Custom Tension Control Solutions for Specialized Manufacturing Needs
In specialized manufacturing, maintaining precise tension control is critical to ensuring product quality, minimizing waste, and optimizing operational efficiency. Whether in industries such as printing, textiles, metal processing, or composites manufacturing, customized tension control solutions provide a competitive edge by addressing unique material handling challenges.
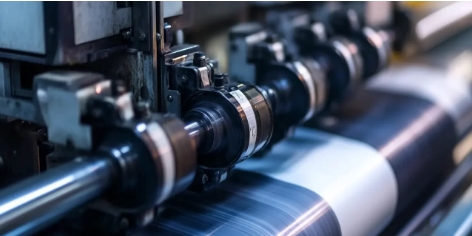
Table of Contents
Challenges of Tension Control in Specialized Manufacturing
This chart outlines various challenges manufacturers may face when implementing tension control solutions for specialized production processes. Addressing these challenges requires advanced technologies, regular maintenance, and careful integration with other production systems.
Challenge | Description | Impact |
Material Variability | Differences in material thickness, elasticity, and surface characteristics can make tension control more complex. | Leads to inconsistent tension, product defects, and material wastage. |
High-Speed Operations | In high-speed production environments, quick adjustments to tension are required to avoid errors. | Increased risk of material breakage or misalignment due to delayed response times. |
Complex Geometries of Materials | Non-uniform or intricate material shapes require specialized tension control methods. | Challenges in maintaining consistent tension across different material sections. |
Environmental Conditions | Changes in humidity, temperature, or ambient conditions affect material behavior and tension control accuracy. | Can result in fluctuating tension and quality issues, especially with sensitive materials. |
Dynamic Process Changes | Variations in speed, thickness, or length of materials during production can affect tension. | Requires constant adjustments to prevent tension inconsistencies or defects. |
Machine Calibration and Maintenance | Frequent recalibration or downtime of tension control equipment due to wear or improper maintenance. | Reduced system accuracy, higher risk of material failure, and increased downtime. |
Integration with Other Systems | The need to integrate tension control systems with other automated or digital systems, such as automated web guide system, printing inspection system, in complex workflows. | Potential for synchronization issues, leading to delays or errors in production. |
Control System Complexity | Advanced control systems may require expertise to set up and manage, making them difficult to implement. | Increased complexity in system setup and operation, leading to higher costs and learning curves. |
Safety Concerns | Ensuring proper tension without exceeding safe limits is crucial to avoid damage to machinery and operators. | Over-tensioning can lead to material breakage, equipment damage, and safety risks. |
Cost of Custom Solutions | Custom-built tension control solutions can be expensive to design, implement, and maintain. | Higher upfront investment and ongoing costs can limit adoption or scalability. |
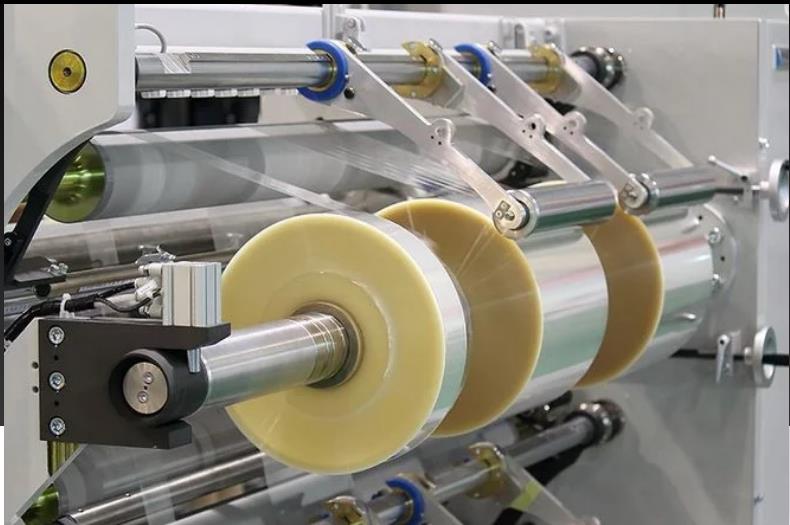
Key Components of Custom Tension Control Systems for Addressing Specialized Needs
Custom tension control systems are designed to address the specific needs of various manufacturing processes, ensuring consistent material tension and preventing defects. These systems consist of multiple components that work in harmony to maintain the correct tension throughout production.
1. Tension Sensors
Tension sensors are the core elements of a tension control system. They measure the force or strain on the material as it moves through the production process. These sensors continuously monitor the tension and send real-time data to the control system. Common types of tension sensors include:
- Load Cells: These are the most common type of sensors used in tension control systems. They measure the mechanical force applied to the material and convert it into an electrical signal.
