Challenges and Solutions of Web Guiding in High-Speed Printing
Web guide systems serve an important role in ensuring the smooth movement of materials through the manufacturing process in high-speed printing, where precision is vital. However, the increased pace of printing operations creates new issues that necessitate innovative solutions. This article explores the challenges faced by web guiding systems in high-speed printing and delves into the solutions that pave the way for enhanced accuracy and efficiency.
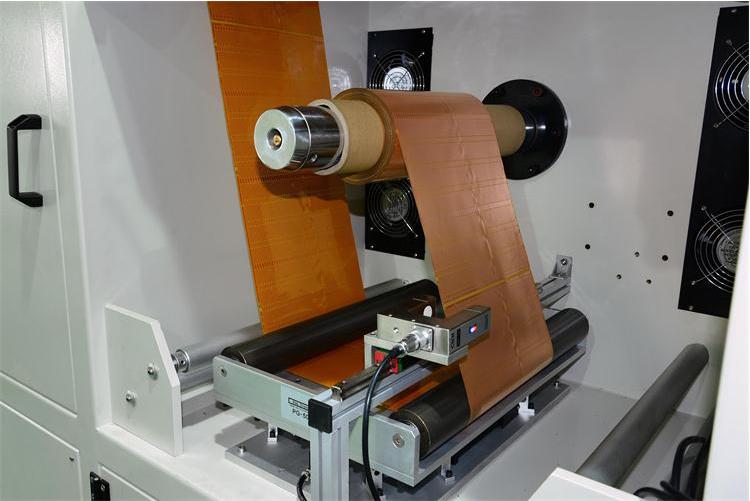
Challenges in Web Guiding for High-Speed Printing
1. Dynamic Tension Variations
High-speed printing processes frequently cause dynamic tension fluctuations in the web as it goes through the system, which has an impact on material alignment and registration.
2. Substrate Variability
Printing substrates and materials can vary in qualities such as elasticity and thickness, making consistent web guiding at high speeds difficult.
3. Accurate Registration Requirements
Color and element registration must be perfect when printing at high speeds. Maintaining proper alignment throughout the printing process presents a substantial difficulty.
4. Web Flutter and Deflection
At increased speeds, the web may experience flutter or deflection, introducing deviations that need to be swiftly detected and corrected by the web guiding system.
5. Vibration and Machine Dynamics
Vibrations and dynamic motions of high-speed printing gear might influence the web’s stability, complicating the challenge of keeping it aligned.
6. Material Stretch and Shrinkage
The high speeds and associated forces can cause materials to stretch or shrink, impacting the accuracy of web guiding systems and requiring real-time adjustments.
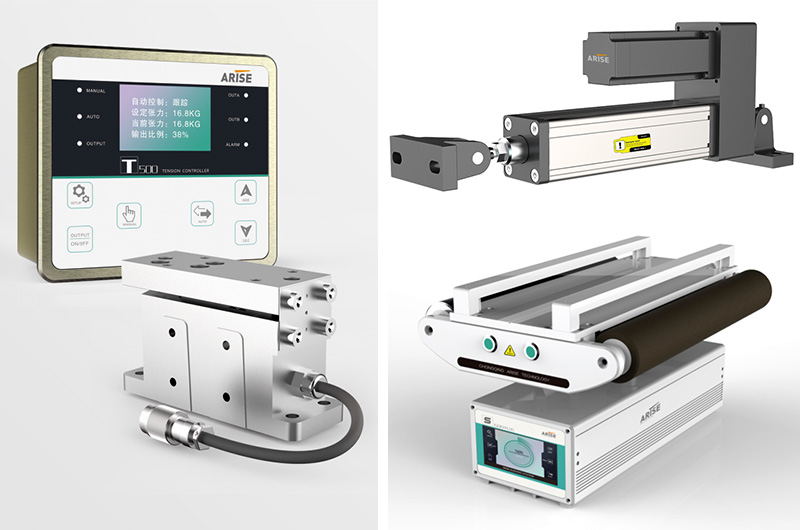
Solutions to Address Web Guiding Challenges in High-speed Printing
1. Advanced Sensor Technologies
Implementing state-of-the-art sensor technologies, such as ultrasonic sensors or laser sensors, enables real-time monitoring of web position and tension, allowing for rapid adjustments to changes in material properties.
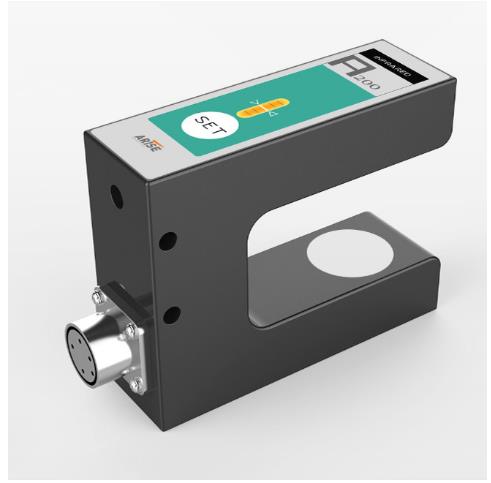
2. Closed-Loop Control Systems
Closed-loop control systems continually analyze sensor feedback and change the web guiding mechanism in real time, ensuring exact alignment even in the face of dynamic tension variations.
