Cost vs. Benefit Analysis of 100% Inspection Systems Used in Printing Industry
Table of Contents
The printing industry requires precision and high-quality standards products. Any slight deviation in print quality, color alignment, or finishing can lead to customer dissatisfaction, wasted materials, and financial losses. To address these issues, many printing companies are turning to 100% inspection systems that allow for real-time, automated quality checks of every printed product. However, implementing such systems requires a detailed cost vs. benefit analysis to determine their impact on productivity and profitability.
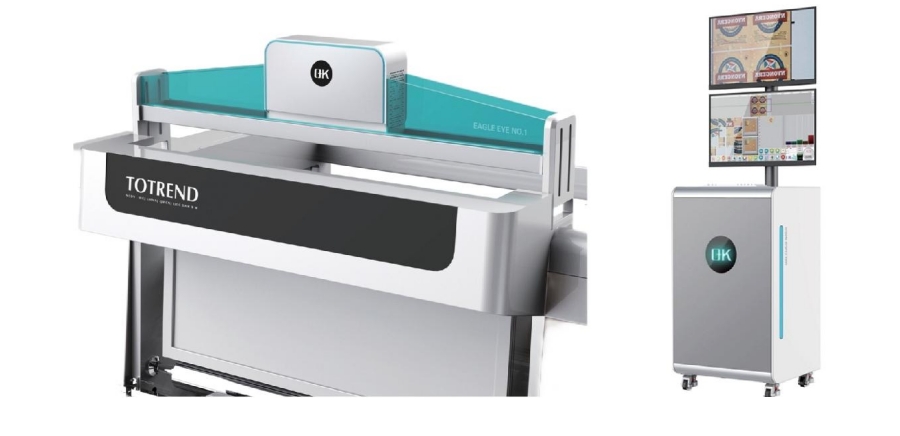
Costs of 100% Inspection Systems in Printing
1. Initial Investment
The upfront costs of acquiring and integrating 100% inspection systems into printing workflows can be substantial. These systems utilize advanced technology, including high-resolution cameras, image processing software, and real-time analytics to inspect every printed sheet, label, or package for defects.
- Equipment Costs: High-performance cameras and image processors are essential for inspecting detailed printed materials, often leading to high capital expenditure.
- Installation and Integration Costs: Incorporating the system into existing printing presses or production lines requires additional engineering and technical expertise, adding to initial setup costs.
- Employee Training: Operators must be trained to use, monitor, and maintain the inspection system, contributing to further upfront expenses.
2. Ongoing Operational Costs
Once installed, 100% inspection systems come with recurring operational expenses that need to be factored in.
- Maintenance and Calibration: Regular maintenance and calibration are necessary to ensure the system remains accurate and functions efficiently.
- Production Speed Impact: Inspection systems may slow down production lines, as each sheet or product must pass through the inspection process, leading to longer cycle times.
- Software Updates and Upgrades: As technology evolves, frequent software updates and potential hardware upgrades may be required, adding to the overall cost of maintaining the system.
- Energy Consumption: High-resolution cameras and image processing systems can increase the facility’s energy usage, impacting operational costs.
3. Material and Labor Costs
Though automated, inspection systems still require human oversight and manual intervention in cases where defects are flagged. This leads to labor costs associated with managing the system, analyzing inspection reports, and conducting corrective actions.