- Laser-based Sensors: These non-contact sensors use laser beams to measure the displacement or position of the material, providing high-precision tension readings.
The tension sensor data is used to adjust the tension by modifying the settings of the other components in the system.
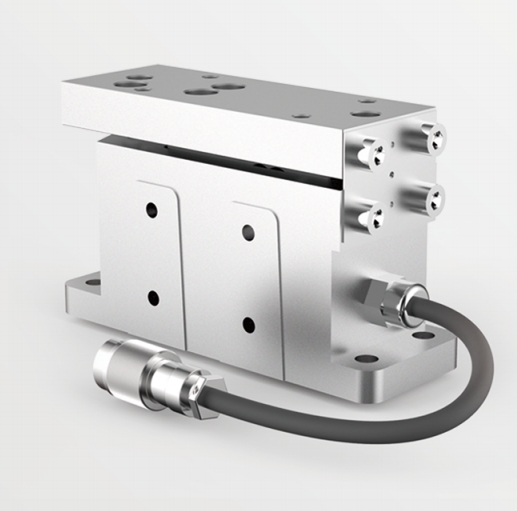
2. Dancer Rolls
Dancer rolls are mechanical devices used to regulate and adjust the tension of the material during the manufacturing process. Positioned along the material’s path, these rolls move based on the changes in tension, ensuring a consistent level throughout the production.
- Functionality: As the material tension increases or decreases, the dancer roll adjusts its position accordingly. The roll’s movement serves as a feedback mechanism to the control system, helping to maintain optimal tension.
- Benefits: Dancer rolls can absorb tension fluctuations, making them ideal for processes with high-speed operations or varying material properties.
3. Braking Systems
Braking systems apply resistance to the movement of the material, helping to regulate tension and prevent the material from over-running or becoming too loose. Brakes are typically used in unwinding and rewinding processes, where material is fed onto or off rolls.
- Types of Brakes: Magnetic powder brakes and pneumatic brakes are commonly used in custom tension control systems. Magnetic brakes are non-contact, providing smooth and precise control, while pneumatic brakes offer adjustable resistance by using air pressure.
- Functionality: Braking systems prevent excessive material movement, helping to control the material’s speed and tension.
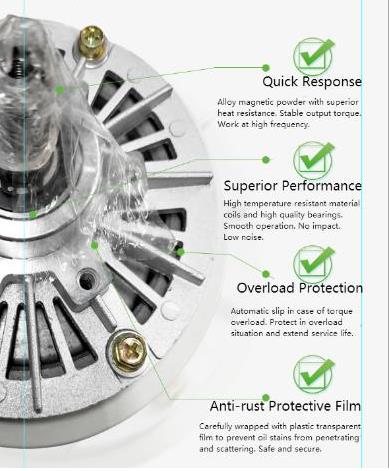
4. Servo Motors and Drives
Servo motors are essential for achieving precise control over tension. These motors adjust the speed of rollers or other tension-controlling mechanisms in response to the real-time data provided by tension sensors.
- High-Precision Adjustment: Servo motors can make quick and fine-tuned adjustments to the speed of rollers, ensuring consistent tension even in high-speed or variable material processing environments.
- Benefits: They offer fast response times, which is crucial for maintaining tension stability in dynamic manufacturing processes.
5. Tension Controllers
The tension controller is the brain of the custom tension control solution. It processes data from tension sensors and other components, issuing commands to adjust the speed, position, or resistance applied by the brakes, motors, and dancer rolls.
- Functions: The control system ensures that all components work together in real time, maintaining consistent tension and responding to fluctuations in material properties or production speed.
- Advanced Features: Modern automatic tension controllers are equipped with digital interfaces, offering remote monitoring, diagnostics, and predictive analytics to help optimize the manufacturing process.
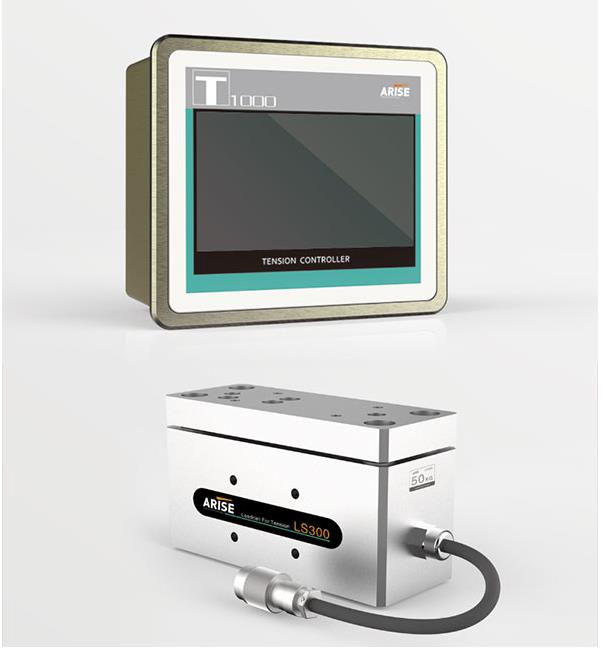
6. Rollers and Rewinders
Rollers are often used to guide the material through the manufacturing process, and rewinders help in winding the material onto a spool or roll. These components are integrated into the tension control system to ensure consistent material flow and proper tension across all stages of production.
