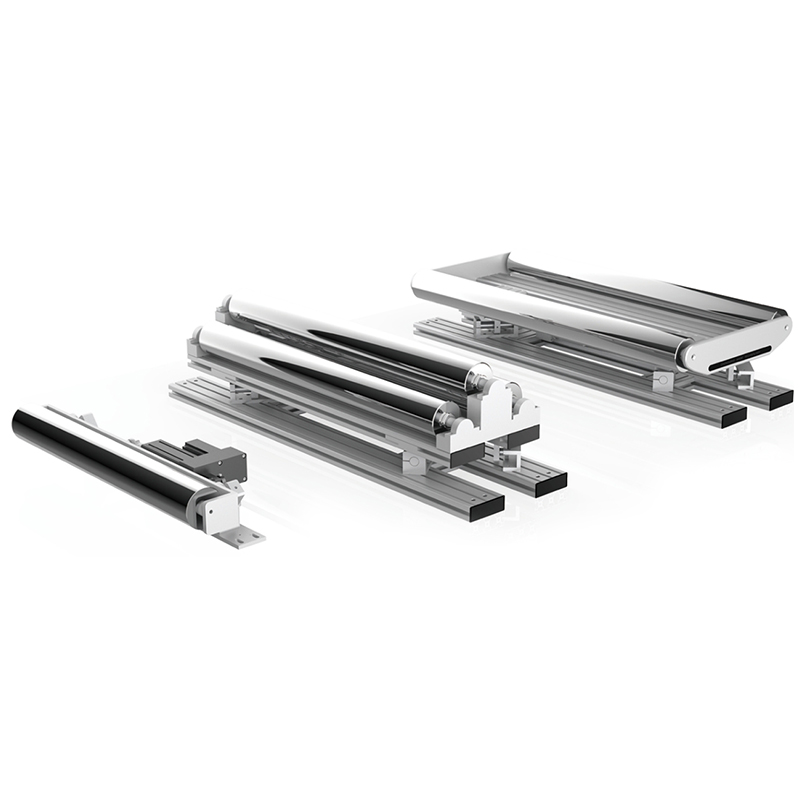
2. Specialized Coatings for Longevity
Rollers now incorporate specialized coatings that further enhance their durability and adaptability in challenging environments:
- Anti-Stick Coatings: These coatings prevent material buildup on the roller surface, especially useful in industries dealing with adhesives or other sticky substances.
- Anti-Corrosion Treatments: Designed for environments prone to moisture or chemical exposure, these treatments protect rollers from degradation and corrosion, ensuring consistent performance.
3. Precision Bearings and Vibration Control
The incorporation of precision-engineered bearings in modern rollers has significantly reduced vibration and improved alignment accuracy:
- Reduced Vibration: This leads to smoother web movement, reducing the likelihood of material misalignment or production errors.
- Enhanced Accuracy: Precision bearings allow for finer control of material movement, critical in high-speed or high-precision applications such as printing or packaging.
4. Low-Friction Designs
New roller designs prioritize low-friction operation, allowing for smoother material handling and less wear on both the roller and the web material. This innovation helps to improve efficiency and reduce the need for frequent maintenance.
5. Future Trends in Roller Innovation
Further advancements in web guide rollers are expected to focus on:
- Lightweight Composite Materials: Lighter rollers that maintain strength and durability will reduce the energy required to drive the web guide systems.
- Self-Cleaning Rollers: Rollers with self-cleaning properties could help minimize maintenance and downtime by automatically preventing material buildup during operation.
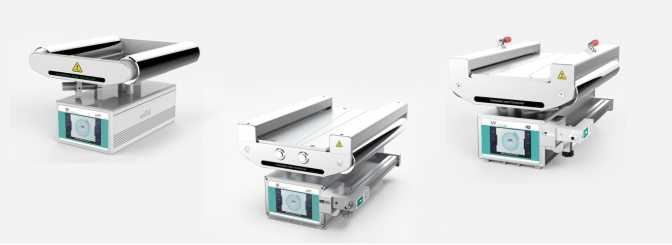
Advanced Actuators in Web Guide Systems
Innovations in actuator technology have led to enhanced control, responsiveness and durability for web guide system, making them essential for industries such as printing, packaging, textiles, and converting.
1. Electromechanical Actuators
Electromechanical actuators have become widely adopted due to their high precision and reliability. These actuators convert electrical energy into mechanical motion, providing fine-tuned control over web alignment.
Key Features
- High Precision: Electromechanical actuators offer precise movement control, essential for maintaining accurate web alignment in high-speed production.
- Programmable Control: Integrated with digital control systems, these actuators allow for automated adjustments, reducing human intervention and increasing efficiency.
- Low Maintenance: Due to fewer moving parts and improved materials, these actuators require less frequent maintenance compared to older hydraulic or pneumatic systems.
2. Servo Motor Actuators
Servo motor actuators provide even greater precision and speed control. The web guide actuators are used in applications where rapid response and exact positioning are critical.
Key Features
- Real-Time Feedback: Servo motors are equipped with encoders that provide continuous feedback on the actuator’s position, allowing for real-time adjustments.
