Cost vs. Benefit Analysis of Investing in Printing Inspection Systems
Table of Contents
As businesses scale up their production or target stricter quality standards, investing in printing inspection systems becomes a strategic consideration. However, with significant costs involved, businesses must weigh the investment against the benefits to make an informed decision. This article explores the cost vs. benefit analysis of printing inspection systems, highlighting their financial impact and operational advantages.
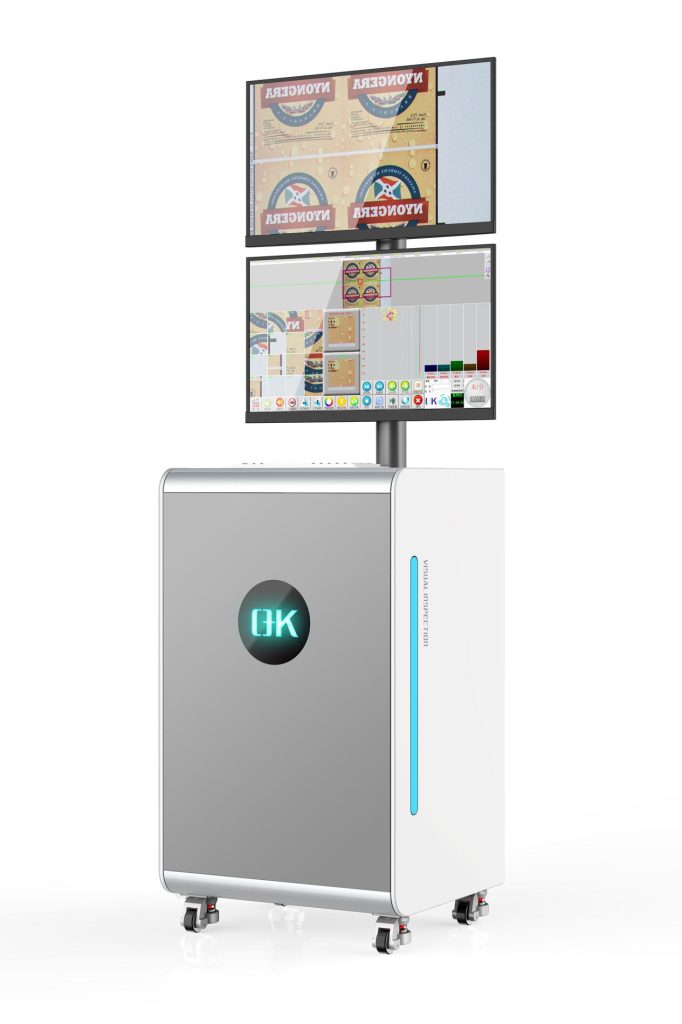
What Are Printing Inspection Systems
Printing inspection systems are advanced technologies designed to detect and identify defects in printed materials during production. Equipped with high-resolution cameras, sensors, and intelligent software, these systems monitor critical parameters, such as:
- Color consistency
- Registration accuracy
- Surface imperfections (e.g., streaks, spots, smudges)
- Content accuracy (e.g., missing text, incorrect images)
By automating the inspection process, these systems help ensure high-quality outputs while minimizing human errors.
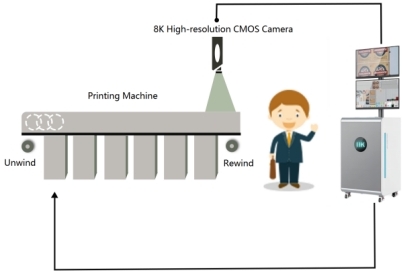
Costs of Printing Inspection Systems
This chart provides a clear view of both upfront and recurring costs to help businesses assess the financial investment required for a print inspection system.