- Adjustable Rollers: Some rollers are adjustable, enabling them to provide tension control based on real-time feedback from sensors.
- Rewinders: Rewinders are used to manage the material once it has been processed, ensuring that it is wound onto rolls without excessive tension or slack.
7. Feedback Mechanisms
Feedback mechanisms are integral to the functioning of the tension control system. These mechanisms continuously monitor the tension and adjust the system’s settings in real time. Feedback is collected from the tension sensors, dancer rolls, and other components, which ensures that the desired tension levels are maintained across the entire manufacturing process.
- Real-Time Adjustments: Feedback systems provide instant updates to the control system, enabling it to make on-the-fly adjustments and maintain optimal tension despite changes in material characteristics or production speeds.
8. Safety Mechanisms
Safety mechanisms are crucial to protecting both the equipment and the material being processed. These can include over-tension detection, emergency stop features, and system shutdown protocols in case of malfunction.
- Over-Tension Detection: If tension exceeds preset limits, the control system can automatically apply resistance or stop the material movement to prevent damage.
- Emergency Stops: Safety protocols are built into custom systems to quickly stop the machinery in case of an emergency, ensuring the safety of workers and the protection of the equipment.
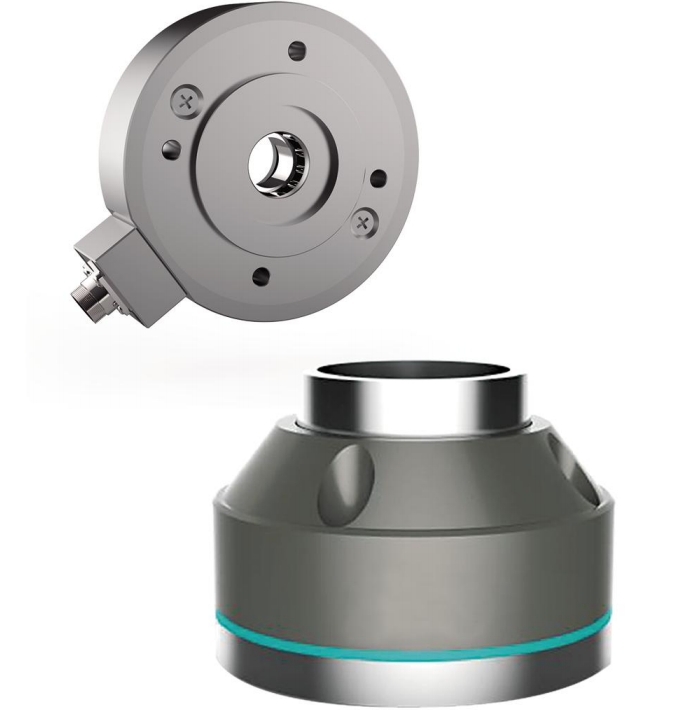
Applications of Custom Tension Control Solutions
This chart highlights a range of industries where custom tension control solutions are applied to improve material handling, product quality, and production efficiency.