- High Speed and Torque: These actuators can handle high-speed web guide operations while maintaining strong torque, ensuring stability even during fast material processing.
- Energy Efficiency: Servo actuators consume less energy compared to hydraulic systems, making them more eco-friendly and cost-effective over time.
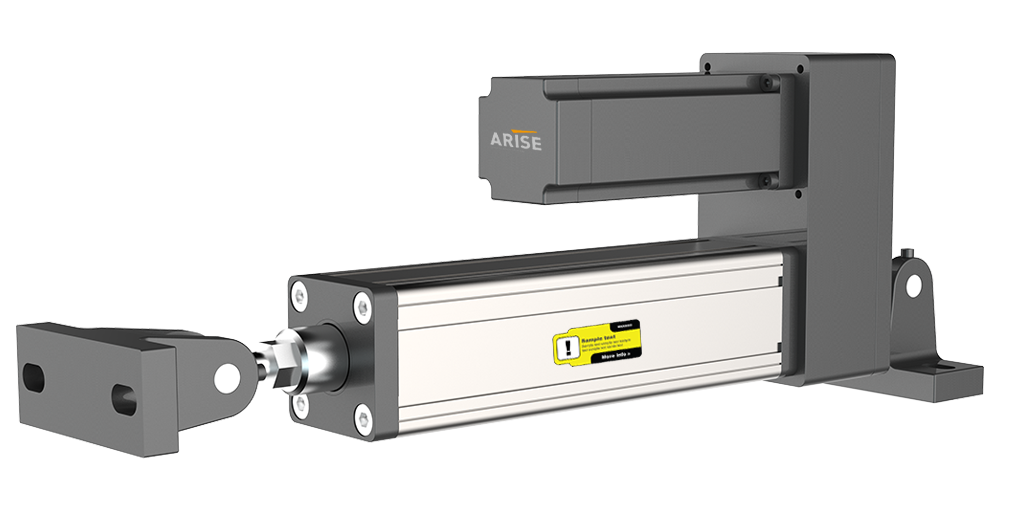
3. Linear Actuators
Linear actuators, particularly electric linear actuators, are commonly used in web guide systems to provide accurate lateral adjustments to the web.
Key Features
- Precise Linear Movement: These actuators offer smooth, controlled linear motion, which is ideal for applications that require delicate adjustments in web positioning.
- Compact Design: Modern linear actuators are designed to fit into tight spaces, making them versatile for different machine configurations.
- Durability: With sealed components and robust construction, linear actuators are built to withstand harsh operating environments.
4. Pneumatic Actuators
While less commonly used in high-precision applications compared to electromechanical or servo actuators, pneumatic actuators remain relevant due to their simplicity and reliability in certain environments.
Key Features
- Cost-Effective: Pneumatic actuators are typically more affordable and simpler to install, making them a good choice for applications that don’t require extreme precision.
- Durable and Resistant: These actuators can perform well in harsh environments, including areas with high humidity, dust, or extreme temperatures.
- Fast Response Time: Pneumatic actuators can achieve quick movements, which can be useful in systems that require rapid correction.
5. Smart Actuators
Smart actuators integrate sensors and communication technology, enabling remote monitoring and control of web guide systems. These advanced systems enhance operational efficiency and reliability.
Key Features
- Condition Monitoring: Smart actuators can monitor their own performance, detecting signs of wear or failure before a breakdown occurs, allowing for predictive maintenance.
- IoT Integration: With the ability to connect to industrial IoT platforms, smart actuators can provide data on system performance and diagnostics, enabling real-time monitoring and control.
- Self-Adjustment: Some smart actuators are capable of automatic adjustments based on web position feedback, further improving precision without manual intervention.
6. Hybrid Actuators
Hybrid actuators combine the best features of different actuator types, such as the precision of electromechanical systems with the robustness of hydraulic actuators. These are increasingly being developed to offer versatility and adaptability in web guide systems.
Key Features
- Versatile Control: Hybrid actuators can adapt to different types of loads and operational conditions, making them suitable for diverse web materials and production speeds.
- Enhanced Force and Speed: By combining multiple technologies, these actuators offer superior force generation and faster response times compared to single-technology actuators.
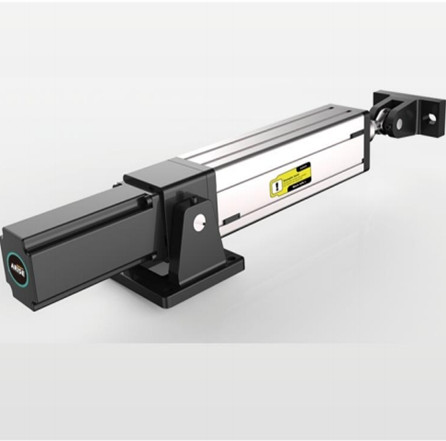
To sum up, innovations in rollers and actuators are enhancing the efficiency, accuracy and durability of web guide system equipment across various industries. With advancements in materials, smart technologies, and actuator precision, modern web guiding control systems are better equipped than ever to handle high-speed production environments while reducing maintenance and operational costs.