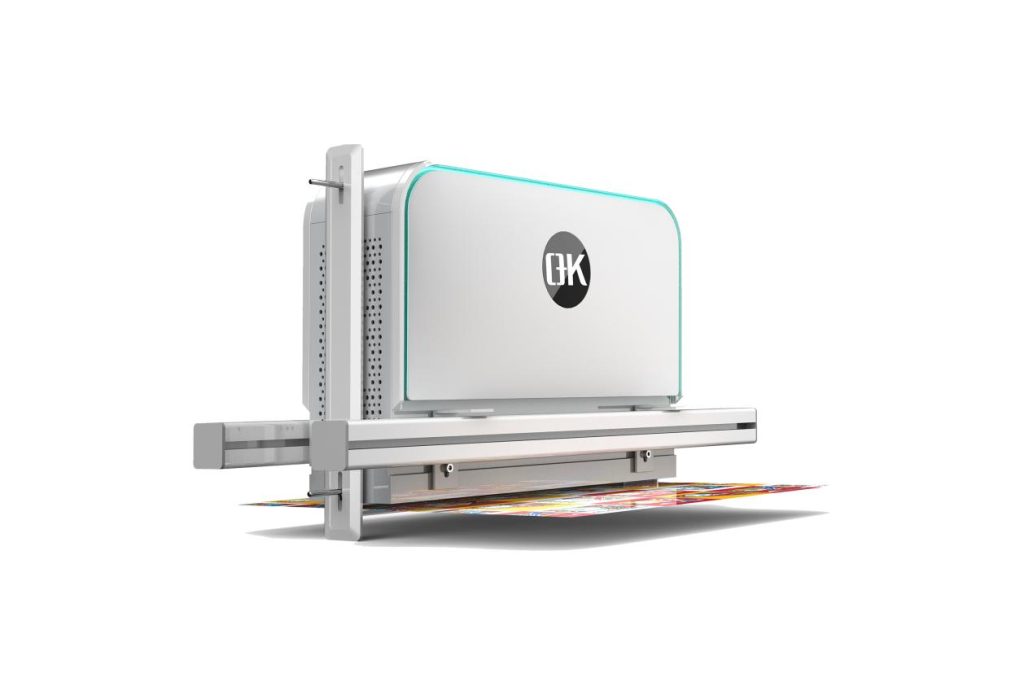
Benefits of 100% Inspection Systems in Printing
1. Defect Detection and Prevention
The primary advantage of 100% inspection systems is the ability to detect printing defects in real-time, allowing immediate correction and preventing defective materials from progressing further along the production line.
- Early Detection of Print Errors: Misalignment, color variations, smudges, and other imperfections can be detected immediately, ensuring high-quality output.
- Waste Reduction: By identifying defects early, less material is wasted, leading to cost savings on paper, ink, and other printing supplies.
- Reduced Rework: Catching issues in real time reduces the need for reprinting, saving time, materials, and labor.
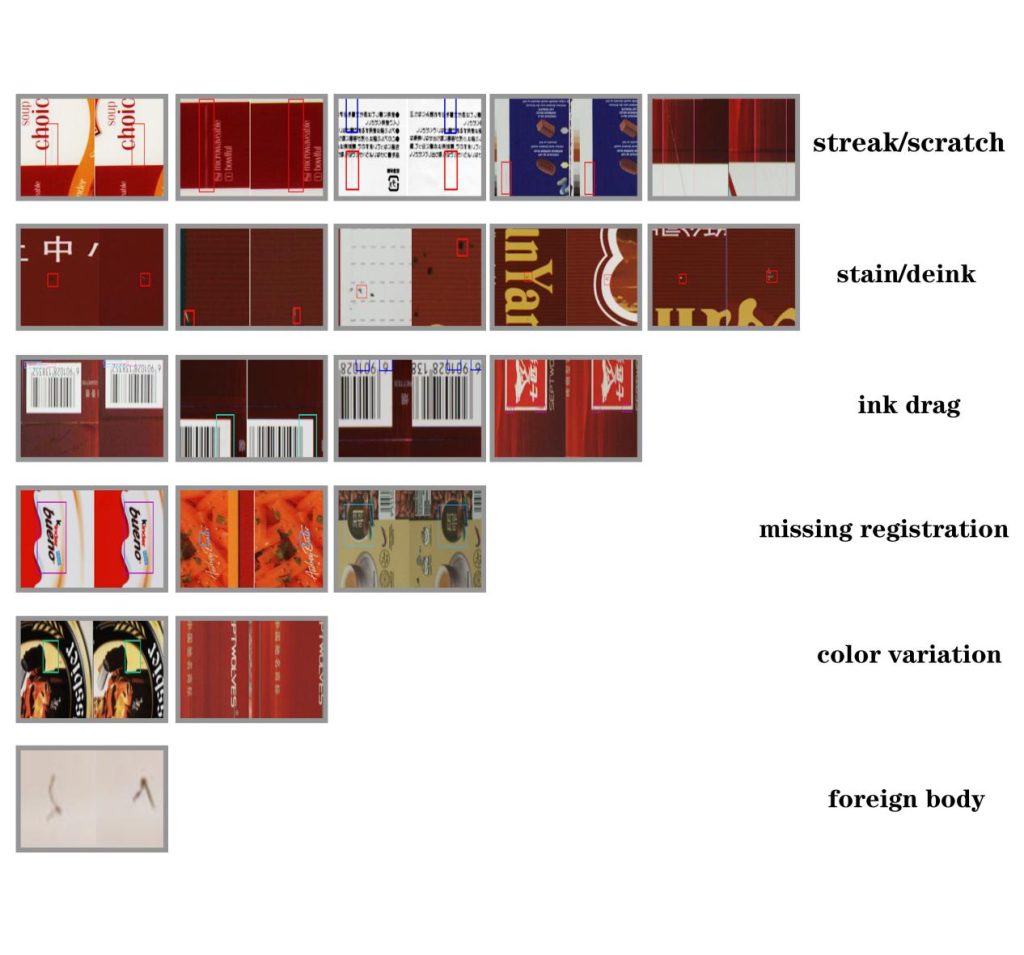
2. Enhanced Quality Control
100% inspection systems ensure that every printed product meets exacting standards, which enhances customer satisfaction and reduces the risk of returns or complaints.
- Consistent Print Quality: With every product inspected, printing companies can guarantee uniform quality across large print runs, building customer trust.
- Compliance with Customer Specifications: The system ensures that prints adhere to customer requirements for color consistency, layout accuracy, and overall appearance.
3. Increased Productivity Through Automation
Although there are initial setup and operational costs, 100% printing inspection systems can ultimately improve productivity by automating quality control.
- Faster Identification of Issues: Automated systems can detect and address issues faster than manual inspections, reducing downtime and avoiding large-scale production errors.
- Data-Driven Improvements: Inspection systems generate valuable data on defect rates and causes, enabling companies to optimize their processes and reduce future errors.