Cost Component | Description | Estimated Range |
Initial Investment | Cost of purchasing the inspection system, which varies based on features, speed, and accuracy. | $50,000 – $300,000 |
Installation and Integration | Expenses for integrating the system into existing workflows and configuring software. | $5,000 – $20,000 |
Training Costs | Employee training to operate, calibrate, and maintain the system. | $1,000 – $5,000 |
Maintenance and Upgrades | Regular calibration, software updates, and occasional repairs. | $2,000 – $10,000 annually |
Downtime Costs | Temporary production disruption during installation and calibration. | Variable (depends on scale) |
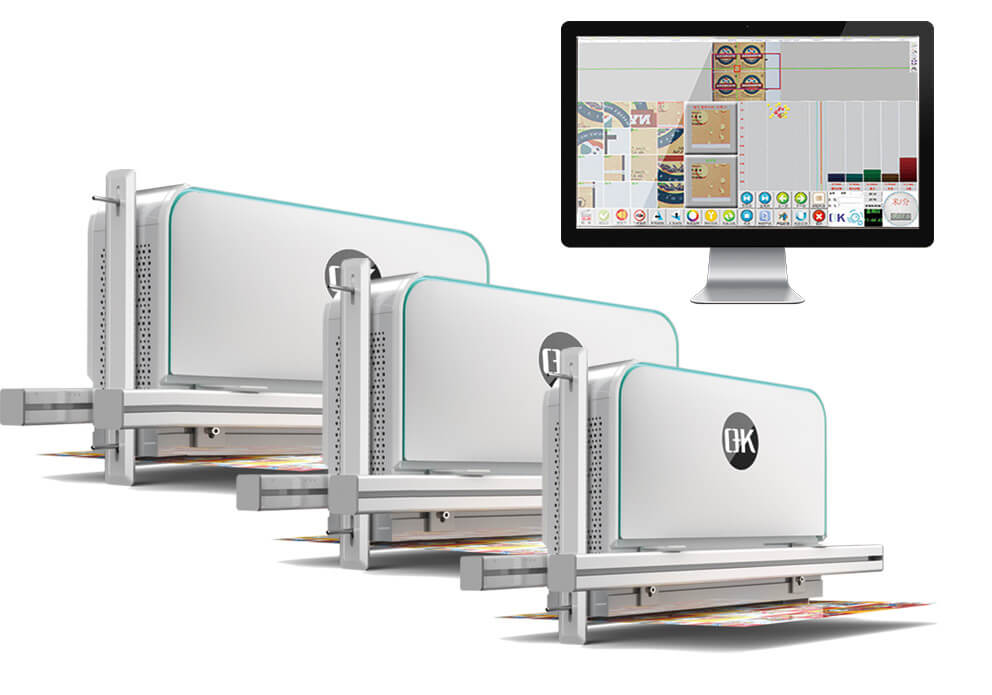
Benefits of Investing in Printing Inspection Systems
Investing in printing inspection systems offers numerous advantages that can significantly improve both operational efficiency and product quality. These benefits, which contribute to long-term savings and growth, make the investment highly worthwhile for many printing businesses.
1. Waste Reduction
Printing inspection systems can detect defects early in the production process, preventing defective products from moving forward. By identifying issues like misprints, color discrepancies, or surface flaws, these systems help reduce material waste and minimize the need for reprints. In many cases, this can result in a 20-30% reduction in waste costs, which significantly enhances cost-efficiency.