Industry/Application | Description | Benefits of Custom Tension Control |
Textile Manufacturing | Controls tension in fabrics during weaving, knitting, and dyeing processes. | Prevents material breakage, ensures consistent fabric quality. |
Paper and Film Processing | Maintains proper tension in rolls of paper, film, or foil during unwinding, processing, and rewinding stages. | Reduces wrinkles, tears, and stretching, ensuring smooth material handling. |
Printing Industry | Ensures uniform tension of paper or film in printing presses. | Prevents image distortion and print quality issues. |
Metal Processing | Manages tension in metal strips during slitting, rolling, or coating processes. | Ensures precise alignment, prevents defects in the metal. |
Wire and Cable Manufacturing | Maintains tension in wire drawing, winding, and spooling operations. | Prevents tangling, breakage, and maintains uniform wire quality. |
Converting and Laminating | Regulates tension in materials during lamination, coating, and converting operations. | Ensures smooth application of coatings, laminates, and adhesives. |
Rubber and Plastic Extrusion | Controls tension in extruded rubber or plastic during stretching or cooling. | Enhances product consistency and prevents material distortion. |
Nonwoven Fabric Production | Maintains tension of fibers during the formation of nonwoven fabrics. | Improves fabric uniformity and strength. |
Automotive Parts Manufacturing | Controls tension in the manufacturing of automotive components, such as seals, gaskets, and trim materials. | Reduces defects, improves dimensional accuracy, and ensures smooth production. |
Packaging Industry | Ensures correct tension in film or foil during packaging material production, particularly for flexible packaging. | Prevents tears and ensures precise wrapping and sealing. |
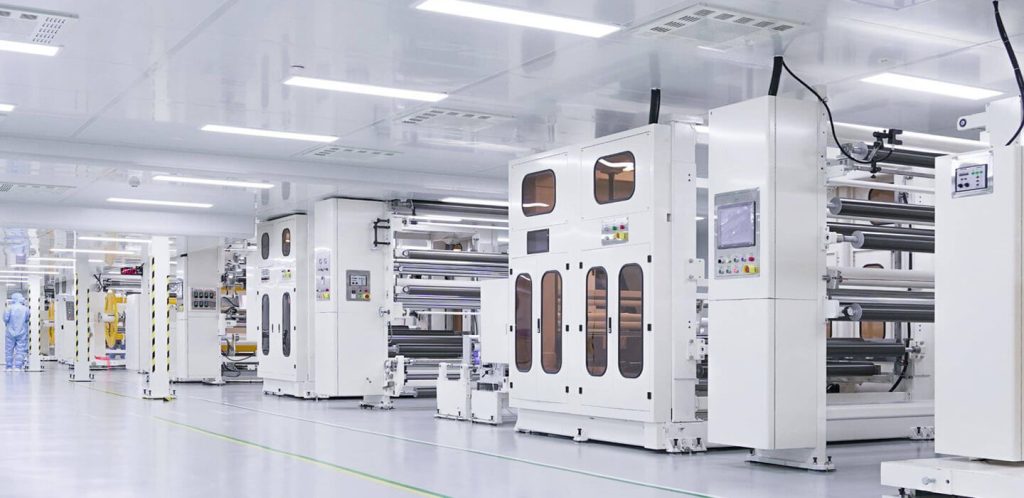
Future Trends in Custom Tension Control
As manufacturing processes continue to advance, the need for increasingly sophisticated tension control systems will grow. With the advent of Industry 4.0 and the Internet of Things (IoT), tension control systems are becoming more integrated and intelligent. Modern custom solutions incorporate predictive analytics and real-time monitoring, enabling manufacturers to identify potential issues before they arise and optimize their processes for better performance.
Additionally, as manufacturers face pressure to reduce energy consumption and lower operational costs, custom tension control solutions are being designed with greater energy efficiency in mind. These systems not only provide precise control but also minimize power usage, helping manufacturers meet sustainability goals without compromising on performance.
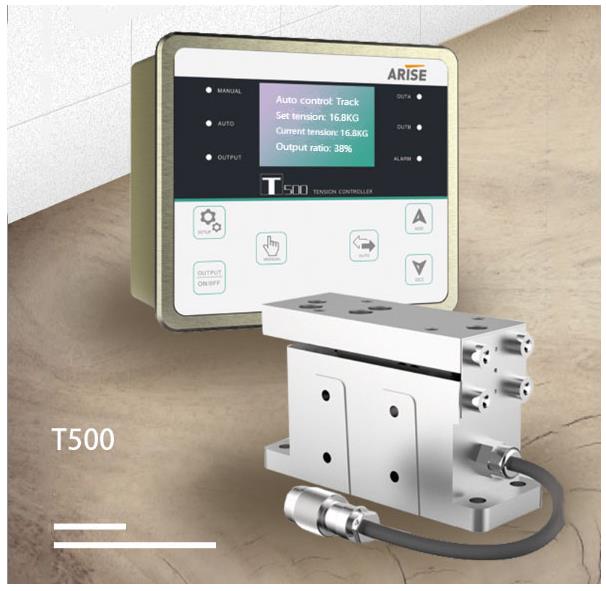
Summary
Custom tension control solutions are essential for specialized manufacturing needs, offering tailored approaches to achieve optimal material handling and prevent defects. Through incorporating advanced tension sensors, digital tension controller, mechanical components, etc, custom solutions ensure precise tension control across a wide range of industries. Whether for textiles, printing, metal processing, or flexible electronics, these tension control systems provide manufacturers with the flexibility, efficiency, and high quality.