4. Brand Reputation and Competitive Advantage
By consistently delivering flawless print products, companies can bolster their reputation for reliability and quality, which can help them stand out in a competitive market.
- Higher Customer Retention: Providing defect-free products leads to higher levels of customer satisfaction and repeat business.
- Attracting New Clients: A strong track record of quality can attract new clients, especially those with stringent quality requirements such as in packaging and branding sectors.
5. Data-Driven Process Optimization
- Insightful Analytics: 100% inspection systems collect valuable data on defect rates and patterns, which can be used to identify the root causes of recurring issues.
- Process Improvements: This data helps companies refine their printing processes and make data-driven adjustments, ultimately enhancing the overall operational efficiency and quality control measures.
6. Compliance with Industry Standards
- Meeting Regulatory Requirements: For industries with stringent quality and regulatory standards, such as pharmaceutical packaging, security printing, and high-end product labels, 100% inspection systems ensure compliance with quality benchmarks.
- Customer-Specific Requirements: These printing inspection systems also allow companies to meet the high expectations of customers who demand flawless print products, helping to fulfill contractual obligations.
7. Reduced Labor Costs
- Automation of Inspection Tasks: By automating the inspection process, companies can reduce their reliance on manual quality checks, freeing up labor for other tasks and reducing human errors that can occur during inspections.
- Lower Rework Rates: Fewer defective products in the production line means less time spent reprinting or repairing faulty prints, resulting in reduced labor costs associated with fixing quality issues.