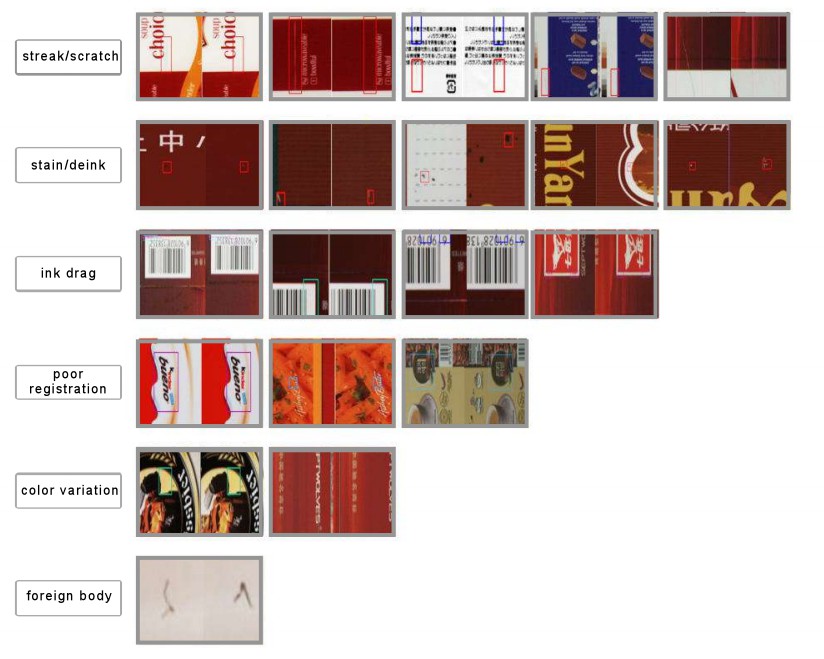
2. Improved Product Quality
High-end inspection systems are capable of performing highly accurate and consistent checks, ensuring that every printed product meets the required quality standards. This not only reduces the chance of defects slipping through unnoticed but also ensures consistent quality throughout production. As a result, businesses benefit from higher-quality products, which directly contribute to increased customer satisfaction and long-term customer loyalty.
3. Increased Production Efficiency
Automated print inspection systems operate at much higher speeds than manual inspections, significantly improving production throughput. These systems can detect defects in real-time, ensuring that the production line continues moving without unnecessary interruptions. By reducing the time spent on quality checks, businesses can experience an increase in production output by 10-20%, leading to faster turnaround times and improved delivery performance.
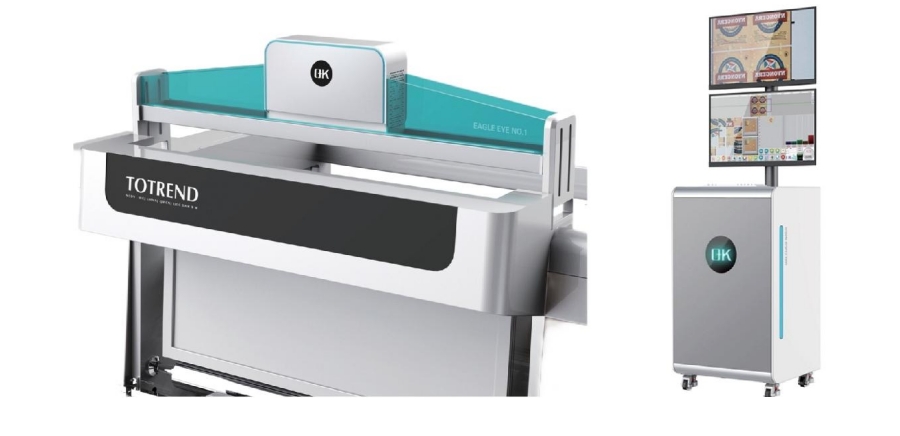
4. Labor Cost Savings
By automating the inspection process, printing businesses can reduce the need for manual labor dedicated to quality control tasks. This allows employees to focus on other more value-added activities, such as machine maintenance or process improvement. Depending on the size and scale of the business, labor cost savings from reduced inspection staffing can range from $10,000 to $50,000 annually, depending on the volume and complexity of production.
5. Enhanced Customer Retention
Delivering consistently high-quality products can have a significant impact on customer satisfaction and retention. With fewer defects and higher-quality outputs, businesses are more likely to retain existing clients and attract new ones. This can ultimately lead to long-term revenue growth and a stronger relationship with customers who depend on reliable quality for their own business success.