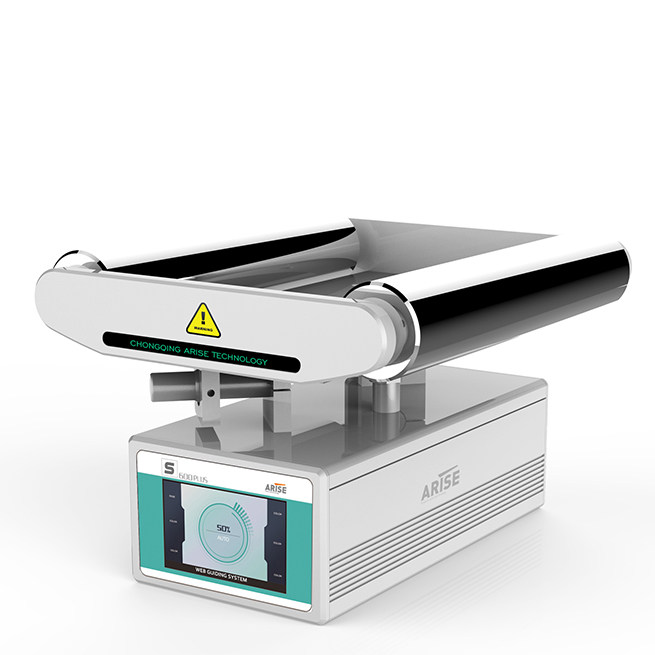
3. Smart Algorithms for Registration Control
Employing smart algorithms that predict and compensate for registration errors ensures accurate alignment of the web throughout the printing process, contributing to high-quality output. Advanced tension control algorithms are computer algorithms that regulate and maintain constant tension levels in online processing activities. These algorithms use real-time data, mathematical models, and feedback loops to dynamically alter tension, ensuring that the material’s speed and tension remain consistent throughout a wide range of web processing scenarios.
4. Web Guiding Systems with Fast Response Times
Investing in web guiding systems with rapid response times ensures that corrections are made swiftly, minimizing the impact of flutter, deflection, or sudden changes in web behavior.
5. Dynamic Tension Control Mechanisms
Incorporating tension control mechanisms that can adjust dynamically to changes in web tension helps to preserve stability, especially in settings where tension fluctuations occur often.
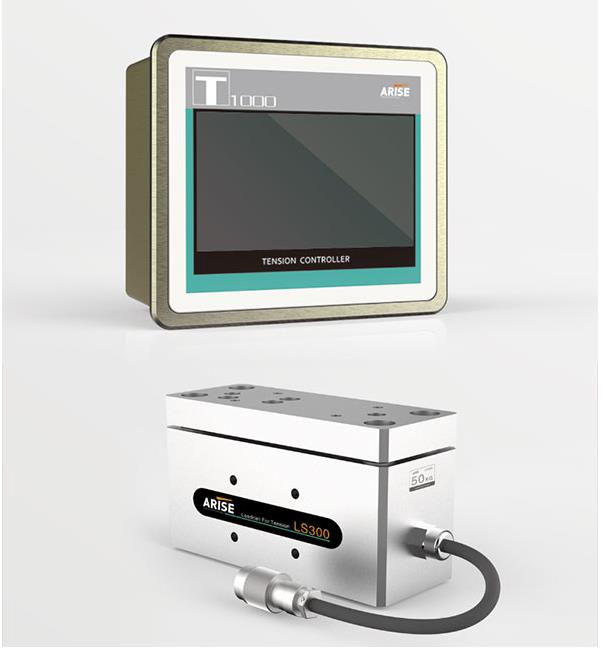
6. Continuous Monitoring and Diagnostics
Implementing continuous monitoring and diagnostics via modern Human-Machine Interface (HMI) systems enables operators to spot possible problems before they affect print quality, decreasing downtime.
7. Precision Rollers and Guiding Components
Upgrading precision-engineered rollers and web guiding components decreases friction and enhances the overall stability of the web guiding system, mitigating the impact of vibrations and dynamic forces.
8. Material-specific Web Guiding Configurations
Tailoring web guiding configurations to the individual qualities of different substrates and materials guarantees that the system can respond to variations in elasticity and thickness, resulting in improved performance.
Conclusion
Web guiding in high-speed printing is a complex dance of precision and speed. Addressing the issues provided by the high pace of modern printing necessitates the use of innovative technology, smart algorithms, and sensitive control systems. As the need for high-quality, high-speed printing grows, the industry’s capacity to solve these problems will become increasingly important in achieving peak performance and producing perfect prints. Web guiding systems can meet the challenge of high-speed printing with unrivaled accuracy and efficiency by focusing on adaptable solutions and continuous innovation.