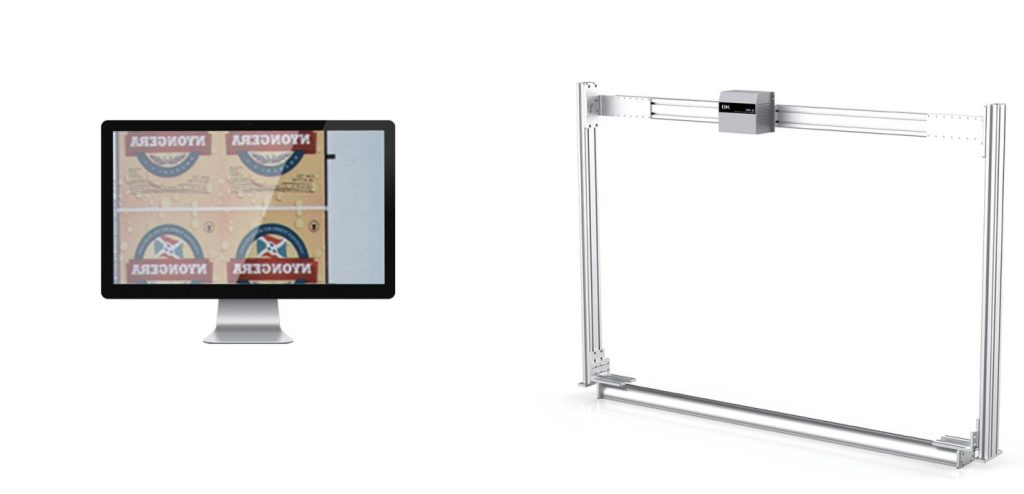
Calculating ROI of 100% Inspection Systems in Different Print Markets
1. High-Value Print Jobs
For sectors like pharmaceutical packaging, security printing, and premium product labels, the ROI of 100% inspection systems is particularly strong. The cost of producing defective materials in these industries is often far higher than the cost of the inspection system itself, making the investment worthwhile.
- Precision Printing: In precision-demanding industries, the ability to guarantee defect-free production justifies the cost of 100% inspection systems.
- Compliance and Safety: Ensuring that printed products meet regulatory standards can protect businesses from costly legal issues and penalties.
2. Short-Run and Custom Printing
In custom and short-run printing jobs, where each product must meet exacting specifications, 100% inspection systems offer a clear return by ensuring that every piece is flawless. This is especially important in personalized or luxury printing jobs.
- Customer Expectations: Meeting the high expectations of clients in these sectors ensures repeat business and premium pricing.
3. High-Volume, Low-Value Printing
In high-volume, low-value print jobs such as flyers or promotional brochures, the ROI of a 100% inspection system may be less significant. In these cases, a sampling-based quality control approach could offer sufficient quality assurance without the need for continuous inspection.
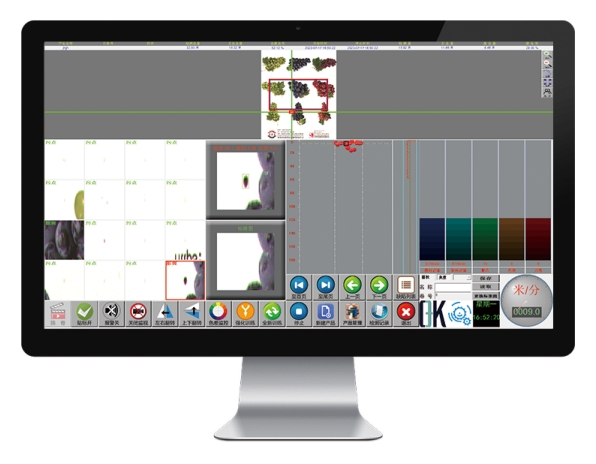
Cost vs. Benefit Summary of 100% Inspection Systems in Printing
Investment Area | Cost | Benefit |
Equipment Purchase | High initial cost for hardware and software integration | Long-term savings through reduced waste and higher quality output |
Labor and Training | Initial training costs for staff, lower labor needs post-implementation | Automated quality inspection reduces manual workload and associated labor costs |
Material Waste Reduction | Significant savings in paper, ink, and other materials | Fewer defective products reduce the need for reprinting and minimize waste |
Customer Satisfaction | High initial cost to meet stringent client demands | Enhanced customer loyalty and retention, reduced complaints, and fewer returns |
Data-Driven Optimization | Maintenance and software updates | Process improvements based on actionable data, leading to reduced defect rates and increased productivity |
Overall, In the printing industry, the decision to implement 100% inspection systems requires careful consideration of both costs and benefits. For high-value and precision-demanding sectors, the investment can deliver a strong return. However, in lower-value production environments, companies may opt for selective inspection methods that balance cost-efficiency with acceptable levels of quality assurance. Ultimately, the choice depends on the specific needs of the printing operation and the quality expectations of its clients.