6. Reduced Rework Costs
One of the most significant financial impacts of investing in 100% printing inspection systems is the reduction in rework costs. With early detection of defects, businesses can prevent expensive reprints or corrections further down the line. This not only saves money but also minimizes disruptions to the production schedule, allowing the business to focus resources on the next phase of production rather than fixing mistakes.
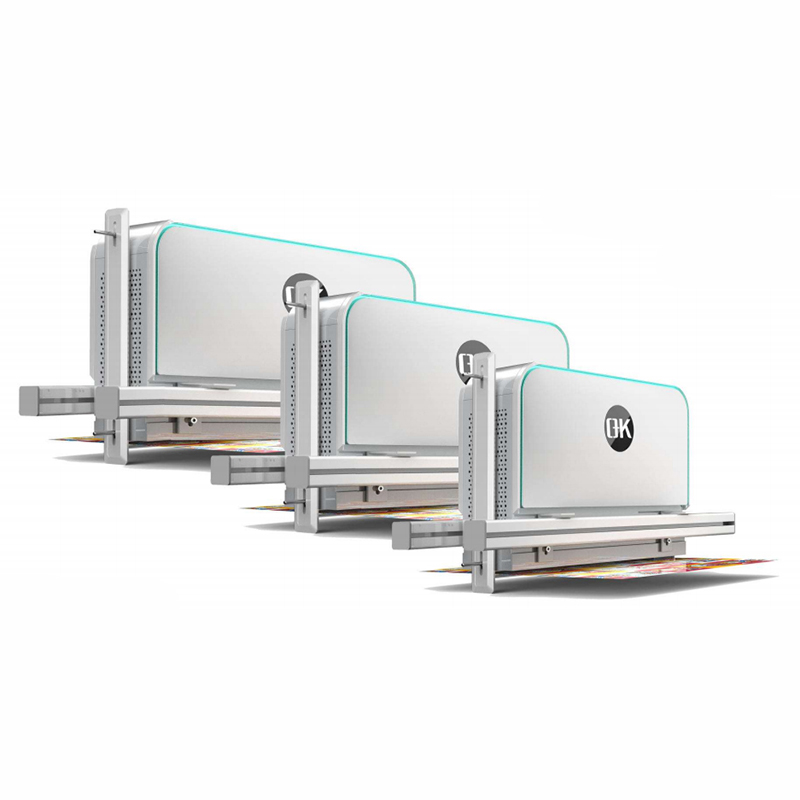
7. Competitive Advantage
With consistent quality, faster production times, and improved customer satisfaction, printing businesses that invest in inspection systems gain a competitive edge in the marketplace. These advantages make the company more attractive to potential customers, particularly those in industries where quality standards are strict, such as pharmaceuticals, packaging, and security printing. Additionally, adhering to high-quality standards enhances the company’s reputation and fosters trust within the industry.
Quantitative Cost vs. Benefit Analysis
To understand the financial impact, let’s consider an example of a mid-sized printing company:
Factor | Cost | Benefit |
Initial Investment | $100,000 | Improved product quality and fewer defects |
Waste Reduction | N/A | 20-30% decrease in material waste |
Rework Savings | N/A | $30,000/year saved in reprints |
Labor Costs | N/A | $20,000/year saved from reduced manual inspection |
Customer Retention | N/A | Increased client satisfaction and loyalty |
Estimated ROI (3-5 Years) | N/A | 2x-4x return on investment |
For a company producing $2 million in annual output, the savings from reduced waste, improved efficiency, and higher-quality output could amount to $50,000-$100,000 annually, enabling the investment to pay for itself in as little as 2-3 years.
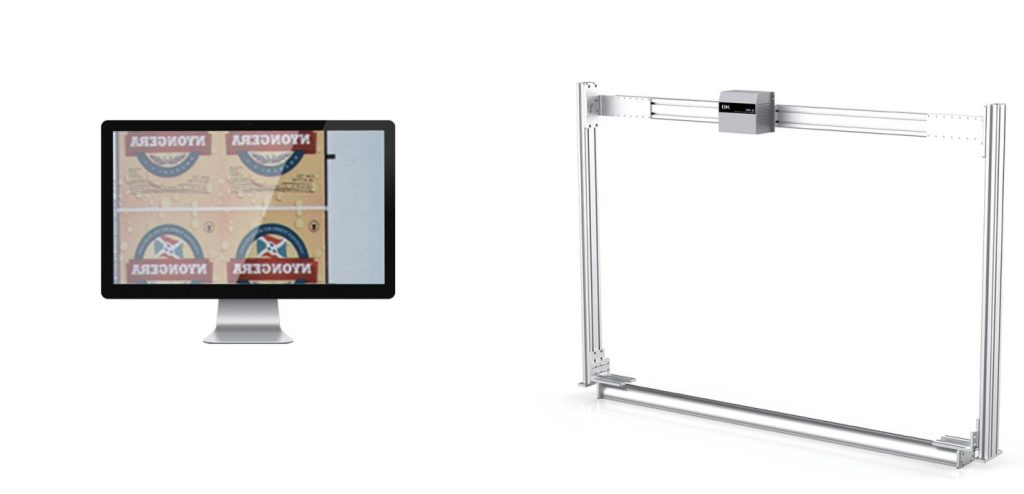
Challenges and Solutions of Investing in Printing Inspection Systems
1. High Upfront Costs
Challenge:
One of the most significant barriers to investing in printing inspection systems is the high initial investment. Depending on the system’s complexity and capabilities, the cost can range from $50,000 to $300,000 or more, which can be difficult for small and medium-sized businesses to justify.
Solution:
- Cost-Benefit Analysis: Conducting a thorough cost-benefit analysis can help businesses evaluate the long-term value of the system, factoring in potential savings from waste reduction, fewer reprints, and improved efficiency. This analysis can help justify the initial investment.
- Financing Options: Many suppliers offer financing plans, lease agreements, or payment installments, which can make the investment more manageable by spreading the cost over time.
- Gradual Integration: Consider starting with a basic system and upgrading over time as the business grows and the return on investment (ROI) becomes more evident. This phased approach can help minimize financial strain.
2. Integration with Existing Equipment
Challenge:
Print quality inspection systems need to integrate seamlessly with existing production lines. Older equipment or machines that aren’t compatible with modern inspection technology may require additional upgrades, leading to potential disruptions in production.
Solution:
- Consultation with Vendors: Work closely with the equipment supplier to ensure compatibility between the inspection system and existing production machinery. Many vendors offer tailored solutions that are compatible with different types of printing presses.
- Modular Systems: Opt for inspection systems that can be easily integrated into existing workflows without major modifications. Modular inspection systems can be added to production lines incrementally, avoiding major disruptions.
- Customization: Many suppliers offer custom configurations that can be adapted to fit unique business needs, reducing the need for costly equipment upgrades.
3. Learning Curve and Training
Challenge:
The complexity of high-end inspection systems for printing quality often requires substantial training for operators to use the equipment effectively. The learning curve can result in temporary inefficiencies and delays.
Solution:
- Comprehensive Training Programs: Invest in thorough training sessions for operators, machine maintenance teams, and managers. Many suppliers offer on-site or remote training programs to ensure employees are fully equipped to operate the system.
- Ongoing Support: Ensure the supplier provides robust customer support, including troubleshooting, technical assistance, and software updates, which can reduce the learning curve.
- Employee Involvement: Engage employees early in the decision-making process to get their buy-in, which can help ease the transition. Additionally, having a few key employees serve as “super-users” who become experts on the system can help others learn faster.
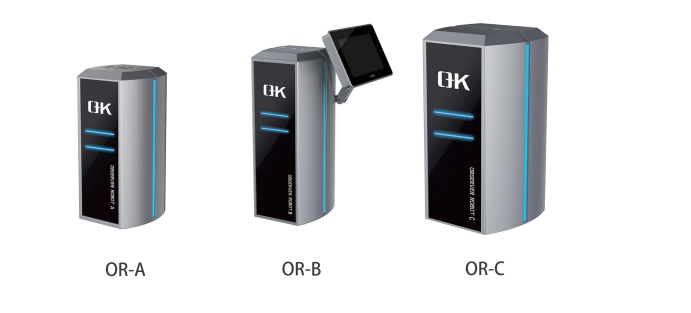
3. Over-Specification Risk
Challenge:
High-end inspection systems for printing quality are often designed with advanced features that may not be necessary for every business. Over-specification can lead to wasted resources if the system’s capabilities exceed the needs of the operation.
Solution:
- Evaluate Actual Needs: Before investing, conduct a detailed analysis of the types of defects and quality checks required for your specific production process. Choose a system that meets these needs without purchasing unnecessary features.
- Consultation with Experts: Work with industry experts or the supplier to ensure the system is well-suited to your specific requirements. This helps prevent purchasing a system that is too advanced for your production needs.
- Scalability: Choose systems that allow for scalability, where you can start with essential features and upgrade as your business grows or requires more capabilities.
4. Ongoing Maintenance Costs
Challenge:
Regular maintenance, calibration, and software updates are necessary to ensure the continued accuracy and efficiency of printing inspection systems. These ongoing costs can accumulate, potentially impacting the business’s overall ROI.
Solution:
- Service Contracts: Many vendors offer service contracts that cover regular maintenance, software updates, and repairs. These contracts provide predictability in terms of costs and ensure that the system remains operational with minimal downtime.
- Training Internal Technicians: Training in-house staff to perform basic maintenance tasks can help reduce service costs and prevent system breakdowns.
- Proactive Maintenance Schedule: Develop a proactive maintenance schedule to minimize the chances of unexpected repairs. Regular checks can also improve system longevity, reducing long-term costs.
5. Downtime During Installation and Calibration
Challenge:
Implementing a new printing inspection system often leads to temporary production downtime, especially during installation and calibration. This downtime can disrupt production schedules and result in a loss of revenue.
Solution:
- Planning for Installation: Plan installation during off-peak production hours or during scheduled downtime to minimize disruption. Clear communication with employees about the timeline and expected impact will help them prepare for the transition.
- Pilot Testing: Conduct a pilot run or test phase before full implementation to ensure everything functions as expected. This will help detect any potential issues early and reduce the need for extended downtime during full-scale integration.
- Phased Rollout: Instead of implementing the system all at once, consider a phased rollout to ensure smoother transitions and allow for any issues to be addressed in smaller batches.
6. Resistance to Change
Challenge:
Employees may resist the adoption of new technology, especially if they feel their roles are being replaced or if they are unfamiliar with the new systems.
Solution:
- Clear Communication: Communicate the benefits of the new inspection system, emphasizing how it will improve quality, efficiency, and working conditions. Address concerns about job displacement by highlighting how automation will free up workers for more complex, value-added tasks.
- Involvement in Decision-Making: Involve employees in the decision-making process early on. Their feedback can help choose a system that aligns with their needs and work processes, making them more likely to embrace the change.
- Supportive Environment: Offer ongoing training and create a support structure where employees feel comfortable asking questions and seeking help during the transition.
Summary
For printing businesses with high production volumes and strict quality standards, printing inspection systems offer a clear return on investment (ROI) within a few years. Ultimately, investing in a printing inspection system is not merely about cost saving and it is a strategic step toward ensuring quality, building trust with customers, and maintaining competitiveness in a demanding market.
Through a thorough cost vs. benefit analysis for inspection systems, print companies can determine whether this investment aligns with their operational needs and long-term goals.